Recycling plastics waste into value-added chemicals using efficient and selective novel nanocatalysts promises economic as well as environmental benefits.
According to a recent document published by the International Union for Conservation of Nature (IUCN), at least 14 million tons of plastic end up in the oceans every year, threatening the marine ecosystem, food safety and economic activities1. Approaches to mitigate the environmental impact of plastics in oceans include reducing use, reusing and recycling. Of the over 400 million tonnes of plastic produced every year, however, only 9% is recycled2, usually with conventional mechanical or thermal pyrolysis methods that necessarily lead to lower-value products than the original plastics or inefficient energy recovery in the form of heat3. In recent years, direct catalytic transformation of waste plastics into value-added fuels, chemicals, and materials is seeing more and more attention, due to its potential environmental and economic benefits.
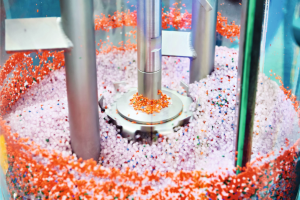
Credit: Sergey Ryzhov / Alamy Stock Photo
A common way to directly upcycle plastics waste is to depolymerize it into value-added monomers or oligomers (or their derivatives) without subsequent transformations. The design of the catalysts determines the products and their distribution. For instance, with an ordered, mesoporous shell/active site/core catalyst architecture that incorporates catalytic platinum sites at the base of the mesopore, high-density polyethylene (HDPE) can be selectively hydrogenolysed into a narrow distribution of diesel and lubricant-range alkanes4. Additionally, ruthenium nanoparticles on HZSM-5 zeolite catalyze solvent/hydrogen-free upcycling of HDPE into a separable distribution of linear (C1–C6) and cyclic hydrocarbons (C7–C15) (see the Article in this issue by Du and colleagues).
Another exciting strategy to directly generate value-added products is by depolymerizing plastics waste and simultaneously functionalizing the resulting crude product. Production of aromatic surfactants from polyethylene can be achieved at relatively mild operating conditions, by combining the aromatization and hydrogenolysis with a platinum/alumina catalyst5. Additionally, propylene can be selectively produced from waste-grade polyethylene with yields as high as 80% by partial dehydrogenation and tandem ethenolysis of the desaturated chain6.
The introduction of heteroatoms and halogens during the depolymerization process also aids the formation of value-added products. For example, gaseous hydrocarbon products can be made from the direct conversion of polyethylene through an oxidative route. A nitric acid treatment converts polyethylene into organic acids (succinic, glutaric, and adipic acid), which can then be photocatalytically or electrocatalytically converted into olefins7. Additionally, oxidative upcycling of polystyrene to aromatic oxygenates has been realized with graphitic carbon nitride photocatalyst under visible light irradiation. The conversion of polystyrene can be more than 90% at 150 °C, obtaining mainly benzoic acid, acetophenone, and benzaldehyde in the liquid phase8.
There are a variety of other, indirect approaches for plastics upcycling, where waste plastics are first depolymerized into monomers, oligomers, or their derivatives, which can then be further transformed into high-value chemicals under thermo-, electro-, photo-, or bio-catalytic conditions. This upcycling route is indirect, as it passes through a separate monomer-generation step and it might have a negative impact on both the environmental ramifications and the economics of the process compared to direct upcycling9.
Commercial plastics are usually a blend of components or formulations that include polymers and small-molecule additives. Key factors such as the molecular identity and arrangement (the degree of branching and/or cross-linking), crystallinity, and molecular weight determine the physico-chemical properties of the polymer and accessibility to chemical bonds, affecting the efficiency and selectivity of the catalytic plastics deconstruction methodology10. To quantitatively compare the catalysts and processes being developed for different feedstocks with the various chemical compositions and physical structures, the physical properties of the polymeric substrate, their chemical composition and structure (monomer identities, molecular weight distribution, melting point, and crystallinity), as well as reaction conditions (pH, temperature, substrate loadings, stirring rate, and so on) should be rigorously reported. This metrology in the reporting literature is essential to coordinate progress in the field and help tackle the issue of plastic pollution in a meaningful manner.
- SEO Powered Content & PR Distribution. Get Amplified Today.
- PlatoData.Network Vertical Generative Ai. Empower Yourself. Access Here.
- PlatoAiStream. Web3 Intelligence. Knowledge Amplified. Access Here.
- PlatoESG. Automotive / EVs, Carbon, CleanTech, Energy, Environment, Solar, Waste Management. Access Here.
- BlockOffsets. Modernizing Environmental Offset Ownership. Access Here.
- Source: https://www.nature.com/articles/s41565-023-01473-5
- :has
- :is
- :where
- $UP
- 1
- 10
- 11
- 13
- 14
- 2017
- 2020
- 2021
- 2022
- 22
- 300
- 32
- 33
- 36
- 46
- 7
- 8
- 9
- a
- accessibility
- achieved
- Additionally
- additives
- affecting
- aids
- AL
- also
- an
- Anchor
- and
- approaches
- architecture
- ARE
- arrangement
- AS
- At
- attention
- base
- BE
- been
- being
- benefits
- Blend
- Bonds
- both
- by
- CAN
- carbon
- Catalyst
- catalysts
- chemical
- chemicals
- click
- colleagues
- combining
- Common
- compare
- compared
- components
- conditions
- CONSERVATION
- conventional
- Conversion
- converted
- coordinate
- credit
- crude
- Degree
- Derivatives
- Design
- Determine
- determines
- developed
- diesel
- different
- direct
- directly
- distribution
- document
- due
- during
- e
- E&T
- Economic
- Economics
- ecosystem
- efficiency
- efficient
- end
- energy
- environmental
- essential
- Ether (ETH)
- Every
- example
- exciting
- factors
- Fall
- February
- field
- First
- food
- For
- form
- formation
- from
- fuels
- further
- generate
- Growing
- Have
- help
- High
- However
- HTTPS
- identities
- Identity
- Impact
- in
- include
- incorporates
- inefficient
- instance
- International
- into
- Introduction
- issue
- IT
- ITS
- Key
- lead
- least
- light
- LINK
- Liquid
- literature
- made
- mainly
- management
- manner
- Marine
- materials
- meaningful
- mechanical
- methods
- Metrology
- might
- mild
- million
- Mitigate
- molecular
- more
- nanotechnology
- Nature
- necessarily
- negative
- novel
- November
- November 2021
- obtaining
- oceans
- OECD
- of
- on
- only
- operating
- or
- organic
- original
- Other
- over
- oxidative
- passes
- physical
- plastic
- plastics
- platinum
- plato
- Plato Data Intelligence
- PlatoData
- Point
- Pollution
- polymer
- Polymers
- potential
- process
- processes
- Produced
- Product
- Production
- Products
- Progress
- promises
- properties
- published
- Rate
- reaction
- realized
- recent
- recovery
- recycling
- reducing
- relatively
- Reported
- Reporting
- resulting
- Route
- s
- Safety
- says
- Science
- see
- seeing
- selective
- separate
- Short
- should
- simultaneously
- Sites
- So
- Step
- stock
- Strategy
- structure
- subsequent
- such
- tackle
- Tandem
- than
- that
- The
- their
- then
- thermal
- this
- Through
- to
- tons
- Transformation
- transformations
- transformed
- treatment
- under
- union
- use
- using
- usually
- variety
- various
- visible
- Waste
- Way..
- weight
- WELL
- which
- with
- without
- year
- years
- yields
- zephyrnet