– Look! Up in the sky! – It’s a Bird! – It’s a Plane! – No! It’s… Oh it’s drones again…
If you hear a bzzzz annoying you, do not rush to look for the unfortunate fly to finish it off. Perhaps it is also troubled by the sound that this flying aluminium box makes.
Drones come in many forms, some harmless and some dangerous. Let’s look at which is which and discuss some of their unique features.
Drones are flying robots, including unmanned aerial vehicles (UAVs) that can fly thousands of kilometers, as well as small drones designed for confined spaces. Aerial vehicles that do not carry a human operator, fly either remotely or autonomously, and carry either lethal (non-friendly) or nonlethal (likely friendly) payloads are considered drones.

Depending on the flight missions of the drones, the size and type of installed equipment are different. Considerable advantages of drones have led to a myriad of studies focusing on the optimization and enhancement of the performances of these drones. According to the mentioned characteristics, drones benefit from the potential to carry out a variety of operations, including reconnaissance, patrolling, protection, transportation of loads, and aerology.
As shown in Fig. 2, there is a wide spectrum of drones from the UAV class with a maximum wing span of 61 m and weight of 15,000 kg to smart dust (SD) with a minimum size of 1 mm and weight of 0.005 g. Between UAV and SD at both ends of the defined spectrum, there are various types of drones, which are called micro drones, such as micro unmanned air vehicle (μUAV), micro air vehicle (MAV), nano air vehicle (NAV), and pico air vehicle (PAV) [1].

Generally, drones can be categorized by their performance characteristics. Features, including weight, wing span, wing loading, range, maximum altitude, speed, endurance, and production costs, are critical design parameters that distinguish different types of drones and provide beneficial classification systems. Furthermore, drones can be classified based on their engine types. For example, UAVs often apply fuel engines, and MAVs use electrical motors. The types of propulsion systems which are used in these unmanned aircraft are different based on their models. The offered classification of drones in Fig. 3 shows various models of these unmanned aircraft as a function of their configuration. The indicated flowchart in Fig. 3 also considers the bio models of micro and nano air vehicles, defined as live controllable birds or insects and flying taxidermy birds.

Propulsion systems
All of the presented drone configurations need to generate motion. Therefore, there are different ways to make a drone fly. The propulsion system of these unmanned aircraft differs according to their shapes and flight modes. For some types of drones, such as fixed-wing UAVs, the propulsion system is usually similar to conventional aircraft. Thus, these drones do not need a unique propulsion system. Therefore, such drones can avoid the time and expense of developing new systems.
On the other hand, some types of drones require new propulsion technology. Thus, they need new designs and concepts. In propulsion systems, power and energy densities are two essential factors. Power density is a measure of the power converter and energy density is a measure of the energy in the power source and the conversion efficiency of the engine. The propulsion system for a drone is proportional to the weight, size, mission, endurance, etc. The selected design must provide fuel economy (gas or battery), low weight, small size, and high reliability. Generally, for all types of drones, propulsion systems (engines, fuels, and actuators) typically constitute 40–60% of their take-off weight. It should be mentioned that the propulsion system’s performance has an enormous effect on air vehicle performance [1].
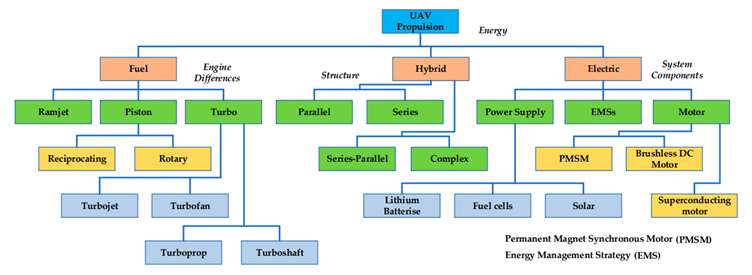
Nevertheless, if we consider UAVs that have found prevalence in the Defence and Intelligence industry, then to this day the most relevant engine is still a gas turbine.
Let’s look at this in more detail. In general terms, several schemes can be considered, shown in Fig 5. On the one hand, a broad view of the Brayton cycle, and on the other, the reverse Brayton cycle (both have a recuperator in the scheme). Usually, the general Brayton cycle is more effective than its reverse interpretation, but it also has positive aspects.

In small-scale propulsion applications, the gas turbine suffers from significantly increased fuel consumption due to second-order scaling effects. Some of these losses stem from geometric features which do not scale linearly with diameters, such as blade relative tip clearance and surface area. The inverse Brayton cycle propulsion system reorganizes traditional gas turbine components. The IBC incorporates expansion before compression, achieving atmospheric engine inlet pressures and sub-atmospheric compressor inlet pressures. For these reasons, the IBC allows for benefits over the traditional Brayton cycle in specific applications. The IBC can be used in what some call a “mirror” configuration, where the IBC is used to further extract work from the waste heat of another gas turbine in a bottoming cycle. Another approach is to use the IBC in a single-cycle configuration to improve the efficiency of small gas turbines. This is possible because the IBC’s sub-atmospheric pressure results in engine components that are larger than when used in traditional configurations and alleviates certain second-order scaling effects. The feasibility of an Inverse Brayton cycle-based UAV propulsion system was considered in a previous paper. Based on design point comparisons with the General Brayton cycle (GBC), it was determined that the IBC provides reduced fuel consumption at the expense of increased weight. Due to the increase in engine weight, an aircraft range increase couldn’t be realized with linearly scaled components [2].
With the development of hydrogen technologies or fuel cells and more efficient energy carriers and energy resources, drones will also become more progressive and open up more applications. Despite this, the main driving force for any air vehicle will remain a bladed machine (propeller, fan, or compressor), which can also be powered by a turbine in addition to an electric motor. Designing all moving elements is easy with commercial tools such as AxSTREAM, and AxSTREAM System Simulation which can help determine all the necessary and best design parameters.
Learn more about the tools used in this blog by requesting a software trial
Reference:
- “Progress in Aerospace Sciences: Classifications, applications, and design challenges of drones: A review”, M. Hassanalian, A. Abdelkefi, May 2017
- “An Off-Design Analysis of an Inverse Brayton Cycle Based UAV Propulsion System”, Nicholas D. Grannan and Ephraim Gutmark, University of Cincinnati, Cincinnati, Ohio, 45222
- https://www.bbc.co.uk/news/world-60047328
- “Overview of Propulsion Systems for Unmanned Aerial Vehicles”, Bowen Zhang, Zaixin Song, Fei Zhao and Chunhua Liu;
- SEO Powered Content & PR Distribution. Get Amplified Today.
- Platoblockchain. Web3 Metaverse Intelligence. Knowledge Amplified. Access Here.
- Source: https://blog.softinway.com/drones-among-us/
- :is
- $UP
- 000
- 1
- a
- About
- According
- achieving
- addition
- advantages
- Aerospace
- AIR
- aircraft
- All
- allows
- among
- analysis
- and
- Another
- applications
- Apply
- approach
- ARE
- AREA
- AS
- aspects
- At
- atmospheric
- autonomously
- based
- battery
- bbc
- BE
- because
- become
- before
- beneficial
- benefit
- benefits
- BEST
- between
- Birds
- BLADE
- Blog
- Box
- broad
- by
- call
- called
- CAN
- carriers
- carry
- Cells
- certain
- challenges
- characteristics
- class
- classification
- classified
- CO
- come
- commercial
- components
- concepts
- Configuration
- Consider
- considerable
- considered
- considers
- constitute
- consumption
- conventional
- Conversion
- Costs
- critical
- cycle
- Dangerous
- day
- defence
- defined
- density
- Design
- designed
- designing
- designs
- Despite
- detail
- Determine
- determined
- developing
- Development
- different
- discuss
- distinguish
- driving
- drone
- Drones
- Dust
- economy
- effect
- Effective
- effects
- efficiency
- efficient
- either
- Electric
- electric motor
- elements
- ends
- energy
- energy density
- Engine
- Engines
- enhancement
- enormous
- equipment
- essential
- etc
- example
- expansion
- extract
- factors
- fan
- Features
- fei
- Fig
- Figure
- finish
- flight
- flying
- focusing
- For
- Force
- forms
- found
- friendly
- from
- Fuel
- fuel cells
- fuels
- function
- further
- Furthermore
- GAS
- GBC
- General
- generally
- generate
- hand
- Have
- hear
- help
- High
- HTTPS
- human
- hydrogen
- IBC
- improve
- in
- Including
- incorporates
- Increase
- increased
- indicated
- industry
- Intelligence
- interpretation
- IT
- ITS
- jpg
- larger
- Led
- likely
- live
- loading
- loads
- Look
- losses
- Low
- machine
- Main
- make
- MAKES
- many
- max-width
- maximum
- measure
- mentioned
- minimum
- Mission
- missions
- models
- modes
- more
- more efficient
- most
- motion
- Motor
- Motors
- moving
- nano
- nav
- necessary
- Need
- NEVADA
- New
- of
- offered
- Ohio
- on
- ONE
- open
- Operations
- operator
- optimization
- Other
- Paper
- parameters
- performance
- performances
- perhaps
- Pico
- plato
- Plato Data Intelligence
- PlatoData
- Point
- positive
- possible
- potential
- power
- powered
- presented
- pressure
- previous
- Production
- progressive
- propulsion
- protection
- provide
- provides
- range
- realized
- reasons
- Reduced
- relevant
- reliability
- remain
- require
- Resources
- Results
- reverse
- robots
- rush
- Scale
- scaling
- scheme
- schemes
- SCIENCES
- SD
- selected
- several
- shapes
- should
- shown
- Shows
- significantly
- similar
- Size
- small
- smart
- Software
- some
- Sound
- Source
- spaces
- span
- specific
- Spectrum
- speed
- Stem
- Still
- studies
- such
- Suffers
- Surface
- system
- Systems
- Technologies
- Technology
- terms
- that
- The
- their
- therefore
- These
- thousands
- time
- tip
- to
- tools
- traditional
- Training
- transportation
- turbine
- types
- typically
- UAV
- unfortunate
- unique
- university
- University of Cincinnati
- use
- usually
- variety
- various
- vehicle
- Vehicles
- View
- Waste
- ways
- weight
- WELL
- What
- which
- wide
- will
- Wing
- with
- Work
- zephyrnet
- Zhao