The fields of energy conversion and propulsion systems stand at the forefront of technological innovation, driving advancements in transportation, aerospace, and sustainable energy solutions. In the quest for optimized performance and efficiency, researchers are increasingly turning to holistic modeling approaches that bridge the gap between 0D and 3D simulations. The integration of simulation levels offers a more comprehensive understanding of complex systems by combining simplified, yet accurate, 0D models with highly detailed 3D representations. In this exploration of holistic modeling, we’ll look into how combining 0D and 3D perspectives is essential for designing, analyzing, and optimizing various systems such as steam power plants and rocket propulsion.
Holistic modeling combines simplified 0D models with detailed 3D simulations, allowing engineers and scientists to get a complete picture of how different components interact within systems. This approach considers both the big picture and the finer details, providing a more faithful view of how systems work in the real world.

Energy conversion and propulsion systems operate as thermodynamic cycles, which engineers must design, evaluate, and optimize. The engineer’s process requires simulation of how a new or existing system and its components perform under different conditions. However, given the sheer multitude of components involved in such cycles, software tools are absolutely necessary for studying cycle operation and component interaction. AxSTREAM System Simulation is SoftInWay’s software tool that enables engineers to study and optimize cycles using methods such as Design of Experiment and Monte Carlo. The platform provides a virtual lab where one can tweak and test different setups to find the most desirable ones, both at steady states and in transient conditions.
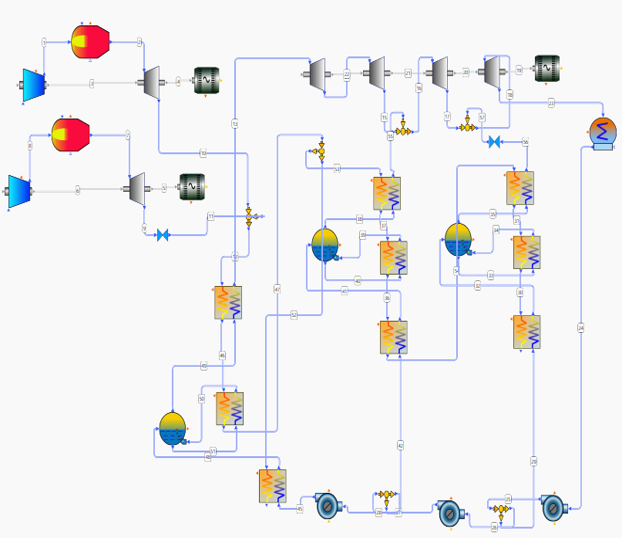
In thermal-fluid networks, fluid moves through various elements with specific pressures, temperatures, and velocities. Each element interacts with others in unique ways, and these interactions define the characteristics of each component. In the context of thermodynamic cycles, engineers face the task of modeling thermal-fluid networks to simulate the fluid and heat flow through the elements. Doing so requires breaking down the model of fluid paths, heat exchange surfaces, and solid structures into connected 1D elements. This helps to capture the complex interactions between different components, providing a detailed understanding of thermal-fluid dynamics within the system.
AxSTREAM System Simulation excels at both system-level modeling and thermal-fluid network modeling. While the tool makes easy work of modeling the two separately, it also allows coupling them in a unified representation. The platform includes a library of 100+ diverse 0D and 1D elements accessible through a user-friendly interface that makes creating coupled 0D & 1D systems simple and straightforward. For instance, users can model a gas turbine engine with all necessary 0D elements, and then couple the fuel system details to their model directly (Figure 3).
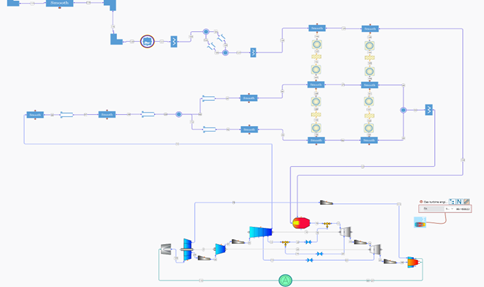
Of course, good models rely on precise elements derived from accurate performance data and comprehensive component details. AxSTREAM’s flow path modules facilitate this by offering multiple avenues for performance data determination. Users can import component performance maps into AxSTREAM System Simulation models, though precision may be limited for secondary flow influence studies. Alternatively, designing within AxSTREAM allows for 1D meanline and 2D throughflow analysis under specific conditions, enhancing precision. For advanced predictions, leveraging artificial intelligence within AxSTREAM provides a sophisticated option, ensuring users can tailor their approach to meet specific analysis requirements.
SoftInWay’s machine learning AI models facilitate preliminary design for turbomachinery. At the press of a button, these models build full 3D geometries and produce performance maps automatically – an ideal fit for AxSTREAM System Simulation. This enables users to focus on high-level models while the AI generates realistic machines.

AxSTREAM also integrates additional modules, including AxCFD for CFD analysis, AxSTRESS as a finite element solver, and modules for bearing and rotordynamics. Once the machine is generated, validation in these modules ensures more precise solutions and performance data.
AxSTREAM stands out as a pivotal tool in the realm of energy system development. By integrating system-level modeling and thermal-fluid network modeling through 0D-3D approaches, it provides a comprehensive understanding of complex systems. This software platform’s adaptability is underscored by its capacity to couple diverse modeling elements, thereby facilitating effective cycle optimization. AxSTREAM adds a significant contribution by providing precise performance data, while employing innovative methodologies such as artificial intelligence for predictive modeling. Complemented by dedicated modules, AxSTREAM ensures robust validation of solutions and performance data. It serves not only to expedite technological development but also guarantees compatibility and includes steady technical support. In essence, AxSTREAM emerges as a much needed toolkit for holistic modeling and optimization of energy conversion and propulsion systems.
Interested in learning more about AxSTREAM? Get in touch! Email us at Sales@softinway.com to set up a private demo.
- SEO Powered Content & PR Distribution. Get Amplified Today.
- PlatoData.Network Vertical Generative Ai. Empower Yourself. Access Here.
- PlatoAiStream. Web3 Intelligence. Knowledge Amplified. Access Here.
- PlatoESG. Carbon, CleanTech, Energy, Environment, Solar, Waste Management. Access Here.
- PlatoHealth. Biotech and Clinical Trials Intelligence. Access Here.
- Source: https://blog.softinway.com/holistic-modeling-of-energy-conversion-propulsion-systems-using-0d-3d-approaches/
- :is
- :not
- :where
- $UP
- 1
- 2D
- 3d
- a
- About
- absolutely
- accessible
- accurate
- Additional
- Adds
- advanced
- advancements
- Aerospace
- AI
- AI models
- All
- Allowing
- allows
- also
- an
- analysis
- analyzing
- and
- approach
- approaches
- ARE
- artificial
- artificial intelligence
- AS
- At
- automatically
- avenues
- BE
- between
- Big
- Big Picture
- both
- Breaking
- BRIDGE
- build
- but
- button
- by
- CAN
- Capacity
- capture
- CFD
- characteristics
- COM
- combined
- combines
- combining
- compatibility
- complete
- complex
- component
- components
- comprehensive
- conditions
- connected
- considers
- context
- contribution
- Conversion
- Couple
- coupled
- course
- Creating
- cycle
- cycles
- data
- dedicated
- define
- Demo
- Derived
- Design
- designing
- detailed
- details
- determination
- Development
- different
- directly
- diverse
- doing
- down
- driving
- dynamics
- each
- easy
- Effective
- efficiency
- element
- elements
- emerges
- employing
- enables
- energy
- Energy Solutions
- Engine
- Engineers
- enhancing
- ensures
- ensuring
- essence
- essential
- Ether (ETH)
- evaluate
- exchange
- existing
- existing system
- expedite
- experiment
- exploration
- Face
- facilitate
- facilitating
- faithful
- Fields
- Figure
- Find
- fit
- flow
- fluid
- Focus
- For
- forefront
- Framework
- from
- Fuel
- full
- gap
- GAS
- generated
- generates
- generative
- get
- given
- good
- guarantees
- helps
- high-level
- highly
- holistic
- How
- However
- HTTPS
- ideal
- ideal fit
- import
- in
- includes
- Including
- increasingly
- influence
- Innovation
- innovative
- instance
- Integrates
- Integrating
- integration
- Intelligence
- interact
- interaction
- interactions
- interacts
- Interface
- into
- involved
- IT
- ITS
- lab
- learning
- levels
- leveraging
- Library
- Limited
- Look
- machine
- machine learning
- Machines
- MAKES
- Maps
- max-width
- May..
- Meet
- methodologies
- methods
- model
- modeling
- models
- Modules
- more
- most
- moves
- much
- multiple
- multitude
- must
- necessary
- needed
- network
- networks
- New
- of
- offering
- Offers
- on
- once
- ONE
- ones
- only
- operate
- operation
- optimization
- Optimize
- optimized
- optimizing
- Option
- or
- Others
- out
- path
- paths
- perform
- performance
- perspectives
- picture
- pivotal
- plants
- platform
- Platforms
- plato
- Plato Data Intelligence
- PlatoData
- power
- power plants
- precise
- Precision
- Predictions
- predictive
- preliminary
- press
- private
- process
- produce
- propulsion
- provides
- providing
- quest
- real
- real world
- realistic
- realm
- rely
- representation
- Requirements
- requires
- researchers
- robust
- rocket
- scientists
- secondary
- serves
- set
- significant
- Simple
- simplified
- simulate
- simulation
- simulations
- So
- Software
- solid
- Solutions
- sophisticated
- specific
- stand
- stands
- States
- steady
- Steam
- straightforward
- structures
- studies
- Study
- Studying
- such
- support
- sustainable
- Sustainable Energy
- system
- Systems
- Task
- Technical
- technical support
- technological
- test
- that
- The
- their
- Them
- then
- thereby
- These
- this
- though?
- Through
- to
- tool
- toolkit
- tools
- transportation
- turbine
- Turning
- tweak
- two
- under
- understanding
- unified
- unique
- us
- user-friendly
- users
- using
- validation
- various
- View
- Virtual
- ways
- which
- while
- with
- within
- Work
- world
- yet
- zephyrnet