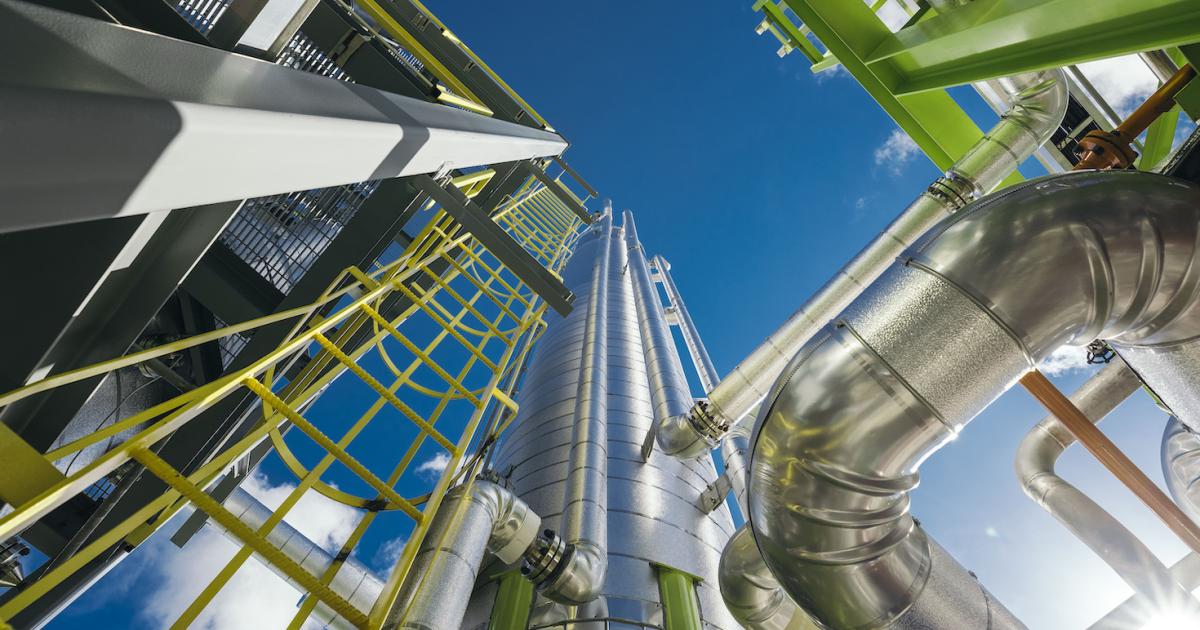
The $5 trillion global chemicals sector is a foundation of our modern economy. It’s also the largest industrial consumer of oil and gas and has the third-largest carbon footprint. Propped up by decades of inefficient, energy intensive and dirty processes, the chemicals industry is under intense pressure to clean up its act.
Founded seven years ago, Houston-based Solugen has developed a process that harnesses biology to produce a range of products, from plant nutrients to corrosion inhibitors, eliminating the carbon-intensive fossil fuel feedstocks and hazardous chemical waste streams associated with conventional petrochemicals.
In late October, the company announced that it is building a new 500,000-square-foot biomanufacturing facility, known as Bioforge 2, in Marshall, Minnesota. Scheduled for phase-one launch in the first half of 2025, Solugen’s second commercial facility marks the beginning of a new era for the chemicals industry, wherein a wide range of the chemicals can be produced at scale at a single plant with no carbon emissions or waste.
“One of the biggest challenges for the chemical industry is speeding up the pace of innovation to develop new catalysts for desired chemical transformations quickly,” said Karthish Manthiram, a professor of chemistry and chemical engineering at the California Institute of Technology. “Solugen has proven that their platform leads to fast results, alleviating this bottleneck.”
Expanding the market
The global green chemicals market was valued at $82.5 billion in 2022 and is predicted to have an annual growth rate of 12.1 percent between now and 2030. But it has struggled to come up with solutions that can reach commercial scale quickly.
A range of companies are attempting to change that. Origin Materials, which turns wood chips into precursors of polyethylene terephthalate, or PET, commonly used in plastic packaging, began operating its first commercial-scale facility in June. Meanwhile, Newlight Technologies has been harnessing the power of microbes at its plant in Huntington Beach, California, to capture greenhouse gases since 2020. The microbes produce a resin that can be used in foodware and textiles. Both startups have raised hundreds of millions of dollars in funding.
Solugen is distinguished by the versatility of its process and the speed at which it scales. While competitors produce a limited range of products, Solugen claims that its genetically engineered enzymes — biological catalysts that can facilitate the chemical reaction of one molecule to another while remaining unchanged themselves — can be designed to produce multiple molecules.
“The efficiency and scalability of our process mean we can provide our customers with the same chemistries they know and trust at a lower cost, higher performance and much more favorable environmental profile,” said Tom Richardson, interim chief commercial officer at Solugen.
Chemical processes can take well over a decade to go from concept to production, but Solugen has taken its flexible platform from a napkin-scribbled idea to not one but two commercial scale facilities in seven years.
Accelerated by AI
The company had its genesis during an innovation boom in the field of synthetic biology — the science that redesigns organisms for useful purposes by engineering them to have new abilities. Today, using artificial intelligence, Solugen can design enzymes at a rate unimaginable 10 years ago.
The process of producing chemicals is remarkably simple compared to traditional petrochemicals. Corn sugar is fed into a reactor, where it is converted by the enzymes into an energetically favorable intermediate. After that, more traditional chemical reactions transform the intermediate into the final product.
The third step is purification, where water and trace impurities are evaporated off to reach the customer-specified concentration.
While a traditional petrochemical process might turn 50 percent of its fossil fuel feedstock into the desired product, the Bioforge converts about 96 percent of its corn sugar feed. The team aims to push that up to 100 percent within a few years, Richardson said.
The whole process is carbon-negative because corn absorbs carbon from the atmosphere to grow, and the plant itself runs entirely on wind energy.
With the advent of Bioforge 2, the chemicals industry finally has a process that produces zero carbon emissions and no waste and can make a flexible range of products. In the long term, Solugen hopes to build a network of sustainable chemical plants that can operate much closer to consumers than hazardous petrochemicals ever could. All of this, Richardson said, will become part of a “decentralized bioeconomy.”
“We envision a world where you can have entirely carbon-negative cities where every single material that you can see, feel and touch can be produced with Solugen’s chemistry that is sequestering CO2 from the atmosphere,” Richardson said.
Other companies will start following in Solugen’s footsteps, said John Cumbers, founder and CEO of the synthetic biology professional network SynBioBeta: “Their success could serve as a beacon for other startups and innovators looking to harness the power of biology for industrial applications.”
- SEO Powered Content & PR Distribution. Get Amplified Today.
- PlatoData.Network Vertical Generative Ai. Empower Yourself. Access Here.
- PlatoAiStream. Web3 Intelligence. Knowledge Amplified. Access Here.
- PlatoESG. Carbon, CleanTech, Energy, Environment, Solar, Waste Management. Access Here.
- PlatoHealth. Biotech and Clinical Trials Intelligence. Access Here.
- Source: https://www.greenbiz.com/article/what-solugens-new-factory-means-future-green-chemicals
- :has
- :is
- :not
- :where
- $UP
- 1
- 10
- 100
- 12
- 2020
- 2022
- 2025
- 2030
- 50
- 500
- a
- abilities
- About
- absorbs
- Act
- advent
- After
- ago
- aims
- All
- also
- an
- and
- announced
- annual
- Another
- applications
- ARE
- artificial
- artificial intelligence
- AS
- associated
- At
- Atmosphere
- attempting
- BE
- Beach
- beacon
- because
- become
- been
- began
- Beginning
- between
- Biggest
- Billion
- biology
- biomanufacturing
- boom
- both
- build
- Building
- but
- by
- california
- CAN
- capture
- carbon
- carbon emissions
- catalysts
- ceo
- challenges
- change
- chemical
- chemicals
- chemistry
- chief
- Chips
- Cities
- claims
- clean
- closer
- co2
- come
- commercial
- commonly
- Companies
- company
- compared
- competitors
- concentration
- concept
- consumer
- Consumers
- conventional
- converted
- corrosion
- Cost
- could
- Customers
- decade
- decades
- decentralized
- Design
- designed
- desired
- develop
- developed
- Distinguished
- dollars
- during
- economy
- efficiency
- eliminating
- Emissions
- energy
- energy intensive
- engineered
- Engineering
- entirely
- environmental
- envision
- Era
- Ether (ETH)
- EVER
- Every
- facilitate
- facilities
- Facility
- factory
- FAST
- favorable
- Fed
- feel
- few
- field
- final
- Finally
- First
- flexible
- following
- For
- fossil
- Fossil fuel
- Foundation
- founder
- Founder and CEO
- from
- Fuel
- funding
- future
- GAS
- Genesis
- Global
- Go
- Green
- Grow
- Growth
- had
- Half
- harness
- Harnessing
- Have
- higher
- hopes
- HTTPS
- Hundreds
- hundreds of millions
- Huntington
- idea
- IEA
- in
- industrial
- industry
- inefficient
- Innovation
- innovators
- Institute
- Intelligence
- interim
- Intermediate
- into
- IT
- ITS
- itself
- John
- jpg
- Know
- known
- Late
- launch
- Leads
- Limited
- Long
- looking
- lower
- make
- Market
- material
- mean
- means
- Meanwhile
- might
- millions
- minnesota
- Modern
- molecule
- more
- much
- multiple
- network
- New
- no
- now
- october
- of
- off
- Officer
- Oil
- Oil and Gas
- on
- ONE
- operate
- operating
- or
- Other
- our
- over
- Pace
- packaging
- part
- percent
- performance
- pet
- plant
- plants
- plastic
- platform
- plato
- Plato Data Intelligence
- PlatoData
- power
- predicted
- pressure
- process
- processes
- produce
- Produced
- produces
- producing
- Product
- Production
- Products
- professional
- Professor
- Profile
- proven
- provide
- purposes
- Push
- quickly
- raised
- range
- Rate
- reach
- reaction
- reactions
- reactor
- remaining
- Resin
- Results
- runs
- Said
- same
- Scalability
- Scale
- scales
- scheduled
- Science
- Second
- sector
- see
- serve
- seven
- Simple
- since
- single
- Solutions
- speed
- start
- Startups
- Step
- streams
- success
- sugar
- sustainable
- synthetic
- Take
- taken
- team
- Technology
- term
- textiles
- than
- that
- The
- The Future
- their
- Them
- themselves
- they
- Third
- this
- to
- today
- tom
- touch
- trace
- traditional
- Transform
- transformations
- Trust
- TURN
- turns
- two
- under
- unimaginable
- used
- using
- valued
- versatility
- was
- Waste
- Water
- we
- WELL
- What
- which
- while
- whole
- wide
- Wide range
- will
- wind
- wind energy
- with
- within
- wood
- world
- years
- you
- zephyrnet
- zero