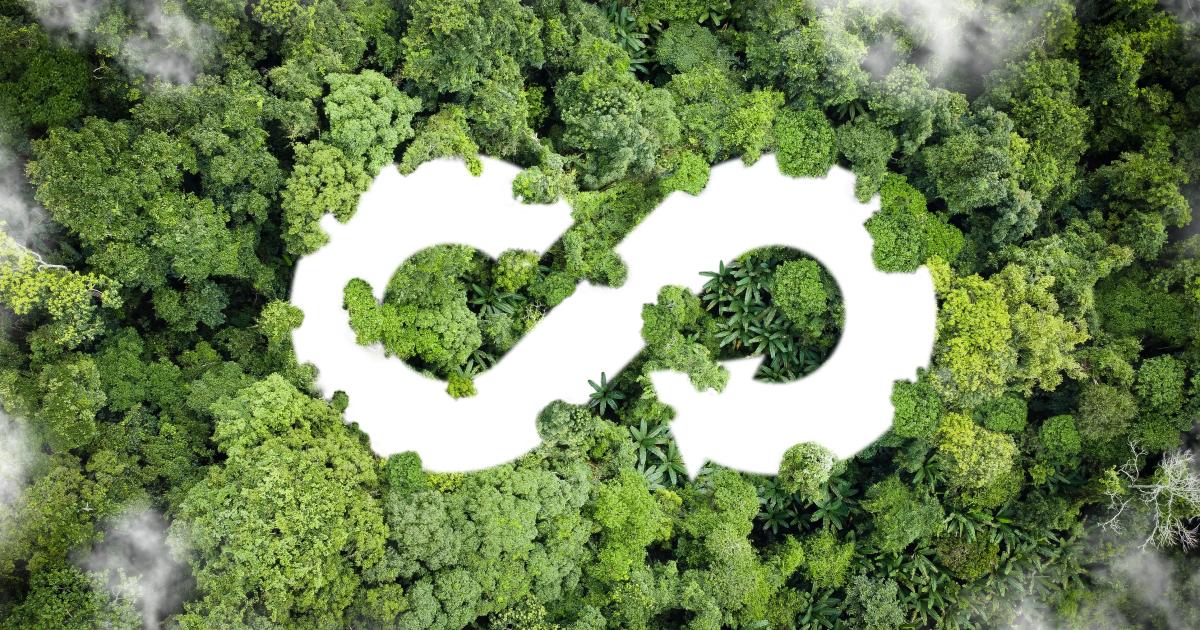
This article is sponsored by 3E.
Growing interest in circularity by product designers has big potential for helping companies achieve sustainability goals. Yet many organizations think of material transparency as a parallel goal rather than an integral part of circularity.
It is much easier and more glamorous to make bold claims about circularity — how a company will repurpose all its scrap materials, or how it will launch a new takeback program. Many of these statements lack details about the how — how will the take-back program work? How is a company prioritizing maintenance, repair and redistribution in its supply chain and business model? Often, this is because many of these steps are far into the future.
That’s why material transparency — which is determined in product design — often is left out of the conversation. One of the best ways to future-proof circularity efforts is to engage in rigorous materials transparency efforts during design so that future recycling efforts have the best chance to work with products that are taken back.
Material transparency defined
Material transparency is knowing what your product is actually made out of. A wood flooring company, for example, knows its product contains wood, an adhesive, a stain and a finish. That is certainly a step towards transparency; however, full product knowledge means knowing exactly what substances and chemical registry numbers make up that adhesive, stain and finish. A threshold of 100 parts per million (PPM) is standard for most material transparency goals.
Circularity cannot succeed without knowledge of product ingredients. Because of the inherent complexity of material transparency and its essential role in circularity, it is critical for companies to address as one of their first conversations on the path to implementing circularity.
However, many manufacturers are not fully aware of the chemicals that are in the goods that they make and sell. This is why the focus of mainstream recycling has historically revolved around goods that are largely homogenous in construction, such as plastic bottles, scrap metals and paper. These products are easy to identify, and their compositions are largely known and consistent among producers. But the circular economy is contingent on the maintenance, reuse, remanufacturing and recycling of complex, heterogeneous goods. Full product knowledge opens doors to circularity that previously never existed.
The benefits of material transparency
We have a lot to lose without material transparency, and a lot to gain from it through a circularity lens. Here are four benefits of embracing it:
- Worker safety: Material recycling is often a hands-on process. Complete knowledge of the chemicals found in a product can ensure that employers are aware of the risks associated with a given product and that workers are provided the correct PPE. Ideally, chemicals that pose a risk would be engineered out of the product to ensure that its recycling poses less risk to humans, but we have many existing products that don’t quite meet that expectation.
- Batch contamination: Only a small amount of a toxic substance is needed to contaminate an entire batch of materials eligible for recyclability. For recyclers whose bottom lines depend on the quality of their outputs and companies that depend on the availability of recycled materials, contaminated batches equate to slimmer margins, outright waste and a shortage of materials. Furthermore, all of our efforts in the creation of safer materials will be undone if they are implemented into a recycling ecosystem that bears a toxic legacy.
- Higher value: Recycled materials whose compositions are fully known and accessible have higher monetary and quality value because an element of mystery is removed. Buyers of recycled materials should be willing to pay more for materials whose compositions are fully known because there is no doubt regarding the material’s toxicity. Additionally, a key tenant of circularity is to keep materials in use at their highest value and recycle them into higher-value products. Product knowledge can better inform how it will perform in the useful life, re-manufacturing and recycling environments.
- Regulatory compliance: Chemical regulations are constantly changing, especially for firms that sell in a diversity of global arenas. Knowledge of chemical composition lowers the costs and time needed to remain compliant should a product be affected by a regulatory change. It also lowers the risk of fines, recalls and remediation expenses. Being in compliance reduces barriers against circular products and initiatives.
Strongly implied in the definitions and ideas of a circular economy is the notion that any materials that are used need to be safe for humans, non-humans and the environment, ensuring that hazardous materials are not endlessly recycled with unintended consequences. Essential to making this notion a reality is the recirculation of clean inputs. The journey towards material transparency is the process through which clean input use can be established. Without the capacity to verify that inputs into the circular economy are safe, the idea of the circular economy poses a greater threat to human and environmental wellbeing than existing manufacturing from virgin materials.
Product passports as a path toward transparency
Another challenge of material transparency is what to do with that information once it’s collected and how to ensure it’s being shared both internally within a manufacturer and externally to their suppliers. One solution is a “Digital Product Passport” or DPP, a term developed by the EU to describe the digital data associated with a particular product or material. A DPP would include formulation data, recycling and end-of-life instructions, and other product attributes. The goal of a DPP is to provide equal access to a form of universal digital data that can be exchanged without loss of information. Manufacturers and recycling facilities would ideally have a DPP for all materials in their product composition, providing the full visibility that circularity requires for its next steps.
Toxnot has already built the technological framework to create a Digital Product Passport for manufacturers today on the Toxnot Exchange, a place for manufacturers and suppliers to come together to manage the data needed to create sustainable, circular and regenerative products and engage with their customers on the topic. The platform improves information disclosure, reduces the reporting time burden and increases supplier incentives to start and maintain data disclosures. It equips manufacturers and suppliers with the ability to create and manage Digital Product & Material Passports. Anyone searching on the exchange can find and share Digital Product Passports created by any of their supply chain partners.
Corporate responsibility and challenging the status quo
Perhaps the biggest challenge that stands in the way of large-scale circularity is the long-standing status quo. Data secrecy, thin supplier profit margins and complex supply chains are standard in most industries and become a significant hindrance to attaining material transparency.
Corporate sustainability teams commonly have large goals and aspirations to make sweeping changes within their companies. To meet the sweeping circularity efforts that everyone hopes to achieve, companies need to better support and incentivize supply chain partners in the interest of planetary health.
- SEO Powered Content & PR Distribution. Get Amplified Today.
- PlatoAiStream. Web3 Data Intelligence. Knowledge Amplified. Access Here.
- Minting the Future w Adryenn Ashley. Access Here.
- Buy and Sell Shares in PRE-IPO Companies with PREIPO®. Access Here.
- Source: https://www.greenbiz.com/article/material-transparency-missing-link-scaling-circularity
- :has
- :is
- :not
- $UP
- 100
- a
- ability
- About
- access
- accessible
- Achieve
- actually
- Additionally
- address
- against
- All
- already
- also
- among
- amount
- an
- and
- any
- anyone
- ARE
- around
- article
- AS
- associated
- At
- attributes
- availability
- aware
- back
- barriers
- BE
- Bears
- because
- become
- being
- benefits
- BEST
- Better
- Big
- Biggest
- bold
- both
- Bottom
- built
- burden
- business
- business model
- but
- buyers
- by
- CAN
- cannot
- Capacity
- certainly
- chain
- chains
- challenge
- challenging
- Chance
- change
- Changes
- changing
- chemical
- chemicals
- circular economy
- claims
- come
- commonly
- Companies
- company
- complete
- complex
- complexity
- compliance
- compliant
- Consequences
- consistent
- constantly
- construction
- contains
- Conversation
- conversations
- correct
- Costs
- create
- created
- creation
- critical
- Customers
- data
- describe
- Design
- designers
- details
- determined
- developed
- digital
- disclosure
- Disclosures
- Diversity
- do
- Dont
- doors
- doubt
- during
- easier
- easy
- economy
- ecosystem
- efforts
- element
- eligible
- embracing
- employers
- endlessly
- engage
- ensure
- ensuring
- Entire
- Environment
- environmental
- environments
- equal
- especially
- essential
- established
- Ether (ETH)
- EU
- everyone
- exactly
- example
- exchange
- existing
- expectation
- expenses
- externally
- facilities
- far
- Find
- fines
- finish
- firms
- First
- Focus
- For
- form
- formulation
- found
- four
- Framework
- from
- full
- fully
- Furthermore
- future
- Gain
- given
- Global
- goal
- Goals
- goods
- greater
- hands-on
- Have
- Health
- helping
- here
- higher
- highest
- hindrance
- historically
- hopes
- How
- How To
- However
- HTTPS
- human
- Humans
- idea
- ideas
- identify
- if
- implemented
- implementing
- implied
- improves
- in
- Incentives
- incentivize
- include
- Increases
- industries
- inform
- information
- inherent
- initiatives
- input
- inputs
- instructions
- integral
- interest
- internally
- into
- IT
- ITS
- journey
- jpg
- Keep
- Key
- Knowing
- knowledge
- known
- Lack
- large
- large-scale
- largely
- launch
- left
- Legacy
- Lens
- less
- Life
- lines
- LINK
- long-standing
- lose
- loss
- Lot
- made
- Mainstream
- maintain
- maintenance
- make
- Making
- manage
- Manufacturer
- Manufacturers
- manufacturing
- many
- margins
- material
- materials
- means
- Meet
- Metals
- million
- missing
- model
- Monetary
- more
- most
- much
- Mystery
- Need
- needed
- never
- New
- next
- no
- Notion
- numbers
- of
- often
- on
- once
- ONE
- only
- opens
- or
- organizations
- Other
- our
- out
- Paper
- Parallel
- part
- particular
- partners
- parts
- passport
- path
- Pay
- perform
- Place
- plastic
- platform
- plato
- Plato Data Intelligence
- PlatoData
- poses
- potential
- PPE
- previously
- prioritizing
- process
- Producers
- Product
- product design
- Products
- Profit
- Program
- provide
- provided
- providing
- quality
- rather
- Reality
- recycling
- reduces
- regarding
- regenerative
- registry
- regulations
- regulatory
- remain
- Removed
- repair
- Reporting
- requires
- responsibility
- reuse
- revolved
- rigorous
- Risk
- risks
- Role
- safe
- safer
- Safety
- scaling
- searching
- sell
- Share
- shared
- shortage
- should
- significant
- small
- So
- solution
- Sponsored
- standard
- stands
- start
- statements
- Status
- Step
- Steps
- substance
- succeed
- such
- suppliers
- supply
- supply chain
- Supply chains
- support
- Sustainability
- sustainable
- teams
- technological
- tenant
- than
- that
- The
- The Future
- their
- Them
- There.
- These
- they
- think
- this
- threat
- threshold
- Through
- time
- to
- today
- together
- topic
- toward
- towards
- Transparency
- Universal
- use
- used
- value
- verify
- Virgin
- visibility
- Waste
- Way..
- ways
- we
- wellbeing
- What
- which
- whose
- why
- will
- willing
- with
- within
- without
- wood
- Work
- workers
- would
- yet
- Your
- zephyrnet