A first-of-its-kind project under construction at a 51-year-old Coca-Cola bottling facility in Elmsford, New York, is notable both for how it will improve the site’s energy reliability and how it will capture carbon dioxide during production to carbonate Sprite, Coke and Fanta made there.
The “quadgeneration” system being installed by Clarke Energy (a division of Kohler Co.) will enable Liberty Coca-Cola Beverages’ 21.5-acre site to generate its own electricity, while also powering heating and cooling processes such as creating steam for sanitation and chilling beverages before they’re bottled. It will also support a new system that will let Liberty use self-recovered carbon dioxide to carbonate its beverages rather than trucking the gas in from elsewhere.
How the system works
At the heart of the installation, scheduled to be up and working in December, are two Jenbacher reciprocating engines fed by an existing gas pipeline that serves the site. This is not a small-scale operation: It produces roughly 41 million cases of beverages annually distributed to restaurants, retailers and supermarkets in five states including New Jersey, New York and Pennsylvania. The company is the largest family-owned producer and distributor for Coca-Cola in the Northeast U.S.
A growing number of industrial sites are using cogeneration systems to simultaneously produce electricity and heat energy. Research firm Guidehouse Insights estimates the global market at about $20 billion in 2023, with the capacity of these systems growing at a compound annual growth rate of about 5 percent between 2019 and 2028.
Quadgeneration technologies — which add carbon capture features to the energy generation processes — are most common in greenhouses, where the CO2 is used to encourage plant growth, said Guidehouse Senior Research Analyst Peter Marrin. “However, another promising market is the food and beverage industry, where CO2 is the most common compressed gas used,” he said.
But the sort of application being installed by Liberty is still relatively unique, according to Liberty and Clarke: While similar equipment is operational in Europe and Africa, it’s the first time the technology is being deployed in North America.
“This complex technology will substantially reduce Liberty’s carbon emissions through high-efficiency local energy production,” said Clarke Energy CEO Jamie Clarke in a statement. “With the benefits of the recent Inflation Reduction Act and increased price of CO2 globally, this provides many opportunities for carbon capture technologies in the United States.”
While Liberty’s co-owner, Paul Mulligan, declined to disclose the cost of the project, he said overall the investment should pay for itself within 3.5 years and the company was able to tap tax incentives made possible by the Inflation Reduction Act. Looking ahead, the installation will help the facility ensure a more reliable source of power as the New York grid mix transitions to renewable sources. Ultimately, the system will provide an estimated 1.7 megawatts of electricity, enough to cover the site’s entire power demand. From an emissions reduction standpoint, it will eliminate about 200 deliveries of carbon dioxide currently brought to the site each year via truck.
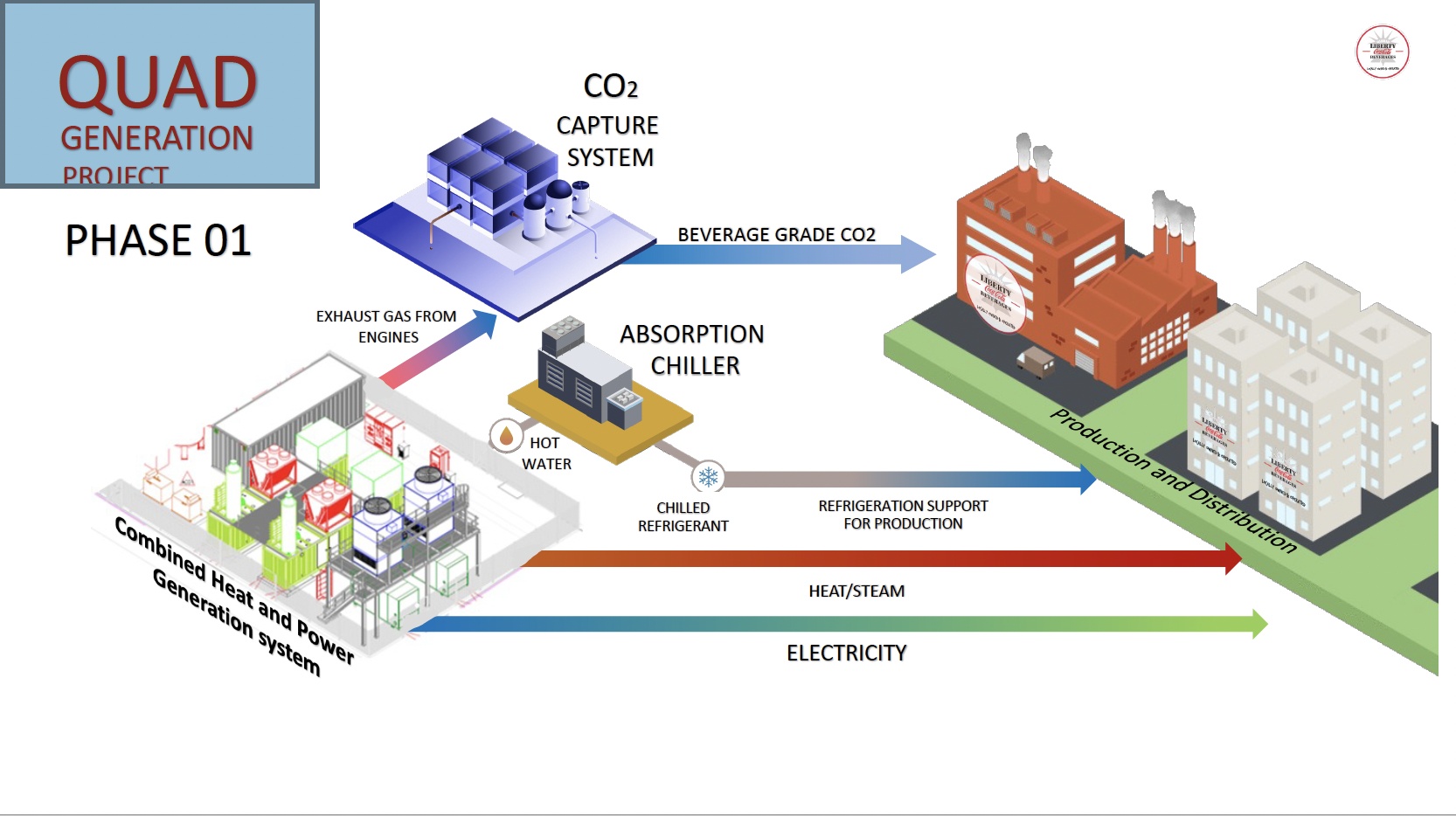
How Liberty got the idea
Many factors inspired this project, which took almost three years to pull off from planning to commissioning — including sporadic blackouts that have become more common in New York state. “This project was approved because it took us off the grid,” said Dylan Penn, senior manager of operations engineering for Liberty.
The company’s production team realized early that it was solving for two related things — the need to reduce atmospheric CO2 while simultaneously ensuring an adequate supply of CO2 purified to food-grade standards. Carbon dioxide is the most commonly used gas in the food and beverage sector, and the U.S. industry faced shortages during 2022 that inspired more companies to think differently.
The company considered many options as part of the request for proposals, including hydrogen fuel cells. The facility’s existing gas line and the potential to upgrade the engines to alternative fuel sources in the future were factors in the selection, Penn said.
Another big consideration was whether integrating the engines would disrupt the existing bottling lines, but Penn said Liberty wasn’t forced to relocate existing equipment. The biggest change in store is the process by which the captured CO2 will be purified and stored in tanks that can accommodate a roughly seven- to 10-day supply.
Aside from the technical evaluations, Liberty spent months working with local officials to earn the approvals — several boards reviewed and approved variances for the towers to absorb the CO2 as well as overall changes to the site to add the new engines. Those talks are ongoing as Liberty moves closer to flipping the system on by January. That’s important for any company considering a similar option, Penn said. “We live in our backyard. We are neighbors of our neighbors that live with the impact of this activity.”
This is part of broader sustainability efforts
Innovations by its bottlers are integral to Coca-Cola’s 5-year-old World Without Waste strategy, which includes goals for making 100 percent of the company’s packaging recyclable by 2025, working toward a one-for-one collection system for Coca-Cola cans and bottles, and collaborating with customers, governments and other organizations to get the job done.
Liberty participates in Coca-Cola bottler gatherings to share best practices toward meeting those goals, and its quadgeneration bet is charting a new course, according to Mulligan.
So far, he said the company has invested more than $60 million in its corporate sustainability efforts. For example, Liberty was the first U.S. soft-drink manufacturer to replace the plastic rings that hold multipacks of cans together with a paperboard alternative called the KeelClip; it transitioned to clear bottles from green in order to improve recycling; and it invested in XCycler systems to compress broken and damaged products — what once took 22 truckloads to remove from its plants now takes just one. Liberty last year inked a deal with renewable natural gas company Clean Energy Fuels that covers about 250 trucks in New York and Philadelphia. The move will reduce emissions by about 300 percent compared with diesel, according to the companies.
“If you really authentically care, you will do the right thing,” Mulligan said.
- SEO Powered Content & PR Distribution. Get Amplified Today.
- PlatoData.Network Vertical Generative Ai. Empower Yourself. Access Here.
- PlatoAiStream. Web3 Intelligence. Knowledge Amplified. Access Here.
- PlatoESG. Automotive / EVs, Carbon, CleanTech, Energy, Environment, Solar, Waste Management. Access Here.
- PlatoHealth. Biotech and Clinical Trials Intelligence. Access Here.
- ChartPrime. Elevate your Trading Game with ChartPrime. Access Here.
- BlockOffsets. Modernizing Environmental Offset Ownership. Access Here.
- Source: https://www.greenbiz.com/article/coca-cola-bottler-will-capture-carbon-dioxide-put-fizz-its-drinks
- :has
- :is
- :not
- :where
- $UP
- 1
- 100
- 15%
- 200
- 2019
- 2023
- 2025
- 2028
- 22
- 250
- 300
- 7
- a
- Able
- About
- accommodate
- According
- Act
- activity
- add
- africa
- ahead
- also
- alternative
- america
- an
- analyst
- and
- annual
- Annually
- Another
- any
- Application
- approvals
- approved
- ARE
- AS
- At
- atmospheric
- authentically
- BE
- because
- become
- before
- being
- benefits
- BEST
- best practices
- Bet
- between
- BEVERAGE
- Beverages
- Big
- Biggest
- Billion
- both
- bottling
- broader
- Broken
- brought
- but
- by
- called
- CAN
- Capacity
- capture
- captured
- carbon
- carbon capture
- carbon dioxide
- carbon emissions
- care
- cases
- Cells
- Center
- ceo
- change
- Changes
- charting
- clean energy
- clear
- click
- closer
- CO
- co2
- coca-cola
- collaborating
- collection
- Common
- commonly
- Companies
- company
- Company’s
- compared
- complex
- Compound
- consideration
- considered
- considering
- construction
- Corporate
- Cost
- course
- cover
- covers
- Creating
- Currently
- Customers
- data
- deal
- December
- Deliveries
- Demand
- deployed
- diesel
- Disclose
- Disrupt
- distributed
- distributor
- Division
- do
- done
- drinks
- during
- each
- Early
- earn
- efforts
- electricity
- eliminate
- elsewhere
- Emissions
- enable
- encourage
- energy
- Engineering
- Engines
- enough
- ensure
- ensuring
- Entire
- equipment
- estimated
- estimates
- Ether (ETH)
- Europe
- evaluations
- example
- existing
- faced
- Facility
- factors
- far
- Features
- Fed
- Firm
- First
- first time
- five
- food
- For
- from
- Fuel
- fuel cells
- fuels
- future
- GAS
- gas pipeline
- gatherings
- generate
- generation
- get
- Global
- global market
- Globally
- Goals
- Governments
- Green
- Grid
- Growing
- Growth
- Have
- he
- Heart
- help
- hold
- How
- However
- HTTPS
- hydrogen
- Hydrogen Fuel
- if
- Impact
- important
- improve
- in
- Incentives
- includes
- Including
- increased
- industrial
- industry
- inflation
- inked
- insights
- inspired
- installation
- integral
- Integrating
- invested
- investment
- IT
- ITS
- itself
- Jamie
- January
- Jersey
- Job
- just
- just one
- largest
- Last
- Last Year
- Liberty
- Line
- lines
- live
- local
- looking
- made
- Making
- manager
- Manufacturer
- many
- Market
- meeting
- million
- mix
- months
- more
- most
- move
- moves
- Natural
- Natural Gas
- Need
- neighbors
- New
- New Jersey
- New York
- New York state
- North
- north america
- notable
- now
- number
- of
- off
- officials
- on
- once
- ONE
- ongoing
- operation
- operational
- Operations
- opportunities
- Option
- Options
- order
- organizations
- Other
- our
- overall
- own
- packaging
- part
- participates
- Paul
- Pay
- Penn
- Pennsylvania
- percent
- Peter
- philadelphia
- pipeline
- planning
- plants
- plastic
- plato
- Plato Data Intelligence
- PlatoData
- possible
- potential
- power
- Powering
- practices
- presentation
- price
- process
- processes
- produce
- producer
- produces
- Production
- Products
- project
- promising
- Proposals
- provide
- provides
- put
- Rate
- rather
- realized
- really
- recent
- recycling
- reduce
- reduction
- related
- relatively
- reliability
- reliable
- remove
- Renewable
- replace
- request
- research
- Restaurants
- retailers
- reviewed
- right
- roughly
- s
- Said
- scheduled
- sector
- selection
- senior
- serves
- several
- Share
- should
- similar
- simultaneously
- site
- Sites
- Solving
- Source
- Sources
- spent
- standards
- standpoint
- State
- Statement
- States
- Steam
- Still
- store
- stored
- substantially
- such
- supply
- support
- Sustainability
- system
- Systems
- takes
- Talks
- Tanks
- Tap
- tax
- team
- Technical
- Technologies
- Technology
- than
- that
- The
- The Future
- There.
- These
- thing
- things
- think
- this
- those
- three
- Through
- time
- to
- together
- took
- toward
- transitions
- truck
- Trucking
- Trucks
- two
- u.s.
- Ultimately
- under
- unique
- United
- United States
- upgrade
- us
- use
- used
- using
- via
- was
- Waste
- we
- WELL
- were
- What
- whether
- which
- while
- Wikipedia
- will
- with
- within
- without
- working
- world
- would
- year
- years
- york
- you
- zephyrnet