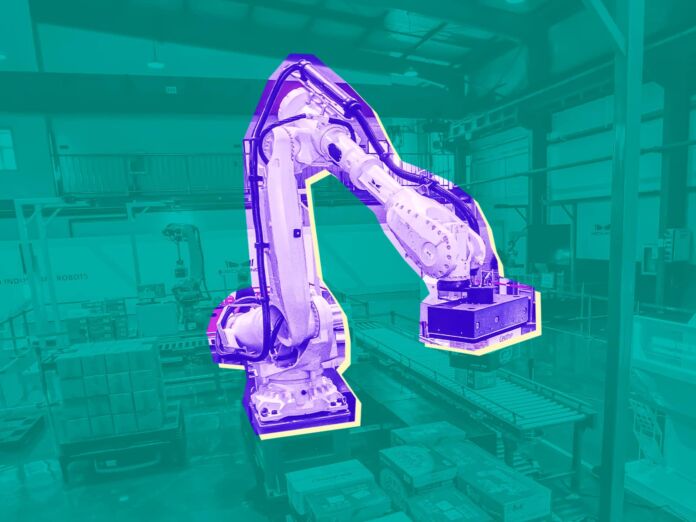
This past spring, Augury conducted the inaugural report “The State of Production Health 2023” wherein 500 manufacturing stakeholders – VPs and higher – offered their views on the current state of manufacturing. The result identifies key challenges, trends, and best practices as manufacturers try to balance the competing demands of profits, people, and the planet.
Many manufacturers are feeling more confident as they apply more Industry 4.0 technologies. However, if one looks more closely at the numbers, it also becomes clear that while AI is becoming the norm, not everyone is harnessing its full potential.
Industry veteran and advisor Scott Reed, who spent over 30 years as a changemaker executive in the building materials industry, talks about what struck him – and surprised him – most about the report’s findings.
Manufacturing Remains the Same
In many ways, the state of manufacturing hasn’t changed much in the last 50 years, according to Scott. “Certainly, in terms of objectives, it’s the same story: getting product out of the door in the most efficient way possible. But in terms of technological advances, the tools have become much more powerful through the evolutions of programs dedicated to continuous improvement such as TQM, Six Sigma, Lean, and TPS, and over time developed into what we now call digital transformation,” says Scott.
“Today, you can hit metrics you only dreamed of a few years ago. We would never imagine hitting 98 percent machine availability – the juice was just not worth the squeeze. But now we have the tools to get us there.”
“This doesn’t change the fact that to get anywhere, you need a plan. You need to, what I call, ‘ready the environment’ where all teams are all purposefully aligned and prepared in directing and managing change,” says Scott. “Especially now when it’s not getting any easier.
You have this never-ending need for efficiency and cost reduction, knowledge transfer issues as we try to replace an aging workforce, upskilling plant-floor workers while also improving safety, creating and attaining sustainability goals, meeting increased demand with a recovering supply chain, and so on… It’s a balancing act that gets more complex every year.”
Happily, the report shows an all-around optimism in how AI and automation can help with the state of manufacturing particularly when it comes to the workforce. “Despite the widespread opinion that AI and automation are ‘stealing jobs,’ 80 percent of respondents say technology adoption will have a positive impact on workforce upskilling efforts. Of those, 12 percent say that it will have a significant positive impact,” according to the report.
Manufacturers Unaware of True Potential
While 70 percent of the respondents believed they were meeting their production potential, other findings seem to contradict this confidence – with 35 percent still citing machine health as a key concern and only 21 percent being able to quantify their AI investment in production health.
“As sad as it is, these numbers suggest that chaos exists in many operations – that they are still too busy with day-to-day firefighting,” says Scott. “There may also be a lack of standards and operational discipline as well as competing functional priorities and objectives.
Simply put, everyone should understand their Asset Capacity, Utilized Capacity, and Realized Capacity as related to the maximum allowed production rate, maximum available hours and scheduled hours, and production losses (downtime, slow time, and quality waste). Yes, this is OEE and Utilization. However, if you don’t know the magnitude of the entitlement, you have no clue where and how far the North Star lies ahead.”
Production is Health Rising
Meanwhile, production health – still a relatively new term – is attracting as much AI investment as the supply chain. Production health is increasingly seen, according to the report, as “the foundation for balancing competing production demands, meeting upskilling needs, and achieving sustainability goals.”
“This totally makes sense,” says Scott. “This idea of production health can really help manufacturers tackle their problems. It rolls everything under one interconnected umbrella: material health, process health, machine health, product health, and people health.”
The Big Picture: Everything is Connected
With 26 percent of the respondents still regarding sustainability as a hindrance to hitting productivity goals, it’s still a good idea to look at the “big picture” of the state of manufacturing, including all the interrelationships. As the report puts it: “Optimizing machines and processes for cleaner, less wasteful production also optimizes them for efficiency, safety, uptime, and capacity, which all lead to more profitable operations.”
“I’m actually very optimistic about the future of our industry,” Scott says. “But the C-Suite really needs to understand what their company is striving for. And then they need to clearly communicate that with the rest of the organization. If it’s not clear in the heads of management, it will get more confusing as you go top-down. And there are no tools – AI or otherwise – that will solve that.”
“People are too focused on their particular pain points. They have a list of 25 priorities but still can’t articulate what’s most important. But the good news in this report is how these different challenges are not mutually exclusive – they’re very much inclusive.”
- SEO Powered Content & PR Distribution. Get Amplified Today.
- PlatoData.Network Vertical Generative Ai. Empower Yourself. Access Here.
- PlatoAiStream. Web3 Intelligence. Knowledge Amplified. Access Here.
- PlatoESG. Automotive / EVs, Carbon, CleanTech, Energy, Environment, Solar, Waste Management. Access Here.
- PlatoHealth. Biotech and Clinical Trials Intelligence. Access Here.
- ChartPrime. Elevate your Trading Game with ChartPrime. Access Here.
- BlockOffsets. Modernizing Environmental Offset Ownership. Access Here.
- Source: https://www.iotforall.com/the-state-of-production-health-2023
- :is
- :not
- :where
- 1
- 12
- 2023
- 25
- 26
- 30
- 35 percent
- 50
- 50 Years
- 500
- 70
- 80
- 98
- a
- Able
- About
- According
- achieving
- Act
- actually
- Adoption
- advances
- Aging
- ago
- ahead
- AI
- aligned
- All
- all-around
- allowed
- also
- an
- and
- any
- anywhere
- Apply
- ARE
- AS
- asset
- At
- attracting
- Automation
- availability
- available
- Balance
- balancing
- BE
- become
- becomes
- becoming
- being
- believed
- BEST
- best practices
- Big
- Big Picture
- Building
- Building Materials
- busy
- but
- C-suite
- call
- CAN
- Capacity
- chain
- challenges
- change
- changed
- Chaos
- clear
- clearly
- closely
- comes
- communicate
- company
- competing
- complex
- Concern
- conducted
- confidence
- confident
- confusing
- continuous
- Cost
- cost reduction
- Creating
- Current
- Current state
- day-to-day
- dedicated
- Demand
- demands
- developed
- different
- digital
- directing
- Doesn’t
- Dont
- Door
- downtime
- easier
- efficiency
- efficient
- efforts
- Entitlement
- Every
- everyone
- everything
- evolutions
- Exclusive
- executive
- exists
- fact
- far
- few
- findings
- focused
- For
- Foundation
- full
- functional
- future
- get
- getting
- Go
- Goals
- good
- Harnessing
- Have
- heads
- Health
- help
- higher
- him
- hindrance
- Hit
- hitting
- HOURS
- How
- However
- HTTPS
- i
- idea
- identifies
- if
- imagine
- Impact
- important
- improvement
- improving
- in
- Inaugural
- Including
- Inclusive
- increased
- increasingly
- industry
- interconnected
- into
- investment
- iot
- issues
- IT
- ITS
- Jobs
- jpg
- just
- Key
- Know
- knowledge
- Lack
- Last
- lead
- less
- lies
- List
- Look
- LOOKS
- losses
- machine
- Machines
- MAKES
- management
- managing
- Manufacturers
- manufacturing
- many
- material
- materials
- max-width
- maximum
- May..
- meeting
- Metrics
- more
- most
- much
- mutually
- Need
- needs
- never
- New
- news
- no
- North
- now
- numbers
- objectives
- of
- offered
- on
- ONE
- only
- operational
- Operations
- Opinion
- Optimism
- Optimistic
- Optimizes
- or
- organization
- Other
- otherwise
- our
- out
- over
- Pain
- Pain points
- particular
- particularly
- past
- People
- percent
- picture
- plan
- planet
- plato
- Plato Data Intelligence
- PlatoData
- points
- positive
- possible
- potential
- powerful
- practices
- prepared
- problems
- process
- processes
- Product
- Production
- productivity
- profitable
- profits
- Programs
- put
- Puts
- quality
- Rate
- realized
- really
- recovering
- reduction
- regarding
- related
- relatively
- remains
- replace
- report
- respondents
- REST
- result
- rolls
- Safety
- same
- say
- says
- scheduled
- scott
- seem
- seen
- sense
- should
- Shows
- Sigma
- significant
- SIX
- slow
- So
- SOLVE
- spent
- spring
- Squeeze
- stakeholders
- standards
- Star
- State
- Still
- Story
- such
- suggest
- supply
- supply chain
- surprised
- Sustainability
- tackle
- Talks
- teams
- technological
- Technologies
- Technology
- term
- terms
- that
- The
- The Future
- The State
- their
- Them
- then
- There.
- These
- they
- this
- those
- Through
- time
- to
- too
- tools
- TOTALLY
- tps
- transfer
- Trends
- true
- try
- umbrella
- under
- understand
- upskilling
- uptime
- us
- utilized
- very
- veteran
- views
- was
- Waste
- Way..
- ways
- we
- WELL
- were
- What
- when
- which
- while
- WHO
- widespread
- will
- with
- workers
- Workforce
- worth
- would
- year
- years
- yes
- you
- zephyrnet