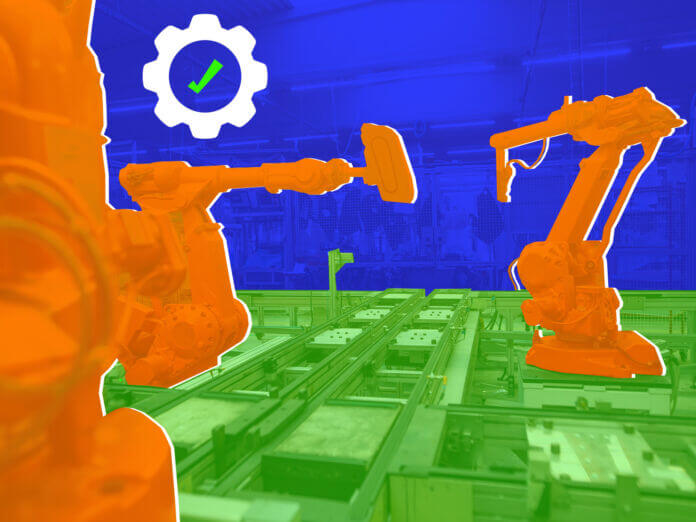
To prevent potential breakdowns, employee injuries, and production loss, more and more companies familiarize themselves with remote asset monitoring. They try to run predictive maintenance systems to catch problems before they occur in manufacturing, minimizing the risks for employee and customer dissatisfaction, and preventing money loss.
Luckily, the 21st century offers modern and effective solutions for predictive maintenance in manufacturing to implement in different industries.
Recently, Prylada has conducted a series of customer development interviews, where we addressed experts from the manufacturing industry. Our team set the goal to collect valuable information about asset monitoring and technology adoption challenges in the industry, and how companies solve them.
During the interviews, we discussed the current state of the market, the most bothersome issues, competition, and recommendations for effective development within the industry.
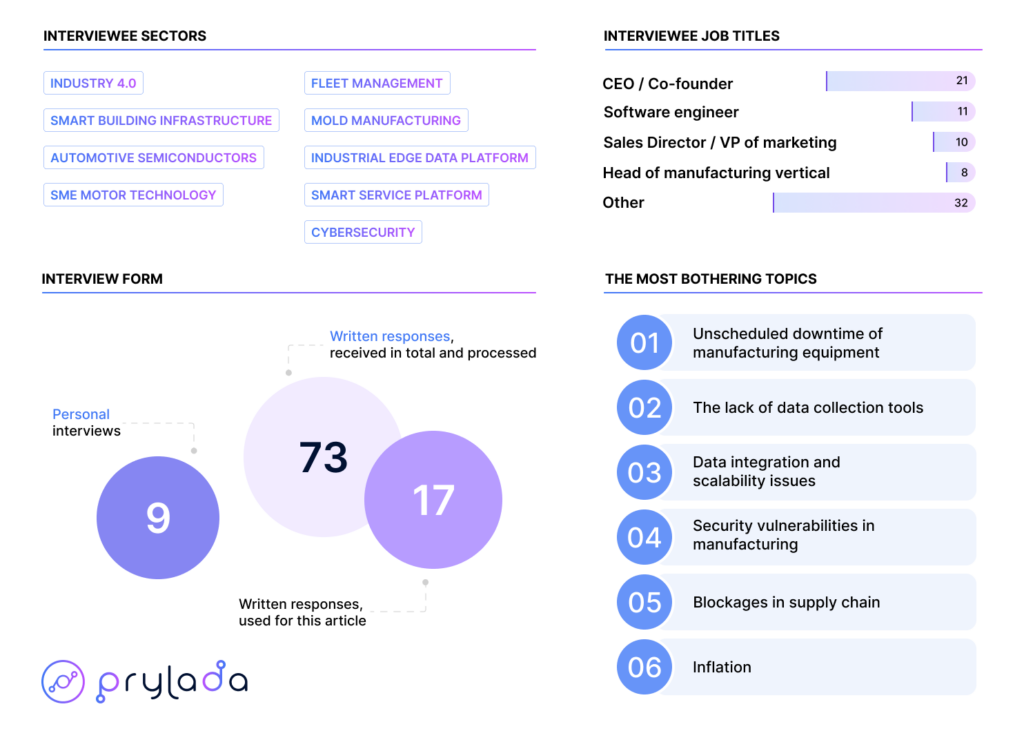
How Has the Manufacturing Market Changed Over the Last 5 Years?
Consumer preferences toward product customization, competitive pricing, and the best delivery frames have become the main drivers for manufacturing companies to rethink their working approach. To keep up with the modern demands, they need to boost productivity by implementing digital technologies. These technologies include digitally enabled sustainability solutions, digital twins, autonomous mobile robots, augmented reality, AI, and machine learning.
“The reality of the past was that manufacturers were working overtime, they were doing stuff very manual, and they were not being supported. They simply got the job done, and now that shifted to where these manufacturing companies have gone from just getting it done to where they need to launch big digital transformation initiatives.”
– Richard Lebovitz, CEO of LeanDNA
Manufacturers started thinking from the following perspective:
- We need to be a lot more connected
- We need to have better visibility not only into the issues that we are struggling with but also what are the actions we need to take.
The overall picture shifted from work as it is to digital transformation prioritizing actions. In addition, COVID-19 has highlighted the importance of strong and adaptable supply networks. Significant losses from the pandemic’s unforeseen consequences led industrial companies to reconsider their current business strategies. As a result, they aimed to optimize existing processes and reduce their dependence on external factors, thus enhancing the resilience to force-majeure situations.
The focus on sustainability becomes a driving force for the greater use of smart IoT technologies, making the manufacturing industry smarter, more efficient, and sustainable, while also improving employee well-being. It’s happening through automation and digital transformation, and it’s leveraging predictive analytics to drive better recommendations. In turn, this gives us a better understanding of what the bottlenecks are, and what the challenges are.
On the other hand, the process of adopting new smart technologies has become more intricate and time-consuming. Supply chain challenges and personnel shortages have led the entire C-Suite to engage deeply with operational matters and decisions at the floor level. This resulted in a greater number of stakeholders who needed to comprehend the risks, align on anticipated value benefits, and balance these considerations against other company initiatives.
The rapid pace of technological advancements in areas such as automation, artificial intelligence, and the Internet of Things requires manufacturers to adapt and integrate new technologies into their operations.
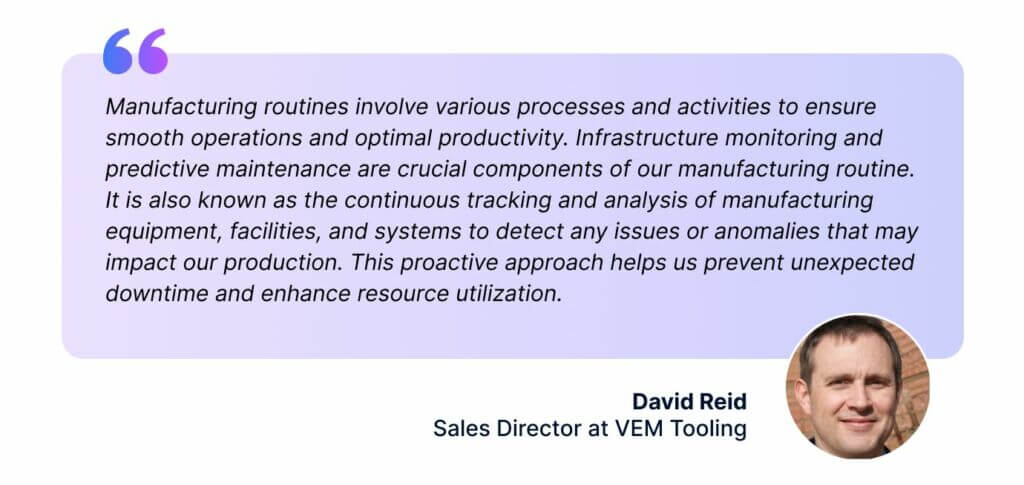
However, the transition to new asset monitoring technologies can be complex and costly, requiring upskilling the workforce and ensuring compatibility with existing systems.
We gathered the most common challenges and barriers associated with this transition, as our interviewees shared with us. Placed first are the points we hear most frequently. This does not necessarily mean that they are the most critical ones, but it does indicate their prevalence. Let’s get started.
Unscheduled Downtime of Manufacturing Equipment
Manufacturing for modern devices involves high-precision complex processes and sophisticated equipment. Unscheduled manufacturing equipment downtime can have a very high cost due to yield loss and lost production time. Recent innovations in predictive maintenance can greatly help reduce the loss of productivity and can save a lot of effort and time.
One of the techniques successfully employed for predictive maintenance in manufacturing uses the analysis of large amounts of fault data, maintenance, and trace data. To strengthen the quality of data used, parameters like process, timestamp, and detailed component information are attributed to fault models to create robust data sets. Several large semiconductor manufacturing companies have reported using such techniques as part of their predictive maintenance models to improve yield.
Challenges remain, as a lot of complex processes tend to have frequent drifts and shifts. Specific parameters are adjusted in between runs to keep the process on target. Techniques like virtual sensors that monitor and capture the parameter configuration in real time can be used to enable proper control. This is an active research area currently, and researchers are actively exploring new techniques including artificial intelligence.
The Lack of Data Collection Tools
As limited asset visibility means increased maintenance and replacement costs, many manufacturers already struggle to capture basic machine data. This data typically includes temperature, vibration, velocity, and other performance indicators.
For many companies, however, investing in data collection tools can be a costly endeavor. This is why they prefer working with available resources, which can hinder development in many ways.
Manufacturers looking to use real-time data for asset monitoring need a tool that can automatically connect and collect data from any source. Ideally, it should also be able to normalize and manage the data, perform analytics, and easily integrate with third-party applications and cloud computing platforms.
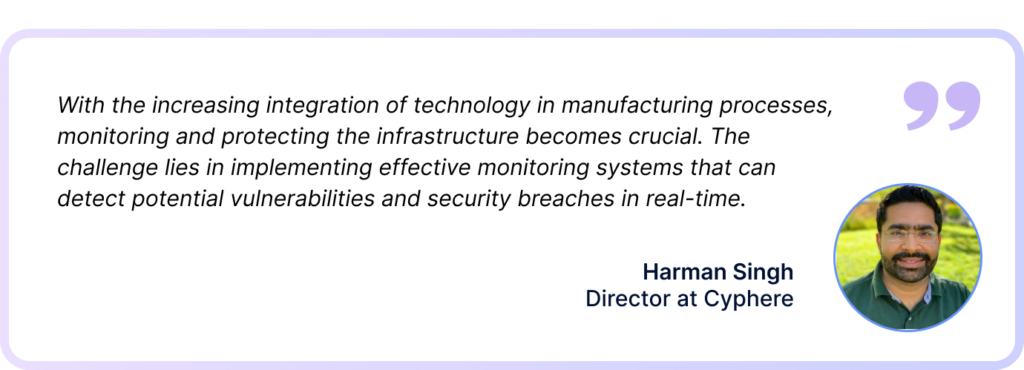
Data Integration and Scalability Issues
Manufacturing infrastructure often comprises diverse systems, such as machinery, production lines, and utility systems. These systems may have been implemented at different times, using varying technologies. Moreover, each system generates data in its format, making integration with third-party systems a formidable task. Inconsistent formats, missing values, and inaccuracies hinder effective integration.
As manufacturing facilities and processes evolve, the data landscape grows. Systems must be scalable to accommodate increasing data volumes. Ensuring seamless and efficient data flow across the manufacturing operations without overwhelming the monitoring infrastructure is essential. Reaching it is possible by investing in modern tools and prioritizing data quality.

Security Vulnerabilities in Manufacturing
The manufacturing industry faces an ever-evolving landscape of cyber threats, from ransomware attacks to supply chain vulnerabilities. In the context of hardware, counterfeit products of lower quality were thought to be a major issue for semiconductors, while chips remained relatively unaffected by security-related issues.
However, in the last few years, attackers have found methods to exploit the intricate semiconductor manufacturing process. They have attempted to manipulate chip architecture by introducing malicious logic through hardware Trojans. Attackers intend these Trojans for either Denial of Service (DoS) or data theft. Notably, Syria reported a major Trojan attack, where attackers embedded a Trojan called “Kill Switch” in a chip to disable the Syrian air defense system, allowing them to execute an airstrike.
In the last few years, manufacturers expanded the use of data analytics concepts based on machine learning and Internet-of-Things (IoT), to ensure that their equipment is appropriately protected. In these techniques, they first initialize equipment for all the monitoring parameters and then apply machine learning algorithms to these parameters, to predict the parameter class on the output. If the results (output) do not match the prediction, manufacturers may flag the equipment.
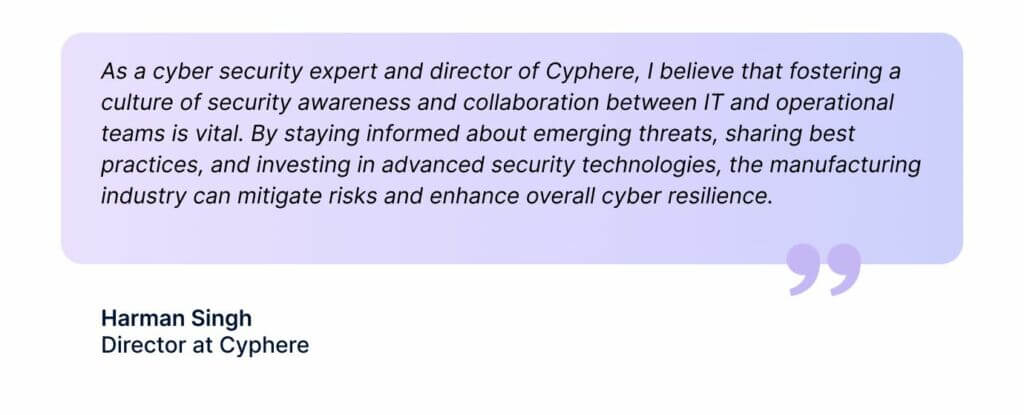
Other Obstacles Preventing Sustainable Manufacturing
Blockages in the Supply Chain
Manufacturers historically faced several difficulties, and 2024 predictions show more of the same. As global trade becomes more complex, producers must prepare to withstand unexpected or sudden interruptions in their supply networks.
According to some of our interviewees, interruptions in supply chains will continue to be one of the most significant difficulties facing the industry for the foreseeable future. Currently, inventories are at their lowest levels in decades, indicating that certain products cannot be manufactured at this time. The severe scarcity of semiconductors from Taiwan, China, and other offshore companies has compelled some automotive manufacturing facilities to close. Domestic production has also been experiencing difficulties.
Inflation
In 2023, inflation was close to double digits due to rising demand and insufficient supply in all major economies. Next year, prices for key manufacturing inputs like aluminum, oil, and steel will increase even more, increasing the pressure on businesses already trying to reduce costs without sacrificing quality.
Locating resources and investments for asset monitoring automation during inflation is hard. But manufacturers must not ignore the potential it brings to the industry. It can help reduce manual errors and speed up tasks by up to 10 times.
To cope with this challenge, the industry must allocate a budget for automation and introduce more AI technology to inspect and automate tasks in real time. It will help not only save costs but also improve efficiency and reduce waste.
Challenges of Adopting Digital Technologies
Manufacturing processes revolve around continuous, routine schedules and tasks operated by hundreds of suppliers and employees at multiple locations, and aimed at the production of consumable goods. This makes it exceptionally difficult for businesses to monitor current routines and identify areas of improvement.
Manufacturers can easily trace each step across their entire value chain by implementing real-time IoT-based monitoring technologies. Such technologies will help them better understand gaps in their sustainability goals and find solutions to improve efficiency, yield, and compliance.
Intelligent asset monitoring is typically associated with two challenges. The first involves integrating and upgrading legacy equipment to be compatible with new technology, enabling the full potential of Industry 4.0. The second supposes reskilling personnel to ensure they can effectively monitor, use, and benefit from a new monitoring system.
Smaller manufacturers often find the initial investment in new technology to be daunting. However, it is essential to recognize that both digital transformation and employee transformation are gradual processes. These changes do not occur overnight.
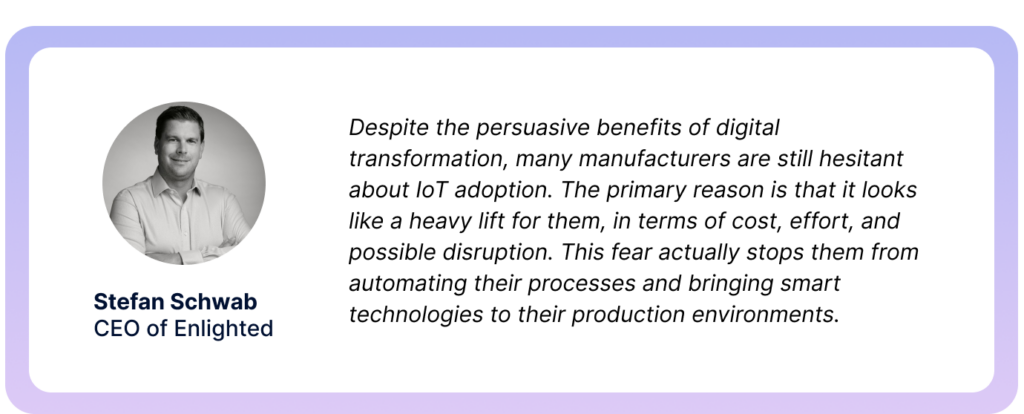
Wrapping Up
The manufacturing industry is already experiencing the effects of automation and robotics, such as artificial intelligence, the Internet of Things, sensors, robots on the floor, and more usage of robotic process automation. The increasing demand for adopting digital technologies and the benefits that manufacturing companies can get from them drive digitalization growth.
As a part of ongoing efforts to cope with the challenges the industry faces nowadays, manufacturers implement IoT-based solutions for intelligent asset monitoring. However, the choice of technology and its implementation option yet depends on the business opportunities and needs.
Unscheduled downtime of industrial machines, data collection issues, security vulnerabilities, and scalability constraints are those challenges that are positioned first on the manufacturing landscape and can be addressed by IoT-based monitoring technologies. Such technologies give manufacturers granular, contextualized data throughout the supply chain so they can quickly pinpoint problems to take action.
Furthermore, they can also predict potential issues before they happen, avoiding recalls and other significant environmental risks. Over time, monitoring technologies will enable users to track the progress of their sustainability goals and ensure compliance with the industry regulations.
We’d like to thank everyone who participated in our customer development interview:
- Vatsal Shah, CEO of Litmus
- Stefan Schwab, CEO of Enlighted
- Tom Richter, Global Head of Discrete and Process Manufacturing Verticals for Digital Industries at Nokia
- Nils Arnold, CEO of Adtance
- Duncan Kerr, former CEO of Aeristech
- Richard Lebovitz, CEO of LeanDNA
- Gulroz Singh, SoC Safety Architect at NXP Semiconductors
- Donnie Rand, Marketing Coordinator at American Association of Owner Operators, LLC
- David Reid, Sales Director at VEM Tooling
- Derrick Hathaway, Sales Director at VEM Medical
- Harman Singh, Director at Cyphere
- Doug Lawson, CEO of ThinkIQ
- And other industry professionals, whose comments were taken for this article
- SEO Powered Content & PR Distribution. Get Amplified Today.
- PlatoData.Network Vertical Generative Ai. Empower Yourself. Access Here.
- PlatoAiStream. Web3 Intelligence. Knowledge Amplified. Access Here.
- PlatoESG. Carbon, CleanTech, Energy, Environment, Solar, Waste Management. Access Here.
- PlatoHealth. Biotech and Clinical Trials Intelligence. Access Here.
- Source: https://www.iotforall.com/experts-discuss-predictive-maintenance-and-innovation-in-manufacturing
- :has
- :is
- :not
- :where
- $UP
- 1
- 10
- 2023
- 2024
- 21st
- 361
- a
- Able
- About
- accommodate
- across
- Action
- actions
- active
- actively
- adapt
- addition
- addressed
- Adjusted
- Adopting
- Adoption
- advancements
- against
- AI
- aimed
- AIR
- algorithms
- align
- All
- allocate
- Allowing
- already
- also
- amounts
- an
- analysis
- analytics
- and
- Anticipated
- any
- applications
- Apply
- approach
- appropriately
- architecture
- ARE
- AREA
- areas
- around
- artificial
- artificial intelligence
- AS
- asset
- associated
- Association
- At
- attack
- Attacks
- attempted
- augmented
- Augmented Reality
- automate
- automatically
- Automation
- automotive
- autonomous
- available
- avoiding
- Balance
- barriers
- based
- basic
- BE
- become
- becomes
- been
- before
- being
- benefit
- benefits
- BEST
- Better
- between
- Big
- boost
- both
- bottlenecks
- Brings
- budget
- business
- businesses
- but
- by
- C-suite
- called
- CAN
- Can Get
- cannot
- capture
- Catch
- Century
- ceo
- certain
- chain
- chains
- challenge
- challenges
- changed
- Changes
- China
- chip
- Chips
- choice
- class
- Close
- Cloud
- cloud computing
- CO
- collect
- collection
- comments
- Common
- Companies
- company
- compatibility
- compatible
- compelled
- competition
- competitive
- complex
- compliance
- component
- comprehend
- comprises
- computing
- concepts
- conducted
- Configuration
- Connect
- Consequences
- considerations
- constraints
- context
- continue
- continuous
- control
- Coordinator
- Cost
- costly
- Costs
- Counterfeit
- COVID-19
- create
- critical
- Current
- Current state
- Currently
- customer
- customization
- cyber
- data
- Data Analytics
- data quality
- data sets
- David
- decades
- decisions
- deeply
- Defense
- delivery
- Demand
- demands
- Demographics
- Denial of Service
- dependence
- depends
- detailed
- Development
- Devices
- different
- difficult
- difficulties
- digital
- Digital Transformation
- Digital twins
- digitalization
- digitally
- digits
- Director
- discuss
- discussed
- diverse
- do
- does
- doing
- Domestic
- done
- DOS
- double
- double digits
- downtime
- drive
- drivers
- driving
- due
- during
- each
- easily
- economies
- Effective
- effectively
- effects
- efficiency
- efficient
- effort
- efforts
- either
- embedded
- employed
- Employee
- employees
- enable
- enabled
- enabling
- endeavor
- engage
- enhancing
- ensure
- ensuring
- Entire
- environmental
- equipment
- Errors
- essential
- Even
- everyone
- evolve
- exceptionally
- execute
- existing
- expanded
- experiencing
- experts
- Exploit
- Exploring
- external
- faced
- faces
- facilities
- facing
- factors
- familiarize
- few
- Find
- First
- Floor
- flow
- Focus
- following
- For
- Force
- foreseeable
- format
- Former
- former ceo
- formidable
- found
- frequent
- frequently
- from
- full
- future
- gaps
- gathered
- generates
- get
- getting
- Give
- gives
- Global
- global trade
- goal
- Goals
- gone
- goods
- got
- gradual
- greater
- greatly
- Grows
- Growth
- hand
- happen
- Happening
- Hard
- Hardware
- Have
- head
- hear
- help
- High
- Highlighted
- hinder
- historically
- How
- However
- http
- HTTPS
- Hundreds
- ideally
- identify
- if
- ignore
- implement
- implementation
- implemented
- implementing
- importance
- improve
- improvement
- improving
- in
- include
- includes
- Including
- Increase
- increased
- increasing
- indicate
- indicating
- Indicators
- industrial
- industries
- industry
- industry 4.0
- inflation
- information
- Infrastructure
- initial
- initiatives
- innovations
- inputs
- integrate
- Integrating
- integration
- Intelligence
- Intelligent
- intend
- Internet
- internet of things
- Internet-of-Things (IoT)
- Interview
- interviewees
- Interviews
- into
- intricate
- introduce
- introducing
- investing
- investment
- Investments
- involves
- iot
- issue
- issues
- IT
- ITS
- Job
- jpg
- just
- Keep
- Key
- Lack
- landscape
- large
- Last
- launch
- learning
- Led
- Legacy
- Level
- levels
- leveraging
- like
- Limited
- lines
- locations
- logic
- looking
- loss
- losses
- lost
- Lot
- lower
- lowest
- machine
- machine learning
- machinery
- Machines
- Main
- maintenance
- major
- MAKES
- Making
- malicious
- manage
- manual
- manufactured
- Manufacturers
- manufacturing
- manufacturing industry
- many
- Market
- Marketing
- Match
- Matters
- max-width
- May..
- mean
- means
- methods
- minimizing
- missing
- Mobile
- models
- Modern
- money
- Monitor
- monitoring
- more
- more efficient
- Moreover
- most
- multiple
- must
- necessarily
- Need
- needed
- needs
- networks
- New
- New technologies
- next
- Nokia
- notably
- now
- number
- obstacles
- occur
- of
- Offers
- often
- Oil
- on
- ONE
- ones
- ongoing
- only
- operated
- operational
- Operations
- operators
- opportunities
- Optimize
- Option
- or
- Other
- our
- output
- over
- overall
- overnight
- overwhelming
- owner
- Pace
- parameter
- parameters
- part
- participated
- past
- perform
- performance
- Personnel
- perspective
- picture
- placed
- Platforms
- plato
- Plato Data Intelligence
- PlatoData
- points
- positioned
- possible
- potential
- predict
- prediction
- Predictions
- predictive
- Predictive Analytics
- prefer
- preferences
- Prepare
- pressure
- prevalence
- prevent
- preventing
- Prices
- pricing
- prioritizing
- problems
- process
- Process Automation
- processes
- Producers
- Product
- Production
- productivity
- Products
- professionals
- Progress
- proper
- protected
- quality
- quickly
- quote
- rand
- ransomware
- Ransomware Attacks
- rapid
- reaching
- real
- real-time
- real-time data
- Reality
- recent
- recognize
- recommendations
- reconsider
- reduce
- reduce waste
- regulations
- relatively
- remain
- remained
- remote
- replacement
- Reported
- requires
- research
- researchers
- resilience
- reskilling
- Resources
- result
- resulted
- Results
- Richter
- rising
- risks
- Robotic Process Automation
- robotics
- robots
- robust
- routine
- Run
- runs
- sacrificing
- Safety
- sales
- same
- Save
- Scalability
- scalable
- Scarcity
- seamless
- Second
- security
- semiconductor
- Semiconductors
- sensors
- Series
- service
- set
- Sets
- several
- severe
- shared
- shifted
- Shifts
- shortages
- should
- show
- significant
- simply
- situations
- smart
- smarter
- So
- Solutions
- SOLVE
- some
- sophisticated
- Source
- specific
- speed
- stakeholders
- started
- State
- steel
- stefan
- Step
- strategies
- Strengthen
- strong
- Struggle
- Struggling
- Successfully
- such
- sudden
- suppliers
- supply
- supply chain
- Supply Chain Challenges
- Supply chains
- Supported
- Survey
- Sustainability
- sustainable
- Syria
- system
- Systems
- Taiwan
- Take
- taken
- Target
- Task
- tasks
- team
- techniques
- technological
- Technologies
- Technology
- tend
- thank
- that
- The
- theft
- their
- Them
- themselves
- then
- These
- they
- things
- Thinking
- third-party
- this
- those
- thought
- threats
- Through
- throughout
- Thus
- time
- time-consuming
- times
- timestamp
- to
- tool
- tools
- toward
- trace
- track
- trade
- Transformation
- transition
- Trojan
- try
- trying
- TURN
- Twins
- two
- typically
- unaffected
- understand
- understanding
- Unexpected
- unforeseen
- upskilling
- us
- Usage
- use
- used
- users
- uses
- using
- utility
- Valuable
- Valuable Information
- value
- Values
- varying
- VeloCity
- verticals
- very
- Virtual
- visibility
- volumes
- Vulnerabilities
- was
- Waste
- ways
- we
- were
- What
- which
- while
- WHO
- whose
- why
- will
- with
- within
- without
- Work
- Workforce
- working
- year
- years
- yet
- Yield
- zephyrnet