Intel’s new manufacturing plant in Leixlip, Ireland, which cost $18.5 billion to build, is replete with technologies touted for conserving energy and water including programmable, all-LED lighting and a water reclamation and filtration system that could save 275 million gallons a year.
One of its more unusual features, however, is an approach that’s often overlooked: capturing heat generated by equipment in the facility and funneling it into production processes rather than expelling it through cooling towers. This was accomplished by the installation of recovery chillers that capture heat created by Intel’s high-temperature manufacturing processes and pipe it in the form of heated water to other places at the facility.
Intel estimates these heat recovery measures will allow it to significantly cut the natural gas it must buy to run operations at the site, Fab 34. It will use nine times as much recovered energy than what is generated by other fuels, the company projects. That so-called "waste heat" can be used for tasks such as preheating the ultra-pure water Intel needs for semiconductor fabrication or keeping buildings at the site warm during cooler weather, said Rich Riley, principal engineer in Intel’s corporate services development group.
"If we didn’t have that heat, we would need that much more gas to facilitate the [heating, ventilation and air-conditioning] operations," Riley said. "This is an overall reduction of natural gas consumption."
Over time, Intel’s plan is to build on heat recovery and other energy efficiency measures by updating them with industrial equipment, such as heat pumps, that run on electricity.
Intel’s near-term energy-related sustainability goals include reducing Scope 1 and 2 emissions by 10 percent by 2030 from a 2019 baseline (it has achieved 4 percent as of fiscal year 2022); and conserving up to 4 billion kilowatt-hours cumulatively.
An untapped source of energy efficiency
Intel hasn’t disclosed the potential impact on its carbon emissions this heat recovery at Fab 34 effort could have, but a retrofit using water-to-water heat pumps in Fab 10 (also in Leixlip) will save an estimated 18.3 million kilowatt-hours of electricity annually. It will reduce Scope 1 emissions by about 4,760 metric tons, but Scope 2 emissions will increase by about 1,627 metric tons because of the electricity needed for the heat pumps.
Industrial energy remains a thorny challenge for corporate sustainability teams: An estimated 20 percent to 25 percent of energy consumed globally by industrial sources is still predominantly powered by coal and natural gas, according to the International Energy Agency.
The potential energy cost savings of using recovered waste heat for industrial processes, district heating applications or to generate electricity could reach up to $152.5 billion annually, slightly less than half the value of the natural gas imported by the European Union in 2022, according to a McKinsey report published in November. The analysis estimates the global recoverable heat potential is at least 3,100 terawatt-hours.
"In our view, if you want to decarbonize, heat recovery and waste heat is one of the most economical levers available," said Ken Somers, a McKinsey partner who was one of the report’s authors. One barrier to adoption has been low natural gas prices, but tariffs and supply shortages have prompted companies to rethink their dependence, he said.
The industrial heat pump technology needed to move heat from where it’s generated to where it’s needed in a production process is also maturing. The potential for manufacturers of chemicals, consumer products, food and pharmaceuticals to use this approach is growing as a precursor to the electrification of production systems, said Patricia Provot, president of thermal production equipment manufacturer Armstrong International.
"If your plan is to fully decarbonize, your first step is to get rid of steam and use hot water, and try to recover as much of that water as possible and put it back into the system," Provot said.
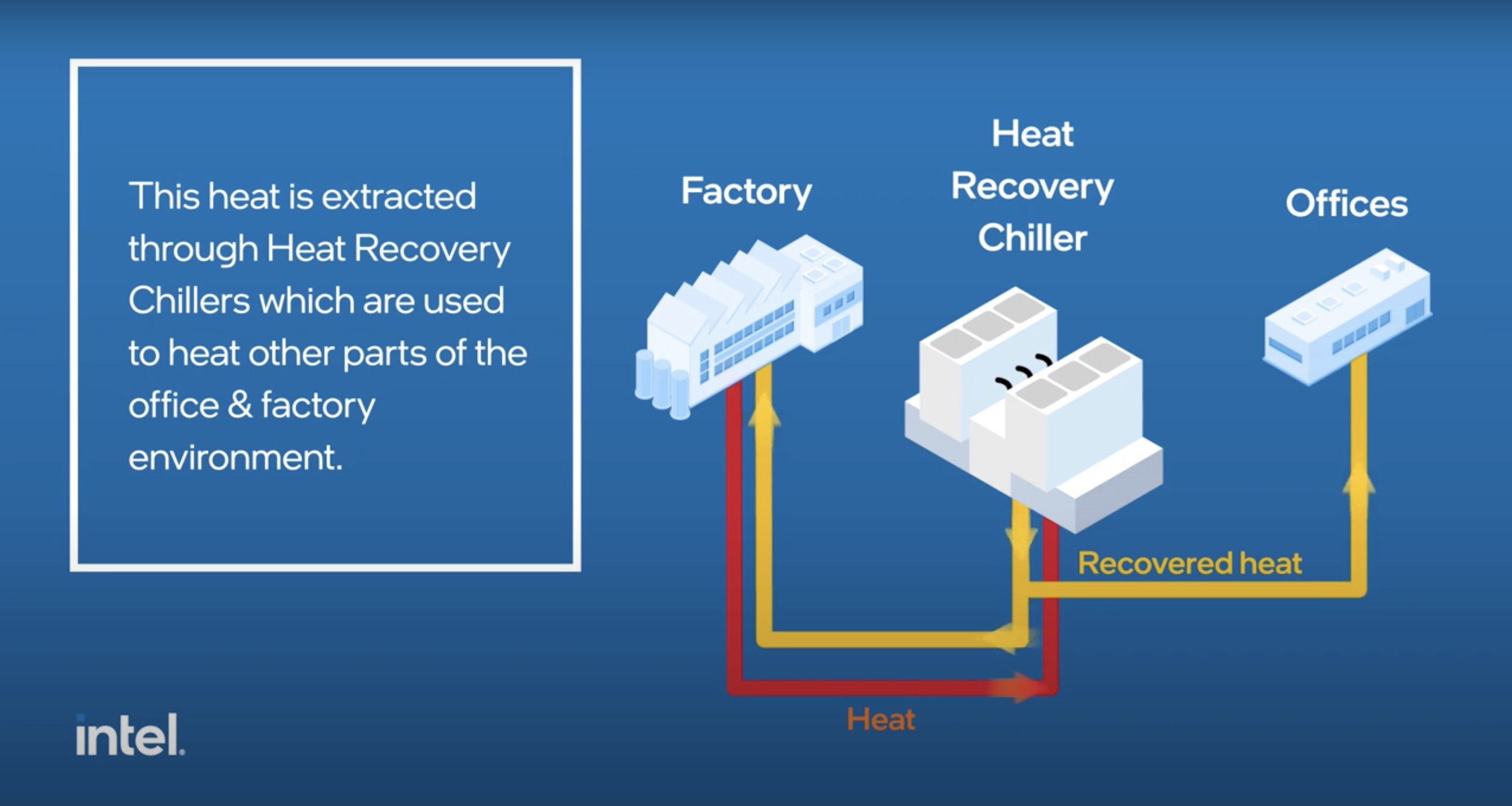
Lessons from Intel’s experience
Aside from the Ireland factory, Intel has introduced heat recovery and recirculation systems in Arizona, Ohio and Germany, and this approach will be considered for every new factory the company builds, said Todd Brady, vice president of global public affairs and chief sustainability officer at Intel. "It takes engineering design, understanding where the heat is generated, how it can be captured and redirected," he said. "A lot of it involves where the equipment is placed."
In the Ireland fab, a high-volume facility for the company’s Intel 4 chips, the engineering team performed an extensive mapping of heat movement to make decisions about how many heat exchangers and chillers were required to minimize the amount of high-grade heat systems powered by natural gas, said Riley.
Low-grade sources, rated between 100 degrees and 200 degrees Celsius, could include exhaust from boilers, air compressors or dryers. Intel still needs natural gas for very high-temperature processes.
Here are questions engineers should consider in designing a heat recovery system, Riley said.
- Have engineers done a "pinch analysis" for all seasons? These assessments study the flow of heat through an industrial process and are used to determine the minimum energy consumption required to get the job done. There are usually different metrics for summer and winter months.
- Will enough heat be generated to make a difference? This requires engaging equipment suppliers and facilities managers, who are responsible for where equipment is placed in an overall site design.
- If it’s a retrofit, how can heat be funneled to where it can be used? If production systems are widely distributed, the logistics of redirecting the heat could require relocating them or installing piping. Otherwise, capture might not make sense.
- Does the price of energy in the region justify the investment? The answer could make or break the return on investment case. In regions where the price of natural gas is high, the payback for these investments will be shorter.
It took Intel several years to refine its process, but now heat recovery is considered as part of every plant production project, Riley said: "It’s pretty complicated, but now it’s routine."
- SEO Powered Content & PR Distribution. Get Amplified Today.
- PlatoData.Network Vertical Generative Ai. Empower Yourself. Access Here.
- PlatoAiStream. Web3 Intelligence. Knowledge Amplified. Access Here.
- PlatoESG. Carbon, CleanTech, Energy, Environment, Solar, Waste Management. Access Here.
- PlatoHealth. Biotech and Clinical Trials Intelligence. Access Here.
- Source: https://www.greenbiz.com/article/intel-using-hot-water-cut-natural-gas-use-its-factories
- :has
- :is
- :not
- :where
- $UP
- 1
- 10
- 100
- 20
- 200
- 2019
- 2022
- 2030
- 25
- 8
- a
- About
- accomplished
- achieved
- Adoption
- Affairs
- AIR
- All
- allow
- also
- amount
- an
- analysis
- and
- Annually
- answer
- applications
- approach
- ARE
- arizona
- Armstrong
- AS
- assessments
- At
- authors
- available
- back
- barrier
- Baseline
- BE
- because
- been
- between
- Billion
- Break
- build
- builds
- but
- buy
- by
- CAN
- capture
- captured
- Capturing
- carbon
- carbon emissions
- case
- Celsius
- challenge
- chemicals
- chief
- Chips
- Coal
- Companies
- company
- Company’s
- complicated
- Consider
- considered
- consumed
- consumer
- Consumer products
- consumption
- Corporate
- Cost
- cost savings
- could
- created
- Cut
- decarbonize
- decisions
- dependence
- Design
- designing
- Determine
- Development
- difference
- different
- distributed
- district
- done
- during
- efficiency
- effort
- electricity
- electrification
- Emissions
- energy
- Energy Consumption
- energy efficiency
- engaging
- engineer
- Engineering
- Engineers
- enough
- equipment
- estimated
- estimates
- Ether (ETH)
- European
- european union
- Every
- exchangers
- extensive
- facilitate
- facilities
- Facility
- factories
- factory
- Features
- First
- Fiscal
- flow
- food
- For
- form
- from
- fuels
- fully
- GAS
- gas prices
- generate
- generated
- Germany
- get
- Global
- Globally
- Goals
- Group
- Growing
- Half
- Have
- he
- High
- HOT
- How
- However
- HTML
- HTTPS
- IEA
- if
- Impact
- in
- include
- Including
- Increase
- industrial
- industrial equipment
- installation
- installing
- Intel
- interested
- International
- into
- introduced
- investment
- Investments
- involves
- ireland
- IT
- ITS
- Job
- keeping
- learning
- least
- less
- Lighting
- logistics
- Lot
- Low
- make
- Managers
- Manufacturer
- Manufacturers
- manufacturing
- many
- mapping
- marketplace
- McKinsey
- measures
- metric
- Metrics
- might
- million
- minimize
- minimum
- months
- more
- most
- move
- movement
- much
- must
- Natural
- Natural Gas
- Need
- needed
- needs
- New
- news
- Newsletter
- nine
- node
- November
- now
- of
- Officer
- often
- Ohio
- on
- ONE
- Operations
- or
- Other
- otherwise
- our
- overall
- part
- partner
- PAYBACK
- percent
- performed
- pharmaceuticals
- pipe
- placed
- Places
- plan
- plant
- plato
- Plato Data Intelligence
- PlatoData
- possible
- potential
- powered
- precursor
- predominantly
- president
- pretty
- price
- Prices
- Principal
- process
- processes
- Production
- Products
- programmable
- project
- projects
- public
- published
- pump
- pumps
- put
- Questions
- rated
- rather
- reach
- Recover
- recoverable
- recovery
- reduce
- reducing
- reduction
- refine
- region
- regions
- remains
- require
- required
- requires
- responsible
- return
- Rich
- Rid
- routine
- Run
- Said
- Save
- Savings
- scope
- seasons
- semiconductor
- sense
- Services
- several
- shortages
- should
- significantly
- site
- Source
- Sources
- Steam
- Step
- Still
- Study
- such
- summer
- suppliers
- supply
- Sustainability
- system
- Systems
- takes
- tariffs
- tasks
- team
- teams
- Technologies
- Technology
- than
- that
- The
- their
- Them
- There.
- thermal
- These
- this
- Through
- time
- times
- to
- todd
- tons
- took
- touted
- Trends
- try
- understanding
- union
- untapped
- unusual
- updating
- use
- used
- using
- usually
- value
- very
- vice
- Vice President
- View
- want
- warm
- was
- Waste
- Water
- we
- Weather
- weekly
- were
- What
- What is
- which
- WHO
- widely
- Wikipedia
- will
- Winter
- with
- would
- year
- years
- you
- Your
- zephyrnet