열 응력은 기계적 응력 문제와 함께 고급 패키징에서 잘 알려진 문제입니다. 둘 다 열팽창 계수(CTE)가 호환되지 않는 재료를 혼합해야 하는 이종 통합으로 인해 악화됩니다.
효과는 이미 나타나고 있으며 패키지 밀도가 칩당 범프 1,000개 이상으로 증가함에 따라 더욱 악화될 것입니다.
“상대적으로 높은 CTE를 가진 금속을 결합한 다음 훨씬 더 큰 CTE 강성을 가진 폴리머를 갖게 되고 CTE가 극도로 낮은 유전체를 갖게 됩니다. 일단 모든 것을 합치면 스트레스를 피할 수 없습니다.
이러한 응력은 종종 심각한 휨 또는 다이 기울기를 초래하여 신뢰성을 저하시키는 조건으로 이어집니다. "당신은 여러 층의 다양한 기판 기술을 다루고 있습니다."라고 엔지니어링 부사장인 Chip Greely는 말했습니다. 프로멕스 산업. “특히 기질의 서로 다른 코어 두께는 뒤틀림을 포함하여 많은 고전적인 기계적 문제를 일으키기 시작하며, 이는 일부 대형 업체의 골칫거리가 되었습니다. 우리는 시스템 인 패키지, 이기종 통합 멀티 칩 모듈을 보유한 많은 고객에게 기판의 쉐도우 모아레 데이터를 제공하여 리플로우 온도에 따라 휨이 어떻게 변하는지 확인하고 이상적으로는 반성점.”
이 변형은 여러 차원에서 경험하는 다양한 부정적인 영향을 미칩니다. 신성. "종종 나노 구조 수준에서 피쳐의 구부러짐과 뒤틀림은 일부 DRAM 및 프런트 엔드 로직 나노시트에서 발견되는 내장된 스트레스로 인해 발생합니다."라고 그는 말했습니다. “또 다른 예는 관통 실리콘 비아(TSV) 주변의 '금지 구역'에서 일반적으로 발생하는 것처럼 유도된 변형이 고급 반도체 구조의 제조를 방지하는 미크론 규모 영역과 관련이 있습니다. 마지막으로, 유도된 변형의 대규모 영향은 웨이퍼 휘어짐을 유발하여 웨이퍼 취급 및 제조를 상당히 복잡하게 하여 웨이퍼 자체가 파손될 위험이 있습니다. 3D NAND 장치 제조 중에 흔히 발생하는 것처럼 두꺼운 유전체 층을 증착하는 동안 웨이퍼 휘어짐이 특히 나타납니다.”
좋은 소식은 업계가 이러한 문제와 관련 문제를 잘 알고 있다는 것입니다. 나쁜 소식은 현재 탐색 중인 많은 접근 방식이 있지만 아직 솔루션이 부족하다는 것입니다.
"뒤틀림을 줄이기 위한 다양한 방법론이 있지만 그 중 어느 것도 완전히 성공적이지 않으며 항상 장단점이 있습니다."라고 응용 프로그램 및 제품 관리 이사인 Frank Chen은 말했습니다. Bruker 나노 표면 및 계측. “문제는 좁은 범위의 애플리케이션에만 국한되지 않습니다. 다이를 다른 기판에 부착할 때마다 이러한 문제가 발생하게 됩니다.”
이 모든 것은 검사와 계측이 계속해서 중요한 역할을 해야 함을 의미합니다. 핫스팟과 같은 다른 문제도 여러 칩이 이기종 패키지에 결합될 때 악화될 수 있습니다.
"테스트 중에 다양한 칩이 서로 다른 시간과 온도에서 가열되어 적절하게 냉각되어야 하는 핫스팟을 생성할 수 있습니다. 앰코. "서로 다른 칩의 영역을 일치시키는 특정 열 능동 컨트롤러를 만드는 것 외에도 테스트 프로그램에서 제공하는 벡터를 기반으로 핫스팟을 '예측'할 수 있는 적응형 열 컨트롤러를 개발하기 위한 상당한 노력이 있습니다."
이러한 조합은 문제의 근원에 가장 신속하게 도달하기 위해 서로 다른 기술을 결합하는 하이브리드 계측의 사용 증가로 이어지고 있습니다.
설계, 검사, 테스트 솔루션
실제로 설계, 검사 및 열역학적 응력 사이의 고전적인 상호 작용은 점점 더 작고 취약한 수천 개의 연결로 인해 더욱 복잡해졌습니다.
한 가지 결과는 과열 및 기계적 스트레스로 이어질 수 있는 CTE 문제와 그에 따른 계단식 효과를 "설계"하기 위해 왼쪽으로 이동에 대한 새로운 강조입니다. 전자 및 반도체 산업 부문의 포트폴리오 개발 책임자인 Andras Vass-Varnai에 따르면 중요한 결함을 발견하고 예방할 가능성을 높이려면 시뮬레이션과 검사가 모두 필요하다고 합니다. Siemens Digital Industries 소프트웨어.
"패키지의 초기 설계 단계에서 전산 흐름 역학(CFD), 유한 요소 모델링(FEA) 등을 사용한 열 및 구조 공동 시뮬레이션은 어셈블리의 예상 성능을 이해하는 데 도움이 되며 ' 많은 설계 선택을 매개변수화할 수 있으므로 AI 기반의 최적화”라고 Vass-Varnai는 설명했습니다. “첫 번째 프로토타입이 제작되면 열 과도 테스트는 구성 요소의 열 성능을 매핑하는 데 도움이 될 수 있습니다. 예상과 실제 열 동작 사이에 불일치가 있는 경우 테스트 데이터를 사용하여 패키지 디지털 트윈의 재료 속성을 '보정'하고 향후 설계의 초기 정확도를 높이기 위해 재료 라이브러리를 업데이트할 수 있습니다.”
범프 어레이를 테스트하고 테스트를 위해 설계하는 가장 좋은 방법을 찾는 것이 점점 더 어려워지고 있습니다. “위아래로 움직이는 신호가 있다면?” Rob Aitken에게 물었다. Synopsys 사람. “그러면 테스트 문제가 발생합니다. 왜냐하면 이제 아무데도 가지 않는 신호와 아무 데서나 오는 또 다른 신호가 있기 때문입니다. 그런 것들을 테스트하는 방법을 알아내야 합니다. 당신은 그들을 조사합니까? 그러나 이 경우 유지해야 하는 물리적 치수가 있으며 기계적 손상의 위험이 있습니다. 아니면 일종의 JTAG와 같은 구조를 찾으십니까? 그러나 그러면 이러한 연결점의 효율성이 감소합니다. 우리는 모두가 '아마 이게 통할거야, 저것도 통할거야'라고 말하는 광대한 실험 단계에 있습니다. 지금 당장은 '그것'이 무엇인지 내기하고 싶지 않을 것입니다.”
JCET에 따르면 결함 조사를 위한 간접 및 직접 테스트 옵션이 모두 있습니다. 예를 들어 CSAM(Computed Scanning Acoustic Tomography) 및 3D X-ray는 간접적인 반면 기계적 단면 분석은 직접 증명을 위한 도구입니다. JCET는 기계적 결함으로 인한 재료/구조 문제를 특성화하는 고급 열 특성화 장비도 보유하고 있습니다.
항상 그렇듯이 광학 검사는 인라인 검사를 위한 가장 빠른 접근 방식이지만 모범 사례는 하이브리드 접근 방식입니다. "단락/개방 및 마진 결함을 감지하는 가장 좋은 방법은 SPI(솔더 페이스트 검사)에서 사전 리플로우 AOI(자동 광학 검사)에서 사후 리플로우 AOI에서 인라인 X-레이로 가는 것입니다."라고 연구 부사장인 Timothy Skunes는 조언했습니다. Nordson Test & Inspection의 개발 사이버 옵틱스 포트폴리오.
또한 특히 고급 노드에서 다른 양식이 유용할 수 있습니다. 예를 들어 반도체 장치의 변형을 특성화하는 최근 접근 방식은 Raman Spectroscopy(RS)입니다. "RS는 온구조 측정에 매우 적합하며, 몇 초 단위로 빠른 측정을 제공하고 세부적인 측정을 가능하게 하는 수 미크론의 작은 스폿 크기를 제공합니다."라고 Nova의 Barak은 말했습니다. "팹에서 인라인 계측 도구로 라만 분광법을 도입하기 전에는 구조물의 변형률을 직접 측정하는 것이 어려웠기 때문에 제조 공정의 훨씬 나중 단계에서 테스트를 해야 했습니다."
궁극적으로 철저한 검사를 위해 모서리가 잘리지 않습니다. 예산 계산에는 새 기기의 초기 비용 대 과도한 RMA의 지속적인 비용과 같은 비교 지표가 필요할 수 있습니다. 그리고 한 가지 더 고려해야 할 사항이 있습니다. 데이터를 신뢰할 수 있는지 확인하는 방법입니다.
“최종 사용자에게 전달하는 자료에 문제가 없는지 확인하기 위해 아마도 좋은 자료였을 것을 버릴 것입니까? 그 비용은 누가 부담할까요?” 소프트웨어 제품 관리 이사인 Mike McIntyre는 다음과 같이 경고했습니다. 혁신에, 자동화된 결함 분류를 수행할 때 정확한 비교 평가를 위해 통계 데이터베이스를 권장합니다.
뒤틀림
응력의 최악의 결과 중 하나는 뒤틀림입니다. 뒤틀림을 감지하기 어려울 수 있다는 것은 놀라운 일이지만 그 효과가 보기만큼 항상 분명한 것은 아닙니다. 휨은 칩과 기판 사이의 동일 평면성에 약간의 차이를 일으켜 일부 마이크로 범프가 아래의 패드와 불충분하게 연결되지 않도록 하며, 이를 비습식이라고 합니다.
"예를 들어, 50~60mm의 고급 프로세서를 고려하십시오."라고 Chen은 말했습니다. “크기가 크기 때문에 뒤틀림 없이 가공하기가 어렵습니다. 그럼에도 불구하고 다이 부착 도구가 공정 창의 중심으로 조정되면 검사를 통과하고 높은 수율로 제조될 수 있습니다. 문제는 허용 오차가 매우 좁을 수 있다는 것입니다. 뒤틀림 위에 약간의 다이 기울기가 생기자마자 젖지 않는 문제가 발생합니다.”
설상가상으로, 이것이 50µm 범위(~35µm 범프 크기)의 범프 피치에서 발생하는 경우 범프 치수가 더 줄어들면서 발생하는 문제를 상상해 보십시오. 2023년에서 2024년에 차세대로 이동함에 따라 이미 자동차 산업의 관심사입니다. 중요한 전환은 28nm 노드 주변이 될 것이라고 Chen은 말했습니다.
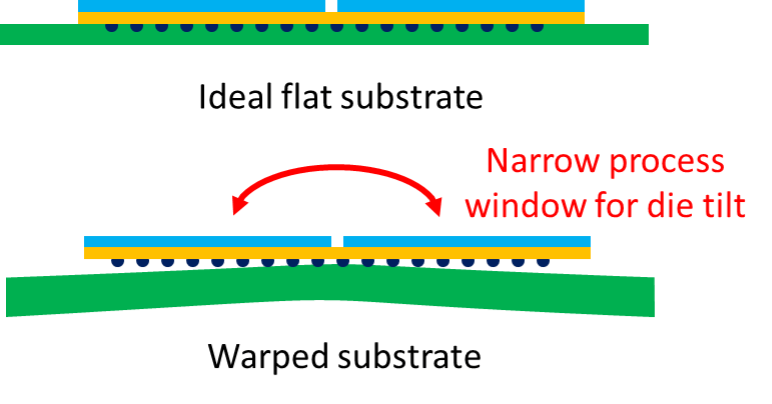
그림 1 다이 부착 도구는 뒤틀림이 있을 때 다이 틸트에 대한 공정 범위가 매우 좁습니다. 출처: 브루커
젖지 않는
"Non-wets"는 솔더 범프에서 발생할 수 있는 몇 가지 문제를 포괄하는 광범위한 용어이며, 그 중 대부분은 매우 미묘합니다. 땜납은 액체 상태인 경우가 많기 때문에 땜납을 도포하는 과정을 "습윤"이라고 합니다. 가느다란 링크는 "비습식(non-wet)"이라고 하며, 더 얇은 연결을 가진 더 작은 노드에서 더 어려운 문제가 되고 있습니다.
젖지 않은 칩은 종종 일반적인 스크리닝 프로세스를 벗어나 나중에 반환된 칩(RMA)으로 나타납니다. 근본 원인은 열적, 기계적 또는 조합일 수 있습니다(예: 거친 지형을 통과하는 자동차의 열 순환). 누적 효과는 접촉을 끊기에 충분한 열-기계적 응력을 제공할 수 있습니다.
특정 유형의 문제를 설명하는 추가 별명이 있습니다. "헤드 인 필로우(head-in-pillow)" 결함에서는 양호한 연결의 매끄럽고 원기둥 모양 대신 베개 위의 머리처럼 하나의 공이 다른 공에 가라앉는 것처럼 보입니다.
"그것은 여전히 접촉하고 있기 때문에 전기적 테스트는 양호할 수 있지만 매우 취약하다는 것을 알 수 있습니다." Chen이 헤드 인 필로우의 X-레이를 가리키며 말했습니다. “열 응력이나 기계적 응력이 가해지면 완전히 파손될 수 있습니다. 비습식 접점인 경우에도 얇은 연결로 인해 높은 저항과 차선의 성능이 발생하고 오래 지속되지 않을 가능성이 높습니다. 개방형 비습식은 전혀 작동하지 않습니다. 다이 틸트가 있는 일반적인 시나리오에서는 잘 형성된 범프에서 젖지 않는 범프로 눈에 띄는 전환이 있습니다.”
중요한 문제는 잠재적인 결함, 즉 전기 테스트를 통과할 만큼 충분히 기능적이지만 현장에서는 실패하는 연결입니다.
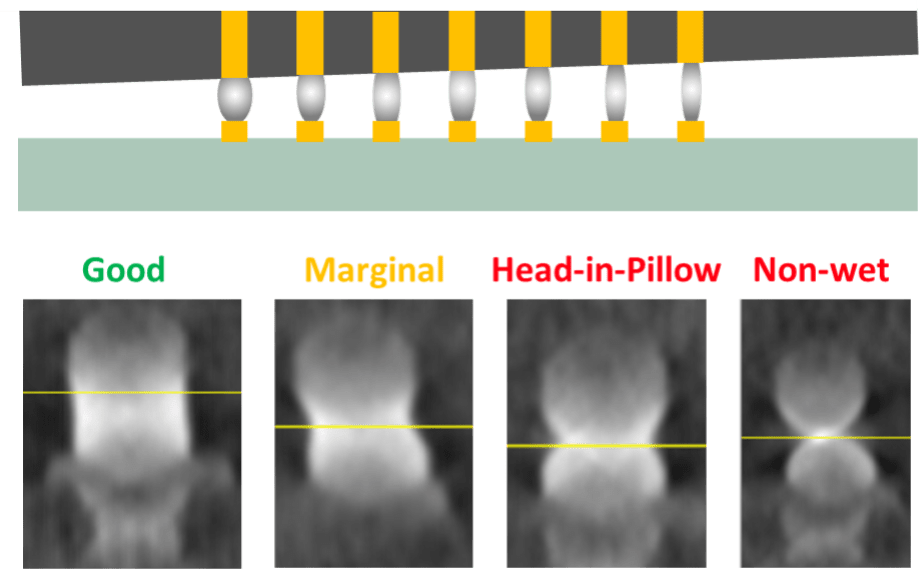
그림 2 다이 기울기가 있는 상태에서 양호한 범프에서 비습식으로의 점진적인 전환. 출처: 브루커
Chen은 "열 스트레스의 영향으로 인해 현재 많은 유형의 장치에서 큰 문제가 되고 있습니다."라고 말했습니다. “한 고객이 e-테스트 심사를 통과한 제품을 가지고 출고했습니다. 불행하게도 나중에 발생하는 비습식 문제로 인해 많은 RMA가 발생했습니다.”
일부 회사는 고통스럽고 지루한 수동 검사를 통해 이 문제를 해결하고 있습니다. 불행하게도, 모든 사람의 검사는 특히 검사관이 여러 시간 동안 교대하는 동안 미묘한 오류를 발견하려고 할 때 작업자 피로에 노출될 수 있습니다.
긍정적인 측면은 이제 인라인으로 사용할 수 있는 X-레이 도구와 같은 검사에 대한 자동화된 접근 방식이 있다는 것입니다. "특히 자동차 산업에서 100dppb 미만을 달성하기 위한 고속 완전 자동 검사를 향한 큰 동인이 있습니다."라고 Chen은 말했습니다.
거기에서 더 복잡해집니다. Draper 연구소 기술 직원의 수석 구성원인 Tom Marinis는 "특히, 많은 비습식의 주범인 솔더도 일렉트로마이그레이션의 영향을 받습니다."라고 말했습니다. “솔더의 녹는 온도가 장치의 작동 온도에 비해 상대적으로 낮을 수 있기 때문에 일정 기간 동안 특정 솔더에 대해 칩과 기판 사이의 연결에서 전류 밀도가 너무 높으면 마이그레이션이 발생할 수 있습니다. 실제로 공극을 형성하고 결국 연결을 엽니다.”
Marinis는 장치-PCB 수준의 상용 모델링 도구가 잠재적인 일렉트로 마이그레이션 문제를 지속적으로 경고할 만큼 충분히 성숙되지 않았으므로 가속 노화 테스트를 계속 수행하는 것이 중요하다고 경고했습니다.
결론
궁극적으로 잠재된 결함에서 신뢰성 문제를 감지하려면 다이 이동, 회전, 높이, 기울기 및 기타 매개변수에 민감한 더 높은 샘플링 계측이 필요합니다. 또한 생산 전에 잠재적인 문제를 예상하고 해결하기 위해 다중 물리 모델링에 더 많이 의존해야 합니다. 그리고 반도체와 자동차 산업이 계속해서 섞이면서 RMA보다 훨씬 더 많은 것이 위태로워졌습니다.
Chen은 "잠재적 결함이 장치에서 모듈, 자동차로 전달되면서 사람들의 생명을 위협할 수 있으므로 실패 비용이 기하급수적으로 증가합니다."라고 말했습니다. 이것이 바로 칩 제조업체가 잠재된 결함을 더 잘 포착하기 위해 설계, 검사 및 테스트를 결합하는 전체론적 솔루션을 만드는 이유입니다.
- SEO 기반 콘텐츠 및 PR 배포. 오늘 증폭하십시오.
- 플라토 블록체인. Web3 메타버스 인텔리전스. 지식 증폭. 여기에서 액세스하십시오.
- 출처: https://semiengineering.com/bump-reliability-is-challenged-by-latent-defects/
- 000
- 1
- 2023
- 2024
- 3d
- a
- 가속 된
- 에 따르면
- 정확한
- 달성
- 활동적인
- 실제로
- 또한
- 추가
- 주소 지정
- 많은
- 노화
- 경보
- All
- 수
- 이미
- 이기는하지만
- 항상
- 분석
- 와
- 다른
- 예상
- 응용할 수 있는
- 어플리케이션
- 적용
- 접근
- 구혼
- 지역
- 지역
- 약
- 조립
- 평가
- 관련
- 붙이다
- 자동화
- 자동차
- 자동차 산업
- 나쁜
- 공
- 기반으로
- 기초
- 곰
- 때문에
- 가
- 되고
- 전에
- 뒤에
- 존재
- 이하
- BEST
- 베팅을
- 더 나은
- 사이에
- 그 너머
- 큰
- 더 큰
- 비트
- 흩어져
- 넓은
- 예산
- 내장
- 내장
- 사업
- 사업 개발
- 라는
- 얻을 수 있습니다
- 자동차
- 자동차
- 케이스
- 잡아라
- 원인
- 원인
- 일으키는
- 센터
- CFD
- 도전
- 도전 한
- 과제
- 도전
- 승산
- 변경
- 특징
- 첸
- 칩
- 칩
- 선택
- 고전적인
- 분류
- 결합
- 조합
- 결합
- 결합 된
- 결합
- 왔다
- 상업
- 공통의
- 기업
- 비교
- 완전히
- 복잡한
- 복잡한
- 구성 요소
- 관심
- 조건
- 연결하기
- 연결
- 연결
- 고려
- CONTACT
- 계속
- 핵심
- 모서리
- 비용
- 수
- 피복
- 만들
- 만든
- 생성
- 만들기
- 임계
- Current
- 현재
- 고객
- 고객
- 절단
- 데이터
- 데이터베이스
- 취급
- density
- 설명
- 디자인
- 디자인
- 상세한
- 개발
- 개발
- 개발
- 장치
- 디바이스
- Mourir
- 차이
- 다른
- 어려움
- 디지털
- 디지털 트윈
- 치수
- 곧장
- 직접
- 책임자
- 하기
- 말라
- 아래 (down)
- 포목상
- 운전사
- 더빙 된
- ...동안
- 역학
- 초기의
- 효과
- 효과
- 효율성
- 노력
- 전자
- 강조
- 엔지니어링
- 충분히
- 확인
- 장비
- 오류
- 특히
- 등
- 에테르 (ETH)
- 조차
- 있을뿐만 아니라
- 모두
- 예
- 행정부
- 확장
- 기대하는
- 경험
- 설명
- 탐험 한
- 기하 급수적으로
- 매우
- 실패
- 고장
- 가장 빠른
- 피로
- 특징
- 사람
- 를
- 들
- 무화과
- 그림
- 최종적으로
- Find
- 발견
- 먼저,
- 흐름
- 형태
- 발견
- 에
- 실망스럽게
- 기능의
- 추가
- 세대
- 얻을
- 간다
- 가는
- 좋은
- 점진적
- 성장하는
- 성장
- 처리
- 하드
- 머리
- 신장
- 도움
- 도움이
- 높은
- 더 높은
- 고도로
- 전체적인
- 희망
- 뜨거운
- 방법
- How To
- HTTPS
- 사람의
- 잡종
- 영향
- 중대한
- in
- 포함
- 증가
- 증가
- 산업
- 산업
- 처음에는
- 를 받아야 하는 미국 여행자
- 기계
- 완성
- 개요
- 조사
- 외딴
- 발행물
- 문제
- IT
- 그 자체
- 종류
- 실험실
- 넓은
- 대규모
- 큰
- 성
- 층
- 레이어
- 리드
- 지도
- 오퍼
- 지도
- 레벨
- 도서관
- 아마도
- 모래밭
- 리퀴드
- 삶
- 긴
- 롯
- 낮은
- 유지하다
- 확인
- 유튜브 영상을 만드는 것은
- 구축
- 매니저
- 조작
- 제조 한
- .
- 지도
- 마리오
- 어울리는
- 자료
- 재료
- 성숙한
- 최대 폭
- 방법
- 측정 시간 상관관계
- 측정
- 기계적인
- 회원
- 금속
- 방법
- 방법론
- 통계
- 도량형
- 수도
- 이주
- 혼합
- 모델링
- 모듈
- 모듈
- 배우기
- 가장
- 이동
- 여러
- 나노
- 필연적으로
- 필요
- 부정
- 그렇지만
- 신제품
- 새로운 기술
- news
- 다음 것
- 노드
- 노드
- 분명한
- 제공
- ONE
- 지속적으로
- 열 수
- 운영
- 연산자
- 최적화
- 옵션
- 주문
- 기타
- 꾸러미
- 패키지
- 포장
- 고통
- 매개 변수
- 특별한
- 특별히
- 합격
- 사람들의
- 수행
- 성능
- 기간
- 상
- 물리적
- 피치
- 플라톤
- 플라톤 데이터 인텔리전스
- 플라토데이터
- 연극
- 플레이어
- 포인트 적립
- 전철기
- 폴리머
- 유가 증권
- 긍정적인
- 가능한
- 가능성
- 연습
- 존재
- 대통령
- 방지
- 교장
- 이전에
- 아마
- 탐침
- 문제
- 문제
- 방법
- 프로세스
- 프로세서
- 프로덕트
- 제품 관리
- 생산
- 프로그램
- 증명
- 정확히
- 속성
- 프로토 타입
- 제공
- 제공
- 놓다
- R&D
- 범위
- 빠른
- 현실
- 최근
- 추천하다
- 감소
- 감소
- 반사
- 상대적으로
- 신뢰성
- 신뢰
- 갱신
- 필요
- 필요
- 연구
- 연구 및 개발
- 결과
- 결과
- 결과
- 위험
- 위험
- 역할
- 뿌리
- 달리기
- 말했다
- 라고
- 저울
- 스캐닝
- 대본
- 전형
- 초
- 것
- 분절
- 선택
- 반도체
- 연장자
- 민감한
- 몇몇의
- 그림자
- 셰이프
- 변화
- 이동
- 제공
- 짧은
- 표시
- 신호
- 상당한
- 크게
- 시뮬레이션
- 크기
- 크기
- 작은
- 작은
- So
- 소프트웨어
- 솔루션
- 일부
- 예정입니다.
- 출처
- 구체적인
- 분광학
- Spot
- 직원
- 단계
- 단계
- 말뚝
- 스타트
- 주 정부
- 통계적인
- 아직도
- 스트레스
- 구조상의
- 구조
- 제목
- 성공한
- 이러한
- 놀라운
- 테크니컬
- 기법
- 기술
- test
- 지원
- XNUMXD덴탈의
- 지역
- 그들의
- 그곳에.
- 열의
- 맡은 일
- 일
- 수천
- 을 통하여
- 던지기
- 시간
- 시대
- 에
- 함께
- 공차
- 너무
- 수단
- 검색을
- 상단
- 방향
- 전이
- 믿어
- 회전
- 유형
- 전형적인
- 이해
- 곧 출시
- 업데이트
- 사용
- 사용자
- 여러
- 거대한
- 부통령
- 눈에 보이는
- 잘 알려진
- 뭐
- 어느
- 동안
- 누구
- 의지
- 없이
- 작업
- 가장 나쁜
- 겠지
- 엑스선
- 산출량
- 너의
- 제퍼 넷