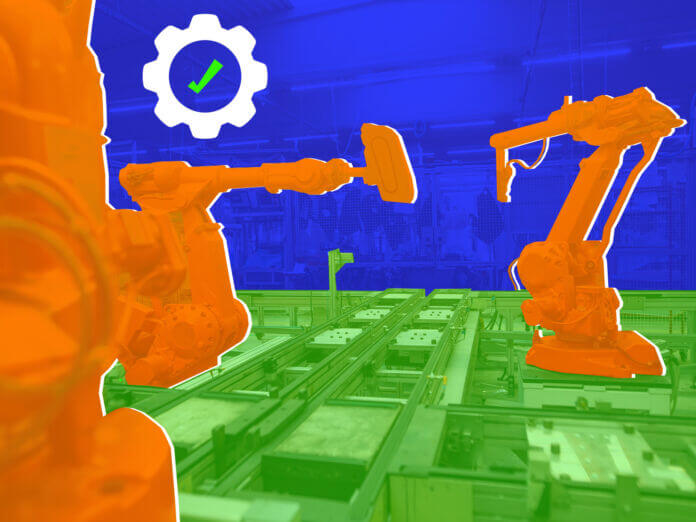
Um mögliche Ausfälle, Verletzungen von Mitarbeitern und Produktionsausfälle zu verhindern, machen sich immer mehr Unternehmen mit der Fernüberwachung von Anlagen vertraut. Sie versuchen zu rennen vorausschauende Wartungssysteme Probleme zu erkennen, bevor sie in der Fertigung auftreten, das Risiko einer Unzufriedenheit von Mitarbeitern und Kunden zu minimieren und Geldverluste zu verhindern.
Glücklicherweise bietet das 21. Jahrhundert moderne und effektive Lösungen für die vorausschauende Wartung in der Fertigung, die in verschiedenen Branchen umgesetzt werden können.
Kürzlich hat Prylada eine Reihe von Interviews zur Kundenentwicklung geführt, in denen wir mit Experten aus der Fertigungsindustrie gesprochen haben. Unser Team hat sich zum Ziel gesetzt, wertvolle Informationen darüber zu sammeln Asset-Überwachung und Herausforderungen bei der Technologieeinführung in der Branche und wie Unternehmen diese lösen.
Während der Interviews besprachen wir die aktuelle Marktlage, die problematischsten Probleme, den Wettbewerb und Empfehlungen für eine effektive Entwicklung innerhalb der Branche.
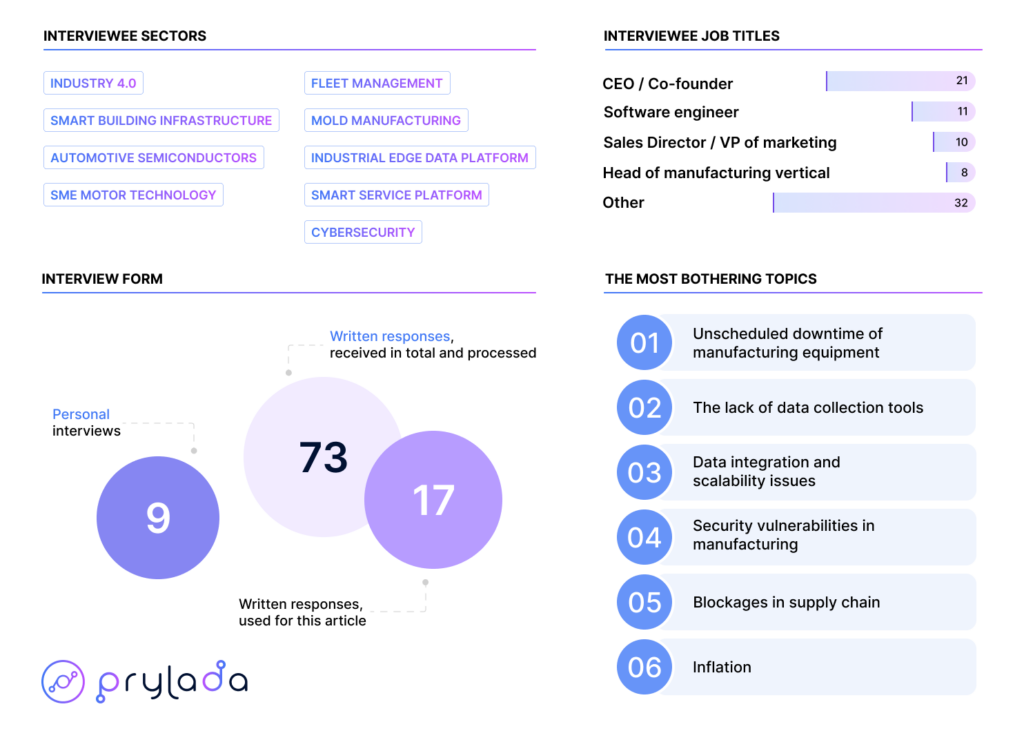
Wie hat sich der Fertigungsmarkt in den letzten 5 Jahren verändert?
Verbraucherpräferenzen in Bezug auf Produktanpassungen, wettbewerbsfähige Preise und die besten Lieferrahmen sind für produzierende Unternehmen zu den Hauptantriebskräften geworden, ihren Arbeitsansatz zu überdenken. Um mit den modernen Anforderungen Schritt zu halten, müssen sie ihre Produktivität durch den Einsatz digitaler Technologien steigern. Zu diesen Technologien gehören digital unterstützte Nachhaltigkeitslösungen, digitale Zwillinge, autonome mobile Roboter, Augmented Reality, KI und maschinelles Lernen.
"Die Realität der Vergangenheit war, dass Hersteller Überstunden machten, Dinge sehr manuell erledigten und nicht unterstützt wurden. Sie haben ihre Arbeit einfach erledigt, und nun hat sich das dahingehend verlagert, dass diese Fertigungsunternehmen von der bloßen Erledigung ihrer Aufgaben zu dem Punkt übergegangen sind, an dem sie große Initiativen zur digitalen Transformation starten müssen."
- Richard Lebovitz, CEO von LeanDNA
Die Hersteller begannen aus folgender Perspektive zu denken:
- Wir müssen viel stärker vernetzt sein
- Wir brauchen nicht nur einen besseren Überblick über die Probleme, mit denen wir zu kämpfen haben, sondern auch darüber, welche Maßnahmen wir ergreifen müssen.
Das Gesamtbild verlagerte sich von der Arbeit, wie sie ist, hin zur digitalen Transformation, bei der Maßnahmen Priorität haben. Darüber hinaus hat COVID-19 die Bedeutung starker und anpassungsfähiger Versorgungsnetzwerke deutlich gemacht. Die unvorhergesehenen Folgen der Pandemie führten zu erheblichen Verlusten Industrieunternehmen ihre aktuellen Geschäftsstrategien zu überdenken. Ziel war es daher, bestehende Prozesse zu optimieren, ihre Abhängigkeit von externen Faktoren zu verringern und so die Widerstandsfähigkeit gegenüber Situationen höherer Gewalt zu erhöhen.
Der Fokus auf Nachhaltigkeit wird zu einer treibenden Kraft für den stärkeren Einsatz intelligenter IoT-Technologien, wodurch die Fertigungsindustrie intelligenter, effizienter und nachhaltiger wird und gleichzeitig das Wohlbefinden der Mitarbeiter verbessert wird. Dies geschieht durch Automatisierung und digitale Transformation und nutzt prädiktive Analysen, um bessere Empfehlungen zu erzielen. Dies wiederum gibt uns ein besseres Verständnis dafür, wo die Engpässe und Herausforderungen liegen.
Andererseits ist der Prozess der Einführung neuer intelligenter Technologien komplizierter und zeitaufwändiger geworden. Herausforderungen in der Lieferkette und Personalengpässe haben dazu geführt, dass sich die gesamte C-Suite intensiv mit betrieblichen Angelegenheiten und Entscheidungen auf der Ebene der Unternehmensebene befasst. Dies führte zu einer größeren Anzahl von Stakeholdern, die die Risiken verstehen, sich auf erwartete Wertvorteile einigen und diese Überlegungen mit anderen Unternehmensinitiativen abwägen mussten.
Das rasante Tempo des technologischen Fortschritts in Bereichen wie Automatisierung, künstlicher Intelligenz und dem Internet der Dinge erfordert von Herstellern, neue Technologien anzupassen und in ihre Abläufe zu integrieren.
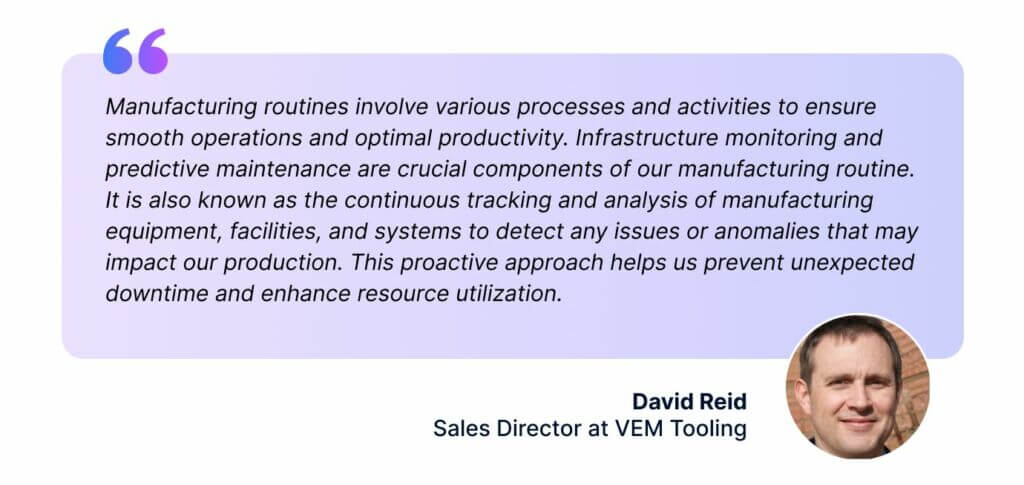
Der Übergang zu neuen Asset-Monitoring-Technologien kann jedoch komplex und kostspielig sein und eine Weiterqualifizierung der Arbeitskräfte sowie die Sicherstellung der Kompatibilität mit bestehenden Systemen erfordern.
Wir haben die häufigsten Herausforderungen und Hindernisse im Zusammenhang mit diesem Übergang zusammengestellt, die uns unsere Befragten mitgeteilt haben. An erster Stelle stehen die Punkte, die wir am häufigsten hören. Dies bedeutet nicht zwangsläufig, dass sie die kritischsten sind, weist aber auf ihre Verbreitung hin. Lass uns anfangen.
Außerplanmäßige Ausfallzeiten von Produktionsanlagen
Die Herstellung moderner Geräte erfordert hochpräzise komplexe Prozesse und hochentwickelte Ausrüstung. Ungeplante Ausfallzeiten von Produktionsanlagen können aufgrund von Ertragsverlusten und verlorener Produktionszeit sehr hohe Kosten verursachen. Jüngste Innovationen im Bereich der vorausschauenden Wartung können erheblich dazu beitragen, Produktivitätsverluste zu reduzieren und viel Aufwand und Zeit zu sparen.
Eine der erfolgreich eingesetzten Techniken zur vorausschauenden Wartung in der Fertigung nutzt die Analyse großer Mengen an Fehlerdaten, Wartungs- und Trace-Daten. Um die Qualität der verwendeten Daten zu verbessern, werden Parameter wie Prozess, Zeitstempel und detaillierte Komponenteninformationen Fehlermodellen zugeordnet, um robuste Datensätze zu erstellen. Mehrere große Halbleiterhersteller haben berichtet, dass sie solche Techniken als Teil ihrer vorausschauenden Wartungsmodelle zur Verbesserung der Ausbeute einsetzen.
Es bleiben Herausforderungen bestehen, da es bei vielen komplexen Prozessen häufig zu Abweichungen und Verschiebungen kommt. Zwischen den Durchläufen werden bestimmte Parameter angepasst, um den Prozess auf dem richtigen Weg zu halten. Techniken wie virtuelle Sensoren, die die Parameterkonfiguration in Echtzeit überwachen und erfassen, können verwendet werden, um eine ordnungsgemäße Steuerung zu ermöglichen. Dies ist derzeit ein aktives Forschungsgebiet, und Forscher erforschen aktiv neue Techniken, einschließlich künstlicher Intelligenz.
Der Mangel an Datenerfassungstools
Da eine eingeschränkte Anlagentransparenz zu höheren Wartungs- und Austauschkosten führt, haben viele Hersteller bereits Schwierigkeiten, grundlegende Maschinendaten zu erfassen. Zu diesen Daten gehören typischerweise Temperatur, Vibration, Geschwindigkeit und andere Leistungsindikatoren.
Für viele Unternehmen kann die Investition in Datenerfassungstools jedoch ein kostspieliges Unterfangen sein. Deshalb arbeiten sie lieber mit verfügbaren Ressourcen, was die Entwicklung in vielerlei Hinsicht behindern kann.
Hersteller, die Echtzeitdaten zur Anlagenüberwachung nutzen möchten, benötigen ein Tool, das automatisch Daten aus beliebigen Quellen verbinden und sammeln kann. Idealerweise sollte es auch in der Lage sein, die Daten zu normalisieren und zu verwalten, Analysen durchzuführen und sich problemlos in Anwendungen von Drittanbietern und Cloud-Computing-Plattformen zu integrieren.
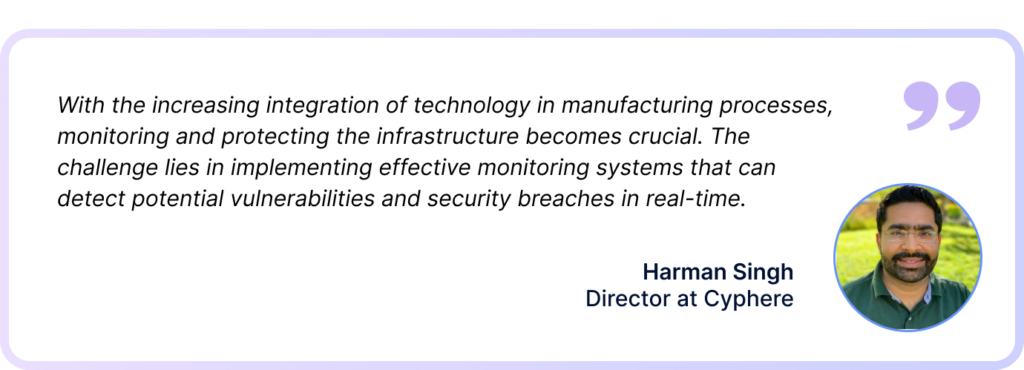
Probleme bei der Datenintegration und Skalierbarkeit
Die Fertigungsinfrastruktur umfasst häufig verschiedene Systeme wie Maschinen, Produktionslinien und Versorgungssysteme. Diese Systeme wurden möglicherweise zu unterschiedlichen Zeiten und unter Verwendung unterschiedlicher Technologien implementiert. Darüber hinaus generiert jedes System Daten in seinem eigenen Format, was die Integration mit Drittsystemen zu einer gewaltigen Aufgabe macht. Inkonsistente Formate, fehlende Werte und Ungenauigkeiten behindern eine effektive Integration.
Mit der Weiterentwicklung von Produktionsanlagen und -prozessen wächst auch die Datenlandschaft. Systeme müssen skalierbar sein, um steigende Datenmengen bewältigen zu können. Es ist von entscheidender Bedeutung, einen nahtlosen und effizienten Datenfluss im gesamten Fertigungsbetrieb sicherzustellen, ohne die Überwachungsinfrastruktur zu überlasten. Dies lässt sich erreichen, indem man in moderne Tools investiert und der Datenqualität Priorität einräumt.

Sicherheitslücken in der Fertigung
Die Fertigungsindustrie ist mit einer sich ständig weiterentwickelnden Landschaft von Cyber-Bedrohungen konfrontiert, von Ransomware-Angriffen bis hin zu Schwachstellen in der Lieferkette. Im Zusammenhang mit Hardware galten gefälschte Produkte von geringerer Qualität als großes Problem bei Halbleitern, während Chips von sicherheitsrelevanten Problemen relativ unberührt blieben.
Allerdings haben Angreifer in den letzten Jahren Methoden gefunden, um den komplizierten Halbleiterherstellungsprozess auszunutzen. Sie haben versucht, die Chip-Architektur zu manipulieren, indem sie mithilfe von Hardware-Trojanern bösartige Logik einführten. Angreifer nutzen diese Trojaner entweder für Denial of Service (DoS) oder Datendiebstahl. Insbesondere Syrien meldete einen großen Trojaner-Angriff, bei dem Angreifer einen Trojaner namens „Kill Switch“ in einen Chip einbauten, um das syrische Luftverteidigungssystem zu deaktivieren und so einen Luftangriff durchzuführen.
In den letzten Jahren haben Hersteller den Einsatz von Datenanalysekonzepten auf Basis von maschinellem Lernen und Internet der Dinge (IoT) ausgeweitet, um sicherzustellen, dass ihre Geräte angemessen geschützt sind. Bei diesen Techniken initialisieren sie zunächst die Ausrüstung für alle Überwachungsparameter und wenden dann maschinelle Lernalgorithmen auf diese Parameter an, um die Parameterklasse in der Ausgabe vorherzusagen. Wenn die Ergebnisse (Ausgabe) nicht mit der Vorhersage übereinstimmen, können Hersteller das Gerät kennzeichnen.
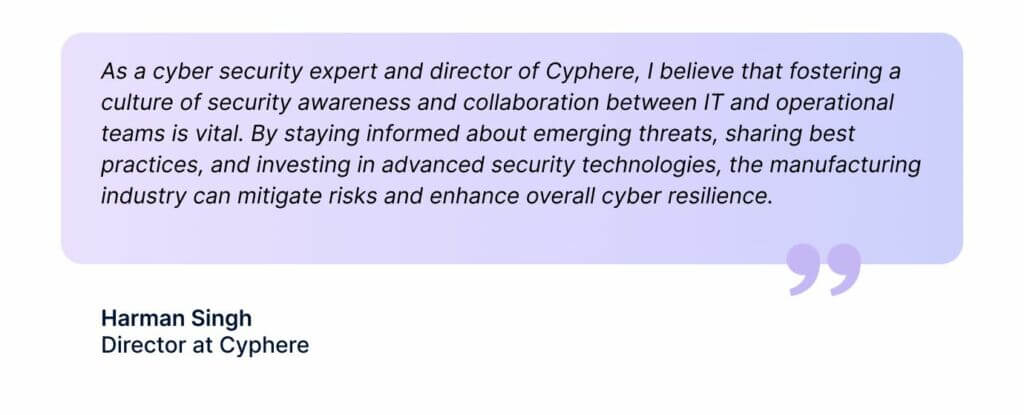
Weitere Hindernisse, die eine nachhaltige Produktion verhindern
Blockaden in der Lieferkette
Hersteller hatten in der Vergangenheit mit mehreren Schwierigkeiten zu kämpfen, und die Prognosen für 2024 zeigen, dass dies noch häufiger der Fall sein wird. Da der Welthandel immer komplexer wird, müssen sich Produzenten darauf vorbereiten, unerwartete oder plötzliche Unterbrechungen in ihren Liefernetzwerken zu überstehen.
Laut einigen unserer Interviewpartner werden Unterbrechungen in den Lieferketten auch in absehbarer Zukunft eine der größten Herausforderungen für die Branche sein. Derzeit sind die Lagerbestände auf dem niedrigsten Stand seit Jahrzehnten, was darauf hindeutet, dass bestimmte Produkte derzeit nicht hergestellt werden können. Der gravierende Mangel an Halbleitern aus Taiwan, China und anderen Offshore-Unternehmen hat zur Schließung einiger Automobilproduktionsstätten geführt. Auch die inländische Produktion hatte mit Schwierigkeiten zu kämpfen.
Inflation
Im Jahr 2023 lag die Inflation aufgrund der steigenden Nachfrage und des unzureichenden Angebots in allen großen Volkswirtschaften nahezu zweistellig. Im nächsten Jahr werden die Preise für wichtige Produktionsrohstoffe wie Aluminium, Öl und Stahl noch weiter steigen, was den Druck auf Unternehmen erhöht, die bereits jetzt versuchen, Kosten zu senken, ohne auf Qualität zu verzichten.
Es ist schwierig, Ressourcen und Investitionen für die Automatisierung der Vermögensüberwachung während der Inflation zu finden. Aber die Hersteller dürfen das Potenzial, das dies für die Branche mit sich bringt, nicht außer Acht lassen. Es kann dazu beitragen, manuelle Fehler zu reduzieren und Aufgaben um das Zehnfache zu beschleunigen.
Um diese Herausforderung zu bewältigen, muss die Branche ein Budget für die Automatisierung bereitstellen und mehr KI-Technologie einführen, um Aufgaben in Echtzeit zu prüfen und zu automatisieren. Dies wird nicht nur dazu beitragen, Kosten zu sparen, sondern auch die Effizienz zu verbessern und Abfall zu reduzieren.
Herausforderungen bei der Einführung digitaler Technologien
Herstellungsprozesse drehen sich um kontinuierliche, routinemäßige Zeitpläne und Aufgaben, die von Hunderten von Lieferanten und Mitarbeitern an mehreren Standorten durchgeführt werden und auf die Produktion von Verbrauchsgütern abzielen. Dies macht es für Unternehmen außerordentlich schwierig, aktuelle Routinen zu überwachen und Verbesserungsmöglichkeiten zu identifizieren.
Hersteller können jeden Schritt entlang ihrer gesamten Wertschöpfungskette einfach nachverfolgen, indem sie Echtzeit-IoT-basierte Überwachungstechnologien implementieren. Solche Technologien werden ihnen helfen, Lücken in ihren Nachhaltigkeitszielen besser zu verstehen und Lösungen zur Verbesserung von Effizienz, Ertrag und Compliance zu finden.
Eine intelligente Anlagenüberwachung ist typischerweise mit zwei Herausforderungen verbunden. Die erste umfasst die Integration und Aufrüstung älterer Geräte, um sie mit der neuen Technologie kompatibel zu machen und so das volle Potenzial von Industrie 4.0 auszuschöpfen. Bei der zweiten geht es um die Umschulung des Personals, um sicherzustellen, dass es ein neues Überwachungssystem effektiv überwachen, nutzen und davon profitieren kann.
Kleinere Hersteller empfinden die Anfangsinvestition in neue Technologien oft als entmutigend. Es ist jedoch wichtig zu erkennen, dass sowohl die digitale Transformation als auch die Mitarbeitertransformation schrittweise Prozesse sind. Diese Veränderungen treten nicht über Nacht auf.
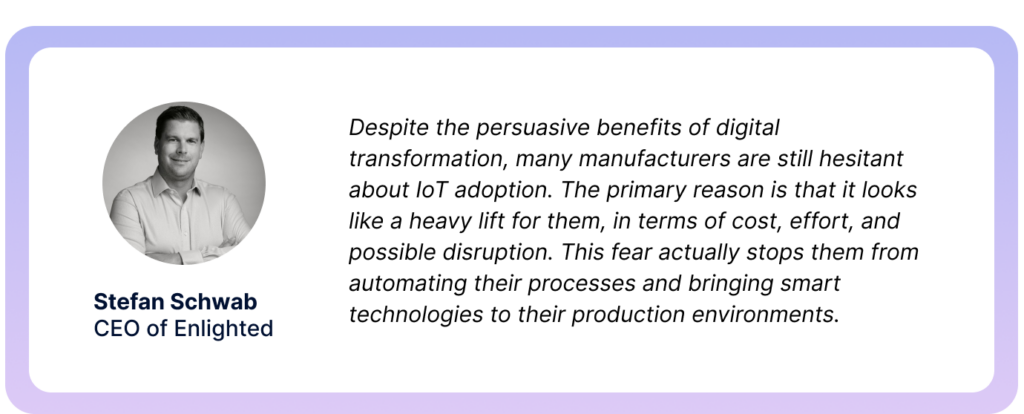
Fazit
Die Fertigungsindustrie erlebt bereits die Auswirkungen von Automatisierung und Robotik, wie z. B. künstliche Intelligenz, das Internet der Dinge, Sensoren, Roboter am Boden und den zunehmenden Einsatz robotergestützter Prozessautomatisierung. Die steigende Nachfrage nach der Einführung digitaler Technologien und die Vorteile, die produzierende Unternehmen daraus ziehen können, treiben das Wachstum der Digitalisierung voran.
Im Rahmen ihrer kontinuierlichen Bemühungen, die Herausforderungen zu bewältigen, mit denen die Branche heutzutage konfrontiert ist, implementieren Hersteller IoT-basierte Lösungen für die intelligente Anlagenüberwachung. Allerdings hängt die Wahl der Technologie und deren Umsetzungsmöglichkeit noch von den Geschäftsmöglichkeiten und -bedürfnissen ab.
Ungeplante Ausfallzeiten von Industriemaschinen, Probleme bei der Datenerfassung, Sicherheitslücken und Skalierbarkeitseinschränkungen sind die Herausforderungen, die in der Fertigungslandschaft an erster Stelle stehen und durch IoT-basierte Überwachungstechnologien angegangen werden können. Solche Technologien liefern Herstellern granulare, kontextualisierte Daten entlang der gesamten Lieferkette, sodass sie Probleme schnell lokalisieren und Maßnahmen ergreifen können.
Darüber hinaus können sie potenzielle Probleme vorhersagen, bevor sie auftreten, und so Rückrufe und andere erhebliche Umweltrisiken vermeiden. Mit der Zeit werden Überwachungstechnologien es Benutzern ermöglichen, den Fortschritt ihrer Nachhaltigkeitsziele zu verfolgen und die Einhaltung der Branchenvorschriften sicherzustellen.
Wir möchten uns bei allen bedanken, die an unserem Kundenentwicklungsinterview teilgenommen haben:
- Vatsal Shah, CEO von Lackmus
- Stefan Schwab, CEO von Erleuchtet
- Tom Richter, Global Head of Discrete and Process Manufacturing Verticals for Digital Industries bei Nokia
- Nils Arnold, CEO von Adance
- Duncan Kerr, ehemaliger CEO von Aeristech
- Richard Lebovitz, CEO von LeanDNA
- Gulroz Singh, SoC-Sicherheitsarchitekt bei NXP Semiconductors
- Donnie Rand, Marketingkoordinator bei American Association of Owner Operators, LLC
- David Reid, Vertriebsleiter bei VEM-Werkzeuge
- Derrick Hathaway, Vertriebsleiter bei VEM Medizin
- Harman Singh, Direktor bei Chiffre
- Doug Lawson, CEO von ThinkIQ
- Und andere Branchenexperten, deren Kommentare für diesen Artikel berücksichtigt wurden
- SEO-gestützte Content- und PR-Distribution. Holen Sie sich noch heute Verstärkung.
- PlatoData.Network Vertikale generative KI. Motiviere dich selbst. Hier zugreifen.
- PlatoAiStream. Web3-Intelligenz. Wissen verstärkt. Hier zugreifen.
- PlatoESG. Kohlenstoff, CleanTech, Energie, Umwelt, Solar, Abfallwirtschaft. Hier zugreifen.
- PlatoHealth. Informationen zu Biotechnologie und klinischen Studien. Hier zugreifen.
- Quelle: https://www.iotforall.com/experts-discuss-predictive-maintenance-and-innovation-in-manufacturing
- :hast
- :Ist
- :nicht
- :Wo
- $UP
- 1
- 10
- 2023
- 2024
- 21.
- 361
- a
- Fähig
- LiveBuzz
- unterbringen
- über
- Action
- Aktionen
- aktiv
- aktiv
- automatisch
- Zusatz
- angesprochen
- Bereinigt
- Die Annahme
- Adoption
- Fortschritte
- gegen
- AI
- gezielt
- LUFT
- Algorithmen
- ausrichten
- Alle
- zuordnen
- Zulassen
- bereits
- ebenfalls
- Beträge
- an
- Analyse
- Analytik
- und
- Vorweggenommen
- jedem
- Anwendungen
- Bewerben
- Ansatz
- passend
- Architektur
- SIND
- Bereich
- Bereiche
- um
- künstlich
- künstliche Intelligenz
- AS
- Vermögenswert
- damit verbundenen
- Verein
- At
- Attacke
- Anschläge
- Versuche
- Augmented
- Erweiterte Realität
- automatisieren
- Im Prinzip so, wie Sie es von Google Maps kennen.
- Automation
- Automobilindustrie
- Autonom
- verfügbar
- Vermeidung von
- Balance
- Barrieren
- basierend
- basic
- BE
- werden
- wird
- war
- Bevor
- Sein
- Nutzen
- Vorteile
- BESTE
- Besser
- zwischen
- Big
- Auftrieb
- beide
- Engpässe
- Brings
- Haushalt
- Geschäft
- Unternehmen
- aber
- by
- C-Suite
- namens
- CAN
- Kann bekommen
- kann keine
- Erfassung
- Ringen
- Jahrhundert
- CEO
- sicher
- Kette
- Ketten
- challenges
- Herausforderungen
- geändert
- Änderungen
- China
- Chip
- Pommes frites
- Wahl
- Klasse
- Menu
- Cloud
- Cloud Computing
- CO
- sammeln
- Sammlung
- Bemerkungen
- gemeinsam
- Unternehmen
- Unternehmen
- Kompatibilität
- kompatibel
- gezwungen
- Wettbewerb
- wettbewerbsfähig
- Komplex
- Compliance
- Komponente
- begreifen
- inbegriffen
- Computing
- Konzepte
- durchgeführt
- Konfiguration
- Vernetz Dich
- Folgen
- Überlegungen
- Einschränkungen
- Kontext
- fortsetzen
- kontinuierlich
- Smartgeräte App
- -Koordinator
- Kosten
- teuer werden
- Kosten
- Fälschung
- COVID-19
- erstellen
- kritischem
- Strom
- Aktuellen Zustand
- Zur Zeit
- Kunde
- Anpassung
- Cyber-
- technische Daten
- Datenanalyse
- Datenqualität
- Datensätze
- Christian
- Jahrzehnte
- Entscheidungen
- tief
- Militär
- Lieferanten
- Demand
- Anforderungen
- Demographie
- Denial of Service
- Abhängigkeit
- hängt
- detailliert
- Entwicklung
- Geräte
- anders
- schwer
- Schwierigkeiten
- digital
- Digitale Transformation
- Digitale Zwillinge
- Digitalisierung
- digital
- Ziffern
- Direktor
- diskutieren
- diskutiert
- verschieden
- do
- die
- Dabei
- Inländische
- erledigt
- DOS
- doppelt
- zweistellig
- Ausfallzeit
- Antrieb
- Treiber
- Fahren
- zwei
- im
- jeder
- leicht
- Wirtschaft
- Effektiv
- effektiv
- Effekten
- Effizienz
- effizient
- Anstrengung
- Bemühungen
- entweder
- eingebettet
- beschäftigt
- Mitarbeiter
- Mitarbeiter
- ermöglichen
- freigegeben
- ermöglichen
- Unterfangen
- engagieren
- Eine Verbesserung der
- gewährleisten
- Gewährleistung
- Ganz
- Umwelt-
- Ausrüstung
- Fehler
- essential
- Sogar
- jedermann
- entwickelt sich
- außergewöhnlich
- ausführen
- vorhandenen
- ergänzt
- erleben
- Experten
- Ausnutzen
- Möglichkeiten sondieren
- extern
- konfrontiert
- Gesichter
- Anlagen
- zugewandt
- Faktoren
- vertraut machen
- wenige
- Finden Sie
- Vorname
- Boden
- Fluss
- Setzen Sie mit Achtsamkeit
- Folgende
- Aussichten für
- Zwingen
- absehbar
- Format
- Früher
- ehemaliger CEO
- gewaltig
- gefunden
- häufig
- häufig
- für
- voller
- Zukunft
- Lücken
- gesammelt
- erzeugt
- bekommen
- bekommen
- ABSICHT
- gibt
- Global
- Welthandel
- Kundenziele
- Ziele
- weg
- Waren
- habe
- allmählich
- mehr
- sehr
- Wächst
- Wachstum
- Pflege
- passieren
- Los
- hart
- Hardware
- Haben
- ganzer
- hören
- Hilfe
- GUTE
- Besondere
- behindern
- historisch
- Ultraschall
- aber
- http
- HTTPS
- hunderte
- im Idealfall
- identifizieren
- if
- ignorieren
- implementieren
- Implementierung
- umgesetzt
- Umsetzung
- Bedeutung
- zu unterstützen,
- Verbesserung
- Verbesserung
- in
- das
- Dazu gehören
- Einschließlich
- Erhöhung
- hat
- zunehmend
- zeigen
- Anzeige
- Anzeigen
- industriell
- Branchen
- Energiegewinnung
- Industrie 4.0
- Inflation
- Information
- Infrastruktur
- Anfangs-
- Initiativen
- Innovationen
- Eingänge
- integrieren
- Integration
- Integration
- Intelligenz
- Intelligent
- wollen
- Internet
- Internet der Dinge
- Internet der Dinge (IoT)
- Interview
- Befragte
- Interviews
- in
- kompliziert
- einführen
- Einführung
- Investitionen
- Investition
- Investments
- beinhaltet
- iot
- Problem
- Probleme
- IT
- SEINE
- Job
- jpg
- nur
- Behalten
- Wesentliche
- Mangel
- Landschaft
- grosse
- Nachname
- starten
- lernen
- geführt
- Legacy
- Niveau
- Cholesterinspiegel
- Nutzung
- Gefällt mir
- Limitiert
- Linien
- Standorte
- Logik
- suchen
- Verlust
- Verluste
- verloren
- Los
- senken
- niedrigste
- Maschine
- Maschinelles Lernen
- Maschinen
- Maschinen
- Main
- Wartung
- Dur
- MACHT
- Making
- böswilligen
- verwalten
- manuell
- hergestellt
- Hersteller
- Herstellung
- Fertigungsindustrie
- viele
- Markt
- Marketing
- Spiel
- Angelegenheiten
- max-width
- Kann..
- bedeuten
- Mittel
- Methoden
- minimieren
- Kommt demnächst...
- Mobil
- für
- modern
- Geld
- Überwachen
- Überwachung
- mehr
- effizienter
- Zudem zeigt
- vor allem warme
- mehrere
- sollen
- Notwendig
- Need
- erforderlich
- Bedürfnisse
- Netzwerke
- Neu
- Neue Technologien
- weiter
- Nokia
- vor allem
- jetzt an
- Anzahl
- Hindernisse
- auftreten
- of
- Angebote
- vorgenommen,
- ÖL
- on
- EINEM
- Einsen
- laufend
- einzige
- betrieben
- Betriebs-
- Einkauf & Prozesse
- Betreiber
- Entwicklungsmöglichkeiten
- Optimieren
- Option
- or
- Andere
- UNSERE
- Möglichkeiten für das Ausgangssignal:
- übrig
- Gesamt-
- über Nacht
- überwältigend
- Eigentümer
- Frieden
- Parameter
- Parameter
- Teil
- teil
- passt
- ausführen
- Leistung
- Personal
- Perspektive
- ein Bild
- platziert
- Plattformen
- Plato
- Datenintelligenz von Plato
- PlatoData
- Punkte
- positioniert
- möglich
- Potenzial
- vorhersagen
- Prognose
- Prognosen
- prädiktive
- Vorausschauende Analytik
- bevorzugen
- Vorlieben
- Danach
- Druck
- Prävalenz
- verhindern
- Verhütung
- Preise
- gebühr
- Priorisierung
- Probleme
- Prozessdefinierung
- Automatisierung von Prozessen
- anpassen
- Producers
- Produkt
- Produktion
- PRODUKTIVITÄT
- Produkte
- Profis
- Fortschritt
- ordnungsgemäße
- geschützt
- Qualität
- schnell
- Angebot!
- and
- Ransomware
- Ransomware-Angriffe
- schnell
- Erreichen
- echt
- Echtzeit
- Echtzeitdaten
- Realität
- kürzlich
- erkennen
- Empfehlungen
- noch einmal überdenken
- Veteran
- Abfall reduzieren
- Vorschriften
- verhältnismäßig
- bleiben
- blieb
- entfernt
- Ersatz
- Berichtet
- erfordert
- Forschungsprojekte
- Forscher
- Elastizität
- Umschulung
- Downloads
- Folge
- Folge
- Die Ergebnisse
- Richter
- Anstieg
- Risiken
- Roboter-Prozessautomatisierung
- Robotik
- Roboter
- robust
- Routine
- Führen Sie
- läuft
- opfern
- Sicherheit
- Vertrieb
- gleich
- Speichern
- Skalierbarkeit
- skalierbaren
- Knappheit
- nahtlos
- Zweite
- Sicherheitdienst
- Halbleiter
- Halbleiter
- Sensoren
- Modellreihe
- kompensieren
- Sets
- mehrere
- schwer
- von Locals geführtes
- verschoben
- Schichten
- Engpässe
- sollte
- erklären
- signifikant
- einfach
- Umstände
- smart
- schlauer
- So
- Lösungen
- LÖSEN
- einige
- anspruchsvoll
- Quelle
- spezifisch
- Geschwindigkeit
- Stakeholder
- begonnen
- Bundesstaat
- Stahl, schwarz
- stefan
- Schritt
- Strategien
- Stärke
- stark
- Kämpfen
- Struggling
- Erfolgreich
- so
- plötzlich
- Lieferanten
- liefern
- Supply Chain
- Herausforderungen in der Lieferkette
- Lieferketten
- Unterstützte
- Umfrage
- Nachhaltigkeit
- nachhaltiger
- Syrien
- System
- Systeme und Techniken
- Taiwan
- Nehmen
- gemacht
- Target
- Aufgabe
- und Aufgaben
- Team
- Techniken
- technologische
- Technologies
- Technologie
- Neigen
- zur Verbesserung der Gesundheitsgerechtigkeit
- Das
- Diebstahl
- ihr
- Sie
- sich
- dann
- Diese
- vom Nutzer definierten
- Denken
- basierte Online-to-Offline-Werbezuordnungen von anderen gab.
- fehlen uns die Worte.
- diejenigen
- dachte
- Bedrohungen
- Durch
- während
- So
- Zeit
- Zeitaufwendig
- mal
- Zeitstempel
- zu
- Werkzeug
- Werkzeuge
- gegenüber
- Spur
- verfolgen sind
- Handel
- Transformation
- Übergang
- Trojan
- versuchen
- Versuch
- WENDE
- Twins
- XNUMX
- typisch
- unberührt
- verstehen
- Verständnis
- Unerwartet
- unvorhergesehen
- Höherqualifizierung
- us
- Anwendungsbereich
- -
- benutzt
- Nutzer
- verwendet
- Verwendung von
- Nutzen
- wertvoll
- Wertvolle Information
- Wert
- Werte
- Variieren
- Geschwindigkeit
- Vertikalen
- sehr
- Assistent
- Sichtbarkeit
- Volumen
- Sicherheitslücken
- wurde
- Abfall / Verschnitt
- Wege
- we
- waren
- Was
- welche
- während
- WHO
- deren
- warum
- werden wir
- mit
- .
- ohne
- Arbeiten
- Belegschaft
- arbeiten,
- Jahr
- Jahr
- noch
- Ausbeute
- Zephyrnet