การป้องกันการแพร่กระจายของข้อบกพร่องอย่างเป็นระบบในกระบวนการออกแบบจนถึงการผลิตเซมิคอนดักเตอร์ในปัจจุบัน จำเป็นต้องมีขั้นตอนการตรวจสอบ การวิเคราะห์ และการปรับให้เหมาะสมหลายขั้นตอน เครื่องมือที่เกี่ยวข้องในกระบวนการนี้อาจรวมถึงการตรวจสอบกฎการออกแบบ (DRC) การตรวจสอบการแก้ไขความใกล้เคียงด้วยแสง (OPC) การเขียนมาสก์และมาตรวิทยา/การตรวจสอบการพิมพ์เวเฟอร์ (เพื่อวัดกระบวนการ) มาตรวิทยา/การตรวจสอบการพิมพ์เวเฟอร์ และการวิเคราะห์ความล้มเหลวทางกายภาพเพื่อยืนยันความล้มเหลว การวินิจฉัย การแลกเปลี่ยนข้อมูลและการเพิ่มประสิทธิภาพร่วมระหว่างขั้นตอนเหล่านี้เป็นกระบวนการที่ซับซ้อน โดยมีลูปฟีดไปข้างหน้าและฟีดแบ็คจำนวนมาก การสื่อสารมักถูกขัดขวางโดย "กำแพง" ระหว่างส่วนต่างๆ ของเทคโนโลยีกระบวนการ ซึ่งทำให้นวัตกรรมช้าลง ในการประชุม SPIE เมื่อเร็วๆ นี้ Siemens EDA ได้นำเสนอคำปราศรัยสำคัญที่เสนอแนวทางต่างๆ ในการทำลายกำแพงเหล่านี้ เพื่อปรับปรุงการออกแบบชิปในกระบวนการผลิต อ่านต่อเพื่อดูว่า Siemens ตั้งเป้าที่จะทำลายอุปสรรคด้านนวัตกรรมด้วยการขยายการเพิ่มประสิทธิภาพร่วมด้านเทคโนโลยีการออกแบบอย่างไร
เกี่ยวกับคีย์โน้ต
SPIE เป็นสมาคมระหว่างประเทศด้านทัศนศาสตร์และโฟโตนิกส์ องค์กรนี้มีอายุย้อนไปถึงปี 1955 และการประชุมได้กลายเป็นงานสำคัญสำหรับหัวข้อการออกแบบและการผลิตขั้นสูง ในงานปีนี้ ซีเมนส์ได้นำเสนอประเด็นสำคัญซึ่งเป็นหัวข้อของโพสต์นี้ มีผู้มีส่วนร่วมในการนำเสนอมากมาย รวมถึง Le Hong, Fan Jiang, Yuansheng Ma, Srividya Jayaram, Joe Kwan, Siemens EDA (สหรัฐอเมริกา); Doohwan Kwak, Siemens EDA (สาธารณรัฐเกาหลี); สังกรณารายานันท์ ปนินจัต อายัพปัน, Siemens EDA (อินเดีย) หัวข้อเสวนาคือ ขยายการเพิ่มประสิทธิภาพเทคโนโลยีการออกแบบร่วมกันตั้งแต่การเปิดตัวเทคโนโลยีไปจนถึง HVM.
การเสวนานี้เป็นส่วนหนึ่งของเซสชั่นการเพิ่มประสิทธิภาพร่วมด้านเทคโนโลยีการออกแบบ (DTCO) แนวคิดนี้ไม่ใช่เรื่องใหม่ แต่ Siemens พิจารณาการประยุกต์ใช้ในขอบเขตที่กว้างขึ้นของกระบวนการ ตั้งแต่การออกแบบไปจนถึงการผลิตในปริมาณมาก (HVM) แนวคิดและผลลัพธ์ที่นำเสนอมีนัยสำคัญ มาดูกันดีกว่า
สิ่งที่ถูกนำเสนอ
ขั้นแรก เราจะนำเสนอสถานะปัจจุบันของการใช้งาน DTCO ในส่วนสำคัญของระบบนิเวศ จากมุมมองของการออกแบบ บริษัท fabless ขั้นสูงหลายแห่งมีทีมงาน DFM ที่มองเห็นขีดจำกัดของแนวทางตามรูปแบบ สิ่งที่จำเป็นจริงๆ คือเทคโนโลยีใหม่ที่จะอำนวยความสะดวกในการเรียนรู้โดยไม่ต้องพึ่งพาโรงหล่อ
โรงหล่อกำลังใช้วิธีการเรียนรู้ของเครื่องตามรูปแบบแบบเดรัจฉาน ซึ่งมีต้นทุนสูงแต่ไม่ได้ผลอย่างสมบูรณ์ พวกเขายังมองหาการขุดข้อมูลที่มีประสิทธิภาพจากข้อมูลการผลิตจำนวนมหาศาลที่พวกเขาสร้างขึ้น ผู้จำหน่ายอุปกรณ์และผู้จำหน่าย EDA ทำงานร่วมกันอย่างใกล้ชิดมากขึ้น และกำลังคิดค้นโซลูชันการเรียนรู้ของเครื่องที่มีประสิทธิภาพมากขึ้น
เมื่อย้อนกลับไปเล็กน้อย พบว่ามีกำแพงกั้นระหว่างขั้นตอนการออกแบบและการผลิตของกระบวนการ บริษัท Fabless สร้างการออกแบบ ดำเนินการ DRC และการออกแบบเพื่อการผลิต (DFM) จากนั้นพวกเขาก็โยนมันข้ามกำแพงให้กับทีม OPC/RET ภายในโรงหล่อหรือ IDM การออกแบบจะทำให้งานต่างๆ เช่น OPC และการตรวจสอบเสร็จสิ้น จากนั้นข้อมูลจะถูกโยนข้ามผนังอีกด้านเพื่อเขียนมาสก์และมาตรวิทยา/การตรวจสอบ ผนังสุดท้ายมีไว้สำหรับการประดิษฐ์ ที่นี่จะเป็นการทดสอบทางไฟฟ้าและการวิเคราะห์ความล้มเหลว เมื่อพบสาเหตุที่แท้จริงของความล้มเหลวก็ผ่านไป 6-18 เดือนแล้ว นั่นเป็นการวนซ้ำความคิดเห็นที่ยาวมาก กราฟิกที่ด้านบนของโพสต์นี้แสดงถึงกระบวนการนี้
DTCO พยายามที่จะทลายกำแพงแต่วิธีการที่มีอยู่ยังไม่สมบูรณ์ DTCO แบบดั้งเดิมเริ่มต้นตั้งแต่เนิ่นๆ ในการพัฒนากระบวนการ เริ่มต้นด้วยความต้องการในการปรับขนาด เซลล์มาตรฐานจะถูกกำหนด และการสังเคราะห์ สถานที่ และเส้นทางจะถูกดำเนินการเพื่อสร้างรูปแบบพื้นฐานและวัดประสิทธิภาพและกำลัง การให้ผลผลิตของ SRAM ก็เสร็จสิ้นเช่นกัน และข้อมูลนั้นจะวนกลับไปที่การออกแบบเซลล์มาตรฐาน
สิ่งที่นำเสนอในประเด็นสำคัญของ SPIE เป็นวิธีหนึ่งที่จะขยายแนวคิดการเพิ่มประสิทธิภาพร่วมนี้ไปยังกระบวนการทั้งหมดตั้งแต่การออกแบบไปจนถึงการผลิต แนวทางนี้เกี่ยวข้องกับการทำให้การไหลเวียนของข้อมูลง่ายขึ้นตั้งแต่การออกแบบไปจนถึงกระบวนการขั้นสุดท้ายและการวิเคราะห์ทางกายภาพโดยการสร้างช่องทางข้อมูล
แม้ว่าสิ่งนี้จะฟังดูตรงไปตรงมา แต่ก็ไม่ใช่ มีการหารือถึงความท้าทายหลายประการด้วยแนวทางที่เป็นรูปธรรมเพื่อบรรเทาปัญหา ตัวอย่างเช่น การออกแบบในช่วงแรกๆ สามารถสร้างได้ด้วยเครื่องกำเนิดไฟฟ้าแบบเค้าโครงสังเคราะห์ เพื่อช่วยปรับเทียบกระบวนการกับปัญหาการออกแบบจริงในขณะที่กระบวนการได้รับการพัฒนา วิธีนี้สามารถบรรเทาความประหลาดใจหลายประการที่กำลังเผชิญกับการระงับกระบวนการตั้งแต่เนิ่นๆ ได้
การจัดการกับข้อมูลปริมาณมหาศาลถือเป็นความท้าทายอีกประการหนึ่ง การใช้เทคนิคการบีบอัดที่ซับซ้อนใหม่ทำให้สามารถปรับปรุงได้ 30 เท่า สิ่งนี้ช่วยปรับปรุงงานการจัดการข้อมูลและการวิเคราะห์ไม่น้อย มีแนวคิดที่เรียกว่า AI . อธิบายได้ สามารถช่วยค้นหาสาเหตุของปัญหาได้รวดเร็วยิ่งขึ้น ความสามารถในการฝึกโมเดล AI ใหม่ในกระบวนการผลิตในภายหลังโดยไม่ทำให้ผลลัพธ์ก่อนหน้านี้เป็นโมฆะเป็นอีกด้านที่ต้องปรับปรุง นอกจากนี้ในด้านการวิเคราะห์ข้อมูลยังมีเทคนิคในการจัดการกับ "ข้อมูลที่ไม่สมดุล" ตัวอย่างเช่น อาจมีฮอตสปอตหนึ่งจุดที่พบใน 100,000,000 รูปแบบ
การรวมทั้งหมดนี้เข้าด้วยกันจะสามารถสร้างโฟลว์การออกแบบตั้งแต่ต้นจนจบที่มีประสิทธิภาพมากขึ้น ดังแสดงในรูปด้านล่าง
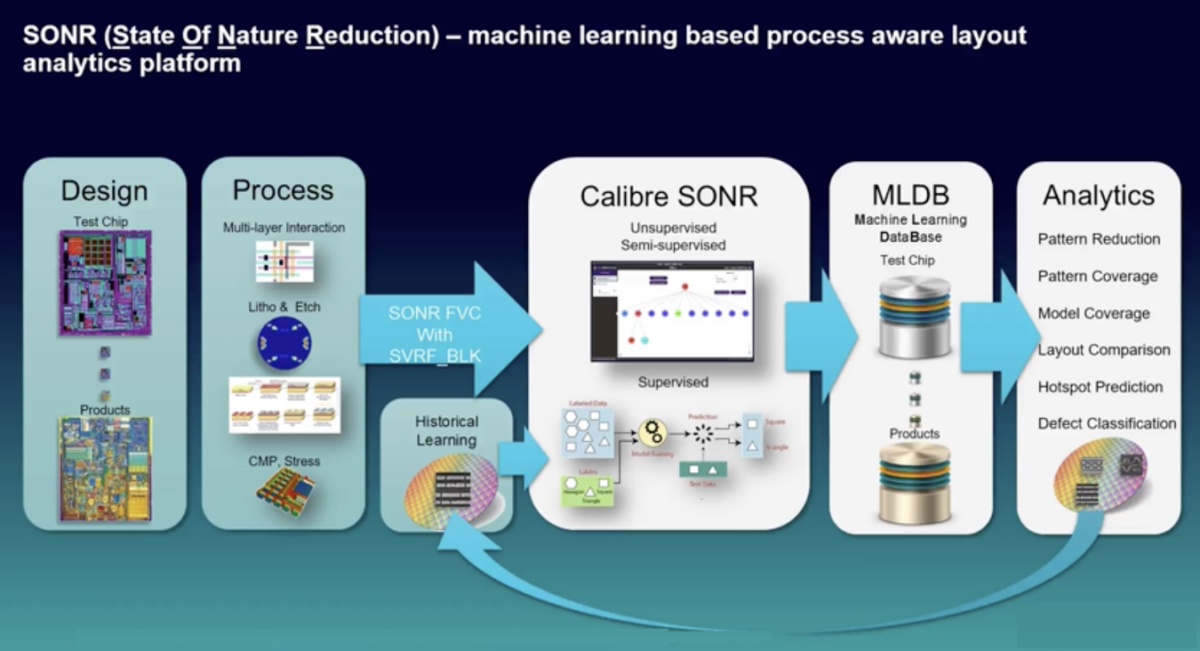
เพื่อเรียนรู้เพิ่มเติม
ผลกระทบของแนวทางที่ระบุไว้ในการนำเสนอประเด็นสำคัญนี้มีความสำคัญมาก คุณสามารถ ดูการนำเสนอและเข้าถึงเอกสารไวท์เปเปอร์เกี่ยวกับกระบวนการได้ที่นี่. มีข้อมูลที่เป็นประโยชน์มากมายที่จะได้รับ และนั่นคือวิธีที่ Siemens ตั้งเป้าที่จะทำลายอุปสรรคด้านนวัตกรรมด้วยการขยายการเพิ่มประสิทธิภาพร่วมด้านเทคโนโลยีการออกแบบ
แชร์โพสต์นี้ผ่าน:
- เนื้อหาที่ขับเคลื่อนด้วย SEO และการเผยแพร่ประชาสัมพันธ์ รับการขยายวันนี้
- PlatoData.Network Vertical Generative Ai เพิ่มพลังให้กับตัวเอง เข้าถึงได้ที่นี่.
- เพลโตไอสตรีม. Web3 อัจฉริยะ ขยายความรู้ เข้าถึงได้ที่นี่.
- เพลโตESG. คาร์บอน, คลีนเทค, พลังงาน, สิ่งแวดล้อม แสงอาทิตย์, การจัดการของเสีย. เข้าถึงได้ที่นี่.
- เพลโตสุขภาพ เทคโนโลยีชีวภาพและข่าวกรองการทดลองทางคลินิก เข้าถึงได้ที่นี่.
- ที่มา: https://semiwiki.com/events/339386-spie-2023-buzz-siemens-aims-to-break-down-innovation-barriers-by-extending-design-technology-co-optimization/
- :มี
- :เป็น
- :ไม่
- $ ขึ้น
- 000
- 100
- 2023
- a
- ความสามารถ
- เข้า
- ข้าม
- ที่อยู่
- สูง
- AI
- โมเดล AI
- จุดมุ่งหมาย
- ทั้งหมด
- บรรเทา
- ด้วย
- an
- การวิเคราะห์
- และ
- อื่น
- การใช้งาน
- เข้าใกล้
- วิธีการ
- เป็น
- AREA
- AS
- At
- ความพยายามในการ
- ใช้ได้
- กลับ
- อุปสรรค
- ขั้นพื้นฐาน
- BE
- กลายเป็น
- รับ
- ด้านล่าง
- ระหว่าง
- บิต
- ทำลาย
- ที่กว้างขึ้น
- แต่
- by
- ที่เรียกว่า
- CAN
- ก่อให้เกิด
- สาเหตุที่
- เซลล์
- ท้าทาย
- ความท้าทาย
- ช่อง
- การตรวจสอบ
- ชิป
- ใกล้ชิด
- CO
- อย่างไร
- มา
- การสื่อสาร
- บริษัท
- อย่างสมบูรณ์
- ซับซ้อน
- แนวคิด
- คอนกรีต
- การประชุม
- ยืนยัน
- ผู้ให้
- แพง
- สร้าง
- ที่สร้างขึ้น
- การสร้าง
- ปัจจุบัน
- สถานะปัจจุบัน
- ขณะนี้
- ข้อมูล
- การวิเคราะห์ข้อมูล
- วันที่
- จัดการ
- กำหนด
- การพึ่งพาอาศัยกัน
- ออกแบบ
- การออกแบบ
- รายละเอียด
- พัฒนา
- พัฒนาการ
- การวินิจฉัยโรค
- กล่าวถึง
- ทำ
- ลง
- DRC
- ก่อน
- ก่อน
- ง่ายดาย
- ระบบนิเวศ
- มีประสิทธิภาพ
- ที่มีประสิทธิภาพ
- การเปิดใช้งาน
- จบสิ้น
- ทั้งหมด
- อุปกรณ์
- เหตุการณ์
- ตัวอย่าง
- ตลาดแลกเปลี่ยน
- ขยายออก
- การขยาย
- ต้องเผชิญกับ
- อำนวยความสะดวก
- ความล้มเหลว
- แฟน
- เร็วขึ้น
- ข้อเสนอแนะ
- รูป
- สุดท้าย
- หา
- ไหล
- สำหรับ
- พบ
- โรงหล่อ
- ราคาเริ่มต้นที่
- ที่ได้รับ
- วัด
- เครื่องกำเนิดไฟฟ้า
- กราฟิก
- การจัดการ
- มี
- ช่วย
- โปรดคลิกที่นี่เพื่ออ่านรายละเอียดเพิ่มเติม
- ฮ่องกง
- ร้อน
- สรุป ความน่าเชื่อถือของ Olymp Trade?
- HTTPS
- ความคิด
- ส่งผลกระทบ
- ผลกระทบ
- ปรับปรุง
- การปรับปรุง
- ช่วยเพิ่ม
- in
- ประกอบด้วย
- รวมทั้ง
- อินเดีย
- ข้อมูล
- นักวิเคราะห์ส่วนบุคคลที่หาโอกาสให้เป็นไปได้มากที่สุด
- International
- ร่วมมือ
- ที่เกี่ยวข้องกับการ
- ปัญหา
- IT
- ITS
- โจ
- คีย์
- ประเด็นสำคัญ
- เกาหลี
- ต่อมา
- เปิดตัว
- แบบ
- เรียนรู้
- การเรียนรู้
- ขีด จำกัด
- นาน
- ดู
- มอง
- Lot
- เครื่อง
- เรียนรู้เครื่อง
- การผลิต
- หลาย
- หน้ากาก
- มาก
- ความกว้างสูงสุด
- อาจ..
- วัด
- วิธีการ
- การทำเหมืองแร่
- บรรเทา
- โมเดล
- เดือน
- ข้อมูลเพิ่มเติม
- มีประสิทธิภาพมากขึ้น
- มาก
- จำเป็นต้อง
- จำเป็น
- ใหม่
- of
- มักจะ
- on
- ONE
- เลนส์
- เลนส์และโฟโตนิกส์
- การเพิ่มประสิทธิภาพ
- or
- organizacja
- ออก
- ที่ระบุไว้
- เกิน
- กระดาษ
- ส่วนหนึ่ง
- ส่วน
- ผ่าน
- รูปแบบ
- ดำเนินการ
- การปฏิบัติ
- ดำเนินการ
- มุมมอง
- กายภาพ
- สถานที่
- เวที
- เพลโต
- เพลโตดาต้าอินเทลลิเจนซ์
- เพลโตดาต้า
- เป็นไปได้
- โพสต์
- อำนาจ
- นายกรัฐมนตรี
- การเสนอ
- นำเสนอ
- การพิมพ์
- ปัญหาที่เกิดขึ้น
- กระบวนการ
- การเผยแผ่
- เสนอ
- ทีเดียว
- อ่าน
- จริง
- จริงๆ
- เมื่อเร็ว ๆ นี้
- สาธารณรัฐ
- ต้อง
- ผลสอบ
- ราก
- เส้นทาง
- กฎ
- ปรับ
- ขอบเขต
- เห็น
- เห็น
- ที่กำลังมองหา
- สารกึ่งตัวนำ
- ชุด
- เซสชั่น
- แสดง
- ซีเมนส์
- สำคัญ
- การชะลอตัว
- สังคม
- โซลูชัน
- ซับซ้อน
- จุด
- มาตรฐาน
- ที่เริ่มต้น
- เริ่มต้น
- สถานะ
- สหรัฐอเมริกา
- ขั้นตอน
- เป็นกอบเป็นกำ
- อย่างเช่น
- ที่น่าประหลาดใจ
- การสังเคราะห์
- สังเคราะห์
- เอา
- คุย
- งาน
- ทีม
- เทคนิค
- เทคโนโลยี
- ทดสอบ
- ที่
- พื้นที่
- แล้วก็
- ที่นั่น
- ล้อยางขัดเหล่านี้ติดตั้งบนแกน XNUMX (มม.) ผลิตภัณฑ์นี้ถูกผลิตในหลายรูปทรง และหลากหลายเบอร์ความแน่นหนาของปริมาณอนุภาคขัดของมัน จะทำให้ท่านได้รับประสิทธิภาพสูงในการขัดและการใช้งานที่ยาวนาน
- พวกเขา
- นี้
- เวลา
- ชื่อหนังสือ
- ไปยัง
- วันนี้
- ร่วมกัน
- เครื่องมือ
- ด้านบน
- หัวข้อ
- หัวข้อ
- โยน
- โยน
- แบบดั้งเดิม
- พร้อมใจกัน
- ประเทศสหรัฐอเมริกา
- การใช้
- ข้อมูลที่เป็นประโยชน์
- การใช้
- การตรวจสอบ
- ต่างๆ
- ผู้ขาย
- การตรวจสอบ
- มาก
- ผ่านทาง
- ไดรฟ์
- ผนัง
- คือ
- ทาง..
- คือ
- อะไร
- ความหมายของ
- ที่
- ขาว
- กระดาษสีขาว
- จะ
- กับ
- ภายใน
- ไม่มี
- การทำงาน
- การเขียน
- ผล
- ยอมให้
- เธอ
- ลมทะเล