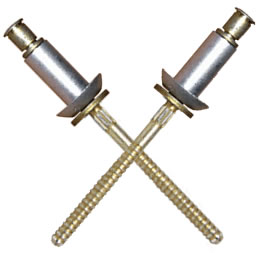
Ever wonder why airplanes don’t use copper rivets? Rivets are permanent fasteners that join two or more structural components. They offer a stronger and longer-lasting joint type than welding. While some airplanes use aluminum or steel rivets, though, you typically won’t find copper rivets in their construction.
Cost
One reason airplanes don’t use copper rivets is the cost. Copper costs more than other common rivet materials. Depending on the region and other market factors, raw copper may cost over twice as much as aluminum. And considering that airplanes often feature thousands or tens of thousands of rivets, opting for copper rivets can be expensive.
Galvanic Corrosion
There are still copper rivets available, but they typically aren’t used in airplanes. This is because copper rivets can trigger an electrochemical process known as galvanic corrosion.
Galvanic corrosion occurs when two dissimilar metals make electric contact with each other in the presence of moisture or humidity. Using copper rivets to create joints for aluminum components, for example, may result in galvanic corrosion. Over time, this electrochemical process can eat away at the component.
Weight
Another reason airplanes don’t use copper rivets is the weight. Copper rivets weigh more than aluminum rivets. Their heavy weight can result in poorer performance for airplanes. Airplanes with copper rivets will consume more fuel and require greater propulsion than those with lighter rivets, such as aluminum rivets.
Regulatory Compliance
Airplanes typically don’t use copper rivets because they lack the regulatory compliance of aluminum and mild steel rivets. Regulatory bodies like the U.S. Federal Aviation Administration (FAA) and the European Union Aviation Safety Agency (EASA) require aerospace components and fasteners to be made of certain materials. These materials have been thoroughly tested to ensure safety.
Lack of Deformation
Copper rivets don’t deform as easily as their aluminum or mild steel counterparts. Deformation, of course, is important for rivets. Rivets are designed to deform during installation. After inserting a rivet through two or more components, you can use a tool to deform it. Deforming it will cause part of the rivet to expand, collapse or otherwise deform so that the components form a permanent joint. If you use copper rivets, you may struggle to deform them — even if you use the right tool.
Poor Heat Resistance
Finally, copper rivets offer poor heat resistance. Copper is considered an excellent conductor of both electricity and heat. When exposed to heat, such as the heat of an airplane engine, it will absorb the heat. As the temperature of a copper rivet increases, it may no longer offer a secure joint.
- SEO Powered Content & PR Distribution. Get Amplified Today.
- PlatoData.Network Vertical Generative Ai. Empower Yourself. Access Here.
- PlatoAiStream. Web3 Intelligence. Knowledge Amplified. Access Here.
- PlatoESG. Carbon, CleanTech, Energy, Environment, Solar, Waste Management. Access Here.
- PlatoHealth. Biotech and Clinical Trials Intelligence. Access Here.
- Source: https://monroeaerospace.com/blog/why-copper-rivets-arent-used-in-airplanes/
- :is
- a
- administration
- Aerospace
- After
- agency
- Airplane
- Airplanes
- an
- and
- ARE
- AS
- At
- available
- aviation
- away
- BE
- because
- been
- bodies
- both
- but
- by
- CAN
- Cause
- certain
- Collapse
- Common
- compliance
- component
- components
- conductor
- considered
- considering
- construction
- consume
- contact
- Copper
- corrosion
- Cost
- Costs
- counterparts
- course
- create
- Depending
- designed
- Dont
- during
- each
- easily
- eat
- Electric
- electricity
- Engine
- ensure
- European
- european union
- Even
- example
- excellent
- Expand
- expensive
- exposed
- faa
- factors
- Feature
- Federal
- Federal Aviation Administration
- Find
- For
- form
- Fuel
- greater
- Have
- heavy
- High
- HTTPS
- if
- important
- in
- Increases
- installation
- IT
- join
- joint
- jpg
- known
- Lack
- lighter
- like
- longer
- made
- make
- Market
- materials
- May..
- Metals
- mild
- more
- much
- no
- of
- offer
- often
- on
- or
- Other
- otherwise
- over
- part
- performance
- permanent
- plato
- Plato Data Intelligence
- PlatoData
- poor
- presence
- process
- propulsion
- Raw
- reason
- region
- regulatory
- Regulatory Compliance
- require
- Resistance
- result
- right
- s
- Safety
- secure
- So
- some
- steel
- Still
- stronger
- structural
- Struggle
- such
- tens
- tested
- than
- that
- The
- their
- Them
- These
- they
- this
- thoroughly
- those
- though?
- thousands
- Through
- time
- to
- tool
- trigger
- Twice
- two
- type
- typically
- u.s.
- union
- use
- used
- using
- weigh
- weight
- when
- while
- why
- will
- with
- wonder
- you
- zephyrnet