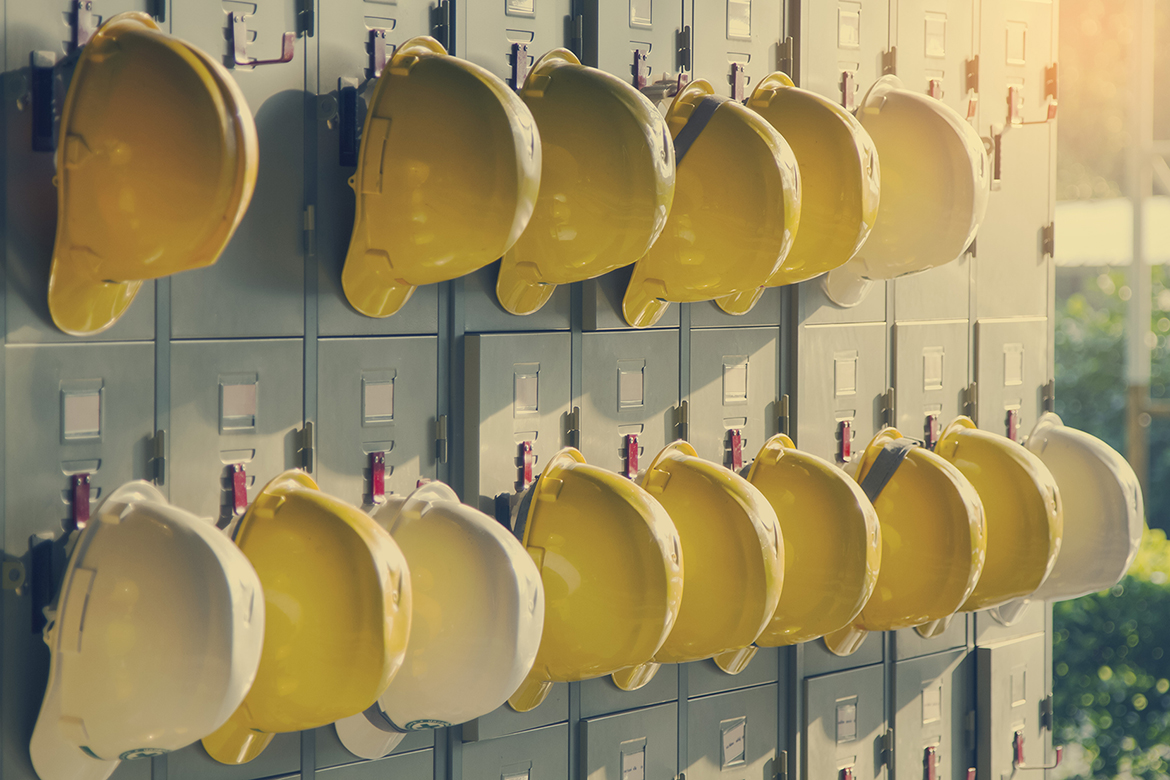
The US supply chain underwent huge changes as a result of Covid-19 pandemic and it has never fully recovered. With pressures on the efficiency of the chain and its workers at an all-time high, it is somewhat predictable that health and safety standards have fallen by the wayside. Nowhere is this more apparent than in warehousing, where, according to NBC, sickness rates are booming as relentless consumer demand is paired with high summer and autumn temperatures inside the steel boxes of most operations.
The supply chain also deals more in manual and secondary labor sectors than any other industry, including construction, lumber and maintenance. Together, all of these areas of work can play host to an insidious level of health and safety risk. As with many other areas of improvement, businesses and regulators are looking to technology – but can it fully bridge the gap?
Protecting businesses, protecting workers
The first important thing to note is that much of the cutting-edge technology being deployed by supply chain businesses seeks to eliminate human input altogether, and especially so in heavy machinery. According to some analysts, up to 73% of businesses are putting together plans to bring increased automation into their heavy industry, with the stated aims of reducing the amount of accidents as well as improving efficiency. As such, the best way to protect workers is through also protecting the business.
There are nuances to this debate which must be answered, however. As one study, published by Springer Nature and focused on the use of AI in construction settings found, many AI schemes are subject to exploitation by hackers, cybercrimes, and privacy intrusion, and can enhance the costs associated with construction. With many primary industries having a strong focus on efficiency, right down to the last brick, incurring large overheads that are then subject to attack can be a hard sell to investors. As such, many tech schemes need to come down to how they can directly improve worker safety.
The move to recognition
Supply & Demand Chain Executive, noting that 14 workers are injured every second in the American supply chain, made recommendations concerning technology that really do advance into the next level, tech-wise. They have cited the use of recognition technology. More typically associated with security issues, such as face recognition, this tech can also ensure that workers are using the right safety elements. For instance, in a warehouse, they can check for hi visibility vests, and, if appropriate, helmets or other PPE.
This technology is not perfect. There have been countless cases of inappropriate recognition, according to analysts, and there is every chance that there can be misidentification. For this reason, it’s essential that there is a human reviewer behind every recognition; someone to whom the information can be referred for a closer check. If this can be accomplished, recognition could be a powerful automated tool to ensure compliance with safety regulations.
Returning to engineering controls
Some of the most innovative uses of technology are the most simple, too. In a review of reducing health and safety risk in the supply chain, Bloomberg Law notes the preference of many businesses for engineering controls. These are where the engineers that maintain and build the devices key to business operation will look to see where safeguards and hazard breaks can be built in. These must comply with Occupational Safety and Health Administration (OSHA) standards but, crucially, can go beyond them, as long as the failsafe installed is high quality.
This also applies to social changes within the workplace. Amending work patterns, hours of operation, rules on operation or break lengths can help to reduce the amount of accidents at a rapid rate. What’s more, this provides an opportunity to bring in big data. By using meta-analysis of accidents in similar workspaces, and indeed by doing deep dives into accidents that occur within the business, employers can identify ways in which their control methods have failed and how to improve them. Using this data to smartly adjust conditions around working, rather than resorting to an arbitrary method or trial and error, will immediately bring in a greater level of safety while remaining fairly cheap to maintain.
Together, it is arguable that these changes can push back the tide of health and safety incidents within supply chain businesses. It’s important to note that there’s not a one-size-fits-all approach, however. AI can be helpful; engineering stops can be helpful; meta-analysis and the use of data can be helpful. A holistic and well-measured method, however, will use all three, and everything else on offer, to build up a multi-layered safety system for employees. Diving headfirst into the first technological system on hand, however, will not. A calm, measured, and data-led approach is crucial, and will arguably improve health and safety in an embattled sector.
About the author
Nina Dixon is a freelancer writer
- SEO Powered Content & PR Distribution. Get Amplified Today.
- PlatoData.Network Vertical Generative Ai. Empower Yourself. Access Here.
- PlatoAiStream. Web3 Intelligence. Knowledge Amplified. Access Here.
- PlatoESG. Carbon, CleanTech, Energy, Environment, Solar, Waste Management. Access Here.
- PlatoHealth. Biotech and Clinical Trials Intelligence. Access Here.
- Source: https://www.allthingssupplychain.com/is-technology-ready-to-stem-the-tide-of-supply-chain-health-and-safety-hazards/?utm_source=rss&utm_medium=rss&utm_campaign=is-technology-ready-to-stem-the-tide-of-supply-chain-health-and-safety-hazards
- :has
- :is
- :not
- :where
- $UP
- 14
- a
- accidents
- accomplished
- According
- adjust
- administration
- advance
- AI
- aims
- All
- also
- altogether
- American
- amount
- an
- Analysts
- and
- any
- apparent
- applies
- approach
- appropriate
- ARE
- areas
- arguably
- around
- AS
- associated
- At
- attack
- Automated
- Automation
- back
- BE
- been
- behind
- being
- BEST
- Beyond
- Big
- Big Data
- Bloomberg
- boxes
- Break
- breaks
- BRIDGE
- bring
- build
- built
- business
- businesses
- but
- by
- CAN
- cases
- chain
- Chance
- Changes
- cheap
- check
- cited
- closer
- come
- compliance
- comply
- concerning
- conditions
- construction
- consumer
- control
- Costs
- could
- COVID-19
- COVID-19 pandemic
- crucial
- crucially
- cutting-edge
- data
- Deals
- debate
- deep
- Demand
- deployed
- Devices
- directly
- diving
- do
- doing
- down
- efficiency
- elements
- eliminate
- else
- employees
- employers
- Engineering
- Engineers
- enhance
- ensure
- error
- especially
- essential
- Ether (ETH)
- Every
- everything
- executive
- exploitation
- Face
- face recognition
- Failed
- fairly
- Fallen
- First
- Focus
- focused
- For
- found
- fully
- gap
- Go
- greater
- hand
- Hard
- Have
- having
- Health
- heavy
- Helmets
- help
- helpful
- hi
- High
- holistic
- host
- HOURS
- How
- How To
- However
- HTTPS
- huge
- human
- identify
- if
- immediately
- important
- improve
- improving
- in
- incidents
- Including
- increased
- industries
- industry
- information
- innovative
- input
- inside
- instance
- into
- Investors
- issues
- IT
- ITS
- jpg
- Key
- labor
- large
- Last
- Law
- Level
- Long
- Look
- looking
- machinery
- made
- maintain
- maintenance
- manual
- many
- measured
- method
- methods
- more
- most
- move
- much
- multi-layered
- must
- Nature
- NBC
- Need
- never
- next
- NIH
- note
- Notes
- noting
- nuances
- occupational
- occur
- of
- offer
- on
- ONE
- operation
- Operations
- Opportunity
- or
- Other
- paired
- pandemic
- patterns
- perfect
- plans
- plato
- Plato Data Intelligence
- PlatoData
- Play
- powerful
- PPE
- Predictable
- primary
- privacy
- protect
- protecting
- provides
- published
- Push
- push back
- Putting
- quality
- rapid
- Rate
- Rates
- rather
- ready
- really
- reason
- recognition
- recommendations
- reduce
- reducing
- referred
- regulations
- Regulators
- relentless
- remaining
- result
- review
- right
- Risk
- rules
- safeguards
- Safety
- schemes
- Second
- secondary
- sector
- Sectors
- security
- see
- Seeks
- sell
- settings
- similar
- Simple
- So
- Social
- some
- Someone
- somewhat
- standards
- stated
- steel
- Stem
- Stops
- strong
- Study
- subject
- such
- summer
- supply
- supply chain
- system
- tech
- technological
- Technology
- than
- that
- The
- the information
- their
- Them
- then
- There.
- These
- they
- thing
- this
- three
- Through
- Tide
- to
- together
- too
- tool
- trial
- trial and error
- typically
- underwent
- us
- use
- uses
- using
- visibility
- Warehouse
- Warehousing
- Way..
- ways
- WELL
- which
- while
- whom
- will
- with
- within
- Work
- worker
- worker safety
- workers
- working
- Workplace
- zephyrnet