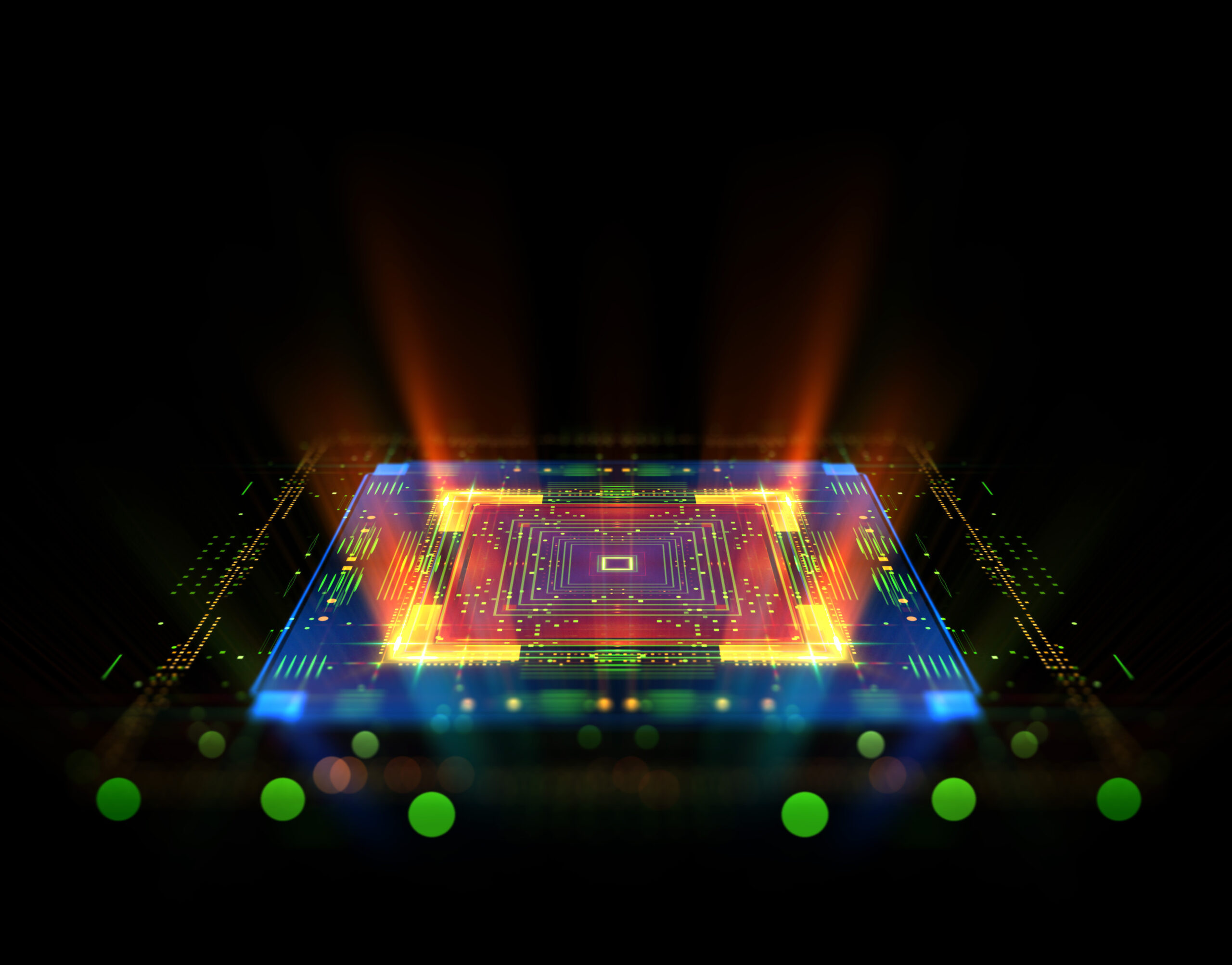
Semiconductor die thickness is getting thinner over time due to improvement of power efficiency in advance power electronic packages. Ultrathin die with convex warpage can easily deteriorate the solder void removal process during solder reflow, leading to various packaging reliability issues. In particular, a new type of packaging defect phenomenon—die-pop—is observed. Vacuum reflow process has been able to reduce the solder void size to minimum value consistently but there is an observable number of die-pop occurrence during the single-step pressure-profile reflow process for ultrathin dies that come with convex warpage. Nevertheless, optimization study has revealed that the application of the two-step pressure-profile and the medium reflow temperature profile within the vacuum reflow process has successfully eliminated the die-pop occurrence when packaging ultrathin dies. Together with the appropriate selection of the solder paste volume and the bond line thickness (BLT) of solder layer, majority of the samples attained the solder void size over die size of below 2% with zero die pop detected, without compromising the manufacturing productivity.
Authors:
Siang Miang Yeo
Amkor Technology, Inc., Telok Panglima Garang, Malaysia
Department of Electrical and Electronic Engineering, Lee Kong Chian Faculty of Engineering and Science, Universiti Tunku Abdul Rahman, Kajang, Malaysia
Ho Kwang Yow
Department of Electrical and Electronics Engineering, Lee Kong Chian Faculty of Engineering and Science and the Centre for Photonics and Advanced Material Research, Universiti Tunku Abdul Rahman, Kajang, Malaysia
Keat Hoe Yeoh
Department of Electrical and Electronics Engineering, Lee Kong Chian Faculty of Engineering and Science and the Centre for Photonics and Advanced Material Research, Universiti Tunku Abdul Rahman, Kajang, Malaysia
Siti Nur Farhana Mohamad Azenal
Amkor Technology, Inc., Telok Panglima Garang, Malaysia
Click here to read more. (Subscriber access needed for this IEEE eXplore article.)
- SEO Powered Content & PR Distribution. Get Amplified Today.
- PlatoData.Network Vertical Generative Ai. Empower Yourself. Access Here.
- PlatoAiStream. Web3 Intelligence. Knowledge Amplified. Access Here.
- PlatoESG. Carbon, CleanTech, Energy, Environment, Solar, Waste Management. Access Here.
- PlatoHealth. Biotech and Clinical Trials Intelligence. Access Here.
- Source: https://semiengineering.com/elimination-of-die-pop-defect-by-vacuum-reflow-for-ultrathin-die-with-warpage-in-semiconductor-packaging-assembly/
- :has
- :is
- 2%
- a
- Able
- access
- advance
- advanced
- an
- and
- Application
- appropriate
- article
- Assembly
- attained
- been
- below
- bond
- but
- by
- CAN
- centre
- come
- compromising
- consistently
- Convex
- detected
- Die
- due
- during
- easily
- efficiency
- Electronic
- Electronics
- eliminated
- Engineering
- explore
- For
- getting
- HTTPS
- IEEE
- improvement
- in
- Inc.
- issues
- Kong
- layer
- leading
- Lee
- Line
- Majority
- manufacturing
- material
- medium
- minimum
- more
- needed
- Nevertheless
- New
- number
- observed
- occurrence
- of
- optimization
- over
- packages
- packaging
- particular
- plato
- Plato Data Intelligence
- PlatoData
- pop
- power
- process
- productivity
- Profile
- Read
- reduce
- reliability
- removal
- research
- Revealed
- Science
- selection
- semiconductor
- Size
- Study
- subscriber
- Successfully
- Technology
- that
- The
- There.
- this
- time
- to
- together
- type
- Vacuum
- value
- various
- volume
- when
- with
- within
- without
- zephyrnet
- zero