Zapobieganie rozprzestrzenianiu się systematycznych defektów we współczesnym procesie od projektowania do produkcji półprzewodników wymaga wielu etapów walidacji, analizy i optymalizacji. Narzędzia zaangażowane w ten proces mogą obejmować sprawdzanie zasad projektowania (DRC), weryfikację korekcji bliskości optycznej (OPC), pisanie masek i metrologię/kontrolę drukowania płytek (w celu oceny procesu), metrologię/kontrolę drukowania płytek oraz analizę uszkodzeń fizycznych w celu potwierdzenia awarii diagnoza. Wymiana informacji i kooptymalizacja pomiędzy tymi etapami to złożony proces, obejmujący wiele pętli sprzężenia zwrotnego i sprzężenia zwrotnego. Komunikację często utrudniają „ściany” pomiędzy różnymi częściami technologii procesowej, spowalniając innowacje. Na niedawnej konferencji SPIE firma Siemens EDA przedstawiła przemówienie programowe, w którym zaproponowała szereg podejść pozwalających przełamać te bariery w celu ulepszenia projektu chipa w procesie produkcyjnym. Przeczytaj dalej, aby zobaczyć, jak firma Siemens zamierza przełamać bariery innowacji poprzez rozszerzenie kooptymalizacji technologii projektowania.
O Keynote
SPIE to międzynarodowe stowarzyszenie zajmujące się optyką i fotoniką. Początki organizacji sięgają 1955 roku, a jej konferencja stała się najważniejszym wydarzeniem poświęconym zaawansowanym kwestiom projektowania i produkcji. Na tegorocznym wydarzeniu firma Siemens przedstawiła myśl przewodnią, która jest tematem tego wpisu. W prezentacji wzięło udział wielu autorów, w tym Le Hong, Fan Jiang, Yuansheng Ma, Srividya Jayaram, Joe Kwan, Siemens EDA (Stany Zjednoczone); Doohwan Kwak, Siemens EDA (Korea Południowa); Sankaranarayanan Paninjath Ayyappan, Siemens EDA (Indie). Tytuł rozmowy brzmiał Rozszerzenie kooptymalizacji technologii projektowania od wprowadzenia technologii do HVM.
Wykład był częścią sesji poświęconej kooptymalizacji technologii projektowania (DTCO). Ta koncepcja nie jest nowa, ale firma Siemens przyjrzała się jej zastosowaniu w szerszym zakresie procesu, od projektu po produkcję wielkoseryjną (HVM). Zaprezentowane pomysły i wyniki mają istotne implikacje. Przyjrzyjmy się bliżej.
Co zostało zaprezentowane
Najpierw przedstawiono spojrzenie na obecny stan wykorzystania DTCO w kluczowych częściach ekosystemu. Z punktu widzenia projektowania wiele zaawansowanych firm bez fabless ma zespół DFM, który dostrzega ograniczenia podejścia opartego na wzorcach. Naprawdę potrzebna jest nowa technologia ułatwiająca naukę wydajności bez uzależnienia od odlewni.
Odlewnie stosują metody uczenia maszynowego oparte na wzorcach brute-force, które są kosztowne, ale nie w pełni skuteczne. Poszukują także wydajnej eksploracji informacji na temat tworzonych przez siebie ogromnych danych produkcyjnych. Dostawcy sprzętu i dostawcy EDA ściślej ze sobą współpracują i opracowują bardziej wydajne rozwiązania w zakresie uczenia maszynowego.
Cofając się nieco, wskazano, że pomiędzy fazą projektowania a fazą produkcji w procesie istnieją mury. Firmy Fabless tworzą projekt, wykonują DRC i projekt do produkcji (DFM), a następnie przesyłają go za ścianę zespołowi OPC/RET w odlewni lub IDM. Projekt wykonuje takie zadania, jak OPC i weryfikacja, a następnie dane są rzucane na inną ścianę w celu napisania maski i metrologii/kontroli. Ostatnia ściana przeznaczona jest do wykonania. Tutaj zostanie przeprowadzony test elektryczny i analiza awarii. Zanim zostanie znaleziona pierwotna przyczyna awarii, mija 6–18 miesięcy. To bardzo długa pętla informacji zwrotnej. Grafika na górze tego postu przedstawia ten proces.
DTCO próbuje przełamać mury, ale dostępne metodologie są niekompletne. Tradycyjne DTCO rozpoczyna się na bardzo wczesnym etapie rozwoju procesu. Zaczynając od potrzeby skalowania, definiuje się standardową komórkę, przeprowadza się syntezę, miejsce i trasę, aby uzyskać podstawowe wzorce oraz zmierzyć wydajność i moc. Dokonuje się również uzysku SRAM, a dane wracają do standardowej konstrukcji ogniwa.
Podczas przemówienia SPIE zaprezentowano sposób rozszerzenia koncepcji kooptymalizacji na cały proces, od projektu po produkcję. Podejście to polega na umożliwieniu łatwiejszego przepływu informacji od projektu aż do procesu końcowego i analizy fizycznej poprzez utworzenie kanału informacyjnego.
Choć brzmi to prosto, wcale takie nie jest. Omówiono wiele wyzwań, przedstawiając konkretne podejścia mające na celu ich złagodzenie. Na przykład wczesne projekty można utworzyć za pomocą generatorów syntetycznego układu, które pomogą w skalibrowaniu procesu pod kątem rzeczywistych problemów projektowych w miarę opracowywania procesu. Może to złagodzić wiele niespodzianek, z którymi borykają się obecnie w przypadku wczesnych przestojów procesu.
Kolejnym wyzwaniem jest radzenie sobie z ogromnymi wolumenami danych. Dzięki zastosowaniu nowych, wyrafinowanych technik kompresji możliwa jest 30-krotna poprawa. Usprawnia to znacznie zadania związane z obsługą i analizą danych. Koncepcja tzw wytłumaczalna sztuczna inteligencja może pomóc znacznie szybciej znaleźć pierwotne przyczyny problemów. Możliwość ponownego uczenia modeli sztucznej inteligencji na późniejszym etapie procesu produkcyjnego bez unieważniania wcześniejszych wyników to kolejny obszar wymagający ulepszeń. W obszarze analizy danych znajdują się również techniki radzenia sobie z „danymi niezrównoważonymi”. Na przykład jeden gorący punkt może zostać znaleziony na 100,000,000 XNUMX XNUMX wzorów.
Połączenie tego wszystkiego może stworzyć znacznie wydajniejszy, kompleksowy proces projektowania, jak pokazano na poniższym rysunku.
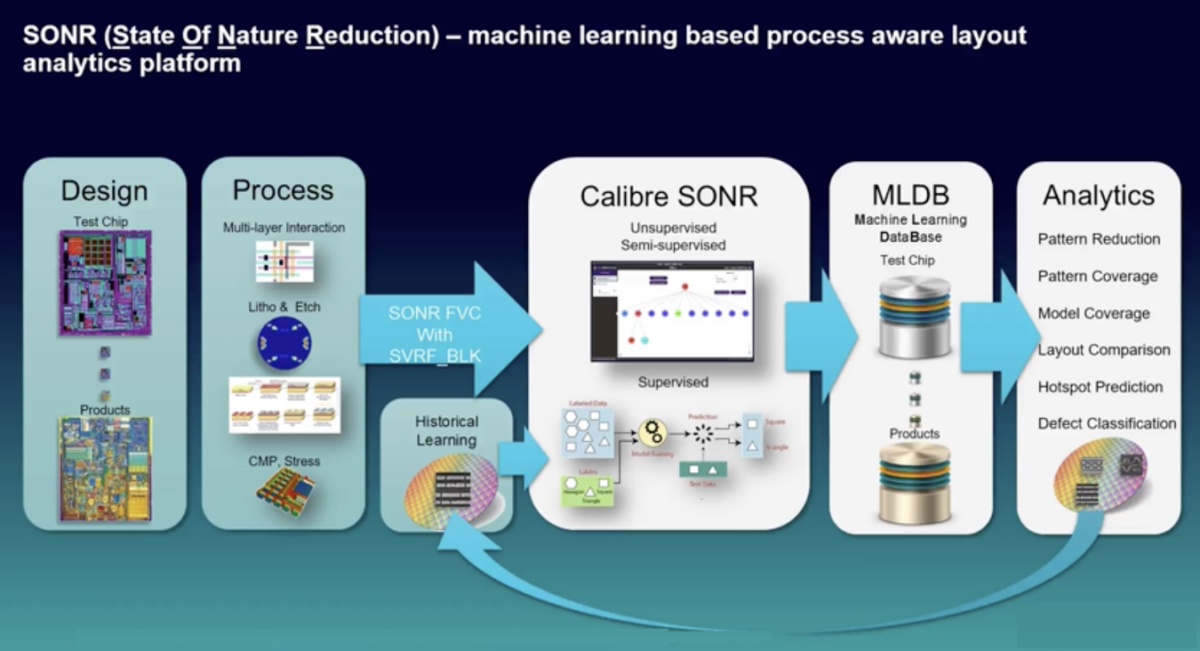
Uczyć się więcej
Wpływ podejść zarysowanych w tej prezentacji przewodniej jest znaczący. Możesz obejrzyj prezentację i uzyskaj dostęp do białej księgi na temat procesu tutaj. Można zdobyć wiele przydatnych informacji. I w ten sposób Siemens zamierza przełamać bariery innowacji poprzez rozszerzenie zakresu kooptymalizacji technologii projektowania.
Udostępnij ten post przez:
- Dystrybucja treści i PR oparta na SEO. Uzyskaj wzmocnienie już dziś.
- PlatoData.Network Pionowe generatywne AI. Wzmocnij się. Dostęp tutaj.
- PlatoAiStream. Inteligencja Web3. Wiedza wzmocniona. Dostęp tutaj.
- PlatonESG. Węgiel Czysta technologia, Energia, Środowisko, Słoneczny, Gospodarowanie odpadami. Dostęp tutaj.
- Platon Zdrowie. Inteligencja w zakresie biotechnologii i badań klinicznych. Dostęp tutaj.
- Źródło: https://semiwiki.com/events/339386-spie-2023-buzz-siemens-aims-to-break-down-innovation-barriers-by-extending-design-technology-co-optimization/
- :ma
- :Jest
- :nie
- $W GÓRĘ
- 000
- 100
- 2023
- a
- zdolność
- dostęp
- w poprzek
- adres
- zaawansowany
- AI
- Modele AI
- Cele
- Wszystkie kategorie
- łagodzić
- również
- an
- analiza
- i
- Inne
- Zastosowanie
- podejście
- awanse
- SĄ
- POWIERZCHNIA
- AS
- At
- Próby
- dostępny
- z powrotem
- bariery
- podstawowy
- BE
- stają się
- być
- poniżej
- pomiędzy
- Bit
- przerwa
- szerszy
- ale
- by
- nazywa
- CAN
- Spowodować
- Przyczyny
- komórka
- wyzwanie
- wyzwania
- Kanał
- kontrola
- żeton
- bliższy
- CO
- jak
- przyjście
- Komunikacja
- Firmy
- całkowicie
- kompleks
- pojęcie
- beton
- Konferencja
- Potwierdzać
- Dostawcy
- kosztowny
- Stwórz
- stworzony
- Tworzenie
- Aktualny
- Stan aktulany
- Obecnie
- dane
- analiza danych
- Daty
- sprawa
- zdefiniowane
- zależność
- Wnętrze
- projekty
- detale
- rozwinięty
- oprogramowania
- diagnoza
- omówione
- zrobić
- na dół
- drc
- Wcześniej
- Wcześnie
- łatwiej
- Ekosystem
- Efektywne
- wydajny
- umożliwiając
- koniec końców
- Cały
- sprzęt
- wydarzenie
- przykład
- wymiana
- rozciągać się
- rozsuwalny
- w obliczu
- ułatwiać
- Brak
- wentylator
- szybciej
- informacja zwrotna
- Postać
- finał
- Znajdź
- pływ
- W razie zamówieenia projektu
- znaleziono
- Odlewnia
- od
- zdobyte
- wskaźnik
- generatory
- graficzny
- Prowadzenie
- Have
- pomoc
- tutaj
- Hong
- HOT
- W jaki sposób
- HTTPS
- pomysły
- Rezultat
- implikacje
- podnieść
- poprawa
- poprawia
- in
- zawierać
- Włącznie z
- Indie
- Informacja
- Innowacja
- na świecie
- zaangażowany
- dotyczy
- problemy
- IT
- JEGO
- joe
- Klawisz
- Myśl przewodnia
- Korea
- później
- uruchomić
- układ
- UCZYĆ SIĘ
- nauka
- Limity
- długo
- Popatrz
- wyglądał
- Partia
- maszyna
- uczenie maszynowe
- produkcja
- wiele
- maska
- masywny
- Maksymalna szerokość
- Może..
- zmierzyć
- metodologie
- Górnictwo
- Złagodzić
- modele
- miesięcy
- jeszcze
- bardziej wydajny
- dużo
- Potrzebować
- potrzebne
- Nowości
- of
- często
- on
- ONE
- optyka
- Optyka i fotonika
- optymalizacja
- or
- organizacja
- na zewnątrz
- opisane
- koniec
- Papier
- część
- strony
- minęło
- wzory
- wykonać
- jest gwarancją najlepszej jakości, które mogą dostarczyć Ci Twoje monitory,
- wykonywane
- perspektywa
- fizyczny
- Miejsce
- Platforma
- plato
- Analiza danych Platona
- PlatoDane
- możliwy
- Post
- power
- premier
- presentation
- przedstawione
- druk
- problemy
- wygląda tak
- propagacja
- zaproponowane
- całkiem
- Czytaj
- real
- naprawdę
- niedawny
- Republika
- Wymaga
- Efekt
- korzeń
- Trasa
- Zasada
- skalowaniem
- zakres
- widzieć
- widzenie
- poszukuje
- Semiconductor
- Serie
- Sesja
- pokazane
- Siemens
- znaczący
- Spowolnienie
- Społeczeństwo
- Rozwiązania
- wyrafinowany
- Spot
- standard
- Startowy
- rozpocznie
- Stan
- Zjednoczone
- Cel
- znaczny
- taki
- niespodzianek
- synteza
- syntetyczny
- Brać
- Mówić
- zadania
- zespół
- Techniki
- Technologia
- test
- że
- Połączenia
- następnie
- Tam.
- Te
- one
- to
- czas
- Tytuł
- do
- dzisiaj
- razem
- narzędzia
- Top
- aktualny
- tematy
- podrzucać
- rzucił
- tradycyjny
- Zjednoczony
- United States
- Stosowanie
- przydatna informacja
- za pomocą
- uprawomocnienie
- różnorodny
- sprzedawców
- Weryfikacja
- początku.
- przez
- kłęby
- Ściana
- była
- Droga..
- były
- Co
- Co to jest
- który
- biały
- biały papier
- będzie
- w
- w ciągu
- bez
- pracujący
- pisanie
- Wydajność
- wydajność
- ty
- zefirnet