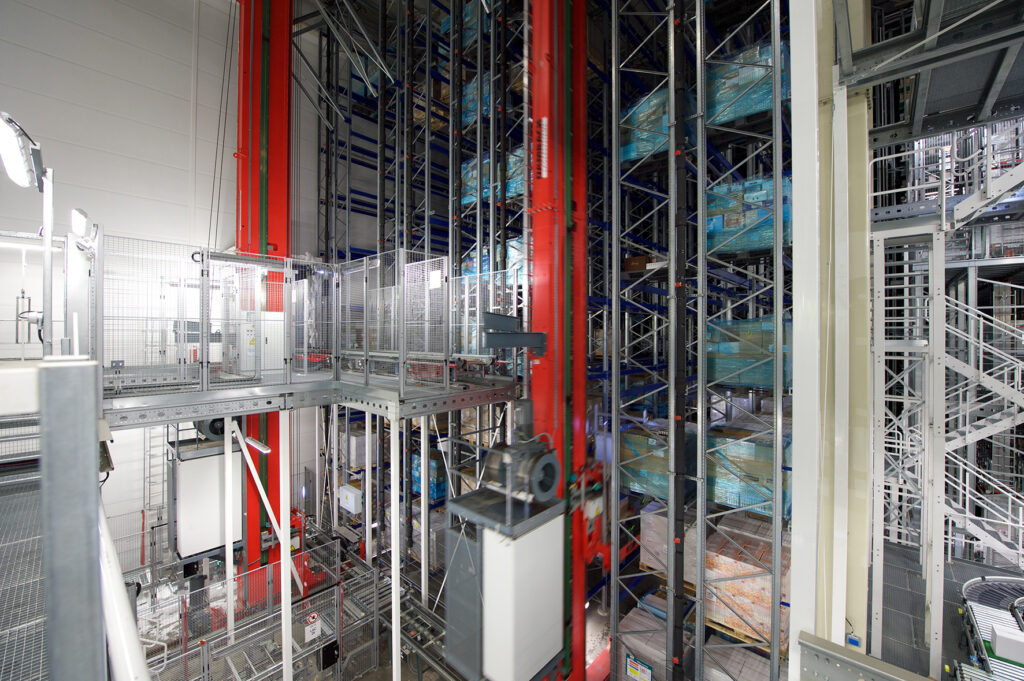
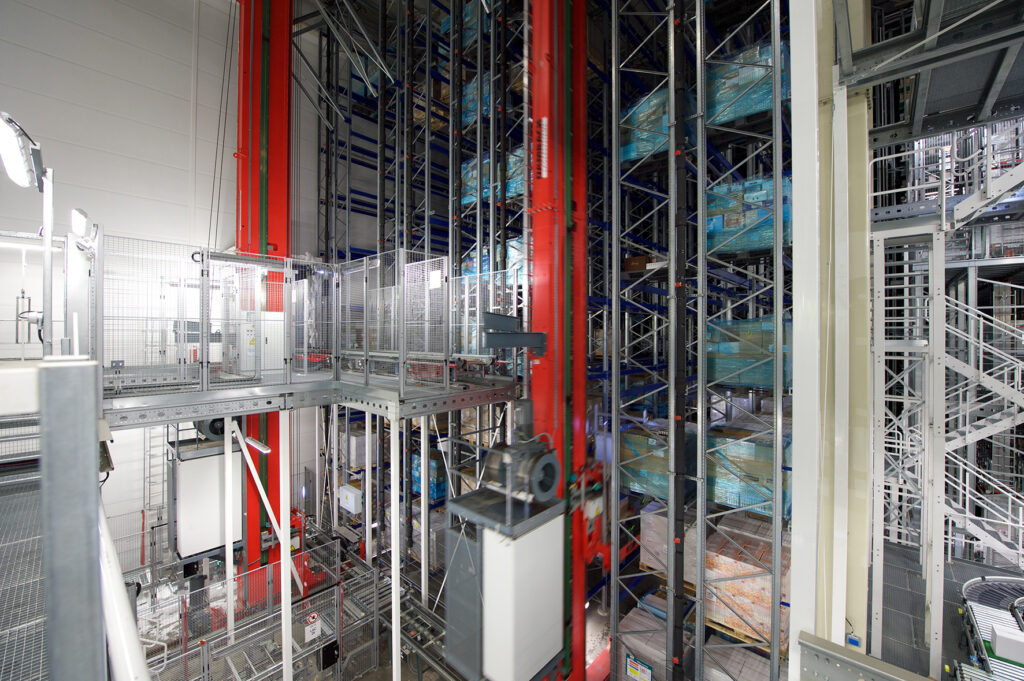
Het uitbreiden van een zeer dynamisch multi-temperatuur logistiek centrum voor ongeveer 1,200 winkels tijdens lopende activiteiten met een toename van de pickprestaties van 480,000 naar bijna 625,000 dozen per dag, is op zich al een enorme uitdaging. Maar wanneer bovendien de winkel- en onlinebestellingen door diverse lockdowns blijven stijgen en de teams vanwege de Covid-19-beperkingen slechts met strenge beperkingen mogen werken, dan is er aan beide kanten veel meer nodig dan alleen technische en organisatorische kennis. het project te laten slagen. WITRON en de levensmiddelenretailer COOP uit Noorwegen hebben dit op indrukwekkende wijze aangetoond.
Toen de twee directeuren Geir Inge Stokke (COOP) en Helmut Prieschenk (WITRON) eind mei 2019 het contract tekenden voor de uitbreiding van het COOP multi-temperatuur distributiecentrum nabij Oslo, hadden ze geen van beiden enig idee van de enorme uitdagingen zij zouden onder ogen moeten zien. Vanaf maart 2020 stond de wereld stil als gevolg van Covid, en de eisen van de consument stegen aanzienlijk als gevolg van verschillende lockdowns. Dit was een ongunstige start voor wat waarschijnlijk het meest uitdagende brownfieldproject in de bedrijfsgeschiedenis van Witron tot nu toe was, waarbij bestaande technologie werd gemoderniseerd en nieuwe modules werden geïntegreerd – zowel in het bestaande gebouw als in een nieuwe uitbreidingsfaciliteit.
De taak die aan Gaute Glomlien van COOP en Holger Weiß van WITRON was gericht, werd als volgt beschreven: de logistieke faciliteit voor droge, verse en diepgevroren goederen uitbreiden van 52,000 vierkante meter naar 84,000 vierkante meter onder Covid 19-veiligheidsmaatregelen, om de doorvoer met 30 procent te verhogen , om nieuwe COM-machines te integreren, om extra pallet- en tray-AS/RS-gangen en diverse transportcomponenten te installeren, om de omvang van de volledig geautomatiseerde verzendbuffer te vergroten, om het bijbehorende WMS-systeem te updaten naar de nieuwste technologie, en om dit alles te implementeren in de bestaande materiaalstroom tijdens lopende werkzaamheden zonder enig prestatieverlies.
“Met de WITRON-systemen hebben we in het verleden jaarlijks miljoenen euro’s kunnen besparen. Daarom was het duidelijk dat we de uitbreiding ook zouden realiseren met WITRON en hun toonaangevende logistieke technologie”, legt COOP-projectmanager Glomlien uit. De uitbreiding was ook nodig omdat de retailer een concurrent kreeg en daardoor sterker en sneller groeide dan bij de oprichting van het logistieke centrum werd aangenomen.
“COOP is voor ons een showcaseproject. Veel internationale klanten bezoeken de faciliteit en met de uitbreiding hebben we op indrukwekkende wijze kunnen bewijzen dat we een dergelijke taak tijdens lopende activiteiten binnen budget en op tijd kunnen uitvoeren, ondanks de toenemende volumes – zowel qua doorvoer als artikelen – in het magazijn en ondanks de pandemie. ”, meldt Holger Weiß trots. In het voorjaar van 2023 zullen 42 COM-machines (er zijn elf nieuwe COM's geïnstalleerd) in alle temperatuurzones actief zijn en kunnen de logistieke systemen van COOP dagelijks meer dan 625,000 dozen verzamelen. In totaal omvat de faciliteit meer dan 600,000 opslaglocaties voor pallets, bakken en trays, evenals 130 stapelkranen en vele kilometers aan transporttechnologie.
Uitdagingen met succes onder de knie
Vanuit de faciliteit (met vijf verschillende temperatuurzones), COOP levert 1,200 winkels verspreid over Noorwegen, vanuit de metropoolregio rond Oslo en het uiterste noorden van Noorwegen vanuit een assortiment van 13,000 verschillende artikelen. “Aan het begin van het project was het duidelijk dat we onze pickcapaciteit substantieel moesten vergroten”, grapt Glomlien vandaag. “Het volume van het logistieke centrum is bijna verdubbeld”, reageert Weiß lachend. Glomlien en hij hebben in sommige situaties lastige discussies gehad. Vandaag zitten ze voor de Teams-microfoons en zijn ze blij elkaar weer virtueel te zien. “Het was een leuke tijd”, vat Weiß na het gesprek samen, en zijn Noorse tegenhanger is het daarmee eens.
Wanneer hij zich verschillende dagen, weken en maanden van het project voor de geest haalt, pauzeert hij even, herinnert zich en gaat dan des te trotser verder. “De grenzen waren gesloten. Er waren complexe toegangsbeperkingen geweest. De autoriteiten hebben strenge quarantainemaatregelen bevolen. Lange tijd mocht het projectteam alleen maar rijden vanaf het hotel (dat om andere redenen niet mocht verlaten) naar het logistieke centrum en terug. Ook de cafetaria's ter plaatse waren gesloten. Zelfs in het hotel werd de service tot een minimum beperkt. Dit is iets wat je als team moet overwinnen. Dit zijn echte ontberingen – voor het klantenteam, maar ook voor onze collega’s. Als projectmanager vraag je jezelf elke avond af hoe je je team gemotiveerd kunt houden”, benadrukt Weiß. Het WITRON-team verplaatste zich met speciale vergunningen van de overheid. De logistiek van COOP was systematisch belangrijk. “Tijdens de pandemie nam het aantal bestellingen nog verder toe”, herinnert Glomlien zich.
De diepvrieslogistiek was een bijzondere technische uitdaging voor de Opper-Palts Holger Weiß. “We hebben de bestaande geautomatiseerde ruimte ‘verwarmd’ van min 25 °C naar min 5 °C, en COOP heeft de goederen tijdelijk naar een conventionele opslagruimte verplaatst om te picken. Vervolgens hebben we binnen acht weken alle aanpassingen gedaan op het gebied van elektrische montage, bordessen, pallet- en traybandtechniek totdat de bestaande vriezer weer werd opgewaardeerd. Vervolgens werden in het nieuwe vriesgebouw de twee nieuwe COM-machines, nog twee palletopslaggangen, vier trayopslaggangen, extra stapelkranen, een depalletiseerder en het bijbehorende transportsysteem geïnstalleerd.
“De installatievolgorde werd zorgvuldig gepland in een gezamenlijk proces, en we gaven prioriteit aan de installatie van de nieuwe palletkranen, wat een efficiënte CPS-picking in het uitgebreide bevroren gebied zou vergemakkelijken. Vervolgens hebben we de nieuwe productiezone gekoeld tot de vereiste temperatuur, onze geautomatiseerde productie verplaatst naar CPS-picking vanaf de nieuwe palletkranen en handmatige palletstellingen, en onze bestaande productieruimte verwarmd om de installatie van WITRON te huisvesten”, voegt Glomlien toe. “De fase vereiste zorgvuldige coördinatie en cross-functionele samenwerking tussen de IT- en mechanische middelen van WITRON, en de teams van COOP die de productie, het transport en het orderbeheer controleerden, vanaf de inbedrijfstelling tot en met de opstart en tijdens de productieve fase.
Nadat WITRON de nieuwe installaties in onze reeds bestaande productiezone had voltooid, werd het proces omgekeerd voor de voltooiing van het nieuwe productiegebied. Vervolgens werd het orderverzamelen terugverplaatst naar de volledig geautomatiseerde OPM-machines.”
Bij COOP noemen de verantwoordelijken de plukruimte ook wel de productieruimte, legt Holger Weiß uit.
Tegenwoordig zijn er in totaal vier COM-machines actief in het diepvriesgedeelte van de vestiging. Toen het systeem weer was afgekoeld tot min 25 °C, kruiste Weiß zijn vingers. “Als de kabels breken, de riemen scheuren, motoren uitvallen of sensoren uitvallen, wordt het spannend omdat het beschikbare tijdvenster krap was” en tegelijkertijd was het belangrijk om rekening te houden met de kwaliteit van de opgeslagen goederen om te voorkomen grote productschade. “Voor een project als dit moet je de beste componenten gebruiken die op de markt verkrijgbaar zijn. We hebben geen bestaande schijven gewijzigd, maar nieuwe geïnstalleerd. Het moet vanaf het begin lopen, omdat het project anders niet op tijd klaar is, of de klant zelfs directe kosten krijgt als de goederen niet verzonden kunnen worden.” Het WITRON OnSite-team gebruikte de tijd van de herbouw om onderhoud aan het systeem uit te voeren. “Als de goederen weer worden opgeslagen, moet je altijd voortdurend met de controlekamer communiceren en ter plaatse snel reageren”, legt Weiß uit. De communicatie tussen het klantenteam, het projectteam en het OnSite-team moet soepel verlopen. “Het resultaat bewijst ongetwijfeld dat het soepel heeft gewerkt”, benadrukt de WITRON-projectmanager. “Het minutieuze detailwerk heeft zijn vruchten afgeworpen. Nadat we het diepvriesgebied hadden uitgebreid, konden we snel weer aan de slag. Er waren geen negatieve verrassingen.”
Efficiënt modificatieconcept, ook voor het drogegoedassortiment
Na uitvoerige gesprekken met WITRONbesloot COOP vijf extra COM-machines te installeren (in totaal 17 met ruimte voor nog eens 4 COM's), nog eens vier palletopslaggangen, nog eens tien trayopslaggangen, de bijbehorende stapelkranen en transportsysteemmonteurs, drie depalletiseerders, evenals één rekwikkelaar in het OPM-gebied van het drogegoedassortiment. “Voor het drogegoedassortiment was er in de herfst van 2021 en de winter van 2022 een cruciale fase aangebroken”, zegt Glomlien. “Dit is het gebied met de hoogste doorvoer in het distributiecentrum, met extra complexiteit doordat twee fysiek gescheiden OPM-subsystemen als één geïntegreerde eenheid werken. Om alle bestellingen op tijd en met dezelfde kwaliteit te kunnen blijven leveren nadat het nieuwe gebied in gebruik werd genomen, werd het opstartproces zorgvuldig gepland en werd onze voorraaddistributie nauwlettend in de gaten gehouden om ervoor te zorgen dat de juiste producten op de juiste plek lagen om te worden gepickt. juiste moment”, zegt Gaute Glomlien, die de goed geplande uitbreiding beschrijft. ”Gedetailleerde emulaties die vooraf werden uitgevoerd door het IT-team van WITRON, in samenwerking met de productieleiders van COOP, waren ook cruciaal om de juiste productiestrategie te identificeren voordat de twee volledig geïntegreerde subsystemen in gebruik werden genomen. “De beslissende factor hier is de exacte balans van de bestellingen en inventarisaties tussen de afzonderlijke subsystemen”, voegt Holger Weiß toe. “Ook deze implementatiestrategie heeft uitstekend gewerkt.”
Optimaliseren van pickstrategieën
De versafdeling kreeg vier extra COM-machines (in totaal 21 met ruimte voor nog eens vijf COM's), nog eens acht trayopslaggangen, nog twee palletopslaggangen, de bijbehorende stapelkranen en transportsysteemmonteurs, twee depalletiseerders en één rek -wikkel. “Vervolgens hebben we in de AGF-afdeling nog een materiaalstroomsectie voor groenten en fruit toegevoegd om de afhandeling van andere goederen in deze sector te vereenvoudigen. Vroeger werden de productgroepen samen geplukt”, legt Glomlien uit.
De volledig geautomatiseerde verzendbuffer, die verschillende temperatuurzones bestrijkt, is opnieuw uitgebreid.
Holger Weiß werkt al aan zijn volgende project in Zweden. De dagelijkse gang van zaken voor COOP bij CLog gaat door. “De upgrade heeft ons een state-of-the-art oplossing opgeleverd die tijdens lopende activiteiten is verbeterd tot een doorvoervolume dat in de oorspronkelijke ontwerpfase niet eens te verwachten was. Nu optimaliseren we de processen verder”, legt Glomlien uit. Met de uitbreiding ook COOP's software systemen werden bijgewerkt naar de nieuwste stand van de techniek van Witron.
Maar ook nadat het project is afgerond blijven de processen in het logistieke centrum veranderen, al was het maar omdat de hele supply chain onderhevig is aan schommelingen en de eisen van de klant veranderen. Daarom is in alle processen een hoge mate van flexibiliteit vereist. “COOP streeft een continu verbeterproces na en heeft de afgelopen jaren veel ervaring opgedaan met de faciliteit. Ook voor ons is dit zeer indrukwekkend. Ze analyseren hun gegevens, hun berekeningen, selecteren de juiste pickstrategieën voor de regio's en winkels en bepalen hoe ze hun bestellingen moeten structureren”, zegt Weiß enthousiast. Ook ondersteunen zij de WITRON-collega’s ter plaatse en in Parkstein wanneer de logica verandert.
Het respect strekt zich uit tot alle partijen die bij het project betrokken zijn
Ook voor Helmut Prieschenk, CEO van WITRON, is de vestiging in Noorwegen in veel opzichten een showcaseproject. “Het toont de transformeerbaarheid van geautomatiseerde processen. Het laat zien hoe efficiënt aanvullende technologie kan worden geïntegreerd in een bestaand systeem of in een bestaand gebouw tijdens lopende activiteiten. Het zijn echter niet alleen technologie en gebouwen die bij dergelijke projecten doorslaggevend zijn, maar ook de mensen die zo’n project succesvol over de eindstreep brengen. Mensen die hebben laten zien hoe zelfs uitdagende situaties efficiënt het hoofd kunnen worden geboden als projectteams gedurende alle projectfasen constructief en vol vertrouwen samenwerken.
Met deze uitbreiding hebben alle betrokkenen bij het project een meesterwerk afgeleverd. Zowel technologisch, maar vooral wat betreft de getoonde inzet. Hoewel de technische vereisten al een uitdagende taak vormden voor de COOP- en WITRON-teams, werd de implementatie ervan gedurende vele maanden verder bemoeilijkt door de Corona-pandemie. Om ondanks de tekortkomingen in het gezondheidsbeleid aan het noodzakelijke strakke tijdschema te kunnen voldoen, hebben de collega’s een maximum aan “hart en ziel” getoond, zijn ze meegegroeid met de uitdagingen en hebben ze uitstekend werk geleverd. Projecten worden gemaakt door mensen voor mensen. En de betrokken mensen hebben een prestatie geleverd die het grootste respect verdient en de geest van beide bedrijven vertegenwoordigt.”
- Door SEO aangedreven content en PR-distributie. Word vandaag nog versterkt.
- PlatoData.Network Verticale generatieve AI. Versterk jezelf. Toegang hier.
- PlatoAiStream. Web3-intelligentie. Kennis versterkt. Toegang hier.
- PlatoESG. Automotive / EV's, carbon, CleanTech, Energie, Milieu, Zonne, Afvalbeheer. Toegang hier.
- Plato Gezondheid. Intelligentie op het gebied van biotech en klinische proeven. Toegang hier.
- ChartPrime. Verhoog uw handelsspel met ChartPrime. Toegang hier.
- BlockOffsets. Eigendom voor milieucompensatie moderniseren. Toegang hier.
- Bron: https://www.logisticsbusiness.com/transport-distribution/cold-chain-logistics/more-throughput-for-coop-dc-during-upgrade/
- : heeft
- :is
- :niet
- $UP
- 000
- 1
- 13
- 17
- 19
- 200
- 2019
- 2020
- 2021
- 2023
- 25
- 30
- 52
- 84
- a
- in staat
- accommoderen
- verworven
- over
- toegevoegd
- toevoeging
- Extra
- aangesproken
- Voegt
- aanpassingen
- Na
- weer
- Alles
- toegestaan
- bijna
- al
- ook
- altijd
- an
- analyseren
- en
- Nog een
- verwachte
- elke
- ZIJN
- GEBIED
- rond
- Kunst
- AS
- vragen
- aspecten
- bijeenkomst
- assortiment
- uitgegaan van
- At
- Overheid
- geautomatiseerde
- Beschikbaar
- vermijd
- terug
- balancing
- BE
- omdat
- geweest
- Begin
- BEST
- tussen
- grenzen
- zowel
- Beide kanten
- Breken
- begroting
- buffer
- Gebouw
- bedrijfsdeskundigen
- maar
- by
- kabels
- CAN
- kan niet
- Inhoud
- voorzichtig
- voorzichtig
- dragen
- gevallen
- Centreren
- centrum
- ceo
- keten
- uitdagen
- uitdagingen
- uitdagend
- verandering
- veranderende
- duidelijk
- CLOSED
- van nabij
- samenwerking
- collega's
- COM
- hoe
- verplichting
- communiceren
- Communicatie
- Bedrijven
- afstand
- concurrent
- Voltooid
- voltooiing
- complex
- ingewikkeldheid
- ingewikkeld
- componenten
- omvat
- concept
- permanent
- constructief
- voortzetten
- blijft
- doorlopend
- contract
- onder controle te houden
- het regelen van
- conventioneel
- Gesprek
- SAMENWERKEN
- coördinatie
- Corona
- te corrigeren
- Overeenkomend
- Kosten
- kon
- Tegenhanger
- heeft betrekking op
- Covidien
- Gekruist
- cruciaal
- klant
- Klanten
- dagelijks
- gegevens
- Datum
- dagelijks
- dagen
- dc
- beslist
- beslissend
- bepalen
- geleverd
- eisen
- gedemonstreerd
- beschreven
- verdient
- Design
- Niettegenstaande
- detail
- gedetailleerd
- DEED
- anders
- directe
- Raad van bestuur
- discussies
- distributie
- documenten
- beneden
- rit
- gedreven
- drives
- drogen
- twee
- gedurende
- dynamisch
- elk
- doeltreffend
- efficiënt
- elf
- benadrukt
- einde
- verbeterde
- verzekeren
- Geheel
- toegang
- gevestigd
- Euro
- Zelfs
- avond
- Alle
- duidelijk
- opwindend
- bestaand
- bestaand systeem
- Uitvouwen
- uitgebreid
- uitbreiding
- ervaring
- uitgelegd
- Verklaart
- strekt
- uitbreiding
- Gezicht
- vergemakkelijken
- Faciliteit
- factor
- FAIL
- Vallen
- ver
- sneller
- weinig
- afmaken
- Voornaam*
- vijf
- Flexibiliteit
- stroom
- schommelingen
- volgt
- eten
- Voor
- vier
- vers
- oppompen van
- voor
- bevroren
- Fruit
- geheel
- verder
- opgedaan
- gegeven
- gaan
- goed
- goederen
- Overheid
- groot
- groeide
- Groep
- HAD
- handvat
- Behandeling
- gelukkig
- Hebben
- he
- Gezondheid
- hier
- Hoge
- hoogst
- zeer
- zijn
- geschiedenis
- hotel
- Hoe
- How To
- Echter
- HTTPS
- reusachtig
- idee
- identificeren
- if
- uitvoeren
- uitvoering
- belangrijk
- indrukwekkend
- verbetering
- in
- Laat uw omzet
- meer
- meer
- individueel
- installeren
- installatie
- integreren
- geïntegreerde
- Internationale
- in
- betrokken zijn
- IT
- artikelen
- Jobomschrijving:
- gewricht
- jpg
- voor slechts
- Houden
- kennis
- laatste
- leiders
- leidend
- links
- Niveau
- als
- beperkingen
- Lijn
- gelegen
- locaties
- lockdowns
- logistiek
- lang
- lange tijd
- uit
- lot
- machinerie
- Machines
- gemaakt
- onderhoud
- groot
- management
- manager
- beheren
- manier
- handboek
- veel
- Maart
- maart 2020
- Markt
- meesterwerk
- materiaal
- maximaal
- Mei..
- maatregelen
- mechanisch
- mechanica
- Maak kennis met
- minutieus
- microfoons
- miljoenen
- denken
- minimum
- Modules
- moment
- bewaakt
- maanden
- meer
- meest
- Motoren
- verplaatst
- Dan moet je
- Nabij
- noodzakelijk
- nodig
- negatief
- Noch
- New
- volgende
- geen
- noorden
- Noorwegen
- Norwegian
- nu
- aantal
- of
- korting
- on
- eens
- EEN
- degenen
- lopend
- online.
- Slechts
- werkzaam
- Operations
- optimaliseren
- or
- bestellen
- orders
- organisatorische
- origineel
- Oslo
- Overige
- anders-
- onze
- over
- Overwinnen
- betaald
- pandemisch
- bijzonder
- partijen
- verleden
- Mensen
- procent
- uitvoeren
- prestatie
- uitgevoerd
- vergunningen
- fase
- fysiek
- kiezen
- uitgekozen
- gepland
- platforms
- Plato
- Plato gegevensintelligentie
- PlatoData
- beleidsmaatregelen
- positie
- Voorafgaand
- geprioriteerd
- waarschijnlijk
- processen
- produceren
- Product
- productie
- productief
- Producten
- project
- projecten
- trots
- Bewijzen
- kwaliteit
- quarantaine
- snel
- reeks
- Reageren
- vast
- realiseren
- redenen
- ontvangen
- Gereduceerd
- verwijzen
- regio
- regio
- Rapporten
- vertegenwoordigt
- nodig
- Voorwaarden
- Resources
- culturele wortels
- verantwoordelijk
- beperkingen
- resultaat
- kleinhandelaar
- terugkeer
- rechts
- Kamer
- ruw
- lopen
- Veiligheid
- dezelfde
- Bespaar
- zegt
- rooster
- sectie
- sector
- zien
- sensor
- apart
- Volgorde
- service
- streng
- verscheept
- Verzending
- showcase
- vertoonde
- getoond
- Shows
- Sides
- Gesigneerd
- aanzienlijk
- vereenvoudigen
- zitten
- website
- situaties
- Maat
- glad
- So
- gestegen
- oplossing
- sommige
- iets
- Tussenruimte
- special
- geest
- voorjaar
- vierkant
- begin
- Land
- state-of-the-art
- Still
- voorraad
- mediaopslag
- shop
- opgeslagen
- winkels
- strategieën
- Strategie
- streng
- sterker
- structuur
- onderwerpen
- slagen
- Met goed gevolg
- dergelijk
- leveren
- toeleveringsketen
- het leveren van
- ondersteuning
- verrassingen
- Zweden
- system
- Systems
- Taak
- team
- teams
- Technisch
- Technologie
- tien
- termen
- neem contact
- dat
- De
- De omgeving
- de wereld
- hun
- Ze
- harte
- Er.
- daarom
- Deze
- ze
- dit
- die
- drie
- Door
- overal
- doorvoer
- niet de tijd of
- naar
- vandaag
- Totaal
- taai
- vervoeren
- ontzettend
- twee
- voor
- ongetwijfeld
- eenheid
- tot
- bijwerken
- bijgewerkt
- upgrade
- us
- .
- gebruikt
- divers
- Groenten
- zeer
- virtueel
- Bezoek
- volume
- volumes
- Magazijn
- was
- we
- weken
- GOED
- waren
- Wat
- wanneer
- welke
- en
- WIE
- Waarom
- wil
- venster
- Winter
- Met
- binnen
- zonder
- WMS
- Mijn werk
- werkte
- werkzaam
- wereld
- zou
- jaar-
- jaar
- u
- Your
- jezelf
- zephyrnet
- zones