熱応力は、機械的応力の課題とともに、高度なパッケージングにおけるよく知られた問題です。 両方とも、熱膨張係数 (CTE) が相容れない材料の混合を必要とする不均一な統合によって悪化します。
影響はすでに現れており、パッケージ密度がチップあたり 1,000 バンプを超えて増加するにつれ、さらに悪化する可能性があります。
「CTE が比較的高い金属を組み合わせると、CTE 剛性がさらに高いポリマーが得られ、CTE が非常に低い誘電体が得られます。 一度すべてをまとめると、ストレスは避けられません」と、imec の機械的および熱的モデリングとキャラクタリゼーションの科学ディレクター兼 R&D マネージャーである Mario Gonzalez は述べています。
このような応力は、多くの場合、重大な反りやダイの傾きを引き起こし、信頼性を低下させる状況につながります。 「複数のレイヤー数を持つさまざまな基板技術を扱っています」と、エンジニアリング担当副社長のチップ グリーリーは述べています プロメックスインダストリーズ. 「特に、基板のコアの厚さが異なると、反りを含む多くの古典的な機械的問題が発生し始めます。これは、一部の大規模なプレーヤーにとっては問題となっています。 システム イン パッケージの異種統合マルチチップ モジュールをお持ちの多くのお客様に、基板のシャドー モアレ データを提供していただくようお願いしています。反省点。」
の高度な新技術担当副社長であるギラド・バラク氏によると、この株はさまざまな悪影響を及ぼし、さまざまな次元のスケールで経験しています。 ノヴァ. 「多くの場合、ナノ構造レベルでのフィーチャの曲げやねじれは、DRAM やフロントエンド ロジックのナノシートで見られるように、作り込まれた組み込み応力に起因します」と彼は言いました。 「別の例は、シリコン貫通ビア (TSV) 周辺の「キープアウト ゾーン」で典型的なように、誘発された歪みがハイエンド半導体構造の製造を妨げるミクロン スケールの領域に関連しています。 最後に、誘発された歪みの大規模な影響により、ウェーハの反りが発生し、ウェーハの取り扱いと製造が大幅に複雑になり、ウェーハ自体が破損するリスクがあります。 ウェーハの反りは、3D NAND デバイスの製造中によく見られるように、厚い誘電体層の堆積中に特に見られます。」
良いニュースは、業界がこれらおよび関連する問題を十分に認識していることです。 悪いニュースは、現在調査中の多くのアプローチがあるにもかかわらず、まだ解決策が不足していることです。
「反りを減らすにはさまざまな方法がありますが、どれも完全に成功するわけではなく、常にトレードオフが伴います。 Bruker Nano Surfaces & Metrology. 「問題は、限られたアプリケーションの選択に限定されたものではありません。 ダイを別の基板に取り付けるときはいつでも、これらの問題が発生します。」
これらすべては、検査と計測が引き続き重要な役割を果たさなければならないことを意味します。 ホット スポットなどの他の問題も、複数のチップを異種パッケージに組み合わせると悪化する可能性があります。
「テスト中、さまざまなチップがさまざまな時間とさまざまな温度で加熱され、適切に冷却する必要があるホット スポットが発生する可能性があります」 アムコール. 「さまざまなチップの面積を一致させる特定の熱アクティブコントローラーを作成することに加えて、テストプログラムによって提供されるベクトルに基づいてホットスポットを「予測」できる適応型熱コントローラーを開発するための重要な努力があります。」
このような組み合わせは、問題の根源に最も迅速に到達するためにさまざまな技術を組み合わせたハイブリッド計測の使用の増加にもつながっています。
設計、検査、試験ソリューション
実際、設計、検査、および熱機械的応力の間の古典的な相互作用は、ますます小さくなり壊れやすい接続が何千もあることで、より複雑になっただけです。
その結果の XNUMX つは、過熱や機械的ストレスにつながる可能性のある CTE の問題と、結果として生じるカスケード効果をうまく「設計」するために、左側にシフトすることを新たに強調することです。 また、重大な欠陥を発見するだけでなく、防止する可能性を高めるには、シミュレーションと検査の両方が必要であると、米国の電子および半導体産業セグメントのポートフォリオ開発エグゼクティブである Andras Vass-Varnai 氏は述べています。 Siemens Digital Industries Software.
「パッケージの初期設計段階で、計算フローダイナミクス (CFD)、有限要素モデリング (FEA) などを使用した熱および構造の協調シミュレーションは、アセンブリの期待される性能を理解するのに役立ち、また、'設計上の選択肢の多くをパラメータ化できるため、AI 主導の最適化が可能です」と Vass-Varnai 氏は説明します。 「最初のプロトタイプが構築されると、熱過渡試験はコンポーネントの熱性能をマッピングするのに役立ちます。 予想される熱挙動と実際の熱挙動との間に不一致がある場合、テスト データを使用してパッケージ デジタル ツインの材料特性を「調整」し、材料ライブラリを更新して、今後の設計の初期精度を高めることができます。」
バンプ アレイをテストし、テスト用に設計するための最良の方法を見つけることは、ますます大きな課題となっています。 「上下する信号があったら?」 ロブ・エイトケンは尋ねた。 シノプシス 仲間。 「これはテストの問題を引き起こします。なぜなら、どこにも行かない信号とどこからともなく来る別の信号があり、それらをどのようにテストするかを考え出さなければならないからです。 それらを調査しますか? しかし、その場合、維持しなければならない物理的な寸法があり、機械的な損傷のリスクがあります。 それとも、ある種の JTAG のような構造を見つけますか? しかし、それはこれらの接続点の効率を低下させます。 私たちは大規模な実験段階にあり、誰もが「これでうまくいくかもしれないし、あれもうまくいくかもしれない」と言っています。 現時点では、必ずしも「それ」が何であるかに賭ける必要はありません。」
JCET によると、欠陥調査には間接テスト オプションと直接テスト オプションの両方があります。 たとえば、CSAM (Computed Scanning Acoustic Tomography) と 3D X 線は間接的なものですが、機械的断面分析は直接的な証拠のためのツールです。 JCET は、機械的欠陥に起因する材料/構造の問題を特徴付けるために、高度な熱特性評価装置も備えています。
いつものように、光学検査はインライン検査の最速のアプローチですが、ベスト プラクティスはハイブリッド アプローチです。 「ショート/オープンおよびわずかな欠陥を検出するための最良の方法は、SPI (はんだペースト検査) からリフロー前の AOI (自動光学検査)、リフロー後の AOI からインライン X 線への検査です」と研究担当副社長のティモシー スクネスは述べています。 Nordson Test & Inspection's での開発 サイバーオプティクス ポートフォリオ。
さらに、特に高度なノードでは、他のモダリティが役立つ場合があります。 たとえば、半導体デバイスの歪みを特徴付ける最近のアプローチは、ラマン分光法 (RS) です。 「RS は構造上の測定に非常に適しています。数秒単位の迅速な測定と、詳細な測定を可能にする数ミクロンの小さなスポット サイズを提供します」と、Nova の Barak 氏は述べています。 「ファブのインライン測定ツールとしてラマン分光法を導入する前に、構造の歪みを直接測定することは困難であったため、製造プロセスのかなり後の段階でテストを行うことになりました。」
最終的に、徹底した検査のために手抜きはありません。 予算の計算には、新しい機器の初期費用と過剰な RMA の継続的な費用など、比較指標が必要になる場合があります。 もう XNUMX つ考慮すべきことがあります。データを信頼できるようにする方法です。
「エンドユーザーに渡すものに問題のある素材が含まれていないことを確認するために、おそらく良い素材だったものを捨てるつもりですか? その費用は誰が負担するのですか?」 のソフトウェア製品管理ディレクターであるマイク・マッキンタイア氏は、次のように警告しています。 イノベーションへ、自動欠陥分類を行う際に正確な比較評価のために統計データベースを推奨しています。
反り
応力による最悪の結果の XNUMX つは反りです。 反りを検出するのが難しいことは驚くかもしれませんが、その影響は見かけほど明らかではありません。 反りにより、チップと基板の間の共平面性にわずかな違いが生じ、一部のマイクロバンプが下のパッドと不十分に接続する原因となります。これは、ノンウェットと呼ばれる障害です。
「例として、50 ~ 60mm の高度なプロセッサーを考えてみてください」と Chen 氏は言います。 「サイズが大きいため、反りのない加工が困難です。 それでも、ダイアタッチ ツールがプロセス ウィンドウの中央に調整されていれば、検査に合格し、高い歩留まりで製造できます。 問題は、許容範囲が非常に狭い可能性があることです。 反りの上にダイが少し傾くとすぐに、ウェット以外の問題が発生します。」
さらに悪いことに、これが 50µm 範囲のバンプ ピッチ ( ̴35µm バンプ サイズ) で発生している場合、バンプの寸法がさらに縮小するにつれて問題が発生することを想像してください。 2023 年から 2024 年にかけて次世代に移行する自動車業界では、すでに懸念材料となっています。重要な移行は 28nm ノードあたりになると、Chen 氏は述べています。
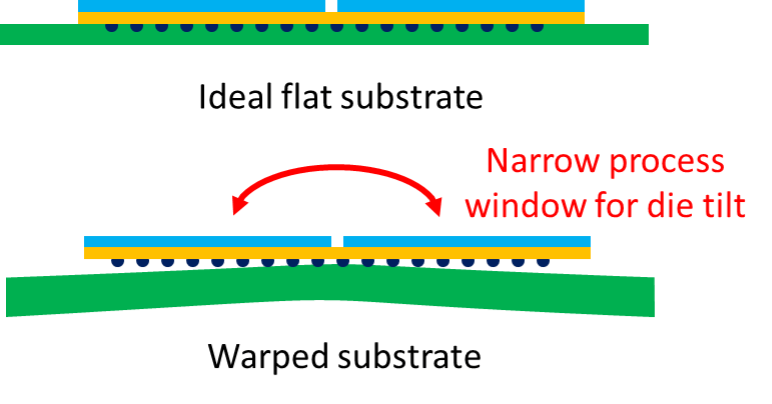
図 1 ダイアタッチ ツールでは、反りがある場合のダイの傾きに対するプロセス ウィンドウが非常に狭くなります。 出典:ブルカー
濡れない
「濡れない」とは、はんだバンプで発生する可能性のあるいくつかの問題を含む広い用語であり、そのほとんどはイライラするほど微妙です。 はんだは多くの場合液体の状態であるため、それを適用するプロセスは「ぬれ」と呼ばれています。 希薄なリンクは「非ウェット」と呼ばれ、接続が薄い小さなノードではより困難になっています。
濡れていないものは、通常のスクリーニング プロセスを逃れることが多く、後で返品されたチップ (RMA) として表示されます。 根本的な原因は、熱的、機械的、または複合的なものである可能性があります。たとえば、起伏の多い地形を走行している車のサーマル サイクリングなどです。 累積効果により、接触を切断するのに十分な熱機械的ストレスが発生する可能性があります。
特定のタイプの問題を説明する追加のニックネームがあります。 良好な接続の滑らかで円柱状の形状の代わりに、「枕に頭が入る」欠陥では、枕の上の頭のように、XNUMX つのボールが別のボールに沈み込むように見えます。
「まだ接触しているので、電気的テストは良好ですが、非常に壊れやすいことがわかります」と、枕の X 線写真を指して Chen 氏は言いました。 「熱ストレスや機械的ストレスがかかるとすぐに、完全に壊れる可能性があります。 接触が濡れていない場合でも、接続が薄いため、抵抗が高く、最適なパフォーマンスが得られず、長くは続かない可能性があります. 開いた濡れていないものはまったく機能しません。 ダイの傾きを伴う典型的なシナリオでは、整形されたバンプから濡れていない状態への目に見える移行があります。」
重大な問題は、潜在的な欠陥です。つまり、電気的テストに合格するのに十分機能する接続ですが、現場では失敗します。
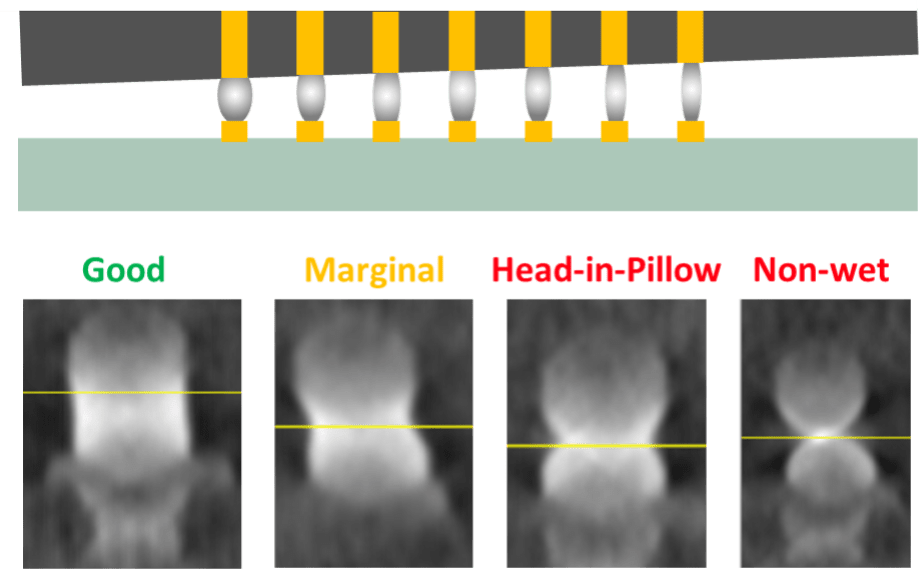
図 2 ダイの傾きが存在する場合の良好なバンプから非ウェットへの段階的な遷移。 出典:ブルカー
「熱応力の影響により、多くのタイプのデバイスで現在大きな問題になっています」とChen氏は述べています。 「ある顧客は、e-test スクリーニングに合格して出荷された製品を持っていました。 残念ながら、その後に発生したウェット以外の故障のために、彼らは多くのRMAを持っていました。」
一部の企業は、非常に面倒な手作業による検査によってこの問題に取り組んでいます。 残念なことに、人間による検査は、特に検査官が数時間のシフト中に微妙なエラーを見つけようとしている場合、オペレーターの疲労の影響を受けます。
良い面としては、インラインで使用できる X 線ツールなど、検査への自動化されたアプローチがあります。 「特に自動車業界では、100dppb 未満を達成するための高速で完全自動化された検査への大きな推進力があります」と、Chen 氏は述べています。
そこからさらに複雑になります。 ドレーパーの研究所技術スタッフの主要メンバーであるトム・マリニスは、次のように述べています。 「チップと基板間の接続の電流密度が一定期間にわたって特定のはんだに対して高すぎる場合、デバイスの動作温度に比べてはんだの溶融温度が比較的低い可能性があるため、マイグレーションが発生する可能性があります。実際にボイドを形成し、最終的に接続を開きます。」
マリニス氏は、デバイス PCB レベルでの商用モデリング ツールは、潜在的なエレクトロマイグレーションの問題を一貫して警告できるほど成熟していないため、加速エージング テストを実行することが重要であると警告しています。
まとめ
最終的に、潜在的な欠陥から信頼性の問題を検出するには、ダイのシフト、回転、高さ、傾き、およびその他のパラメーターに敏感な、より高度なサンプリング計測が必要になります。 また、製造前に潜在的な問題を予測して解決するために、マルチフィジックス モデリングへの依存度を高める必要があります。 また、半導体産業と自動車産業が混同し続ける中、RMA だけでなく、はるかに多くのことが危険にさらされています。
「人々の命を危険にさらす可能性のある潜在的な欠陥がデバイスからモジュール、さらには自動車へと移行するにつれて、失敗のコストは指数関数的に増大します」とチェン氏は述べています。 そのため、チップ メーカーは、設計、検査、およびテストを組み合わせて潜在的な障害をより適切に検出する総合的なソリューションを作成しています。
- SEO を活用したコンテンツと PR 配信。 今日増幅されます。
- Platoblockchain。 Web3メタバースインテリジェンス。 知識の増幅。 こちらからアクセスしてください。
- 情報源: https://semiengineering.com/bump-reliability-is-challenged-by-latent-defects/
- 000
- 1
- 2023
- 2024
- 3d
- a
- 加速された
- 従った
- 精度
- 正確な
- 達成する
- アクティブ
- 実際に
- 添加
- NEW
- アドレッシング
- 高度な
- 高齢化
- 警告
- すべて
- ことができます
- 既に
- しかし
- 常に
- 分析
- &
- 別の
- 予想する
- 適用可能な
- 適用
- アプローチ
- アプローチ
- AREA
- エリア
- 周りに
- アセンブリ
- 評価
- 関連する
- アタッチ
- 自動化
- 自動車
- 自動車産業
- 悪い
- 玉
- ベース
- 基礎
- くま
- なぜなら
- になる
- になる
- 背後に
- さ
- 以下
- BEST
- 賭ける
- より良いです
- の間に
- 越えて
- ビッグ
- より大きい
- ビット
- ブレーク
- 広い
- 予算
- 内蔵
- 内蔵
- ビジネス
- 事業開発
- 呼ばれます
- 取得することができます
- 自動車
- 自動車
- 場合
- レスリング
- 原因となる
- 原因
- 原因
- センター
- CFD
- 挑戦する
- 挑戦した
- 課題
- 挑戦
- チャンス
- 変更
- 特徴づけます
- チェン
- チップ
- チップ
- 選択肢
- クラシック
- 分類
- 組み合わせ
- 組み合わせ
- 組み合わせる
- 組み合わせた
- 結合
- 来ます
- コマーシャル
- コマンドと
- 企業
- 比べ
- 完全に
- 複雑な
- 複雑な
- コンポーネント
- 懸念
- 条件
- お問合せ
- 接続
- Connections
- 検討
- 接触
- 続ける
- 基本
- コーナー
- 費用
- 可能性
- カバーする
- 作ります
- 作成した
- 作成します。
- 作成
- 重大な
- 電流プローブ
- 現在
- 顧客
- Customers
- 切断
- データ
- データベース
- 取引
- 密度
- 説明する
- 設計
- デザイン
- 詳細な
- 開発する
- 発展した
- 開発
- デバイス
- Devices
- 死
- の違い
- 異なります
- 難しさ
- デジタル
- デジタルツイン
- 大きさ
- 直接
- 直接に
- 取締役
- すること
- ドント
- ダウン
- 呉服屋
- ドライバー
- ダビングされた
- 間に
- ダイナミクス
- 早い
- 効果
- 効果
- 効率
- 努力
- 電子
- 強調
- エンジニアリング
- 十分な
- 確保
- 装置
- エラー
- 特に
- 等
- エーテル(ETH)
- さらに
- 最終的に
- すべてのもの
- 例
- エグゼクティブ
- 拡大
- 予想される
- 経験豊かな
- 説明
- 調査済み
- 指数関数的に
- 非常に
- フェイル
- 不良解析
- 最速
- 疲労
- 特徴
- 仲間
- 少数の
- フィールド
- イチジク
- フィギュア
- 最後に
- もう完成させ、ワークスペースに掲示しましたか?
- 発見
- 名
- フロー
- フォーム
- 発見
- から
- イライラする
- 機能的な
- さらに
- 世代
- 取得する
- ゴエス
- 行く
- 良い
- 緩やかな
- 成長
- 育ちます
- ハンドリング
- ハード
- 高さ
- 助けます
- ことができます
- ハイ
- より高い
- 非常に
- 包括的な
- うまくいけば
- HOT
- 認定条件
- How To
- HTTPS
- 人間
- ハイブリッド
- 影響
- 重要
- in
- 含めて
- 増える
- の増加
- 産業
- 産業を変えます
- 初期
- を取得する必要がある者
- 楽器
- 統合
- 概要
- 調査
- 分離された
- 問題
- 問題
- IT
- 自体
- 種類
- 実験室
- 大
- 大規模
- より大きい
- 姓
- 層
- 層
- つながる
- 主要な
- リード
- ツェッペリン
- レベル
- ライブラリ
- 可能性が高い
- リンク
- 液体
- 命
- 長い
- たくさん
- ロー
- 維持する
- make
- 作成
- 管理
- マネージャー
- マニュアル
- 製造された
- 多くの
- 地図
- マリオ
- マッチング
- 材料
- 材料
- 成熟した
- 最大幅
- 手段
- 測定結果
- 計測
- 機械的な
- メンバー
- 金属
- 方法
- 方法論
- メトリック
- 計量
- かもしれない
- 移行
- 混じる
- モデリング
- モジュール
- モジュール
- 他には?
- 最も
- 移動
- の試合に
- ドワーフ
- 必ずしも
- 必要とされる
- 負
- それにもかかわらず
- 新作
- 新技術
- ニュース
- 次の
- ノード
- 明白
- 提供すること
- ONE
- 継続
- 開いた
- オペレーティング
- オペレータ
- 最適化
- オプション
- 注文
- その他
- パッケージ
- パッケージ
- 包装
- 痛み
- パラメータ
- 特定の
- 特に
- 渡された
- 人々の
- 実行する
- パフォーマンス
- 期間
- 相
- 物理的な
- ピッチ
- プラトン
- プラトンデータインテリジェンス
- プラトデータ
- プレイ
- プレーヤー
- ポイント
- ポイント
- ポリマー
- ポートフォリオ
- 正の
- 可能
- 潜在的な
- 練習
- プレゼンス
- 社長
- 予防
- 校長
- 事前の
- 多分
- プローブ
- 問題
- 問題
- プロセス
- ラボレーション
- プロセッサ
- プロダクト
- 製品管理
- 生産
- 演奏曲目
- 証明
- 正しく
- プロパティ
- プロトタイプ
- 提供します
- 提供
- 置きます
- R&D
- 範囲
- 急速な
- リアル
- 最近
- お勧めする
- 減らします
- 軽減
- 反射
- 相対的に
- 信頼性
- 依存
- 新たな
- 必要とする
- 必要
- 研究
- 研究開発
- 結果
- 結果として
- 結果
- リスク
- リスク
- 役割
- ルート
- ラン
- 前記
- 言う
- 秤
- スキャニング
- シナリオ
- スクリーニング
- 秒
- と思われる
- セグメント
- 選択
- 半導体
- シニア
- 敏感な
- いくつかの
- Shadow
- 形状
- シフト
- シフト
- 出荷
- ショート
- 表示する
- シグナル
- 重要
- 著しく
- サイズ
- サイズ
- 小さい
- より小さい
- So
- ソフトウェア
- ソリューション
- 一部
- すぐに
- ソース
- 特定の
- 分光法
- Spot
- スタッフ
- ステージ
- ステージ
- 利害関係
- start
- 都道府県
- 統計的
- まだ
- ストレス
- 構造の
- 構造
- テーマ
- 成功した
- そのような
- 驚くべき
- 技術的
- テクニック
- テクノロジー
- test
- テスト
- エリア
- アプリ環境に合わせて
- そこ。
- サーマル
- もの
- 物事
- 数千
- 介して
- 投げる
- 時間
- <font style="vertical-align: inherit;">回数</font>
- 〜へ
- 一緒に
- 公差
- あまりに
- ツール
- 豊富なツール群
- top
- に向かって
- 遷移
- 信頼
- 順番
- 典型的な
- わかる
- 今後の
- アップデイト
- つかいます
- ユーザー
- さまざまな
- 広大な
- 副会長
- 目に見える
- 周知
- この試験は
- which
- while
- 誰
- 意志
- 無し
- 仕事
- 最悪
- でしょう
- X線
- 収量
- あなたの
- ゼファーネット