Prevenire la propagazione di difetti sistematici negli odierni processi dalla progettazione alla fabbricazione dei semiconduttori richiede numerose fasi di convalida, analisi e ottimizzazione. Gli strumenti coinvolti in questo processo possono includere il controllo delle regole di progettazione (DRC), la verifica della correzione ottica di prossimità (OPC), la scrittura di maschere e la metrologia/ispezione della stampa di wafer (per valutare il processo), la metrologia/ispezione della stampa di wafer e l'analisi dei guasti fisici per confermare il guasto. diagnosi. Lo scambio di informazioni e la coottimizzazione tra queste fasi è un processo complesso, con molti cicli di feed-forward e feedback. La comunicazione è spesso ostacolata da “muri” tra le varie parti della tecnologia di processo, che rallentano l’innovazione. Alla recente conferenza SPIE, Siemens EDA ha presentato un discorso programmatico in cui proponeva una serie di approcci per abbattere questi muri e migliorare la progettazione dei chip nel processo di produzione. Continua a leggere per scoprire come Siemens mira ad abbattere le barriere dell'innovazione estendendo la co-ottimizzazione della tecnologia di progettazione.
Informazioni sulla nota chiave
SPIE è la società internazionale di ottica e fotonica. L'organizzazione risale al 1955 e la sua conferenza è diventata un evento di primo piano per argomenti di progettazione e produzione avanzati. All’evento di quest’anno, Siemens ha presentato il keynote che è l’argomento di questo post. Molti hanno contribuito alla presentazione, tra cui Le Hong, Fan Jiang, Yuansheng Ma, Srividya Jayaram, Joe Kwan, Siemens EDA (Stati Uniti); Doohwan Kwak, Siemens EDA (Repubblica di Corea); Sankaranarayanan Paninjath Ayyappan, Siemens EDA (India). Il titolo del discorso era Estensione della co-ottimizzazione della tecnologia di progettazione dal lancio della tecnologia all'HVM.
L'intervento faceva parte di una sessione sulla co-ottimizzazione della tecnologia di progettazione (DTCO). Questo concetto non è nuovo, ma Siemens ha esaminato la sua applicazione in un ambito più ampio del processo, dalla progettazione alla produzione ad alto volume (HVM). Le idee e i risultati presentati hanno implicazioni significative. Diamo uno sguardo più da vicino.
Cosa è stato presentato
Innanzitutto è stato presentato uno sguardo allo stato attuale dell’utilizzo del DTCO nelle parti chiave dell’ecosistema. Dal punto di vista del design, molte aziende fabless avanzate dispongono di un team DFM che vede i limiti di un approccio basato su modelli. Ciò che è veramente necessario è una nuova tecnologia per facilitare l’apprendimento della resa senza dipendere dalla fonderia.
Le fonderie utilizzano approcci di apprendimento automatico basati su modelli di forza bruta, che sono costosi ma non completamente efficaci. Stanno anche cercando un efficiente information mining degli enormi dati di produzione che creano. I fornitori di apparecchiature e i fornitori di EDA hanno lavorato più strettamente insieme e stanno proponendo soluzioni di apprendimento automatico più efficienti.
Facendo un passo indietro, è stato sottolineato che esistono dei muri tra le fasi di progettazione e produzione del processo. Le aziende Fabless creano il progetto, eseguono la DRC e la progettazione per la produzione (DFM), quindi lo lanciano oltre il muro al team OPC/RET all'interno della fonderia o IDM. Il progetto esegue attività come OPC e verifica, quindi i dati vengono gettati su un altro muro per la scrittura della maschera e la metrologia/ispezione. Il muro finale è per la fabbricazione. Qui verranno eseguiti test elettrici e analisi dei guasti. Quando viene individuata la causa principale del fallimento, sono trascorsi 6-18 mesi. È un ciclo di feedback molto lungo. Il grafico nella parte superiore di questo post descrive questo processo.
DTCO tenta di abbattere i muri, ma le metodologie disponibili sono incomplete. Il DTCO tradizionale inizia molto presto nello sviluppo del processo. A partire da un'esigenza di ridimensionamento, viene definita una cella standard e vengono eseguiti la sintesi, il posizionamento e il percorso per elaborare modelli di base e misurare le prestazioni e la potenza. Viene eseguito anche il cedimento della SRAM e i dati ritornano al design della cella standard.
Ciò che è stato presentato al keynote di SPIE è stato un modo per estendere questo concetto di co-ottimizzazione all'intero processo, dalla progettazione alla produzione. L'approccio implica consentire un flusso più semplice di informazioni dalla progettazione fino al processo finale e all'analisi fisica creando un canale informativo.
Anche se questo sembra semplice, non lo è. Molte sfide sono state discusse con approcci concreti per mitigare i problemi. Ad esempio, i primi progetti possono essere creati con generatori sintetici di layout per aiutare a calibrare il processo rispetto ai problemi di progettazione reali man mano che il processo viene sviluppato. Ciò può alleviare molte delle sorprese attualmente affrontate con le prime eliminazioni dei processi.
Gestire enormi volumi di dati è un’altra sfida. Utilizzando nuove e sofisticate tecniche di compressione, è possibile un miglioramento di 30 volte. Ciò migliora notevolmente le attività di gestione e analisi dei dati. Un concetto chiamato AI spiegabile può aiutare a trovare le cause profonde dei problemi molto più velocemente. Un’altra area di miglioramento è la capacità di riqualificare i modelli di intelligenza artificiale in una fase successiva del processo di produzione senza invalidare i risultati precedenti. Anche nell’area dell’analisi dei dati ci sono tecniche per gestire i “dati sbilanciati”. Ad esempio, potrebbe essere presente un punto caldo in 100,000,000 di modelli.
Mettere insieme tutto questo può creare un flusso di progettazione end-to-end molto più efficiente, come mostrato nella figura seguente.
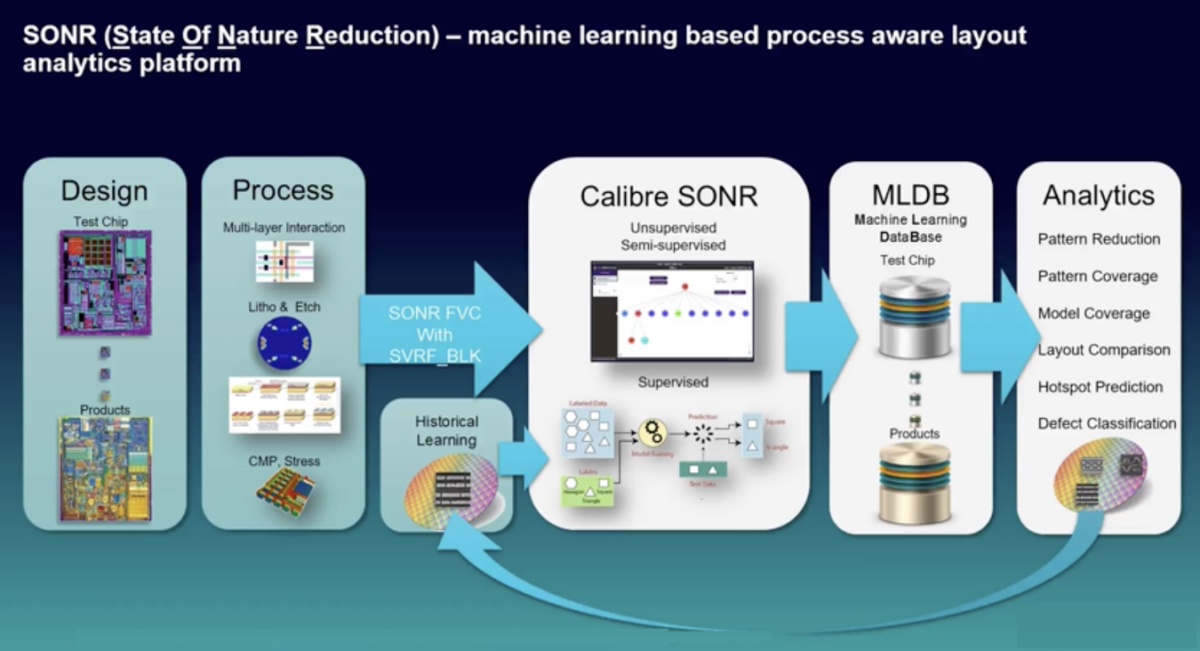
Per saperne di più
L’impatto degli approcci delineati in questa presentazione principale è sostanziale. Puoi visualizza la presentazione e accedi a un white paper sul processo qui. Ci sono molte informazioni utili da ottenere. Ed è così che Siemens mira ad abbattere le barriere dell’innovazione estendendo la co-ottimizzazione della tecnologia di progettazione.
Condividi questo post tramite:
- Distribuzione di contenuti basati su SEO e PR. Ricevi amplificazione oggi.
- PlatoData.Network Generativo verticale Ai. Potenzia te stesso. Accedi qui.
- PlatoAiStream. Intelligenza Web3. Conoscenza amplificata. Accedi qui.
- PlatoneESG. Carbonio, Tecnologia pulita, Energia, Ambiente, Solare, Gestione dei rifiuti. Accedi qui.
- Platone Salute. Intelligence sulle biotecnologie e sulle sperimentazioni cliniche. Accedi qui.
- Fonte: https://semiwiki.com/events/339386-spie-2023-buzz-siemens-aims-to-break-down-innovation-barriers-by-extending-design-technology-co-optimization/
- :ha
- :È
- :non
- $ SU
- 000
- 100
- 2023
- a
- capacità
- accesso
- operanti in
- indirizzo
- Avanzate
- AI
- Modelli AI
- mira
- Tutti
- alleviare
- anche
- an
- .
- ed
- Un altro
- Applicazioni
- approccio
- approcci
- SONO
- RISERVATA
- AS
- At
- Tentativi
- disponibile
- precedente
- barriere
- basic
- BE
- diventare
- stato
- sotto
- fra
- Po
- Rompere
- più ampia
- ma
- by
- detto
- Materiale
- Causare
- cause
- cella
- Challenge
- sfide
- canale
- verifica
- patata fritta
- più vicino
- CO
- Venire
- arrivo
- Comunicazione
- Aziende
- completamente
- complesso
- concetto
- calcestruzzo
- Convegno
- Confermare
- contributori
- costoso
- creare
- creato
- Creazione
- Corrente
- Stato attuale
- Attualmente
- dati
- analisi dei dati
- Date
- affare
- definito
- dipendenza
- Design
- disegni
- dettagli
- sviluppato
- Mercato
- diagnosi
- discusso
- fatto
- giù
- Repubblica Democratica del Congo
- In precedenza
- Presto
- più facile
- ecosistema
- Efficace
- efficiente
- consentendo
- da un capo all'altro
- Intero
- usate
- Evento
- esempio
- exchange
- estendere
- estendendo
- di fronte
- facilitare
- Fallimento
- fan
- più veloce
- feedback
- figura
- finale
- Trovare
- flusso
- Nel
- essere trovato
- Fonderia
- da
- guadagnato
- valutare
- Generatori
- grafico
- Manovrabilità
- Avere
- Aiuto
- qui
- Hong
- HOT
- Come
- HTTPS
- idee
- Impact
- implicazioni
- competenze
- miglioramento
- migliora
- in
- includere
- Compreso
- India
- informazioni
- Innovazione
- Internazionale
- coinvolto
- comporta
- sicurezza
- IT
- SUO
- joe
- Le
- Nota fondamentale
- Corea
- dopo
- lanciare
- disposizione
- IMPARARE
- apprendimento
- limiti
- Lunghi
- Guarda
- guardò
- lotto
- macchina
- machine learning
- consigliato per la
- molti
- mask
- massiccio
- max-width
- Maggio..
- misurare
- metodologie
- Siti di estrazione mineraria
- Ridurre la perdita dienergia con una
- modelli
- mese
- Scopri di più
- più efficiente
- molti
- Bisogno
- di applicazione
- New
- of
- di frequente
- on
- ONE
- ottica
- Ottica e fotonica
- ottimizzazione
- or
- organizzazione
- su
- delineato
- ancora
- Carta
- parte
- Ricambi
- Passato
- modelli
- eseguire
- performance
- eseguita
- prospettiva
- Fisico
- posto
- piattaforma
- Platone
- Platone Data Intelligence
- PlatoneDati
- possibile
- Post
- energia
- premier
- presentazione
- presentata
- stampa
- problemi
- processi
- propagazione
- proposto
- abbastanza
- Leggi
- di rose
- veramente
- recente
- Repubblica
- richiede
- Risultati
- radice
- strada
- Regola
- scala
- portata
- vedere
- vedendo
- cerca
- semiconduttore
- Serie
- Sessione
- mostrato
- Siemens
- significativa
- Rallentamento
- Società
- Soluzioni
- sofisticato
- Spot
- Standard
- Di partenza
- inizio
- Regione / Stato
- stati
- Passi
- sostanziale
- tale
- sorprese
- sintesi
- sintetico
- Fai
- Parlare
- task
- team
- tecniche
- Tecnologia
- test
- che
- Il
- poi
- Là.
- Strumenti Bowman per analizzare le seguenti finiture:
- di
- questo
- tempo
- Titolo
- a
- di oggi
- insieme
- strumenti
- top
- argomento
- Argomenti
- scossa
- sballottati
- tradizionale
- Unito
- Stati Uniti
- Impiego
- informazioni utili
- utilizzando
- convalida
- vario
- fornitori
- Convalida
- molto
- via
- volumi
- Muro
- Prima
- Modo..
- sono stati
- Che
- Che cosa è l'
- quale
- bianca
- white paper
- volere
- con
- entro
- senza
- lavoro
- scrittura
- dare la precedenza
- cedevole
- Tu
- zefiro