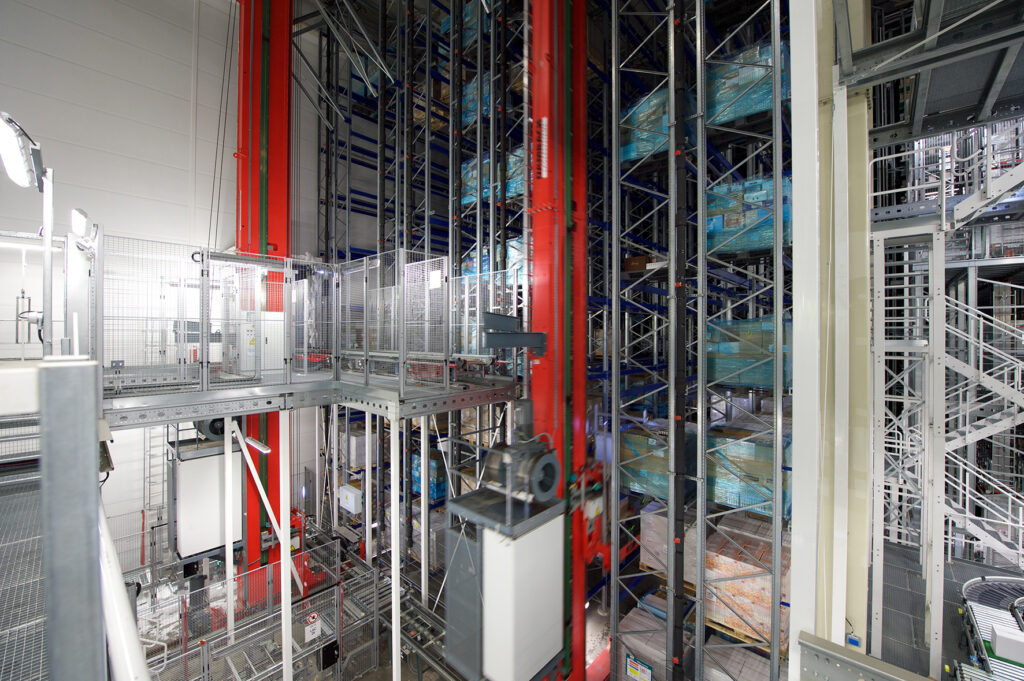
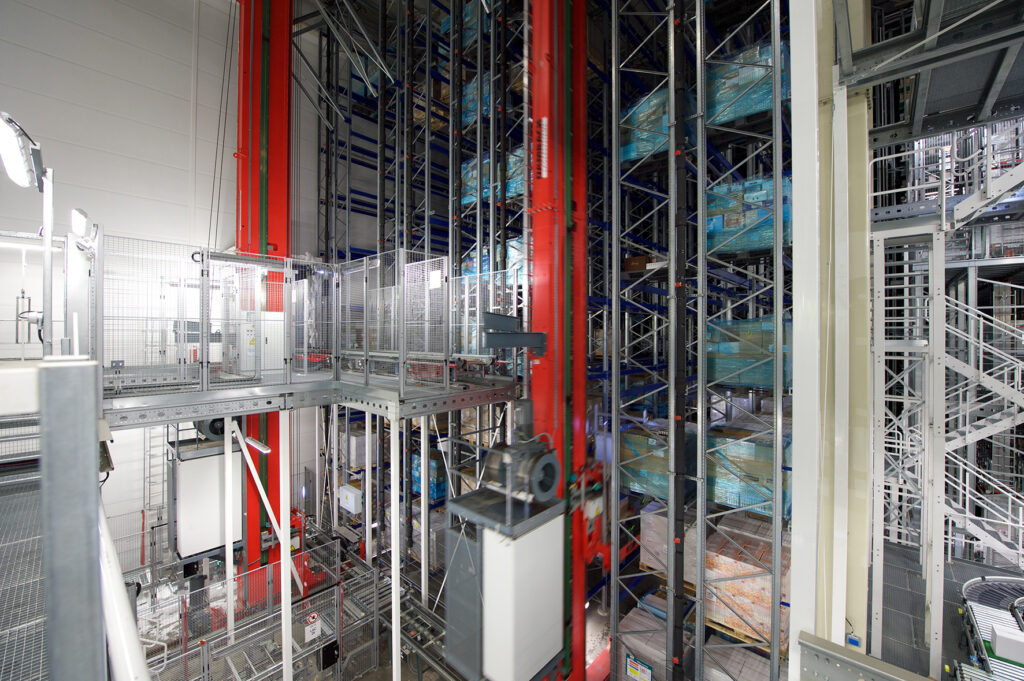
Memperluas pusat logistik multi-suhu yang sangat dinamis untuk sekitar 1,200 toko selama operasi yang sedang berlangsung dengan peningkatan kinerja pengambilan dari 480,000 menjadi hampir 625,000 peti setiap hari, merupakan tantangan yang sangat besar. Namun ketika pesanan di toko dan online terus melonjak karena berbagai lockdown dan tim hanya diperbolehkan bekerja dengan keterbatasan yang parah karena pembatasan Covid 19, maka diperlukan lebih dari sekadar pengetahuan teknis dan organisasi di kedua sisi untuk proyek tersebut agar berhasil. WITRON dan pengecer makanan COOP dari Norwegia telah menunjukkan hal ini dengan mengesankan.
Ketika dua direktur pelaksana Geir Inge Stokke (COOP) dan Helmut Prieschenk (WITRON) menandatangani kontrak perluasan pusat distribusi multi-suhu COOP di dekat Oslo pada akhir Mei 2019, tidak satu pun dari mereka yang mengetahui tantangan besar tersebut. mereka harus menghadapinya. Sejak bulan Maret 2020, dunia terhenti karena Covid, dan permintaan konsumen melonjak secara signifikan didorong oleh berbagai kebijakan lockdown. Ini merupakan awal yang kurang menguntungkan untuk proyek brownfield yang mungkin paling menantang dalam sejarah perusahaan WITRON hingga saat ini, di mana teknologi yang ada dimodernisasi dan modul-modul baru diintegrasikan – baik di gedung yang ada maupun di fasilitas perluasan baru.
Tugas yang ditujukan kepada Gaute Glomlien dari COOP dan Holger Weiß dari WITRON dijelaskan sebagai berikut: untuk memperluas fasilitas logistik barang kering, segar, dan beku dari 52,000 meter persegi menjadi 84,000 meter persegi di bawah langkah-langkah keselamatan Covid 19, untuk meningkatkan produksi sebesar 30 persen , untuk mengintegrasikan mesin COM baru, untuk memasang lorong AS/RS palet dan baki tambahan serta berbagai komponen konveyor, untuk meningkatkan ukuran buffer pengiriman yang sepenuhnya otomatis, untuk memperbarui sistem WMS yang sesuai ke teknologi terbaru, dan untuk menerapkan semua ini ke dalam aliran material yang ada selama operasi yang sedang berlangsung tanpa kehilangan kinerja.
“Kami mampu menghemat jutaan euro setiap tahunnya dengan sistem WITRON. Oleh karena itu, jelas bahwa kami juga akan mewujudkan ekspansi tersebut dengan WITRON dan teknologi logistik terdepannya”, jelas manajer proyek COOP, Glomlien. Perluasan ini juga diperlukan karena pengecer mengakuisisi pesaing dan oleh karena itu tumbuh lebih kuat dan lebih cepat dari yang diperkirakan ketika pusat logistik didirikan.
“COOP adalah proyek pertunjukan bagi kami. Banyak pelanggan internasional mengunjungi fasilitas tersebut dan dengan perluasan ini kami mampu membuktikan secara mengesankan bahwa kami dapat menangani tugas tersebut selama operasi berjalan sesuai anggaran dan tepat waktu meskipun terjadi peningkatan volume – baik dari segi hasil produksi maupun item – di gudang dan meskipun terjadi pandemi ”, Holger Weiß dengan bangga melaporkan. Pada musim semi 2023, 42 mesin COM (sebelas COM baru telah dipasang) akan beroperasi di seluruh zona suhu dan sistem logistik COOP dapat menangani lebih dari 625,000 kasus setiap hari. Secara total, fasilitas ini terdiri dari lebih dari 600,000 lokasi penyimpanan palet, tas jinjing, dan baki serta 130 derek penumpuk, dan teknologi konveyor berkilo-kilo meter.
Tantangan berhasil dikuasai
Dari fasilitas (dengan lima zona suhu berbeda), MENGURUNG memasok 1,200 toko yang berlokasi di seluruh Norwegia, dari wilayah metropolitan di sekitar Oslo dan ujung utara Norwegia dari berbagai macam 13,000 item yang berbeda. “Pada awal proyek, terlihat jelas bahwa kami perlu meningkatkan kapasitas pengambilan secara signifikan”, canda Glomlien hari ini. “Volume pusat logistik meningkat hampir dua kali lipat”, jawab Weiß sambil tertawa. Glomlien dan dia melakukan diskusi yang sulit dalam beberapa situasi. Hari ini, mereka duduk di depan mikrofon Teams dan senang bisa bertemu lagi secara virtual. “Itu adalah saat yang tepat”, Weiß menyimpulkan setelah percakapan, dan rekannya dari Norwegia setuju.
Ketika dia mengingat beberapa hari, minggu, dan bulan dalam proyek tersebut, dia berhenti sejenak, mengingat, dan kemudian melanjutkan dengan lebih bangga. “Perbatasan ditutup. Ada pembatasan masuk yang rumit. Pihak berwenang memerintahkan tindakan karantina yang ketat. Selama ini tim proyek hanya diperbolehkan berkendara dari hotel (yang tidak boleh ditinggal karena alasan lain) ke pusat logistik dan sebaliknya. Kafetaria di lokasi juga ditutup. Bahkan di hotel, layanannya dikurangi seminimal mungkin. Ini adalah sesuatu yang harus Anda atasi sebagai sebuah tim. Ini adalah kerugian nyata – tidak hanya bagi tim pelanggan, tetapi juga bagi kolega kami. Sebagai manajer proyek, Anda bertanya pada diri sendiri setiap malam bagaimana Anda dapat menjaga motivasi tim Anda”, tegas Weiß. Tim WITRON berpindah-pindah dengan izin khusus dari pemerintah. Logistik COOP secara sistematis penting. “Selama pandemi, jumlah pesanan semakin meningkat”, kenang Glomlien.
Sektor logistik makanan beku merupakan tantangan teknis khusus bagi Upper falz Holger Weiß. “Kami “memanaskan” area otomatis yang ada dari minus 25 °C menjadi minus 5 °C, dan COOP untuk sementara memindahkan barang ke area penyimpanan konvensional untuk diambil. Dalam waktu delapan minggu, kami kemudian melakukan semua penyesuaian di bidang perakitan listrik, platform, teknologi konveyor palet dan baki hingga freezer yang ada ditingkatkan kembali. Dua mesin COM baru, serta dua lorong penyimpanan palet lagi, empat lorong penyimpanan baki, derek penumpuk tambahan, de-palletizer, dan sistem konveyor yang sesuai kemudian dipasang di gedung freezer baru.
“Urutan pemasangan direncanakan dengan cermat dalam proses bersama, dan kami memprioritaskan pemasangan derek palet baru terlebih dahulu, yang akan memfasilitasi pengambilan CPS secara efisien di area beku yang luas. Kami kemudian mendinginkan zona produksi baru hingga suhu yang diperlukan, memindahkan produksi otomatis kami ke pengambilan CPS dari derek palet baru dan rak palet manual, serta memanaskan area produksi yang ada untuk mengakomodasi instalasi WITRON”, Glomlien menambahkan. “Fase ini memerlukan koordinasi yang cermat dan kolaborasi lintas fungsi antara sumber daya TI dan mekanik WITRON, serta tim COOP yang mengendalikan produksi, transportasi, dan manajemen pesanan, mulai dari commissioning hingga ramp-up dan selama fase produktif.
Setelah WITRON menyelesaikan instalasi baru di zona produksi kami yang sudah ada sebelumnya, prosesnya dibalik untuk penyelesaian area produksi baru. Pengambilan kemudian dipindahkan kembali ke mesin OPM yang sepenuhnya otomatis.”
Di COOP, penanggung jawab juga menyebut area pengambilan sebagai area produksi, jelas Holger Weiß.
Saat ini, total empat mesin COM bekerja di area barang beku di fasilitas tersebut. Ketika sistem didinginkan lagi hingga minus 25 °C, Weiß menyilangkan jari. “Jika kabel putus, ikat pinggang robek, motor mati, atau sensor rusak, hal ini akan sangat menarik karena rentang waktu yang tersedia sangat sempit” dan pada saat yang sama penting untuk mengingat kualitas barang yang disimpan untuk menghindari kerusakan produk yang besar. “Anda harus menggunakan komponen terbaik yang tersedia di pasar untuk proyek seperti ini. Kami tidak mengubah drive yang ada, tetapi kami memasang yang baru. Ini harus dijalankan sejak awal, karena jika tidak, proyek tidak akan selesai tepat waktu, atau pelanggan bahkan akan dikenakan biaya langsung jika barang tidak dapat dikirim.” Tim WITRON OnSite menggunakan waktu pembangunan kembali untuk melakukan pemeliharaan pada sistem. “Saat barang disimpan kembali, Anda harus selalu berkomunikasi dengan ruang kendali dan bereaksi cepat di lokasi”, jelas Weiß. Komunikasi antara tim pelanggan, tim proyek, dan tim di Tempat harus berjalan lancar. “Hasilnya tidak diragukan lagi menunjukkan bahwa ini berjalan dengan lancar”, manajer proyek WITRON menekankan. “Pekerjaan yang sangat detail membuahkan hasil. Setelah kami meningkatkan area barang beku, kami dapat dengan cepat kembali ke performa terbaik. Tidak ada kejutan negatif.”
Konsep modifikasi yang efisien juga untuk rangkaian barang kering
Mengikuti diskusi rinci dengan WITRON, COOP memutuskan untuk memasang lima mesin COM tambahan (total 17 dengan ruang untuk 4 COM lagi), empat lorong penyimpanan palet lagi, sepuluh lorong penyimpanan baki lagi, derek penumpuk dan mekanik sistem konveyor yang sesuai, tiga depalletizer, serta satu stretch-wrapper di area OPM rangkaian barang kering. “Fase penting telah tiba untuk rangkaian barang kering pada musim gugur tahun 2021 dan musim dingin tahun 2022”, kata Glomlien. “Ini adalah area dengan throughput tertinggi di pusat distribusi, dengan kompleksitas tambahan dengan dua sub-sistem OPM yang terpisah secara fisik yang bekerja sebagai satu unit terintegrasi. Untuk terus memasok semua pesanan tepat waktu dengan kualitas yang sama setelah dimulainya penggunaan area baru, proses peningkatan direncanakan dengan cermat, dan distribusi stok kami dipantau secara ketat untuk memastikan produk yang tepat siap untuk diambil di lokasi. waktu yang tepat”, kata Gaute Glomlien, menggambarkan perluasan yang terencana dengan baik. ”Emulasi mendetail yang dilakukan di awal oleh tim TI WITRON, bekerja sama dengan pemimpin produksi COOP, juga penting untuk mengidentifikasi strategi produksi yang tepat sebelum mulai menggunakan dua sub-sistem yang terintegrasi penuh. “Faktor yang menentukan di sini adalah keseimbangan pesanan yang tepat dan inventarisasi antar sub-sistem individual”, tambah Holger Weiß. “Strategi penerapan ini juga berhasil dengan sangat baik.”
Mengoptimalkan strategi pengambilan
Area makanan segar menerima empat mesin COM tambahan (total 21 dengan ruang untuk lima COM lagi), delapan lorong penyimpanan baki, dua lorong penyimpanan palet lagi, derek penumpuk dan mekanik sistem konveyor yang sesuai, dua de-palletizer, dan satu peregangan -pembungkus. “Kami kemudian menambahkan satu lagi bagian aliran material untuk sayuran dan buah-buahan di area produk segar untuk menyederhanakan penanganan barang lain di sektor ini. Di masa lalu, kelompok produk dipilih bersama-sama”, jelas Glomlien.
Buffer pengiriman yang sepenuhnya otomatis, yang mencakup berbagai zona suhu, telah diperluas sekali lagi.
Holger Weiß sedang mengerjakan proyek berikutnya di Swedia. Bisnis sehari-hari berlanjut untuk COOP di CLog. “Peningkatan ini telah memberi kami solusi canggih yang telah ditingkatkan selama operasi yang sedang berlangsung hingga mencapai volume keluaran yang bahkan tidak dapat diantisipasi dalam fase desain awal. Sekarang, kami lebih mengoptimalkan prosesnya”, jelas Glomlien. Dengan adanya perluasan, juga COOP perangkat lunak sistem diperbarui ke kondisi terkini WITRON.
Namun bahkan setelah proyek selesai, proses di pusat logistik terus berubah, hanya karena seluruh rantai pasokan dapat berfluktuasi dan kebutuhan pelanggan berubah. Itu sebabnya diperlukan fleksibilitas tingkat tinggi dalam semua proses. “COOP sedang melakukan proses perbaikan berkelanjutan dan telah memperoleh banyak pengalaman dengan fasilitas ini selama beberapa tahun terakhir. Ini juga sangat mengesankan bagi kami. Mereka menganalisis data, perhitungan, memilih strategi pengambilan yang tepat untuk wilayah dan toko, serta menentukan cara menyusun pesanan”, kata Weiß dengan antusias. Mereka juga mendukung rekan-rekan WITRON di lokasi dan di Parkstein ketika logika berubah.
Rasa hormat meluas ke semua pihak yang terlibat dalam proyek ini
Bagi CEO WITRON Helmut Prieschenk, fasilitas di Norwegia ini merupakan proyek pameran dalam banyak aspek. “Ini menunjukkan kemampuan transformasi proses otomatis. Hal ini menunjukkan seberapa efisien teknologi tambahan dapat diintegrasikan ke dalam sistem yang ada atau ke dalam gedung yang sudah ada selama operasi yang sedang berlangsung. Namun, bukan hanya teknologi dan bangunan yang menentukan proyek tersebut, namun juga orang-orang yang berhasil melaksanakan proyek tersebut hingga mencapai garis akhir. Orang-orang yang telah menunjukkan bagaimana situasi yang menantang sekalipun dapat diatasi secara efisien ketika tim proyek bekerja sama dengan cara yang konstruktif dan penuh kepercayaan di seluruh fase proyek.
Dengan perluasan ini, semua pihak yang terlibat dalam proyek ini telah menghasilkan sebuah mahakarya. Baik secara teknologi, namun terlebih lagi dalam hal komitmen yang ditunjukkan. Meskipun persyaratan teknis sudah menjadi tugas yang menantang bagi tim COOP dan WITRON, penerapannya menjadi semakin rumit selama berbulan-bulan akibat pandemi Corona. Untuk memenuhi jadwal waktu yang ketat meskipun terdapat hambatan dalam kebijakan kesehatan, para kolega menunjukkan “hati dan jiwa” yang maksimal, tumbuh dengan tantangan, dan melakukan pekerjaan dengan baik. Proyek dibuat oleh manusia untuk manusia. Dan orang-orang yang terlibat telah memberikan kinerja yang patut dihormati dan mewakili semangat kedua perusahaan.”
- Konten Bertenaga SEO & Distribusi PR. Dapatkan Amplifikasi Hari Ini.
- PlatoData.Jaringan Vertikal Generatif Ai. Berdayakan Diri Anda. Akses Di Sini.
- PlatoAiStream. Intelijen Web3. Pengetahuan Diperkuat. Akses Di Sini.
- PlatoESG. Otomotif / EV, Karbon, teknologi bersih, energi, Lingkungan Hidup, Tenaga surya, Penanganan limbah. Akses Di Sini.
- PlatoHealth. Kecerdasan Uji Coba Biotek dan Klinis. Akses Di Sini.
- ChartPrime. Tingkatkan Game Trading Anda dengan ChartPrime. Akses Di Sini.
- BlockOffset. Modernisasi Kepemilikan Offset Lingkungan. Akses Di Sini.
- Sumber: https://www.logisticsbusiness.com/transport-distribution/cold-chain-logistics/more-throughput-for-coop-dc-during-upgrade/
- :memiliki
- :adalah
- :bukan
- $NAIK
- 000
- 1
- 13
- 17
- 19
- 200
- 2019
- 2020
- 2021
- 2023
- 25
- 30
- 52
- 84
- a
- Sanggup
- menampung
- diperoleh
- di seluruh
- menambahkan
- tambahan
- Tambahan
- dialamatkan
- Menambahkan
- penyesuaian
- Setelah
- lagi
- Semua
- diizinkan
- hampir
- sudah
- juga
- selalu
- an
- analisa
- dan
- Lain
- Diantisipasi
- Apa pun
- ADALAH
- DAERAH
- sekitar
- Seni
- AS
- meminta
- aspek
- Majelis
- bermacam-macam
- diasumsikan
- At
- Pihak berwenang
- Otomatis
- tersedia
- menghindari
- kembali
- balancing
- BE
- karena
- menjadi
- Awal
- TERBAIK
- antara
- perbatasan
- kedua
- Kedua sisi
- Istirahat
- anggaran belanja
- penyangga
- Bangunan
- bisnis
- tapi
- by
- kabel
- CAN
- tidak bisa
- Kapasitas
- hati-hati
- hati-hati
- membawa
- kasus
- pusat
- pusat
- ceo
- rantai
- menantang
- tantangan
- menantang
- perubahan
- mengubah
- jelas
- tertutup
- rapat
- kolaborasi
- rekan
- COM
- bagaimana
- komitmen
- menyampaikan
- Komunikasi
- Perusahaan
- perusahaan
- saingan
- Lengkap
- penyelesaian
- kompleks
- kompleksitas
- rumit
- komponen
- terdiri dari
- konsep
- terus-menerus
- konstruktif
- terus
- terus
- kontinu
- kontrak
- kontrol
- mengendalikan
- konvensional
- Percakapan
- BEKERJA SAMA
- koordinasi
- Korona
- benar
- Sesuai
- Biaya
- bisa
- Mitra
- meliputi
- Jelas
- menyeberang
- sangat penting
- pelanggan
- pelanggan
- harian
- data
- Tanggal
- hari ke hari
- Hari
- dc
- memutuskan
- menentukan
- menetapkan
- disampaikan
- tuntutan
- menunjukkan
- dijelaskan
- layak
- Mendesain
- Meskipun
- rinci
- terperinci
- MELAKUKAN
- berbeda
- langsung
- Direksi
- diskusi
- distribusi
- dokumen
- turun
- mendorong
- didorong
- drive
- kering
- dua
- selama
- dinamis
- setiap
- efisien
- efisien
- sebelas
- menekankan
- akhir
- ditingkatkan
- memastikan
- Seluruh
- masuk
- mapan
- Euro
- Bahkan
- malam
- Setiap
- jelas
- menarik
- ada
- sistem yang ada
- Lihat lebih lanjut
- diperluas
- perluasan
- pengalaman
- menjelaskan
- Menjelaskan
- Meluas
- perpanjangan
- Menghadapi
- memudahkan
- Fasilitas
- faktor
- GAGAL
- Jatuh
- jauh
- lebih cepat
- beberapa
- menyelesaikan
- Pertama
- lima
- keluwesan
- aliran
- fluktuasi
- berikut
- makanan
- Untuk
- empat
- segar
- dari
- depan
- beku
- Buah-buahan
- sepenuhnya
- lebih lanjut
- diperoleh
- diberikan
- akan
- baik
- barang
- Pemerintah
- besar
- tumbuh
- Grup
- memiliki
- menangani
- Penanganan
- senang
- Memiliki
- he
- Kesehatan
- di sini
- High
- paling tinggi
- sangat
- -nya
- sejarah
- hotel
- Seterpercayaapakah Olymp Trade? Kesimpulan
- How To
- Namun
- HTTPS
- besar
- ide
- mengenali
- if
- melaksanakan
- implementasi
- penting
- impresif
- perbaikan
- in
- Meningkatkan
- Pada meningkat
- meningkatkan
- sendiri-sendiri
- install
- instalasi
- mengintegrasikan
- terpadu
- Internasional
- ke
- terlibat
- IT
- item
- Pekerjaan
- bersama
- jpg
- hanya
- Menjaga
- pengetahuan
- Terbaru
- pemimpin
- terkemuka
- meninggalkan
- Tingkat
- 'like'
- keterbatasan
- baris
- terletak
- lokasi
- kuncian
- logistik
- Panjang
- lama
- lepas
- Lot
- mesin-mesin
- Mesin
- terbuat
- pemeliharaan
- utama
- pengelolaan
- manajer
- pelaksana
- cara
- panduan
- banyak
- March
- Maret 2020
- Pasar
- hasil karya
- bahan
- maksimum
- Mungkin..
- ukuran
- mekanis
- mekanika
- Pelajari
- dengan cermat
- mikrofon
- jutaan
- keberatan
- minimum
- Modul
- saat
- dipantau
- bulan
- lebih
- paling
- motor
- terharu
- harus
- Dekat
- perlu
- dibutuhkan
- negatif
- juga tidak
- New
- berikutnya
- tidak
- utara
- Norway
- Norwegia
- sekarang
- jumlah
- of
- lepas
- on
- sekali
- ONE
- yang
- terus-menerus
- secara online
- hanya
- operasi
- Operasi
- mengoptimalkan
- or
- urutan
- perintah
- organisatoris
- asli
- Oslo
- Lainnya
- jika tidak
- kami
- lebih
- Mengatasi
- dibayar
- pandemi
- tertentu
- pihak
- lalu
- Konsultan Ahli
- persen
- melakukan
- prestasi
- dilakukan
- izin
- tahap
- Secara fisik
- memilih
- terpilih
- berencana
- Platform
- plato
- Kecerdasan Data Plato
- Data Plato
- kebijaksanaan
- posisi
- Sebelumnya
- diprioritaskan
- mungkin
- proses
- proses
- menghasilkan
- Produk
- Produksi
- produktif
- Produk
- proyek
- memprojeksikan
- dengan bangga
- Rasakan itu
- kualitas
- karantina
- segera
- jarak
- Bereaksi
- nyata
- menyadari
- alasan
- diterima
- mengurangi
- lihat
- wilayah
- daerah
- laporan
- merupakan
- wajib
- Persyaratan
- Sumber
- menghormati
- tanggung jawab
- pembatasan
- mengakibatkan
- pengecer
- kembali
- benar
- Kamar
- kira-kira
- Run
- Safety/keselamatan
- sama
- Save
- mengatakan
- menjadwalkan
- Bagian
- sektor
- melihat
- sensor
- terpisah
- Urutan
- layanan
- parah
- dikirimkan
- Pengiriman
- menampilkan
- menunjukkan
- ditunjukkan
- Pertunjukkan
- Sisi
- tertanda
- signifikan
- menyederhanakan
- duduk
- situs web
- situasi
- Ukuran
- lancar
- So
- melonjak
- larutan
- beberapa
- sesuatu
- Space
- khusus
- semangat
- musim semi
- kotak
- awal
- Negara
- state-of-the-art
- Masih
- saham
- penyimpanan
- menyimpan
- tersimpan
- toko
- strategi
- Penyelarasan
- ketat
- lebih kuat
- struktur
- subyek
- berhasil
- berhasil
- seperti itu
- menyediakan
- supply chain
- memasok
- mendukung
- kejutan
- Swedia
- sistem
- sistem
- tugas
- tim
- tim
- Teknis
- Teknologi
- sepuluh
- istilah
- dari
- bahwa
- Grafik
- Daerah
- Dunia
- mereka
- Mereka
- kemudian
- Sana.
- karena itu
- Ini
- mereka
- ini
- itu
- tiga
- Melalui
- di seluruh
- keluaran
- waktu
- untuk
- hari ini
- Total
- sulit
- mengangkut
- dahsyat
- dua
- bawah
- niscaya
- satuan
- sampai
- Memperbarui
- diperbarui
- meningkatkan
- us
- menggunakan
- bekas
- berbagai
- Sayur-sayuran
- sangat
- sebenarnya
- Mengunjungi
- volume
- volume
- Gudang
- adalah
- we
- minggu
- BAIK
- adalah
- Apa
- ketika
- yang
- sementara
- SIAPA
- mengapa
- akan
- jendela
- Musim dingin
- dengan
- dalam
- tanpa
- WMS
- Kerja
- bekerja
- kerja
- dunia
- akan
- tahunan
- tahun
- kamu
- Anda
- diri
- zephyrnet.dll
- zona