Empêcher la propagation de défauts systématiques dans le processus actuel de la conception à la fabrication des semi-conducteurs nécessite de nombreuses étapes de validation, d’analyse et d’optimisation. Les outils impliqués dans ce processus peuvent inclure la vérification des règles de conception (DRC), la vérification de la correction optique de proximité (OPC), l'écriture de masques et la métrologie/inspection de l'impression de plaquettes (pour évaluer le processus), la métrologie/l'inspection de l'impression de plaquettes et l'analyse des défaillances physiques pour confirmer la défaillance. diagnostic. L'échange d'informations et la co-optimisation entre ces étapes sont un processus complexe, avec de nombreuses boucles de rétroaction et de rétroaction. La communication est souvent entravée par des « murs » entre les différentes parties de la technologie des procédés, ce qui ralentit l'innovation. Lors de la récente conférence SPIE, Siemens EDA a présenté un discours liminaire proposant une série d'approches pour briser ces barrières afin d'améliorer la conception des puces jusqu'au processus de fabrication. Découvrez comment Siemens vise à éliminer les barrières de l'innovation en étendant la co-optimisation des technologies de conception.
À propos du discours d'ouverture
SPIE est la société internationale de l'optique et de la photonique. L'organisation remonte à 1955 et sa conférence est devenue un événement de premier plan sur des sujets avancés de conception et de fabrication. Lors de l'événement de cette année, Siemens a présenté le discours d'ouverture qui fait l'objet de cet article. De nombreux contributeurs à la présentation ont participé, notamment Le Hong, Fan Jiang, Yuansheng Ma, Srividya Jayaram, Joe Kwan, Siemens EDA (États-Unis) ; Doohwan Kwak, Siemens EDA (République de Corée) ; Sankaranarayanan Paninjath Ayyappan, Siemens EDA (Inde). Le titre de la conférence était Extension de la co-optimisation des technologies de conception depuis le lancement de la technologie jusqu'à HVM.
La conférence faisait partie d'une session sur la co-optimisation des technologies de conception (DTCO). Ce concept n'est pas nouveau, mais Siemens a étudié son application dans une portée plus large du processus, de la conception à la fabrication en grand volume (HVM). Les idées et les résultats présentés ont des implications significatives. Regardons de plus près.
Ce qui a été présenté
Tout d’abord, un aperçu de l’état actuel de l’utilisation du DTCO dans des éléments clés de l’écosystème a été présenté. Du point de vue de la conception, de nombreuses entreprises avancées sans usine disposent d'une équipe DFM qui voit les limites d'une approche basée sur des modèles. Ce qu’il faut réellement, c’est une nouvelle technologie pour faciliter l’apprentissage du rendement sans dépendre de la fonderie.
Les fonderies utilisent des approches d’apprentissage automatique basées sur des modèles de force brute, qui sont coûteuses mais pas totalement efficaces. Ils recherchent également une extraction efficace des informations sur les données de fabrication massives qu’ils créent. Les fournisseurs d'équipements et les fournisseurs d'EDA ont travaillé plus étroitement ensemble et proposent des solutions d'apprentissage automatique plus efficaces.
En prenant un peu de recul, il a été souligné qu'il existe des murs entre les phases de conception et de fabrication du processus. Les entreprises sans fabrique créent la conception, réalisent le DRC et la conception pour la fabrication (DFM), puis elles le jettent par-dessus le mur à l'équipe OPC/RET au sein de la fonderie ou de l'IDM. La conception effectue des tâches telles que l'OPC et la vérification, puis les données sont projetées par-dessus un autre mur pour l'écriture du masque et la métrologie/inspection. Le mur final est destiné à la fabrication. Ici, des tests électriques et une analyse des pannes seront effectués. Au moment où la cause profonde de l’échec est trouvée, 6 à 18 mois se sont écoulés. C’est une très longue boucle de rétroaction. Le graphique en haut de cet article décrit ce processus.
DTCO tente de faire tomber les murs, mais les méthodologies disponibles sont incomplètes. Le DTCO traditionnel commence très tôt dans le développement du processus. En commençant par un besoin de mise à l'échelle, une cellule standard est définie et une synthèse, un emplacement et un itinéraire sont effectués pour proposer des modèles de base et mesurer les performances et la puissance. La production de SRAM est également effectuée et ces données reviennent à la conception de cellule standard.
Ce qui a été présenté lors de la keynote de SPIE était une manière d'étendre ce concept de co-optimisation à l'ensemble du processus, de la conception à la fabrication. L'approche consiste à faciliter la circulation des informations depuis la conception jusqu'au processus final et à l'analyse physique en créant un canal d'information.
Même si cela semble simple, ce n’est pas le cas. De nombreux défis ont été discutés avec des approches concrètes pour atténuer les problèmes. Par exemple, les premières conceptions peuvent être créées avec des générateurs synthétiques de mise en page pour aider à calibrer le processus en fonction des problèmes de conception réels au fur et à mesure du développement du processus. Cela peut atténuer bon nombre des surprises auxquelles sont actuellement confrontés les premiers retraits de processus.
Gérer des volumes de données massifs constitue un autre défi. Grâce à de nouvelles techniques de compression sophistiquées, une amélioration de 30 fois est possible. Cela améliore considérablement les tâches de traitement et d’analyse des données. Un concept appelé IA explicable peut aider à trouver les causes profondes des problèmes beaucoup plus rapidement. La possibilité de recycler les modèles d’IA plus tard dans le processus de fabrication sans invalider les résultats antérieurs est un autre domaine à améliorer. Dans le domaine de l’analyse des données figurent également des techniques permettant de traiter les « données déséquilibrées ». Par exemple, il peut y avoir un point chaud trouvé dans 100,000,000 XNUMX XNUMX de modèles.
Rassembler tout cela peut créer un flux de conception de bout en bout beaucoup plus efficace, comme le montre la figure ci-dessous.
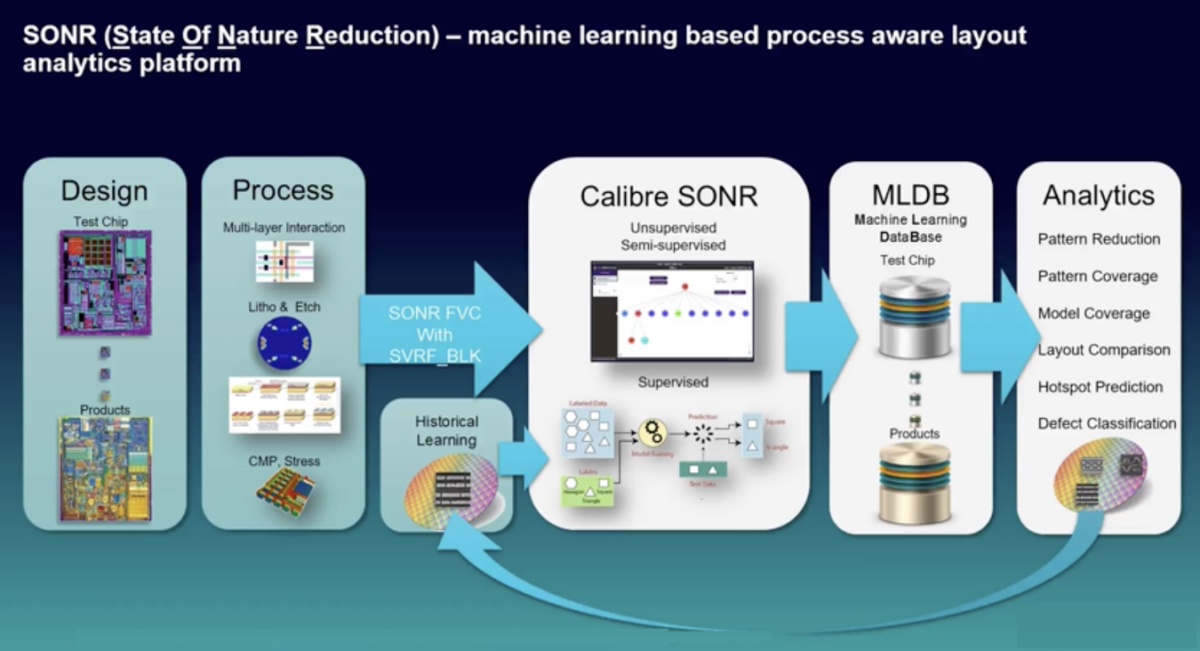
Pour apprendre plus
L’impact des approches décrites dans cette présentation principale est substantiel. Tu peux consultez la présentation et accédez à un livre blanc sur le processus ici. Il y a beaucoup d’informations utiles à obtenir. Et c’est ainsi que Siemens entend éliminer les barrières de l’innovation en élargissant la co-optimisation des technologies de conception.
Partagez cet article via:
- Contenu propulsé par le référencement et distribution de relations publiques. Soyez amplifié aujourd'hui.
- PlatoData.Network Ai générative verticale. Autonomisez-vous. Accéder ici.
- PlatoAiStream. Intelligence Web3. Connaissance Amplifiée. Accéder ici.
- PlatonESG. Carbone, Technologie propre, Énergie, Environnement, Solaire, La gestion des déchets. Accéder ici.
- PlatoHealth. Veille biotechnologique et essais cliniques. Accéder ici.
- La source: https://semiwiki.com/events/339386-spie-2023-buzz-siemens-aims-to-break-down-innovation-barriers-by-extending-design-technology-co-optimization/
- :possède
- :est
- :ne pas
- $UP
- 000
- 100
- 2023
- a
- capacité
- accès
- à travers
- propos
- Avancée
- AI
- Modèles AI
- vise
- Tous
- alléger
- aussi
- an
- selon une analyse de l’Université de Princeton
- ainsi que
- Une autre
- Application
- une approche
- approches
- SONT
- Réservé
- AS
- At
- Tentatives
- disponibles
- RETOUR
- obstacles
- Essentiel
- BE
- devenez
- était
- ci-dessous
- jusqu'à XNUMX fois
- Bit
- Pause
- plus large
- mais
- by
- appelé
- CAN
- Causes
- les causes
- cellule
- challenge
- globaux
- Développement
- vérification
- puce
- plus
- CO
- comment
- Venir
- Communication
- Sociétés
- complètement
- complexe
- concept
- béton
- Congrès
- Confirmer
- contributeurs
- cher
- engendrent
- créée
- La création
- Courant
- État actuel
- Lecture
- données
- l'analyse des données
- Dates
- affaire
- défini
- dépendance
- Conception
- Avec nos Bagues Halo
- détails
- développé
- Développement
- diagnostic
- discuté
- fait
- down
- rdc
- Plus tôt
- "Early Bird"
- plus facilement
- risque numérique
- Efficace
- efficace
- permettant
- end-to-end
- Tout
- l'équipements
- événement
- exemple
- échange
- étendre
- extension
- face
- faciliter
- Échec
- ventilateur
- plus rapide
- Réactions
- Figure
- finale
- Trouvez
- flux
- Pour
- trouvé
- Fonderie
- De
- gagné
- jauge
- générateurs
- graphique HD
- Maniabilité
- Vous avez
- vous aider
- ici
- Hong
- HOT
- Comment
- HTTPS
- et idées cadeaux
- Impact
- implications
- améliorer
- amélioration
- améliore
- in
- comprendre
- Y compris
- Inde
- d'information
- Innovation
- International
- impliqué
- implique
- vous aider à faire face aux problèmes qui vous perturbent
- IT
- SES
- joe
- ACTIVITES
- Tonique
- Corée
- plus tard
- lancer
- Disposition
- APPRENTISSAGE
- apprentissage
- limites
- Location
- Style
- regardé
- Lot
- click
- machine learning
- fabrication
- de nombreuses
- masque
- massif
- largeur maximale
- Mai..
- mesurer
- méthodologies
- Mines
- Réduire les
- numériques jumeaux (digital twin models)
- mois
- PLUS
- plus efficace
- beaucoup
- Besoin
- nécessaire
- Nouveauté
- of
- souvent
- on
- ONE
- optique
- Optique et photonique
- à mettre en œuvre pour gérer une entreprise rentable. Ce guide est basé sur trois décennies d'expérience
- or
- organisation
- ande
- décrit
- plus de
- Papier
- partie
- les pièces
- passé
- motifs
- effectuer
- performant
- effectué
- objectifs
- Physique
- Place
- plateforme
- Platon
- Intelligence des données Platon
- PlatonDonnées
- possible
- Post
- power
- premier
- présentation
- présenté
- impression
- d'ouvrabilité
- processus
- propagation
- proposé
- assez
- Lire
- réal
- vraiment
- récent
- Centrafricaine
- a besoin
- Résultats
- racine
- Itinéraire
- Règle
- mise à l'échelle
- portée
- sur le lien
- voir
- recherche
- semi-conducteur
- Série
- Session
- montré
- Siemens
- significative
- Le ralentissement de la
- Société
- Solutions
- sophistiqué
- Spot
- Standard
- Commencez
- départs
- Région
- États
- Étapes
- Ces
- tel
- surprises
- synthèse
- haute
- Prenez
- discutons-en
- tâches
- équipe
- techniques
- Technologie
- tester
- qui
- La
- puis
- Là.
- Ces
- l'ont
- this
- fiable
- Titre
- à
- aujourd'hui
- ensemble
- les outils
- top
- sujet
- Les sujets
- mélanger
- jeté
- traditionnel
- Uni
- États-Unis
- Utilisation
- informations utiles
- en utilisant
- validation
- divers
- fournisseurs
- Vérification
- très
- via
- volumes
- Wall
- était
- Façon..
- ont été
- Quoi
- Qu’est ce qu'
- qui
- blanc
- papier blanc
- sera
- comprenant
- dans les
- sans
- de travail
- écriture
- Rendement
- élastique
- you
- zéphyrnet