Tänapäeva pooljuhtide projekteerimisest valmistamise protsessis süstemaatiliste defektide leviku vältimine nõuab palju valideerimise, analüüsi ja optimeerimise etappe. Sellesse protsessi kaasatud tööriistad võivad hõlmata disainireeglite kontrollimist (DRC), optilise läheduse korrigeerimise (OPC) kontrollimist, maski kirjutamist ja vahvliprintimise metroloogiat/kontrolli (protsessi mõõtmiseks), vahvliprintimise metroloogiat/ülevaatust ja füüsilise rikke analüüsi rikke kinnitamiseks. diagnoos. Teabevahetus ja kaasoptimeerimine nende etappide vahel on keerukas protsess, mis sisaldab palju edasi- ja tagasisideahelaid. Suhtlemist takistavad sageli protsessitehnoloogia erinevate osade vahelised "seinad", mis aeglustavad innovatsiooni. Hiljutisel SPIE konverentsil esitas Siemens EDA peaettekande, milles pakkus välja mitmeid lähenemisviise nende seinte lõhkumiseks, et parandada kiibi disaini kuni tootmisprotsessini. Lugege edasi, et näha, kuidas Siemensi eesmärk on kaotada innovatsioonitõkked, laiendades disainitehnoloogia kaasoptimeerimist.
Keynote'i kohta
SPIE on rahvusvaheline optika ja fotoonika selts. Organisatsioon pärineb aastast 1955 ja selle konverentsist on saanud kõrgetasemeliste disaini- ja tootmisteemade peamine sündmus. Tänavusel üritusel esitles Siemens selle postituse teemaks olevat põhiettekannet. Esitlusele aitasid kaasa palju, sealhulgas Le Hong, Fan Jiang, Yuansheng Ma, Srividya Jayaram, Joe Kwan, Siemens EDA (Ameerika Ühendriigid); Doohwan Kwak, Siemens EDA (Korea Vabariik); Sankaranarayanan Paninjath Ayyappan, Siemens EDA (India). Kõne pealkiri oli Disainitehnoloogia kaasoptimeerimise laiendamine tehnoloogia käivitamisest HVM-ile.
Kõne oli osa disainitehnoloogia kaasoptimeerimise (DTCO) sessioonist. See kontseptsioon ei ole uus, kuid Siemens vaatles selle rakendust protsessi laiemas ulatuses, alates projekteerimisest kuni suuremahulise tootmiseni (HVM). Esitatud ideedel ja tulemustel on märkimisväärne mõju. Vaatame lähemalt.
Mida esitleti
Esiteks esitati ülevaade DTCO kasutamise hetkeseisust ökosüsteemi peamistes osades. Disaini vaatenurgast on paljudel arenenud muinasjuttude ettevõtetel DFM-i meeskond, kes näeb mustripõhise lähenemisviisi piire. Tegelikult on vaja uut tehnoloogiat, mis hõlbustaks saagi õppimist ilma valukojast sõltumata.
Valukojad kasutavad jõhkra jõuga mustripõhiseid masinõppe lähenemisviise, mis on kulukad, kuid mitte täiesti tõhusad. Samuti otsivad nad nende loodud tohutute tootmisandmete tõhusat teabekaevet. Seadmete müüjad ja EDA müüjad on teinud tihedamat koostööd ja tulevad välja tõhusamate masinõppelahendustega.
Veidi tagasi astudes toodi välja, et protsessi projekteerimis- ja tootmisfaasi vahel on seinad. Fablessi ettevõtted loovad disaini, teostavad Kongo Demokraatliku Vabariigi ja tootmiseks mõeldud disaini (DFM), seejärel viskavad nad selle valukoja või IDM-i OPC/RET meeskonnale üle seina. Disain saab tehtud ülesanded, nagu OPC ja kontrollimine, ning seejärel visatakse andmed maski kirjutamiseks ja metroloogia/kontrollimiseks üle teise seina. Viimane sein on valmistamiseks. Siin tehakse elektrikatse ja rikete analüüs. Ebaõnnestumise algpõhjuse leidmise ajaks on möödunud 6–18 kuud. See on väga pikk tagasiside ahel. Selle postituse ülaosas olev graafik kujutab seda protsessi.
DTCO üritab seinu lõhkuda, kuid olemasolevad metoodikad on puudulikud. Traditsiooniline DTCO algab protsessi arendamise alguses. Alustades skaleerimisvajadusest, määratletakse standardne lahter ning süntees, koht ja marsruut viiakse läbi põhimustrite leidmiseks ning jõudluse ja võimsuse mõõtmiseks. Samuti tehakse SRAM-i andmine ja see andmesilmus naaseb standardse rakukujunduse juurde.
SPIE põhiettekandes esitleti viis, kuidas seda kaasoptimeerimise kontseptsiooni laiendada kogu protsessile alates projekteerimisest kuni valmistamiseni. Lähenemisviis hõlmab teabekanali loomise kaudu lihtsama teabevoo võimaldamist disainist kuni lõppprotsessini ja füüsilise analüüsini.
Kuigi see kõlab otsekohene, pole see nii. Arutati paljusid väljakutseid konkreetsete lähenemisviiside abil probleemide leevendamiseks. Näiteks saab varajasi kujundusi luua paigutussünteetiliste generaatoritega, mis aitavad protsessi väljatöötamisel kalibreerida protsessi tegelike disainiprobleemidega. See võib leevendada paljusid üllatusi, mis praegu varajaste protsesside lindistamisega silmitsi seisavad.
Teine väljakutse on tohutute andmemahtudega tegelemine. Uute keerukate tihendustehnikate abil on võimalik 30-kordne paranemine. See parandab andmetöötluse ja analüüsi ülesandeid üsna palju. Mõiste nimega seletatav AI aitab palju kiiremini leida probleemide algpõhjuseid. Võimalus AI-mudeleid hiljem tootmisprotsessis ümber õpetada ilma varasemaid tulemusi kehtetuks tunnistamata on veel üks täiustamist vajav valdkond. Andmeanalüüsi valdkonnas on ka tehnikaid tasakaalustamata andmetega tegelemiseks. Näiteks võib 100,000,000 XNUMX XNUMX mustri hulgast olla üks kuum koht.
Selle kõige kokkupanemine võib luua palju tõhusama otsast lõpuni disainivoo, nagu on näidatud alloleval joonisel.
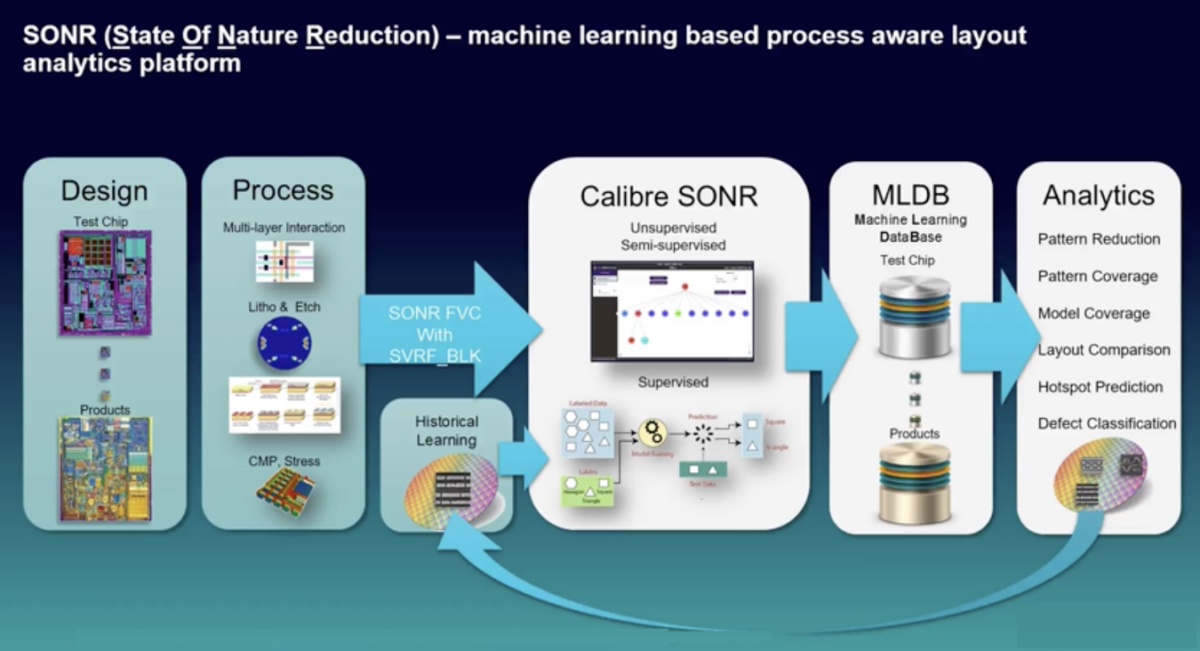
Lisateabe saamiseks
Selles põhiettekandes kirjeldatud lähenemisviiside mõju on märkimisväärne. Sa saad vaadake esitlust ja vaadake protsessi valget raamatut siin. Saada on palju kasulikku teavet. Ja nii püüab Siemens kaotada innovatsioonitõkked, laiendades disainitehnoloogia kaasoptimeerimist.
Jaga seda postitust:
- SEO-põhise sisu ja PR-levi. Võimenduge juba täna.
- PlatoData.Network Vertikaalne generatiivne Ai. Jõustage ennast. Juurdepääs siia.
- PlatoAiStream. Web3 luure. Täiustatud teadmised. Juurdepääs siia.
- PlatoESG. Süsinik, CleanTech, Energia, Keskkond päikeseenergia, Jäätmekäitluse. Juurdepääs siia.
- PlatoTervis. Biotehnoloogia ja kliiniliste uuringute luureandmed. Juurdepääs siia.
- Allikas: https://semiwiki.com/events/339386-spie-2023-buzz-siemens-aims-to-break-down-innovation-barriers-by-extending-design-technology-co-optimization/
- :on
- :on
- :mitte
- $ UP
- 000
- 100
- 2023
- a
- võime
- juurdepääs
- üle
- aadress
- edasijõudnud
- AI
- AI mudelid
- Eesmärgid
- Materjal: BPA ja flataatide vaba plastik
- leevendada
- Ka
- an
- analüüs
- ja
- Teine
- taotlus
- lähenemine
- lähenemisviisid
- OLEME
- PIIRKOND
- AS
- At
- Katsed
- saadaval
- tagasi
- tõkked
- põhiline
- BE
- muutuma
- olnud
- alla
- vahel
- Natuke
- Murdma
- laiem
- kuid
- by
- kutsutud
- CAN
- Põhjus
- põhjuste
- rakk
- väljakutse
- väljakutseid
- Kanal
- kontroll
- kiip
- lähemale
- CO
- Tulema
- tulevad
- KOMMUNIKATSIOON
- Ettevõtted
- täiesti
- keeruline
- mõiste
- betoon
- Konverents
- Kinnitama
- toetajad
- kulukas
- looma
- loodud
- loomine
- Praegune
- Praegune olek
- Praegu
- andmed
- andmete analüüs
- Kuupäevad
- tegelema
- määratletud
- sõltuvus
- Disain
- disainilahendused
- detailid
- arenenud
- & Tarkvaraarendus
- diagnoos
- arutatud
- tehtud
- alla
- drc
- Ajalugu
- Varajane
- lihtsam
- ökosüsteemi
- Tõhus
- tõhus
- võimaldades
- Lõpuks-lõpuni
- Kogu
- seadmed
- sündmus
- näide
- vahetamine
- laiendama
- laiendades
- silmitsi seisnud
- hõlbustada
- ebaedu
- lehvikut
- kiiremini
- tagasiside
- Joonis
- lõplik
- leidma
- voog
- eest
- avastatud
- Valukoda
- Alates
- saadud
- gabariit
- generaatorid
- graafiline
- Käsitsemine
- Olema
- aitama
- siin
- Hong
- KUUM
- Kuidas
- HTTPS
- ideid
- mõju
- mõjud
- parandama
- paranemine
- parandab
- in
- sisaldama
- Kaasa arvatud
- India
- info
- Innovatsioon
- rahvusvaheliselt
- seotud
- hõlmab
- küsimustes
- IT
- ITS
- joe
- Võti
- Põhitoon
- Korea
- pärast
- algatama
- Layout
- Õppida
- õppimine
- piirid
- Pikk
- Vaata
- Vaatasin
- Partii
- masin
- masinõpe
- tootmine
- palju
- mask
- suur
- max laiuse
- mai..
- mõõtma
- metoodikad
- Kaevandamine
- Leevendada
- mudelid
- kuu
- rohkem
- tõhusam
- palju
- Vajadus
- vaja
- Uus
- of
- sageli
- on
- ONE
- optika
- Optika ja fotoonika
- optimeerimine
- or
- organisatsioon
- välja
- välja toodud
- üle
- Paber
- osa
- osad
- Vastu võetud
- mustrid
- täitma
- jõudlus
- teostatud
- perspektiiv
- füüsiline
- Koht
- inimesele
- Platon
- Platoni andmete intelligentsus
- PlatoData
- võimalik
- post
- võim
- peaminister
- esitlus
- esitatud
- trükkimine
- probleeme
- protsess
- paljundamine
- pakutud
- üsna
- Lugenud
- reaalne
- tõesti
- hiljuti
- Vabariik
- Vajab
- Tulemused
- juur
- Marsruut
- Eeskiri
- ketendamine
- ulatus
- vaata
- nägemine
- otsib
- pooljuht
- Seeria
- istung
- näidatud
- Siemens
- märkimisväärne
- Aeglustub
- Ühiskond
- Lahendused
- keeruline
- Kaubandus-
- standard
- Käivitus
- algab
- riik
- Ühendriigid
- Sammud
- mahukas
- selline
- üllatusi
- süntees
- sünteetiline
- Võtma
- rääkima
- ülesanded
- meeskond
- tehnikat
- Tehnoloogia
- test
- et
- .
- SIIS
- Seal.
- Need
- nad
- see
- aeg
- Kapslid
- et
- tänane
- kokku
- töövahendid
- ülemine
- teema
- Teemasid
- viskama
- visanud
- traditsiooniline
- Ühendatud
- Ühendriigid
- Kasutus
- kasulik informatsioon
- kasutamine
- kinnitamine
- eri
- müüjad
- Kontrollimine
- väga
- kaudu
- mahud
- Sein
- oli
- Tee..
- olid
- M
- Mis on
- mis
- valge
- valge paber
- will
- koos
- jooksul
- ilma
- töö
- kirjutamine
- saak
- saagikus
- sa
- sephyrnet