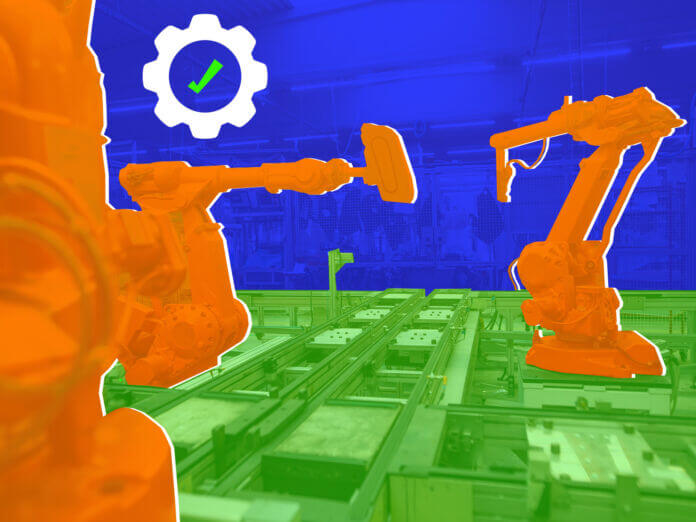
Para evitar possíveis avarias, lesões de funcionários e perdas de produção, cada vez mais empresas se familiarizam com o monitoramento remoto de ativos. Eles tentam correr sistemas de manutenção preditiva para detectar problemas antes que eles ocorram na fabricação, minimizando os riscos de insatisfação de funcionários e clientes e evitando perdas de dinheiro.
Felizmente, o século 21 oferece soluções modernas e eficazes de manutenção preditiva na manufatura para implementação em diferentes setores.
Recentemente, Prylada conduziu uma série de entrevistas de desenvolvimento de clientes, nas quais abordamos especialistas da indústria manufatureira. Nossa equipe estabeleceu o objetivo de coletar informações valiosas sobre monitoramento de ativos e desafios de adoção de tecnologia na indústria e como as empresas os resolvem.
Durante as entrevistas, discutimos o estado atual do mercado, os assuntos mais incômodos, a concorrência e recomendações para um desenvolvimento efetivo do setor.
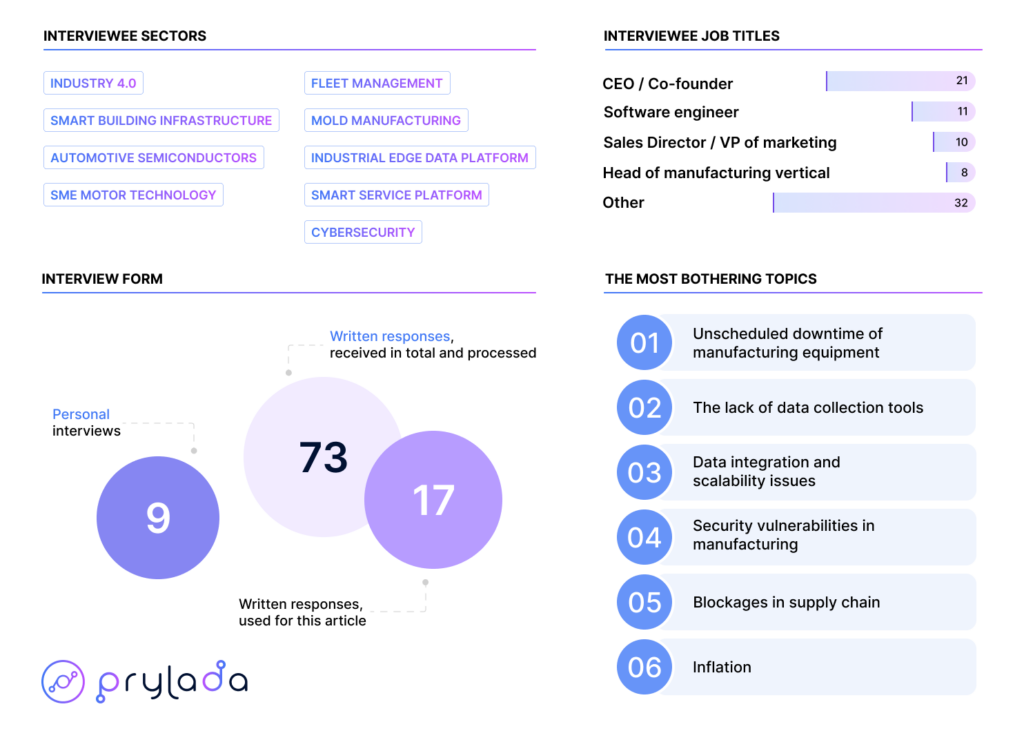
Como o mercado manufatureiro mudou nos últimos 5 anos?
As preferências dos consumidores em relação à personalização dos produtos, aos preços competitivos e aos melhores prazos de entrega tornaram-se os principais impulsionadores para as empresas industriais repensarem a sua abordagem de trabalho. Para acompanharem as exigências modernas, precisam de aumentar a produtividade através da implementação de tecnologias digitais. Essas tecnologias incluem soluções de sustentabilidade habilitadas digitalmente, gêmeos digitais, robôs móveis autônomos, realidade aumentada, IA e aprendizado de máquina.
"A realidade do passado era que os fabricantes faziam horas extras, faziam coisas muito manuais e não recebiam apoio. Eles simplesmente realizaram o trabalho, e agora isso mudou para onde essas empresas de manufatura passaram de apenas fazer o trabalho para onde precisam lançar grandes iniciativas de transformação digital."
- Richard Lebovitz, CEO da LeanDNA
Os fabricantes começaram a pensar da seguinte perspectiva:
- Precisamos estar muito mais conectados
- Precisamos de ter melhor visibilidade não só das questões com que nos debatemos, mas também das ações que precisamos de tomar.
O quadro geral mudou do trabalho como ele é para a transformação digital priorizando ações. Além disso, a COVID-19 destacou a importância de redes de abastecimento fortes e adaptáveis. Perdas significativas decorrentes das consequências imprevistas da pandemia levaram empresas industriais reconsiderar suas atuais estratégias de negócios. Como resultado, visaram otimizar os processos existentes e reduzir a sua dependência de fatores externos, aumentando assim a resiliência a situações de força maior.
O foco na sustentabilidade torna-se uma força motriz para uma maior utilização de tecnologias inteligentes de IoT, tornando a indústria transformadora mais inteligente, mais eficiente e sustentável, ao mesmo tempo que melhora o bem-estar dos funcionários. Isso está acontecendo por meio da automação e da transformação digital, e está aproveitando a análise preditiva para gerar melhores recomendações. Por sua vez, isto dá-nos uma melhor compreensão de quais são os estrangulamentos e quais são os desafios.
Por outro lado, o processo de adoção de novas tecnologias inteligentes tornou-se mais complexo e demorado. Os desafios da cadeia de abastecimento e a escassez de pessoal levaram todo o C-Suite a envolver-se profundamente com questões operacionais e decisões ao nível do chão. Isto resultou num maior número de partes interessadas que precisavam de compreender os riscos, alinhar-se com os benefícios de valor previstos e equilibrar estas considerações com outras iniciativas da empresa.
O ritmo acelerado dos avanços tecnológicos em áreas como a automação, a inteligência artificial e a Internet das Coisas exige que os fabricantes se adaptem e integrem novas tecnologias nas suas operações.
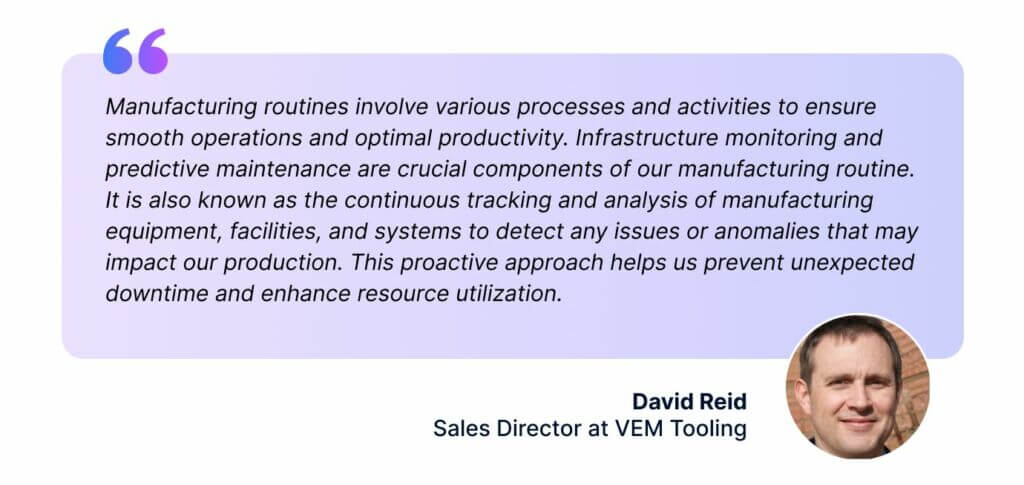
No entanto, a transição para novas tecnologias de monitorização de ativos pode ser complexa e dispendiosa, exigindo a melhoria das competências da mão de obra e a garantia da compatibilidade com os sistemas existentes.
Reunimos os desafios e barreiras mais comuns associados a esta transição, conforme partilharam connosco os nossos entrevistados. Colocados em primeiro lugar estão os pontos que ouvimos com mais frequência. Isto não significa necessariamente que sejam os mais críticos, mas indica a sua prevalência. Vamos começar.
Tempo de inatividade não programado de equipamentos de fabricação
A fabricação de dispositivos modernos envolve processos complexos de alta precisão e equipamentos sofisticados. Paradas não programadas de equipamentos de fabricação podem ter um custo muito alto devido à perda de rendimento e perda de tempo de produção. Inovações recentes em manutenção preditiva podem ajudar muito a reduzir a perda de produtividade e economizar muito esforço e tempo.
Uma das técnicas empregadas com sucesso para manutenção preditiva na fabricação utiliza a análise de grandes quantidades de dados de falhas, manutenção e dados de rastreamento. Para fortalecer a qualidade dos dados utilizados, parâmetros como processo, carimbo de data/hora e informações detalhadas dos componentes são atribuídos a modelos de falhas para criar conjuntos de dados robustos. Várias grandes empresas fabricantes de semicondutores relataram o uso de tais técnicas como parte de seus modelos de manutenção preditiva para melhorar o rendimento.
Os desafios permanecem, pois muitos processos complexos tendem a sofrer desvios e mudanças frequentes. Parâmetros específicos são ajustados entre as execuções para manter o processo no alvo. Técnicas como sensores virtuais que monitoram e capturam a configuração dos parâmetros em tempo real podem ser utilizadas para possibilitar o controle adequado. Esta é uma área de investigação activa actualmente, e os investigadores estão a explorar activamente novas técnicas, incluindo inteligência artificial.
A falta de ferramentas de coleta de dados
Como a visibilidade limitada dos ativos significa maiores custos de manutenção e substituição, muitos fabricantes já lutam para capturar dados básicos da máquina. Esses dados normalmente incluem temperatura, vibração, velocidade e outros indicadores de desempenho.
Para muitas empresas, no entanto, investir em ferramentas de recolha de dados pode ser um empreendimento dispendioso. É por isso que preferem trabalhar com os recursos disponíveis, o que pode dificultar o desenvolvimento de várias maneiras.
Os fabricantes que desejam usar dados em tempo real para monitoramento de ativos precisam de uma ferramenta que possa conectar e coletar automaticamente dados de qualquer fonte. Idealmente, também deve ser capaz de normalizar e gerenciar os dados, realizar análises e integrar-se facilmente com aplicativos de terceiros e plataformas de computação em nuvem.
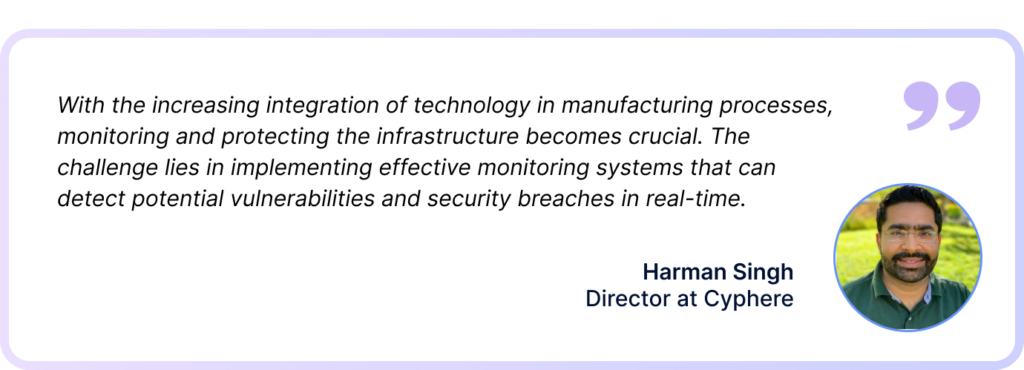
Problemas de integração e escalabilidade de dados
A infraestrutura de fabricação geralmente compreende diversos sistemas, como máquinas, linhas de produção e sistemas de utilidades. Esses sistemas podem ter sido implementados em momentos diferentes, utilizando tecnologias variadas. Além disso, cada sistema gera dados em seu formato, tornando a integração com sistemas de terceiros uma tarefa formidável. Formatos inconsistentes, valores ausentes e imprecisões dificultam uma integração eficaz.
À medida que as instalações e os processos de fabricação evoluem, o cenário de dados cresce. Os sistemas devem ser escaláveis para acomodar volumes crescentes de dados. É essencial garantir um fluxo de dados contínuo e eficiente em todas as operações de fabricação, sem sobrecarregar a infraestrutura de monitoramento. Alcançar isso é possível investindo em ferramentas modernas e priorizando a qualidade dos dados.

Vulnerabilidades de segurança na fabricação
A indústria transformadora enfrenta um cenário em constante evolução de ameaças cibernéticas, desde ataques de ransomware até vulnerabilidades na cadeia de abastecimento. No contexto do hardware, os produtos falsificados de qualidade inferior eram considerados um grande problema para os semicondutores, enquanto os chips permaneciam relativamente inalterados por questões relacionadas com a segurança.
No entanto, nos últimos anos, os invasores encontraram métodos para explorar o intrincado processo de fabricação de semicondutores. Eles tentaram manipular a arquitetura do chip introduzindo lógica maliciosa por meio de Trojans de hardware. Os invasores utilizam esses Trojans para negação de serviço (DoS) ou roubo de dados. Notavelmente, a Síria relatou um grande ataque de Trojan, onde os atacantes incorporaram um Trojan chamado “Kill Switch” num chip para desativar o sistema de defesa aérea sírio, permitindo-lhes executar um ataque aéreo.
Nos últimos anos, os fabricantes expandiram o uso de conceitos de análise de dados baseados em aprendizado de máquina e Internet das Coisas (IoT), para garantir que seus equipamentos estejam devidamente protegidos. Nessas técnicas, eles primeiro inicializam o equipamento para todos os parâmetros de monitoramento e depois aplicam algoritmos de aprendizado de máquina a esses parâmetros, para prever a classe do parâmetro na saída. Se os resultados (saída) não corresponderem à previsão, os fabricantes poderão sinalizar o equipamento.
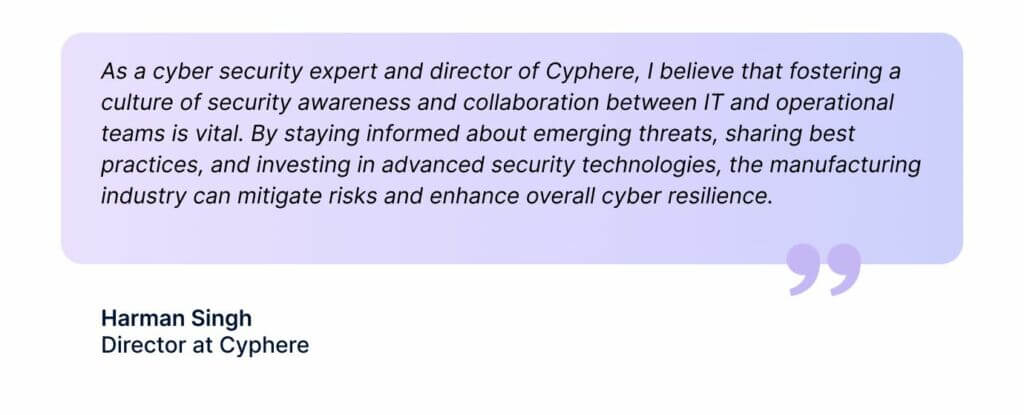
Outros obstáculos que impedem a produção sustentável
Bloqueios na Cadeia de Abastecimento
Historicamente, os fabricantes enfrentaram diversas dificuldades e as previsões para 2024 mostram mais do mesmo. À medida que o comércio global se torna mais complexo, os produtores devem preparar-se para resistir a interrupções inesperadas ou repentinas nas suas redes de abastecimento.
De acordo com alguns dos nossos entrevistados, as interrupções nas cadeias de abastecimento continuarão a ser uma das dificuldades mais significativas que a indústria enfrentará no futuro próximo. Atualmente, os estoques estão nos níveis mais baixos em décadas, indicando que determinados produtos não podem ser fabricados neste momento. A grave escassez de semicondutores de Taiwan, China e outras empresas offshore forçou o fechamento de algumas fábricas automotivas. A produção nacional também tem enfrentado dificuldades.
Inflação
Em 2023, a inflação esteve próxima dos dois dígitos devido ao aumento da procura e à oferta insuficiente em todas as principais economias. No próximo ano, os preços dos principais factores de produção, como o alumínio, o petróleo e o aço, aumentarão ainda mais, aumentando a pressão sobre as empresas que já tentam reduzir custos sem sacrificar a qualidade.
É difícil localizar recursos e investimentos para automação do monitoramento de ativos durante a inflação. Mas os fabricantes não devem ignorar o potencial que isso traz para a indústria. Pode ajudar a reduzir erros manuais e acelerar tarefas em até 10 vezes.
Para fazer face a este desafio, a indústria deve alocar um orçamento para a automação e introduzir mais tecnologia de IA para inspecionar e automatizar tarefas em tempo real. Ajudará não só a poupar custos, mas também a melhorar a eficiência e a reduzir o desperdício.
Desafios da adoção de tecnologias digitais
Os processos de fabricação giram em torno de cronogramas e tarefas contínuas e rotineiras operadas por centenas de fornecedores e funcionários em vários locais e voltadas para a produção de bens consumíveis. Isto torna excepcionalmente difícil para as empresas monitorar as rotinas atuais e identificar áreas de melhoria.
Os fabricantes podem rastrear facilmente cada etapa de toda a sua cadeia de valor, implementando tecnologias de monitoramento em tempo real baseadas em IoT. Essas tecnologias irão ajudá-los a compreender melhor as lacunas nos seus objetivos de sustentabilidade e a encontrar soluções para melhorar a eficiência, o rendimento e a conformidade.
O monitoramento inteligente de ativos está normalmente associado a dois desafios. A primeira envolve a integração e atualização de equipamentos legados para serem compatíveis com novas tecnologias, possibilitando todo o potencial da Indústria 4.0. A segunda pressupõe a requalificação do pessoal para garantir que possa monitorizar, utilizar e beneficiar eficazmente de um novo sistema de monitorização.
Os pequenos fabricantes muitas vezes consideram o investimento inicial em novas tecnologias assustador. No entanto, é essencial reconhecer que tanto a transformação digital como a transformação dos colaboradores são processos graduais. Essas mudanças não ocorrem da noite para o dia.
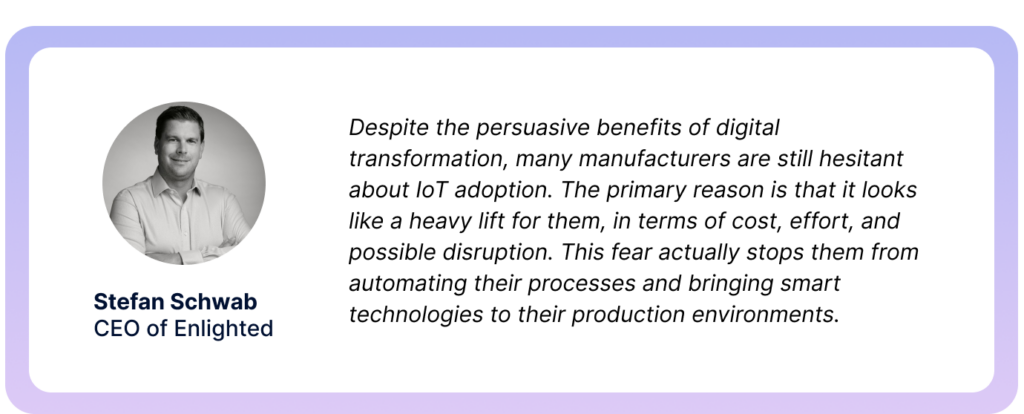
Resumindo
A indústria transformadora já está a experimentar os efeitos da automação e da robótica, como a inteligência artificial, a Internet das Coisas, sensores, robôs no local e cada vez mais utilização da automação robótica de processos. A crescente procura pela adoção de tecnologias digitais e os benefícios que as empresas industriais podem obter delas impulsionam o crescimento da digitalização.
Como parte dos esforços contínuos para lidar com os desafios que a indústria enfrenta atualmente, os fabricantes implementam soluções baseadas em IoT para monitoramento inteligente de ativos. No entanto, a escolha da tecnologia e a sua opção de implementação ainda dependem das oportunidades e necessidades do negócio.
Tempo de inatividade não programado de máquinas industriais, problemas de coleta de dados, vulnerabilidades de segurança e restrições de escalabilidade são os desafios que estão posicionados em primeiro lugar no cenário de produção e podem ser abordados por tecnologias de monitoramento baseadas em IoT. Essas tecnologias fornecem aos fabricantes dados granulares e contextualizados em toda a cadeia de fornecimento, para que possam identificar rapidamente os problemas e tomar medidas.
Além disso, também podem prever potenciais problemas antes que aconteçam, evitando recalls e outros riscos ambientais significativos. Com o tempo, as tecnologias de monitorização permitirão aos utilizadores acompanhar o progresso dos seus objetivos de sustentabilidade e garantir a conformidade com os regulamentos da indústria.
Gostaríamos de agradecer a todos que participaram de nossa entrevista de desenvolvimento de clientes:
- Vatsal Shah, CEO da Tornassol
- Stefan Schwab, CEO da Iluminado
- Tom Richter, chefe global de verticais de fabricação discreta e de processos para indústrias digitais da Nokia
- Nils Arnold, CEO da Adance
- Duncan Kerr, ex-CEO da Aeristech
- Richard Lebovitz, CEO da LeanDNA
- Gulroz Singh, arquiteto de segurança SoC da NXP Semiconductors
- Donnie Rand, coordenador de marketing da Associação Americana de Operadores Proprietários, LLC
- David Reid, Diretor de Vendas da Ferramentas VEM
- Derrick Hathaway, diretor de vendas da VEM Médico
- Harman Singh, diretor da Cifra
- Doug Lawson, CEO da PenseIQ
- E outros profissionais do setor, cujos comentários foram levados para este artigo
- Conteúdo com tecnologia de SEO e distribuição de relações públicas. Seja amplificado hoje.
- PlatoData.Network Gerativa Vertical Ai. Capacite-se. Acesse aqui.
- PlatoAiStream. Inteligência Web3. Conhecimento Amplificado. Acesse aqui.
- PlatãoESG. Carbono Tecnologia Limpa, Energia, Ambiente, Solar, Gestão de resíduos. Acesse aqui.
- PlatoHealth. Inteligência em Biotecnologia e Ensaios Clínicos. Acesse aqui.
- Fonte: https://www.iotforall.com/experts-discuss-predictive-maintenance-and-innovation-in-manufacturing
- :tem
- :é
- :não
- :onde
- $UP
- 1
- 10
- 2023
- 2024
- 21st
- 361
- a
- Capaz
- Sobre
- acomodar
- em
- Açao Social
- ações
- ativo
- ativamente
- adaptar
- Adição
- endereçado
- Ajustado
- Adotando
- Adoção
- avanços
- contra
- AI
- Destinado
- AR
- algoritmos
- alinhar
- Todos os Produtos
- distribuir
- Permitindo
- já
- tb
- quantidades
- an
- análise
- analítica
- e
- Antecipado
- qualquer
- aplicações
- Aplicar
- abordagem
- adequadamente
- arquitetura
- SOMOS
- ÁREA
- áreas
- por aí
- artificial
- inteligência artificial
- AS
- ativo
- associado
- Associação
- At
- ataque
- Ataques
- tentada
- aumentado
- Realidade Aumentada
- automatizar
- automaticamente
- Automação
- automotivo
- Autônomo
- disponível
- evitando
- Equilíbrio
- barreiras
- baseado
- basic
- BE
- tornam-se
- torna-se
- sido
- antes
- ser
- beneficiar
- Benefícios
- MELHOR
- Melhor
- entre
- Grande
- impulsionar
- ambos
- gargalos
- Traz
- orçamento
- negócio
- negócios
- mas a
- by
- C-suite
- chamado
- CAN
- Pode obter
- não podes
- capturar
- luta
- Century
- Chefe executivo
- certo
- cadeia
- correntes
- desafiar
- desafios
- mudado
- Alterações
- China
- lasca
- Chips
- escolha
- classe
- Fechar
- Na nuvem
- computação em nuvem
- CO
- coletar
- coleção
- comentários
- comum
- Empresas
- Empresa
- compatibilidade
- compatível
- obrigado
- competição
- competitivo
- integrações
- compliance
- componente
- compreender
- compreende
- computação
- conceitos
- conduzido
- Configuração
- Contato
- Consequências
- Considerações
- restrições
- contexto
- continuar
- contínuo
- ao controle
- Coordenador
- Custo
- dispendioso
- custos
- Falsificação
- Covid-19
- crio
- crítico
- Atual
- Estado atual
- Atualmente
- cliente
- personalização
- cibernético
- dados,
- Análise de Dados
- qualidade de dados
- conjuntos de dados
- David
- décadas
- decisões
- profundamente
- Defesa
- Entrega
- Demanda
- demandas
- Demografia
- Denial of Service
- dependência
- depende
- detalhado
- Desenvolvimento
- Dispositivos/Instrumentos
- diferente
- difícil
- dificuldades
- digital
- Transformação Digital
- Gêmeos digitais
- digitalização
- digitalmente
- dígitos
- Diretor
- discutir
- discutido
- diferente
- do
- parece
- fazer
- Doméstico
- feito
- DOS
- duplo
- Dois digitos
- tempo de inatividade
- distância
- Drivers
- condução
- dois
- durante
- cada
- facilmente
- economias
- Eficaz
- efetivamente
- efeitos
- eficiência
- eficiente
- esforço
- esforços
- ou
- incorporado
- empregada
- Empregado
- colaboradores
- permitir
- habilitado
- permitindo
- esforço
- engajar
- aprimorando
- garantir
- assegurando
- Todo
- ambiental
- equipamento
- erros
- essencial
- Mesmo
- todos
- evolui
- excepcionalmente
- executar
- existente
- expandido
- experimentando
- especialistas
- Explorar
- Explorando
- externo
- enfrentou
- rostos
- instalações
- enfrentando
- fatores
- familiarizar
- poucos
- Encontre
- Primeiro nome
- Andar
- fluxo
- Foco
- seguinte
- Escolha
- força
- o previsível
- formato
- Antigo
- ex-ceo
- formidável
- encontrado
- freqüente
- freqüentemente
- da
- cheio
- futuro
- lacunas
- colhido
- gera
- ter
- obtendo
- OFERTE
- dá
- Global
- comércio global
- meta
- Objetivos
- ido
- bens
- tem
- gradual
- maior
- grandemente
- Cresce
- Growth
- mão
- acontecer
- Acontecimento
- Queijos duros
- Hardware
- Ter
- cabeça
- ouvir
- ajudar
- Alta
- Destaque
- dificultar
- historicamente
- Como funciona o dobrador de carta de canal
- Contudo
- http
- HTTPS
- Centenas
- idealmente
- identificar
- if
- ignorar
- executar
- implementação
- implementado
- implementação
- importância
- melhorar
- melhoria
- melhorar
- in
- incluir
- inclui
- Incluindo
- Crescimento
- aumentou
- aumentando
- indicam
- indicador
- indicadores
- industrial
- indústrias
- indústria
- indústria 4.0
- inflação
- INFORMAÇÕES
- Infraestrutura
- do estado inicial,
- iniciativas
- e inovações
- inputs
- integrar
- Integração
- integração
- Inteligência
- Inteligente
- pretender
- Internet
- internet das coisas
- Internet das coisas (IoT)
- Entrevista
- entrevistados
- Entrevistas
- para dentro
- intricado
- introduzir
- introduzindo
- investir
- investimento
- Investimentos
- envolve
- iot
- emitem
- questões
- IT
- ESTÁ
- Trabalho
- jpg
- apenas por
- Guarda
- Chave
- Falta
- paisagem
- grande
- Sobrenome
- lançamento
- aprendizagem
- levou
- Legado
- Nível
- níveis
- aproveitando
- como
- Limitado
- linhas
- locais
- lógica
- procurando
- fora
- perdas
- perdido
- lote
- diminuir
- menor
- máquina
- aprendizado de máquina
- maquinaria
- máquinas
- a Principal
- manutenção
- principal
- FAZ
- Fazendo
- malicioso
- gerencia
- manual
- fabricado
- Fabricantes
- fabrica
- indústria de transformação
- muitos
- mercado
- Marketing
- Match
- Matéria
- max-width
- Posso..
- significar
- significa
- métodos
- minimizando
- desaparecido
- Móvel Esteira
- modelos
- EQUIPAMENTOS
- dinheiro
- Monitore
- monitoração
- mais
- mais eficiente
- Além disso
- a maioria
- múltiplo
- devo
- necessariamente
- você merece...
- necessário
- Cria
- redes
- Novo
- Novas tecnologias
- Próximo
- Nokia
- notavelmente
- agora
- número
- obstáculos
- ocorrer
- of
- Oferece
- frequentemente
- AZEITE E AZEITE EVO
- on
- ONE
- queridos
- contínuo
- só
- operado
- operacional
- Operações
- operadores
- oportunidades
- Otimize
- Opção
- or
- Outros
- A Nossa
- saída
- Acima de
- global
- durante a noite
- esmagador
- proprietário
- Paz
- parâmetro
- parâmetros
- parte
- Participou
- passado
- realizar
- atuação
- Pessoal
- perspectiva
- fotografia
- colocado
- Plataformas
- platão
- Inteligência de Dados Platão
- PlatãoData
- pontos
- posicionado
- possível
- potencial
- predizer
- predição
- Previsões
- preditivo
- Análise Preditiva
- preferir
- preferências
- Preparar
- pressão
- predomínio
- evitar
- impedindo
- Valores
- preços
- priorização
- problemas
- processo
- Automação de Processos
- processos
- Produtores
- Produto
- Produção
- produtividade
- Produtos
- Progresso
- adequado
- protegido
- qualidade
- rapidamente
- citar
- rand
- ransomware
- Ataques de Ransomware
- rápido
- chegando
- reais
- em tempo real
- dados em tempo real
- Realidade
- recentemente
- reconhecer
- recomendações
- reconsiderar
- reduzir
- reduzir o desperdício
- regulamentos
- relativamente
- permanecem
- permaneceu
- remoto
- substituição
- Informou
- exige
- pesquisa
- pesquisadores
- resiliência
- requalificação
- Recursos
- resultar
- resultou
- Resultados
- Richter
- ascensão
- riscos
- Automação de Processo Robótica
- robótica
- robôs
- uma conta de despesas robusta
- rotina
- Execute
- é executado
- sacrificando
- Segurança
- vendas
- mesmo
- Salvar
- AMPLIAR
- escalável
- Escassez
- desatado
- Segundo
- segurança
- Semicondutor
- Semicondutores
- sensor
- Série
- serviço
- conjunto
- Conjuntos
- vários
- grave
- compartilhado
- deslocado
- Turnos
- escassez
- rede de apoio social
- mostrar
- periodo
- simplesmente
- situações
- smart
- mais inteligente
- So
- Soluções
- RESOLVER
- alguns
- sofisticado
- fonte
- específico
- velocidade
- partes interessadas
- começado
- Estado
- aço
- Stefan
- Passo
- estratégias
- Fortalecer
- mais forte,
- Lutar
- Lutando
- entraram com sucesso
- tal
- súbito
- fornecedores
- supply
- cadeia de suprimentos
- Desafios da cadeia de suprimentos
- Redes de fornecimento
- Suportado
- Vistorias
- Sustentabilidade
- sustentável
- Síria
- .
- sistemas
- Taiwan
- Tire
- tomado
- Target
- Tarefa
- tarefas
- Profissionais
- técnicas
- tecnológica
- Tecnologias
- Tecnologia
- Tender
- obrigado
- que
- A
- roubo
- deles
- Eles
- si mesmos
- então
- Este
- deles
- coisas
- Pensando
- De terceiros
- isto
- aqueles
- pensamento
- ameaças
- Através da
- todo
- Assim
- tempo
- demorado
- vezes
- timestamp
- para
- ferramenta
- ferramentas
- para
- traçar
- pista
- comércio
- Transformação
- transição
- troiano
- tentar
- tentando
- VIRAR
- Twins
- dois
- tipicamente
- não afetado
- compreender
- compreensão
- Inesperado
- imprevisto
- aprimoramento
- us
- Uso
- usar
- usava
- usuários
- usos
- utilização
- utilidade
- Valioso
- Informação valiosa
- valor
- Valores
- variando
- Velocidade
- Verticais
- muito
- Virtual
- visibilidade
- volumes
- vulnerabilidades
- foi
- Desperdício
- maneiras
- we
- foram
- O Quê
- qual
- enquanto
- QUEM
- de quem
- porque
- precisarão
- de
- dentro
- sem
- Atividades:
- Força de trabalho
- trabalhar
- ano
- anos
- ainda
- Produção
- zefirnet