Le stress thermique est un problème bien connu dans les emballages avancés, au même titre que les défis liés au stress mécanique. Les deux sont exacerbés par une intégration hétérogène, qui nécessite souvent de mélanger des matériaux présentant des coefficients de dilatation thermique (CTE) incompatibles.
Les effets sont déjà visibles et ne feront probablement qu’empirer à mesure que la densité des paquets augmentera au-delà de 1,000 XNUMX bosses par puce.
« Vous combinez des métaux qui ont un CTE relativement élevé, puis vous avez des polymères qui ont une rigidité CTE encore plus grande, et enfin des diélectriques qui ont un CTE extrêmement faible. Une fois que vous avez tout mis en place, le stress est inévitable », a déclaré Mario Gonzalez, directeur scientifique et responsable R&D pour la modélisation et la caractérisation mécaniques et thermiques chez imec.
De telles contraintes entraînent souvent un gauchissement ou une inclinaison importante de la matrice, qui à leur tour conduisent à des conditions qui diminuent la fiabilité. « Vous avez affaire à différentes technologies de substrat avec un nombre de couches multiples », a déclaré Chip Greely, vice-président de l'ingénierie chez Promex Industries. « Les différentes épaisseurs de noyau dans les substrats, en particulier, commencent à créer de nombreux problèmes mécaniques classiques, notamment le gauchissement, qui est devenu un problème pour certains des plus grands acteurs. Nous demandons à beaucoup de nos clients qui disposent d'un module multi-puces à intégration hétérogène intégré dans un boîtier, de fournir les données de moiré d'ombre de leurs substrats afin que nous puissions voir la façon dont sa déformation change en fonction de la température de refusion et, idéalement, trouver son point de réflexion. »
Cette souche a divers effets négatifs, ressentis à plusieurs échelles dimensionnelles, selon Gilad Barak, vice-président des nouvelles technologies avancées chez La Nova. "Souvent, la courbure et la torsion des caractéristiques au niveau de la nanostructure résultent de la contrainte intégrée qui a été créée, comme on le trouve dans certaines DRAM et nanofeuilles de logique frontale", a-t-il déclaré. « Un autre exemple concerne les zones à l'échelle micrométrique où les contraintes induites empêchent la fabrication de structures semi-conductrices haut de gamme, comme cela est typique dans les « zones interdites » autour des vias traversants en silicium (TSV). Enfin, les impacts à grande échelle des contraintes induites peuvent provoquer une courbure de la tranche, ce qui complique considérablement sa manipulation et sa fabrication, ce qui risque de la fracturer elle-même. La courbure des plaquettes est particulièrement visible lors du dépôt de couches diélectriques épaisses, comme cela est courant lors de la fabrication de dispositifs NAND 3D.
La bonne nouvelle est que l’industrie est très consciente de ces problèmes et des problèmes qui y sont associés. La mauvaise nouvelle est que les solutions manquent encore, même si de nombreuses approches sont actuellement explorées.
"Il existe différentes méthodologies pour réduire le gauchissement, mais aucune d'entre elles n'est totalement efficace et elles impliquent toujours des compromis", a déclaré Frank Chen, directeur des applications et de la gestion des produits chez Bruker Nano Surfaces & Métrologie. « Les problèmes ne se limitent pas à une sélection restreinte d’applications. Chaque fois que vous attachez une matrice à un autre substrat, vous rencontrerez ces problèmes.
Tout cela signifie que l’inspection et la métrologie doivent continuer à jouer un rôle essentiel. D'autres problèmes, tels que les points chauds, peuvent également être exacerbés lorsque plusieurs puces sont combinées dans des boîtiers hétérogènes.
"Pendant les tests, diverses puces chaufferont à des moments différents et à des températures différentes, créant ainsi des points chauds potentiels qui doivent être correctement refroidis", a déclaré Andrei Berar, directeur principal du développement commercial des tests chez Amkor. "En plus de créer des contrôleurs thermiques actifs spécifiques - correspondant à la surface des différentes puces - des efforts importants sont déployés pour développer des contrôleurs thermiques adaptatifs capables d'"anticiper" les points chauds en fonction des vecteurs fournis par le programme de test."
De telles combinaisons conduisent également à un recours croissant à la métrologie hybride, combinant différentes techniques pour aller plus rapidement à la racine des problèmes.
Solutions de conception, d’inspection et de test
En effet, l’interaction classique entre la conception, l’inspection et les contraintes thermomécaniques n’a fait que se complexifier avec des milliers de connexions toujours plus petites et plus fragiles.
L’un des résultats est un accent renouvelé sur le déplacement à gauche, dans l’espoir de « concevoir » les problèmes de CTE et les effets en cascade qui en résultent, qui peuvent conduire à une surchauffe et à des contraintes mécaniques. Et pour augmenter les chances de prévenir et de détecter les défauts critiques, la simulation et l'inspection sont toutes deux nécessaires, selon Andras Vass-Varnai, responsable du développement de portefeuille au sein du segment Industrie électronique et semi-conducteurs de Siemens Digital Industries Software.
« La co-simulation thermique et structurelle utilisant la dynamique des écoulements informatiques (CFD), la modélisation par éléments finis (FEA), etc., dès les premières étapes de conception du package, aide à la fois à comprendre les performances attendues de l'assemblage et permet également une bonne base pour ' Optimisation basée sur l'IA, car de nombreux choix de conception peuvent être paramétrés », a expliqué Vass-Varnai. « Une fois le premier prototype construit, les tests thermiques transitoires peuvent aider à cartographier les performances thermiques du composant. S'il existe un décalage entre le comportement thermique attendu et le comportement thermique réel, les données de test peuvent être utilisées pour « calibrer » les propriétés matérielles du jumeau numérique du boîtier et mettre à jour les bibliothèques de matériaux pour une plus grande précision initiale des conceptions à venir.
Trouver la meilleure façon de tester les réseaux de tests et de les concevoir pour les tests constitue un défi croissant. « Et s'il y a un signal qui monte et descend ? » a demandé Rob Aitken, un Synopsys compagnon. « Cela crée un problème de test, car maintenant vous avez un signal qui ne va nulle part et un autre signal qui vient de nulle part, et vous devez comprendre comment vous allez tester ces choses. Les sondez-vous ? Mais dans ce cas, vous devez respecter certaines dimensions physiques, et vous courez alors le risque de dommages mécaniques. Ou trouvez-vous une sorte de structure de type JTAG ? Mais cela réduit alors l’efficacité de ces points de connexion. Nous sommes dans une vaste phase d'expérimentation où tout le monde dit : "Peut-être que ça marchera, peut-être que ça marchera". Pour le moment, je ne voudrais pas nécessairement parier sur ce que « ça » signifie.
Il existe des options de tests indirects et directs pour l'enquête sur les défauts, selon le JCET. Par exemple, le CSAM (Computed Scanning Acoustic Tomography) et les rayons X 3D sont indirects, tandis que l'analyse mécanique transversale est un outil de preuve directe. JCET dispose également d'équipements de caractérisation thermique avancés pour caractériser les problèmes de matériaux/structures résultant de défauts mécaniques.
L’inspection optique est, comme toujours, l’approche la plus rapide pour l’inspection en ligne, mais la meilleure pratique est une approche hybride. "La meilleure méthode pour détecter les courts-circuits/ouvertures et les défauts marginaux serait l'inspection SPI (pâte à souder) pour pré-refusionner l'AOI (inspection optique automatisée) et post-refusionner l'AOI sur les rayons X en ligne", a conseillé Timothy Skunes, vice-président de la recherche. et développement chez Nordson Test & Inspection Cyberoptique portefeuille.
De plus, d’autres modalités peuvent être utiles, notamment au niveau des nœuds avancés. Par exemple, une approche récente pour caractériser la déformation dans les dispositifs semi-conducteurs est la spectroscopie Raman (RS). "RS est hautement applicable pour les mesures sur structure, offrant des mesures rapides de l'ordre de quelques secondes et de petites tailles de points de quelques microns pour permettre des mesures détaillées", a déclaré Barak de Nova. "La difficulté de mesurer directement la contrainte sur les structures avant l'introduction de la spectroscopie Raman comme outil de métrologie en ligne dans l'usine a conduit à des tests à des étapes beaucoup plus tardives du processus de fabrication."
En fin de compte, pour une inspection approfondie, il n’y a pas de raccourcis. Les calculs budgétaires peuvent nécessiter des mesures comparatives, telles que le coût initial d'un nouvel instrument par rapport au coût continu de RMA excessives. Et il y a encore une chose à considérer : comment vous assurer que vous pouvez faire confiance à vos données.
« Allez-vous jeter ce qui était probablement du bon matériel pour vous assurer que vous n'aurez aucun problème dans ce que vous transmettrez à l'utilisateur final ? Qui va en supporter le coût ? » a prévenu Mike McIntyre, directeur de la gestion des produits logiciels chez Sur l'innovation, qui recommande une base de données statistique pour une évaluation comparative précise lors de la classification automatisée des défauts.
Warpage
L'un des pires résultats du stress est le gauchissement. Il peut être surprenant que la déformation soit difficile à détecter, mais l'effet n'est pas toujours aussi évident qu'il y paraît. Le gauchissement provoque de légères différences de coplanarité entre la puce et le substrat, provoquant une connexion insuffisante de certaines microbosses avec les plots situés en dessous, une défaillance appelée non humide.
« Prenons l'exemple d'un processeur avancé mesurant 50 à 60 mm », a déclaré Chen. « En raison de sa grande taille, il est difficile de le traiter sans déformation. Néanmoins, si l’outil de fixation de matrice est réglé au centre de sa fenêtre de processus, il peut passer l’inspection et être fabriqué avec des rendements élevés. Le problème est que la tolérance peut être très étroite. Dès que vous avez un peu d'inclinaison de la matrice au-dessus du gauchissement, vous avez des problèmes de non-mouillage.
Pire encore, si cela se produit à des pas de bosse de l'ordre de 50 µm (taille de bosse de ̴ 35 µm), imaginez les problèmes à mesure que les dimensions de bosse diminuent davantage. C'est déjà une préoccupation pour l'industrie automobile, alors qu'elle se dirige vers sa prochaine génération en 2023 et 2024. La transition critique se fera autour du nœud de 28 nm, a déclaré Chen.
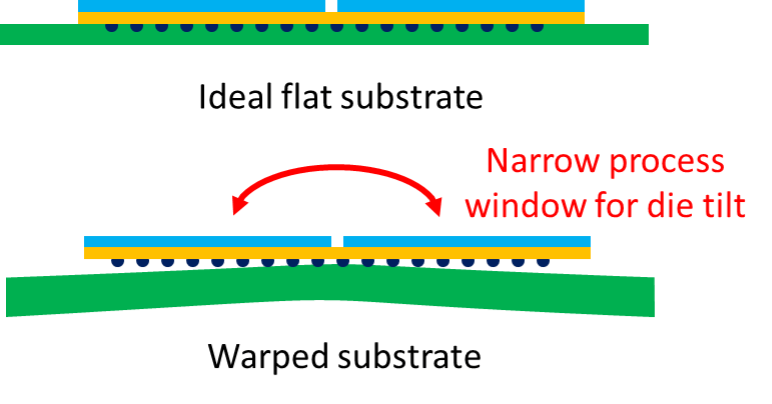
Fig. 1 Les outils de fixation de matrice ont une fenêtre de processus très étroite pour l'inclinaison de la matrice en cas de gauchissement. Source : Bruker
Non mouillé
« Non mouillé » est un terme général couvrant plusieurs problèmes pouvant survenir avec des bosses de soudure, dont la plupart sont d'une subtilité frustrante. Étant donné que la soudure est souvent à l’état liquide, son processus d’application a été surnommé « mouillage ». Les liens ténus sont appelés « non humides », et deviennent de plus en plus problématiques sur les nœuds plus petits dotés de connexions plus fines.
Les produits non mouillés échappent souvent aux processus de criblage classiques, pour ensuite apparaître plus tard sous forme de copeaux retournés (RMA). Les causes profondes peuvent être thermiques, mécaniques ou une combinaison de celles-ci, comme le cyclage thermique dans une voiture qui roule également sur un terrain accidenté. L'effet cumulatif peut fournir suffisamment de contraintes thermomécaniques pour rompre le contact.
Il existe des surnoms supplémentaires qui décrivent des types spécifiques de problèmes. Au lieu de la forme lisse et colonnaire d’une bonne connexion, dans un défaut « tête dans l’oreiller », une boule semble s’enfoncer dans l’autre, comme une tête sur un oreiller.
"Il est toujours en contact, donc le test électrique peut être bon, mais vous pouvez voir qu'il est très fragile", a déclaré Chen, désignant la radiographie d'un oreiller pour la tête. «Dès que vous subissez une contrainte thermique ou mécanique, il peut se briser complètement. Même s'il s'agit d'un contact non humide, la connexion mince conduit à une résistance élevée, des performances sous-optimales et ne durera probablement pas longtemps. Un non-humide ouvert ne fonctionnera pas du tout. Dans un scénario typique avec inclinaison de la matrice, il y a une transition visible entre des bosses bien formées et des bosses non mouillées.
Le problème critique concerne les défauts latents : des connexions suffisamment fonctionnelles pour réussir les tests électriques mais qui échouent sur le terrain.
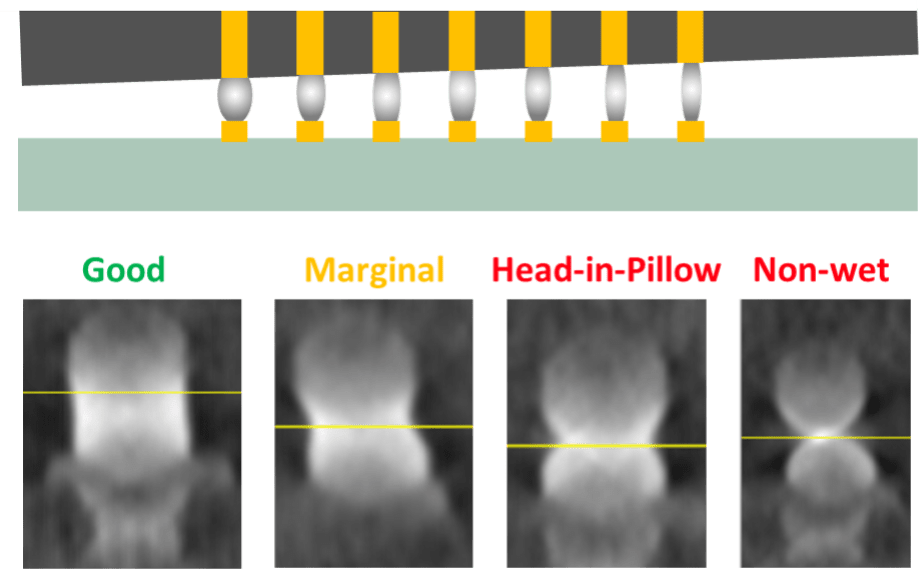
Fig. 2 Transition progressive des bonnes bosses aux non mouillés en présence d'une inclinaison de la matrice. Source : Bruker
"C'est actuellement un gros problème avec de nombreux types d'appareils en raison des effets du stress thermique", a déclaré Chen. « Un client avait un produit qui avait passé avec succès le test électronique et qui a été expédié. Malheureusement, ils ont eu beaucoup de RMA en raison de défaillances non mouillées qui se sont développées par la suite.
Certaines entreprises résolvent ce problème en effectuant des inspections manuelles péniblement fastidieuses. Malheureusement, tout examen humain est sujet à la fatigue de l'opérateur, en particulier lorsque les examinateurs tentent de détecter des erreurs subtiles au cours d'un quart de travail de plusieurs heures.
Du côté positif, il existe désormais des approches automatisées d’inspection, telles que les outils à rayons X qui peuvent être utilisés en ligne. « Il y a une forte motivation en faveur d'une inspection à grande vitesse et entièrement automatisée pour atteindre <100 dppb, en particulier pour l'industrie automobile », a déclaré Chen.
À partir de là, cela devient plus compliqué. "En particulier, la soudure, responsable de nombreux produits non humides, est également sujette à l'électromigration", a déclaré Tom Marinis, membre principal du personnel technique du laboratoire de Draper. « Si la densité de courant dans une connexion entre une puce et un substrat est trop élevée pour une soudure particulière sur une période donnée, car la température de fusion de la soudure peut être relativement basse par rapport à la température de fonctionnement de l'appareil, vous pouvez obtenir une migration. des atomes et forment des vides et finissent par ouvrir une connexion.
Marinis a averti que les outils de modélisation commerciaux au niveau des circuits imprimés ne sont pas assez matures pour alerter de manière cohérente sur les problèmes potentiels d'électromigration. Il est donc important de continuer à effectuer un test de vieillissement accéléré.
Conclusion
En fin de compte, la détection des problèmes de fiabilité dus à des défauts latents nécessitera une métrologie d'échantillonnage plus élevée, sensible au déplacement de la matrice, à la rotation, à la hauteur, à l'inclinaison et à d'autres paramètres. Cela nécessitera également de s'appuyer davantage sur la modélisation multiphysique pour tenter d'anticiper et de résoudre les problèmes potentiels avant la production. Et alors que les industries des semi-conducteurs et de l’automobile continuent de s’entremêler, les enjeux vont bien au-delà des simples RMA.
« Le coût d'une panne augmente de façon exponentielle à mesure que les défauts latents se propagent des appareils aux modules jusqu'aux voitures, ce qui pourrait mettre la vie des personnes en danger », a déclaré Chen. C'est pourquoi les fabricants de puces créent des solutions globales combinant conception, inspection et tests pour mieux détecter les défauts latents.
- Contenu propulsé par le référencement et distribution de relations publiques. Soyez amplifié aujourd'hui.
- Platoblockchain. Intelligence métaverse Web3. Connaissance Amplifiée. Accéder ici.
- La source: https://semiengineering.com/bump-reliability-is-challenged-by-latent-defects/
- 000
- 1
- 2023
- 2024
- 3d
- a
- accéléré
- Selon
- précision
- Avec cette connaissance vient le pouvoir de prendre
- atteindre
- infection
- actually
- ajout
- Supplémentaire
- adresser
- Avancée
- anti-âge
- Alerte
- Tous
- permet
- déjà
- Bien que
- toujours
- selon une analyse de l’Université de Princeton
- ainsi que
- Une autre
- anticiper
- en vigueur
- applications
- Application
- une approche
- approches
- Réservé
- domaines
- autour
- Assemblée
- Évaluation de risque climatique
- associé
- joindre
- Automatisation
- l'automobile
- industrie automobile
- Mal
- balle
- basé
- base
- Gardez
- car
- devenez
- devenir
- before
- derrière
- va
- ci-dessous
- LES MEILLEURS
- Pari
- Améliorée
- jusqu'à XNUMX fois
- Au-delà
- Big
- plus gros
- Bit
- Pause
- vaste
- budget
- construit
- intégré
- la performance des entreprises
- Développement des affaires
- appelé
- Peut obtenir
- fournisseur
- voitures
- maisons
- Attraper
- Causes
- les causes
- causer
- Canaux centraux
- CFD
- challenge
- contesté
- globaux
- difficile
- chances
- Modifications
- caractériser
- chen
- puce
- chips
- choix
- classiques
- classification
- combinaison
- комбинации
- combiner
- combiné
- combinant
- comment
- commercial
- Commun
- Sociétés
- par rapport
- complètement
- complexe
- compliqué
- composant
- PROBLÈMES DE PEAU
- conditions
- NOUS CONTACTER
- connexion
- Connexions
- Considérer
- contact
- continuer
- Core
- coins
- Prix
- pourriez
- couvrant
- engendrent
- créée
- crée des
- La création
- critique
- Courant
- Lecture
- des clients
- Clients
- Coupe
- données
- Base de données
- traitement
- densité
- décrire
- Conception
- Avec nos Bagues Halo
- détaillé
- développer
- développé
- Développement
- dispositif
- Compatibles
- J'ai noté la
- différences
- différent
- Difficulté
- numérique
- jumeau numérique
- dimensions
- directement
- Directeur
- faire
- Ne pas
- down
- marchand de nouveautés
- driver
- doublé
- pendant
- dynamique
- "Early Bird"
- effet
- les effets
- efficace
- efforts
- Electronique
- l'accent
- ENGINEERING
- assez
- assurer
- l'équipements
- Erreurs
- notamment
- etc
- Ether (ETH)
- Pourtant, la
- faire une éventuelle
- peut
- exemple
- exécutif
- avec des données
- attendu
- expérimenté
- expliqué
- Exploré
- exponentielle
- extrêmement
- FAIL
- Échec
- le plus rapide
- sensation de fatigue
- Fonctionnalités:
- compagnon
- few
- champ
- figues
- Figure
- finalement
- Trouvez
- trouver
- Prénom
- flux
- formulaire
- trouvé
- de
- frustrant
- fonctionnel
- plus
- génération
- obtenez
- Goes
- aller
- Bien
- graduel
- Croissance
- Pousse
- Maniabilité
- Dur
- front
- la taille
- aider
- aide
- Haute
- augmentation
- très
- holistique
- Avec optimisme
- HOT
- Comment
- How To
- HTTPS
- humain
- Hybride
- Impacts
- important
- in
- Y compris
- Améliore
- croissant
- secteurs
- industrie
- initiale
- plutôt ;
- instrument
- l'intégration
- Introduction
- enquête
- isolé
- aide
- vous aider à faire face aux problèmes qui vous perturbent
- IT
- lui-même
- Genre
- laboratoire
- gros
- grande échelle
- plus importantes
- Nom de famille
- couche
- poules pondeuses
- conduire
- conduisant
- Conduit
- LED
- Niveau
- bibliothèques
- Probable
- Gauche
- Liquide
- Vit
- Location
- Lot
- Faible
- maintenir
- faire
- Fabrication
- gestion
- manager
- Manuel
- fabriqué
- de nombreuses
- Localisation
- Mario
- assorti
- Matériel
- matières premières.
- mature
- largeur maximale
- veux dire
- des mesures
- mesure
- mécanique
- membre
- Métaux
- méthode
- méthodologies
- Métrique
- Métrologie
- pourrait
- migration
- se mêlant
- modélisation statistique
- module
- Modules
- PLUS
- (en fait, presque toutes)
- se déplace
- plusieurs
- nano
- nécessairement
- nécessaire
- négatif
- Néanmoins
- Nouveauté
- Les nouvelles technologies
- nouvelles
- next
- nœud
- nœuds
- évident
- offrant
- ONE
- en cours
- ouvert
- d'exploitation
- opérateur
- à mettre en œuvre pour gérer une entreprise rentable. Ce guide est basé sur trois décennies d'expérience
- Options
- de commander
- Autre
- paquet
- Forfaits
- l'emballage
- Pain
- paramètres
- particulier
- particulièrement
- passé
- peopleâ € ™ s
- effectuer
- performant
- période
- phase
- Physique
- emplacements
- Platon
- Intelligence des données Platon
- PlatonDonnées
- Jouez
- joueurs
- Point
- des notes bonus
- polymères
- portefeuille
- positif
- possible
- défaillances
- pratique
- présence
- président
- prévention
- Directeur
- Avant
- Probablement
- sonde
- Problème
- d'ouvrabilité
- processus
- les process
- Processeur
- Produit
- gestion des produits
- Vidéo
- Programme
- preuve
- correctement
- propriétés
- prototype
- fournir
- à condition de
- mettre
- R & D
- gamme
- Nos tests de diagnostic produisent des résultats rapides et précis sans nécessiter d'équipement de laboratoire complexe et coûteux,
- réal
- récent
- recommande
- réduire
- réduit
- réflexion
- relativement
- fiabilité
- dépendance
- renouvelé
- exigent
- a besoin
- un article
- Recherche et développement
- résultat
- résultant
- Résultats
- Analyse
- risques
- rôle
- racine
- Courir
- Saïd
- dit
- Balance
- balayage
- scénario
- dépistage
- secondes
- semble
- clignotant
- sélection
- semi-conducteur
- supérieur
- sensible
- plusieurs
- Shadow
- Forme
- décalage
- DÉPLACEMENT
- expédiés
- Shorts
- montrer
- Signal
- significative
- de façon significative
- simulation
- Taille
- tailles
- petit
- faibles
- So
- Logiciels
- Solutions
- quelques
- disponible
- Identifier
- groupe de neurones
- Spectroscopie
- Spot
- L'équipe
- Étape
- étapes
- pieu
- Commencer
- Région
- statistique
- Encore
- stress
- de construction
- structure
- sujet
- réussi
- tel
- surprenant
- Technique
- techniques
- Les technologies
- tester
- Essais
- La
- La Région
- leur
- Là.
- thermique
- chose
- des choses
- milliers
- Avec
- Lancement
- fiable
- fois
- à
- ensemble
- tolérance
- trop
- outil
- les outils
- top
- vers
- transition
- La confiance
- TOUR
- types
- débutante
- comprendre
- prochain
- Mises à jour
- utilisé
- Utilisateur
- divers
- Vaste
- Vice-président
- visible
- bien connu
- Quoi
- qui
- tout en
- WHO
- sera
- sans
- Activités principales
- pire
- pourra
- radiographie
- rendements
- Votre
- zéphyrnet